Figure 4.1Photograph of the Technophar capsule manufacturing machine.
Hard capsule shell manufacturing remained almost exclusively in the United States from the 1880s until after the Second World War. Eli Lilly Co. and Parke, Davis & Co. were leaders in this field; both opened plants in the United Kingdom in the 1950s; during the 1960s, between them, they built further plants in Europe in France, Belgium, Italy, and Spain and then in other parts of the world: Mexico, Argentina, Australia, and Japan. Since then, manufacture has become a global industry, with large companies established in India (www.acg-associatedcapsules.com), China and South Korea, and numerous smaller companies in Asia, Europe, and North and South America.
Capsule Shell Design
The standard shape for a hard gelatin capsule was established by Lehuby in his original patent. From then until the 1960s, except for a few minor exceptions, capsule design remained unaltered. This changed with the introduction of automation for filling and packaging products; handling stresses applied to filled capsules increased and they came apart shedding their contents: the need for a “self-locking” capsule to prevent reopening became a requirement. Previously, capsules were held together by powder trapped in the overlap between cap and body formed to the machine filling process. Automatic machines filled soft plugs of powder into capsules; powder was no longer present in significant amounts in this overlap. The first patent for a “self-locking” capsule in the modern era was granted to Eli Lilly & Co.5 Their Lokcaps capsule had a circular indentation on the inside of the cap, and when the capsules were closed together after filling, this formed an interference fit with the body, increasing the force required to separate the two parts. However, capsules could not be fully closed during manufacture because the filling machines were unable to separate them. Lilly overcame this problem by adding two small rectangular indentations on the inside of the cap on opposite sides about halfway along the cylinder, called “Preloks.” These held the capsule parts together, now closed to a longer length, when they were empty; avoiding separation problems during handling and transfer from manufacturer to capsule filler. Parke, Davis & Co. followed this lead later in the 1960s with the introduction of Snapfit capsules.6 These had two oval pre-lock indentations on the cap and two circular locking features, one on each half. The body indentation was located on the outside close to its cut edge and the cap one was located on its inside surface close to the domed end, which provided a positive closure. The problem of filled capsules coming apart was increased by the speed automatic filling machines closed filled capsules; bodies entered into caps faster, resulting in more air trapped inside, increasing the internal pressure, and on storage, caps could be “blown” off their bodies. Air vents had to be included in the pin design. Eli Lilly solved the problem by introducing three lands, nonindented areas, in the circular cap groove.
Most manufactures have designed their own pins and all provide for the same set of functions. The features required are as follows: to hold empty capsules together to prevent separation on handling, to aid the entry of the body into the cap, to allow air to escape during re-closure after filling, and to hold the cap and body together after filling, (see Figure 4.2). Initially, there were two pre-lock features on capsules and it was observed that this tended to make the cap less round. Manufacturers now use multiple pre-locks, four or six, placed symmetrically round the cap, thus maintaining its circular shape. Air vents have been placed in various positions in both cap and body. Cap circular indents with unindented spaces (Eli Lilly) and on the bodies flat areas are molded on the outside surface from the cut edge crossing any circular indents (Parke Davis): both of these features provide channels for air to escape during capsule closure. The clearance between the body and the cap is very small, and rejoining the cap and body together after filling needs careful control. For good closure, the cap and the body must be in perfect alignment, and anything that prevents this must be countered. If not, the body will come into contact with the cap edge and a sliver of shell wall will be cut, which passes up the outside of the cap. This fault, in capsule makers’ jargon, is called a “telescope,” which is a totally wrong analogy, and would be better described as a “bad or incorrect join.” It is a fault seen during capsule filling. Capsule shells have flexible walls and thus the open ends of caps and bodies can become slightly distorted, caused by poor storage or handling. The filling process also plays a part because if loose powder is present in the capsule bushings, the cap might not be seated correctly, resulting in them being tilted enough to contact the body edge. This coupled with wear of the bushings will cause this fault. Capsugel made a capsule, the Coni-Snap, which had a chamfer at the open edge of the body, reducing its effective diameter and making it easier for the body to enter the cap, thus reducing problems caused by worn bushings.7 Elanco Qualicaps added a circular indentation close to the open end of the cap to maintain the circularity during closure.8 The common practice for circular locking feature is to have them on both the cap and the body to provide an interference fit that increases the force to separate them to a level above those to which filled capsules are subjected to during handling.

Figure 4.2Drawing of a hard capsule showing the features that have been used by various manufacturers in their own preferred arrangements.
