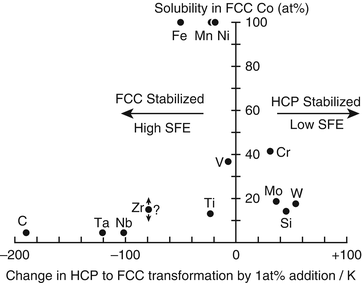
Fig. 7.2
Effects of alloying elements on the temperature of the transformation from hcp Co to fcc Co as a function of solubility of the elements in fcc Co [5]
In this chapter, first, the history and current status of biomedical Co-Cr alloys such as Co-28mass%Cr-6mass%Mo and Co-20mass%Cr-15mass%W-10mass%Ni alloys are briefly reviewed. Their microstructure, processing, and properties are then discussed. Control of the microstructure of Co-Cr alloys is essential for practical applications, as it is for other metallic materials. Therefore, the effects of different processing techniques and the alloy composition including minor alloying elements on the microstructure are described with a focus on grain refinement and precipitation. As a novel processing technique for implant fabrication, an additive manufacturing technique using an electron beam and a laser beam is mentioned. Finally, the mechanical properties and corrosion and wear resistances of the alloys are presented. Hereafter, the chemical composition of the alloys is reported in units of mass%, although the mass% notation is omitted.
7.2 Co-Cr Alloys as Metallic Biomaterials
7.2.1 History
Co-based alloys in the Co-Cr and Co-Cr-W systems have been established since the early 1900s, and the Stellite alloys manufactured by Haynes became important industrial materials for wear-resistant hardfacing applications [5]. In the 1930s, a cast Co-Cr-Mo alloy, Vitallium, was developed, a technique for the lost-wax (investment) casting of the alloy was established, and the alloy was commercialized for dental prosthetics [7, 8]. Venable and Stuck used Vitallium devices for internal fixation of fractures and showed in the late 1930s that the alloy can be used in medical implants [9–11]. Vitallium was also used for prosthetic acetabular cups by Smith-Petersen in the late 1930s [12, 13]. These cups were used in the standard method for hip reconstruction until total hip replacement operations were introduced in the 1960s [12]. In the 1950s and early 1960s, metal-on-metal-type and metal-on-polymer-type artificial hip joints using Vitallium were developed. The former are represented by the McKee-Farrar joint, and the latter were pioneered by Charnley [14]. Other Co-Cr alloys such as Co-Cr-W-Ni (L-605, HS25, ASTM F 90) [15], Co-Ni-Cr-Mo (MP35N, ASTM F 562), and Co-Cr-Fe-Ni-Mo (Elgiloy, ASTM F 1058 grade 1) system alloys, which are still used in practical applications at the present time, had been developed in the early 1960s. Thus, the Co-Cr alloys have a long history consisting of more than 80 years of use as dental and medical materials.
Currently, cast and wrought Co-Cr alloys are widely used for implants such as artificial joints, denture wires, and stents. Metal-on-metal-type total hip replacements made of Co-Cr-Mo alloys were revived in the late 1980s [14] because the loosening of the metal-on-UHMWPE (ultrahigh molecular weight polyethylene)-type artificial hip joints was found to be related to osteolysis caused by the formation of UHMWPE wear debris [16]. Recently, however, a decrease in the number of stemmed metal-on-metal-type artificial hip joints made of Co-Cr-Mo alloys used for hip replacements in England and Wales was reported [17].
7.2.2 Types of Co-Cr Alloys
With their long history of practical applications, Co-Cr alloys have been listed in the ASTM standards for surgical implant applications [18]. Table 7.1 shows the chemical compositions from the standards. The contents of not only the main alloying elements such as Cr, W, and Mo but also minor alloying elements such as carbon and nitrogen are standardized. ASTM F 75 is for castings, and the others are for wrought products. The maximum carbon content in ASTM F 75 (Co-28Cr-6Mo) is 0.35 mass%. The low carbon content in ASTM F 75 alloy possibly causes the formation of the σ-phase (intermetallic compound, Co(CrMo)), which likely deteriorates the mechanical properties of the alloy. Carbon suppresses the formation of the σ-phase by forming carbides. The ASTM F 799 and F 1537 alloys, whose chemical compositions are registered as Co-28Cr-6Mo, have three types: Alloy 1 and Alloy 2 have low (C ≤ 0.14mass%) and high (0.15mass% ≤ C ≤ 0.35mass%) carbon contents, respectively, and Alloy 3 contains Al and La, which form oxide particles that provide dispersion strengthening [19].