Manufacture of Hard Gelatin Capsule Shells
This section describes the process used for gelatin. Other polymers are used and the differences in their processing behavior will be discussed in the “Gelatin Alternatives for Hard Capsule Manufacture” section.
Preparation of the Manufacturing Solutions
The first task is to make a bubble-free concentrated solution of gelatin. The simplest way to dissolve gelatin is to soak it in water at 15°C, allow it to swell and fully hydrate, and warm it to above 35°C when it will dissolve and produce a bubble-free solution. On an industrial scale, this is not a practical process because among other factors, the microbial quality of solutions could be compromised. Gelatin solutions are a good substrate for bacterial growth at ambient temperatures. In the past, preservatives such as methyl and propyl parabens and sodium metabisulfite were added into gelatin solutions to control microbial levels during production. They played no role in finished capsules because the water activity at their moisture content of 13–16% was insufficient to maintain bacterial growth.9 Currently, preservatives are not used in gelatin capsules manufactured in Europe, and in the United States, they are only used in older products that were registered some time ago. Problems can also be avoided if the temperature of gelatin solutions is maintained at ≥45°C. The process conditions are set to maintain this temperature all through the process and equipment is designed to avoid any cooler spots. This maintains the microbial quality to the same level as the incoming gelatin.
Gelatins used are usually purchased from more than one supplier against purchasing specifications that specify in addition to standard pharmaceutical chemical and microbial purity levels two factors specific to capsule manufacture, viscosity and Bloom strength, a measure of gel rigidity.10 Gelatins are used as single lots or blended with other lots to achieve the required quality. Solutions are prepared in large stainless steel water-jacketed pressure vessels. These are first charged with hot demineralized water at about 70°C. Gelatin is fed into the top of the tank usually by an air transport system. The concentration of gelatin is between 30% and 40% w/w. The tanks are stirred for several hours to dissolve the gelatin. When it is all dissolved, the resulting solution contains air bubbles caused either by the mixing process or by the raw material gelatin that during processing after extraction is extruded through a votator to produce small hollow tubes, which are broken up during final milling. To remove these, a vacuum suction is applied to the tank and the bubbles rise to the surface. In hot solutions, gelatin hydrolyzes with time and its Bloom strength and viscosity values fall; thus, the rate of usage on the manufacturing machines governs the lot sizes that can be manufactured.
When the solution is ready, aliquots of solutions ≥25 L are dispensed from the tank in to suitable sized containers and prepared for delivery to individual machines. First, measured quantities of dye solutions and pigment suspensions, as required to produce the correct capsule color, are added to the vessels and various process additives, such as sodium lauryl sulfate, a USP permitted wetting agent, or colloidal silicon dioxide, a substance to modify the surface structure of the film and thus reduce its frictional properties. This latter additive has been listed as a component of capsule shell formulations in products registered by the European Medicines Agency. The solution is carefully mixed with a suitable stirrer, to ensure that no air bubbles are produced. The viscosity in the individual vessels is then measured using a viscometer, usually an electromechanical one with a rotating cylinder, and the calculated amount of water is added to adjust the value to that required for the lot of capsules concerned. The target viscosity is dependent on the capsule size and whether it is for cap or body. Once the machine has been started up, subsequent deliveries to the machines have lower values than the original one made for machine setup as water is lost by evaporation during the process. Prepared solutions in their vessels are sometimes referred to as “pourings.” These are delivered to the machines at regular intervals and transferred into larger water-jacketed holding vessels from which the solution is fed into the dipping container via a pipe that has a valve to regulate flow. The amount is controlled by a level sensor in the dipping container. This is a large rectangular water-jacketed vessel, inside of which is a second smaller open-top rectangular box. This is called the dip pan or dip pot. Gelatin solution is pumped up through the central box and overflows the edge, returning to the bulk of the solution below. This simple device ensures that the level of the solution in the central section is always the same during the dipping process. Baffles in the central box ensure gentle mixing of the solution as it passes through. In the outer area, at the entry end from the feeding tank, there is usually an electromechanical rotating cylinder viscometer measuring the solution viscosity. This is connected to a control system that adds hot demineralized water to keep the solution viscosity within the target limits. The viscosity of the system is always run on the slightly high side so that only water needs to be added to maintain control and not concentrated gelatin solution.