Table 7.1
Chemical compositions (mass%) of Co-Cr alloys registered in the ASTM standards for biomedical applications
ASTM | Conditions | Chemical composition (mass%) | |||||||||||||||||
---|---|---|---|---|---|---|---|---|---|---|---|---|---|---|---|---|---|---|---|
Cr | Mo | Ni | Fe | C | Si | Mn | W | P | S | N | Al | Ti | B | La | Be | Co | |||
F 75-12 | Casting | 27.00 | 5.00 | <0.50 | <0.75 | <0.35 | <1.00 | <1.00 | <0.20 | <0.020 | <0.010 | <0.25 | <0.10 | <0.10 | <0.010 | – | – | Bal. | |
−30.00 | −7.00 | ||||||||||||||||||
F 799-11 | Forgings | Alloy1 (low carbon) | 26.0 | 5.0 | <1.0 | <0.75 | <0.14 | <1.0 | <1.0 | – | – | – | <0.25 | – | – | – | – | – | Bal. |
F 1537-11 | Wrought | −30.0 | −7.0 | ||||||||||||||||
Alloy2 (high carbon) | 26.0 | 5.0 | <1.0 | <0.75 | 0.15 | <1.0 | <1.0 | – | – | – | <0.25 | – | – | – | – | – | Bal. | ||
−30.0 | −7.0 | −0.35 | |||||||||||||||||
Alloy3 (dispersion strengthened) | 26.0 | 5.0 | <1.0 | <0.75 | <0.14 | <1.0 | <1.0 | – | – | – | <0.25 | 0.30 | – | – | 0.03 | – | Bal. | ||
−30.0 | −7.0 | −1.00 | −0.20 | ||||||||||||||||
F 90-09 | Wrought | 19.00 | – | 9.00 | <3.00 | 0.05 | <0.40 | 1.00 | 14.00 | <0.040 | <0.030 | – | – | – | – | – | – | Bal. | |
F 1091-12 | Wrought (wire) | −21.00 | −11.00 | −0.15 | −2.00 | −16.00 | |||||||||||||
F 56-13 | Wrought | 19.0 | 9.0 | 33.0 | <1.0 | <0.025 | <0.15 | <0.15 | – | <0.015 | <0.010 | – | – | <1.0 | <0.015 | – | – | Bal. | |
F 68-10 | Wrought (plate, sheet, and foil) | −21.0 | −10.5 | −37.0 | |||||||||||||||
F 96-08 | Forgings | ||||||||||||||||||
F 1058-08 | Wrought (wire and strip) | Grade 1 | 19.0 | 6.0 | 14.0 | Bal. | <0.15 | <1.20 | 1.5–2.5 | – | <0.015 | <0.015 | – | – | – | – | – | <0.10 | 39.0 |
−21.0 | −8.0 | −16.0 | −41.0 | ||||||||||||||||
Grade 2 | 18.5 | 6.5 | 15.0 | Bal. | <0.15 | <1.20 | 1.0–2.0 | – | <0.015 | <0.015 | – | – | – | – | – | <0.001 | 39.0 | ||
−21.5 | −7.5 | −18.0 | −42.0 |
Another classification of the Co-Cr alloys focuses on Ni content. The Ni content in ASTM F 75 alloy is required to be less than 0.5 mass%, and the Ni contents in ASTM F 799 and F 1537 alloys are required to be less than 1.0mass%. Other Co-Cr alloys such as ASTM F 90 (Co-20Cr-15W-10Ni), ASTM F 562 (Co-35Ni-20Cr-10Mo), and ASTM F 1058 (40Co-20Cr-16Fe-15Ni-7Mo) are allowed to contain Ni as an alloying element.
Figure 7.3 shows the stacking fault energies (SFEs) of three types Co-Cr alloys compared with those of Fe-based alloys [20]. The ASTM F 75 alloy, which is represented as Co-29Cr-6Mo in the figure, has a low SFE, so the hcp ε-phase with poor workability would form during the cooling process in a casting or heat treatment. In contrast, Co-30Ni-20Cr-10Mo (close composition to ASTM F 562) and Co-20Cr-15W-10Ni (ASTM F 90) alloys, which contain Ni as an alloying element, exhibit mid-level and high SFEs, respectively. Therefore, the formation of the hcp ε-phase is suppressed, and these alloys have excellent hot and cold workability. In this context, Co-28Cr-6Mo alloys are basically unsuitable for wrought applications, but the workability in the Co-28Cr-6Mo alloys can be improved by optimizing the amounts of minor alloying elements such as nitrogen and by thermomechanical treatments (see Sect. 7.4.1).
7.2.3 Applications
Table 7.2 summarizes the applications of Co-Cr alloys. Cast Co-28Cr-6Mo (ASTM F 75) alloy has been used in the stem, ball, and cup of artificial hip joints including both metal-on-UHMWPE and metal-on-metal joints as well as in the sliding components of artificial knee joints. Since artificial knee joints have complicated shapes, investment casting is essential for their production. Wrought Co-28Cr-6Mo Alloy 1 and Alloy 2 (ASTM F 799 and F 1537) have been used in the joint replacements for hips, knees, shoulders, and so on. The Co-Cr alloys in the Co-Cr-W-Ni (ASTM F 90/F 1091), Co-Ni-Cr-Mo (ASTM F 562), and Co-Cr-Fe-Ni-Mo (ASTM F 1058) systems are used for wrought products that require a large deformation to fabricate. Since they exhibit excellent hot and cold workability and can be strengthened by cold working, they have been used in fixation wires, vascular stents, springs, catheters, surgical clips, orthodontic dental archwires, and so on.
Table 7.2
Applications of Co-Cr alloys
ASTM | Alloys (mass%) | Trade name | Application |
---|---|---|---|
F 75-12 | Co-28Cr-6Mo | Vitallium (Howmedica, Inc) | Stem, ball, and cup of artificial joints |
Haynes-Stellite 21(HS21) (Cabot Corp.) | Fixation screws | ||
Protasul-2 (Sulzer AG) | Bone plates | ||
Zimaloy (Zimmer Inc.) | |||
F 799-11 | BioDur CCM Plus Alloy (Carpenter Technology Corp.) | Joint replacements (hip, knee, shoulder) | |
F 1537-11 | Fixation devices | ||
F 90-09 | Co-20Cr-15W-10Ni | Haynes-Stellite 25 (HS25) (Cabot Corp.) | Fixation wires |
F 1091-12 | L-605 (Carpenter Technology Corp.) | Vascular stents | |
Heart valves | |||
F 562-13 | Co-35Ni-20Cr-10Mo | MP35N (SPS Technologies, Inc.) | Lead conductor wires |
F 688-10 | Biophase (Richards Medical Co.) | Springs | |
F 961-08 | Protasul-10 (Sulzer AG) | Stylets | |
Catheters | |||
Orthopedic cables | |||
Cardiovascular stents | |||
F 1058-08 | 40Co-20Cr-16Fe-15Ni-7Mo | Elgiloy (Elgiloy Ltd.) | Arch wires |
Phynox (ArcelorMittal Stainless & Nickel Alloys) | Springs | ||
Conichrome (Carpenter Technology Corp.) | Lead conductor wires | ||
Surgical clips | |||
Balloon-expandable stents (annealed) | |||
Self-expanding stents (aged) |
7.3 Microstructure and Processing in Co-Cr Alloys
7.3.1 Grain Refinement
Grain refinement can be used to strengthen metallic materials while maintaining their ductility. It is known that ultrafine grains smaller than 1 μm have been produced by severe plastic deformation; however, the severe plastic deformation techniques have not been applied to Co-Cr-Mo alloy parts because of their dual-phase microstructure and the strain-induced martensitic transformation during plastic deformation from the γ-phase to the ε-phase [21].
The grain refinement of Co-Cr-Mo alloys using conventional hot-compression deformation [21] and reverse transformation [22] has been reported. Yamanaka et al. [21] reported an ultrafine-grained microstructure with a grain size of around 0.6 μm obtained by the conventional hot-compression deformation of Co-29Cr-6Mo alloy with low carbon and low nitrogen contents. This microstructure was formed by dynamic recrystallization at 1,323 K under a strain rate of 0.1 s−1 from an initial average grain size of 40 μm. It was suggested that this fine microstructure was a product of the inhomogeneity in the local strain distribution induced by planar slips and deformation twins due to the lower SFE of this alloy at elevated temperatures [23]. A Co-29Cr-6Mo alloy with an average grain size of 0.8 μm produced by hot-compression deformation exhibited a significantly high 0.2 % proof strength of 1,330 MPa [24]. Kurosu et al. [22] developed a grain refinement process based on the reverse transformation from a lamellar (hcp ε-phase + Cr2N) phase to an fcc γ-phase for the Co-27Cr-5Mo-0.16N alloy. Their process consisted of a two-step heat treatment without a hot or cold plastic transformation: solution-treated alloy was subjected to isothermal aging at 1,073 K for 90 ks to form a lamellar structure consisting of the hcp ε-phase + Cr2N, and then the aged alloy with the complete lamellar microstructure was reverse-treated at a temperature of 1,273–1,473 K. The temperatures of 1,073 K and 1,273–1,473 K are in the stability regions for the ε -phase and γ-phase, respectively. The average grain size was reduced from 200 μm initially to 20–25 μm. Figure 7.4 shows the stress-strain curves of the Co-27Cr-5Mo-0.16N alloys after solution treatment (ST), aging treatment (AT), and reverse treatment (RT) at 1,273 K for 300 s [22]. The tensile strength was improved by the reverse transformation, while the ductility remained almost the same.
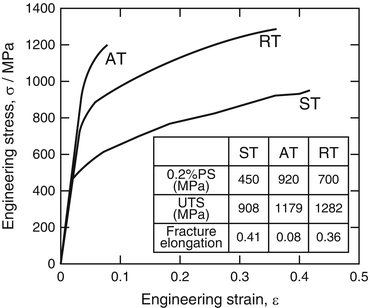
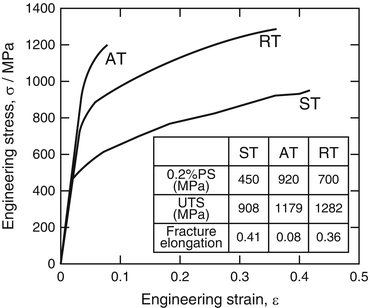
Fig. 7.4
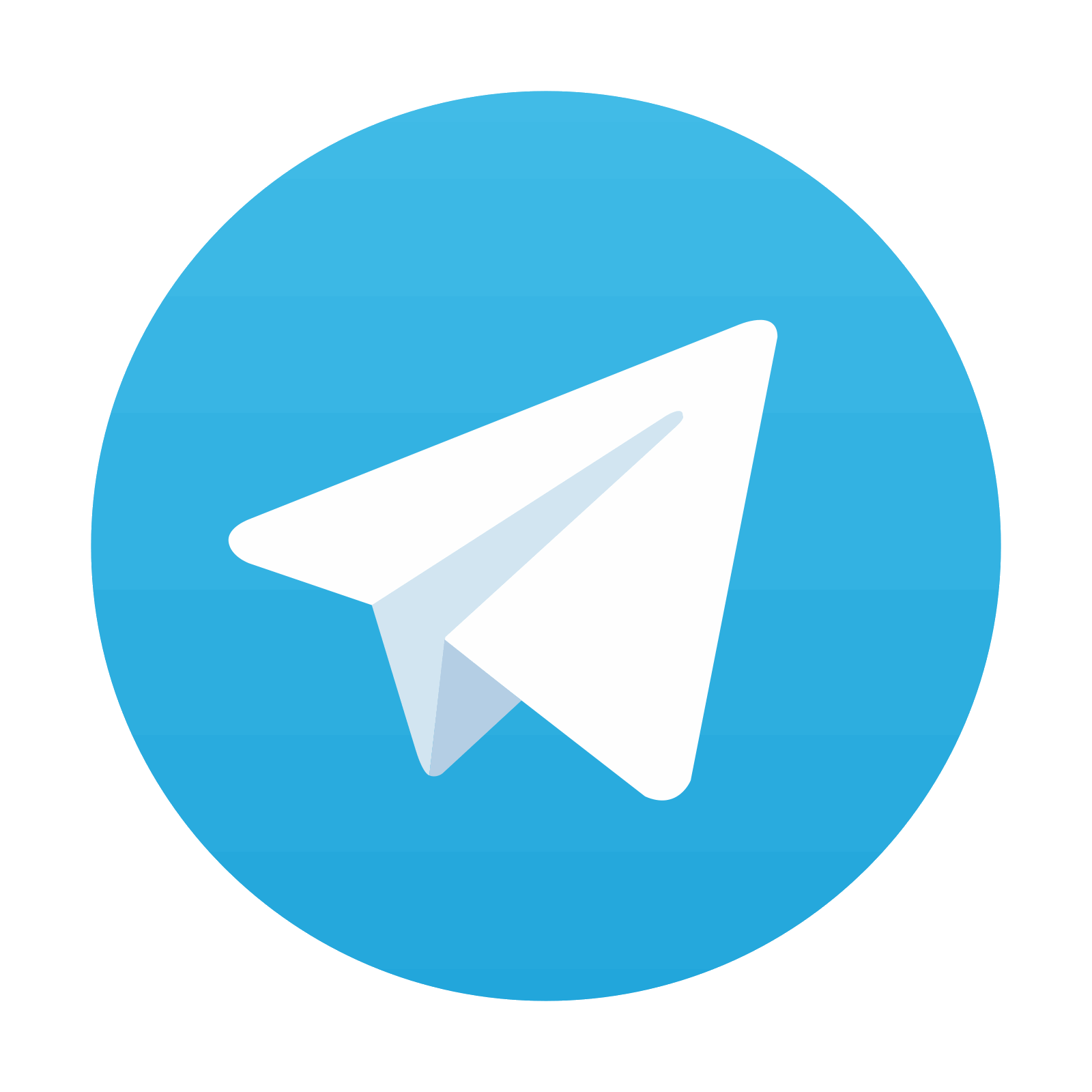
Stress-strain curves of the Co-27Cr-5Mo-0.16N alloys after solution treatment (ST), aging treatment (AT), and reverse transformation (RT) at 1,273 K for 300 s. A table of the mechanical properties for each specimen is shown as an inset in the figure (Reprinted from Ref. [22], Copyright 2010, with permission from Elsevier)
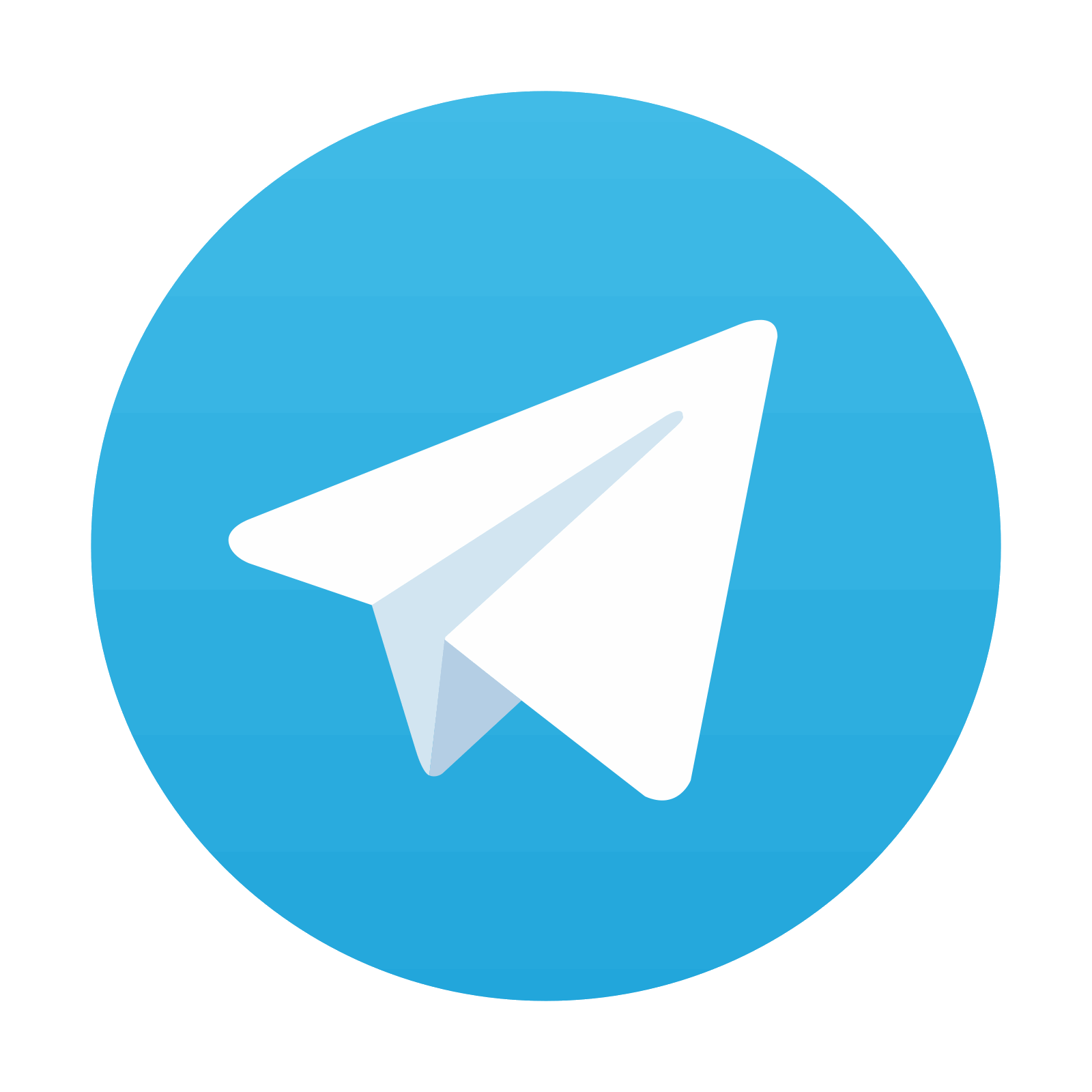
Stay updated, free articles. Join our Telegram channel
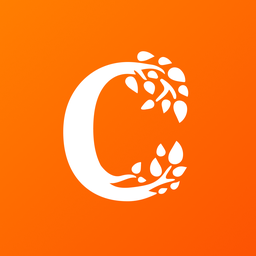
Full access? Get Clinical Tree
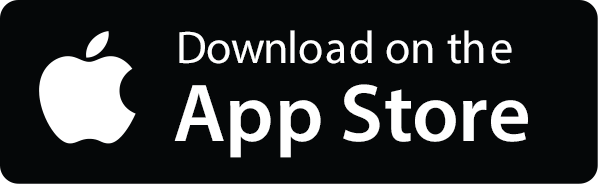

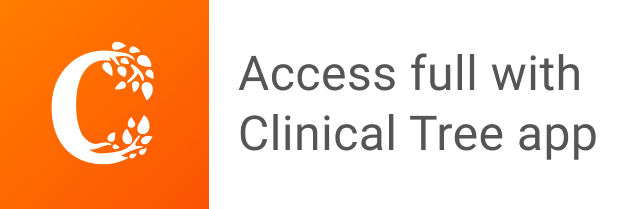