Formation of Hard Capsule Shells
The capsule manufacturing machines are housed in a carefully controlled environment: the humidity and temperature are controlled to ± 0.5% relative humidity (RH) and 0.5°C, respectively, and the air is circulated at a rate of 8 to 10 changes per hour. The process for forming hard capsules starts at the front end of the machine11 (see Figure 4.3). Stainless steel molds, commonly known as pins, are mounted 30 in a line on metal bars. The shape of the mold pin is cylindrical with a hemispherical end; the shaft has a taper along its length toward the end of 0.1–0.3 mm cm−1: this makes it easier to remove the dried films from the pins. Sets of pin bars, ≥5, are assembled in a rack above the dipping area and then are dipped into the gelatin solution. Mold pins are at about 22°C and the solution is at about 45–50°C. The mold pin temperature is lower than the gelling point of the solution. When this contacts the mold pins, it changes state from a sol to a gel, forming a homogeneous film on their surface. The set of pin bars is slowly raised out of the solution and any ungelled solution drains off (see Figure 4.4). The rate of drain-off of the wet film is directly proportional to solution viscosity. The amount retained on the pin is directly related to the solution viscosity. The higher the viscosity, the greater the amount retained on the pin. This is used to control the thickness of capsule shells. When the mold pin emerges from the surface of the solution, a string-like connection forms between the pin base and the solution surface: with further movement, it gets thinner (i.e., necking), until it eventually breaks, leaving a blob of gelatin on the end of the pin. Pin bars are then rotated end over end as they are transferred from the dipping area to the upper deck of the machine. As this happens, the gelatin on the end of the pin flows to form a more uniform film. Cool air is blown over the pins to complete the gelling of the polymer. When the mold pins arrive on the top deck, they are now at 180° from their dipping orientation and the film is set. Pin bars are now assembled in groups, and when the table is full, this set is pushed though the drying kilns toward the rear of the machine. When sets arrive at the rear of the machine, there is a transfer elevator that lowers them down to the lower level where they are pushed forward toward the front of the machine through the remaining kilns.

Figure 4.3Outline of the hard capsule manufacturing process.

Figure 4.4(See color insert.) Photograph of pins after dipping being withdrawn from the dip pan.
The sets of pins bars as described above are passed through four or five separately controlled drying kilns in which large volumes of air at a controlled temperature and humidity and variable flow rates are directly blown over each pin. The wet films after dipping have a moisture content of about 70%, and about 80% of this needs to be removed before they emerge from the drying kilns. The air in the kilns is at different temperatures, between 0°C and 4°C above ambient conditions in the machine room. At the start of the drying process, not too much heat can be used; otherwise, the films would revert to the sol state. The temperatures later in the process are controlled so that when the mold pins exit from the kilns, they are back at 22°C, ready for the next cycle.
When the dried films emerge from the kilns, their moisture content is 15% to 18%, which is higher than the standard for empty gelatin capsules of 13.0% to 16.0% w/w. This is to enable the dried films to be easily stripped off the mold pins. There is an open area after the sets of pin bars exit the last kiln. The next part of the machine is often called the “automatic section.” Before entry to this, a pair of cap and body pin bars are selected, lifted up, tipped onto their sides, and pushed into slots into the center of the automatic section. Sets of metal jaws with softer metal inserts in the open position are pushed over the mold pins. The jaws are closed and pulled backward, and in doing so, the dried films are pulled off the pins, transferring them into a matching set of four-leaf collets. The end of the film protrudes from the collet. The jaws move away and the collets are closed so that they grip the dried films. Situated above the open end of each set of collets is a knife holder with one knife for each collet. The knife bar is lowered and the collets revolve against the tip of the knife blades, cutting each capsule part to the correct length. The pieces cut off are thin and feathery and are sucked away to a collecting device. This material can be recycled.
Gelatin is a very tough material and needs a very sharp blade to cut it. These knives were originally made of steel and various grades of toughened material have been used to try and improve their performance and time between requiring sharpening. Diamond tipped blades, which cut films very well, were used at one time but proved impractical because they were very brittle and easily damaged. One of the best solutions to date has been the use of ceramic knives. These are made from the ceramic that was developed to make the heat shield tiles on US space shuttles. It is a robust material and knives made of it retain their sharpness longer than those made from other materials, giving them an increased production life.
Cut films are now pushed by rods out of the collet holders into a central joining block. The caps and bodies are joined together to form a capsule. They are closed to a specific value, the unclosed joined length, which is a position where the pre-locking features (but not the locking ones) are engaged (see the “Capsule Shell Design” section). After this, capsules are ejected from the block onto a moving conveyor belt that delivers them to a container at the machine exit.
Pin bars pass on to the next part of the machine where the mold pins are cleaned and lubricated with mold release aid. In order to be able to easily strip dried films off mold pins, it is essential to apply a release aid to their surface. The formulation for the release aid is propriety to each manufacturer and is made from food-grade materials and is listed in the manufacturer’s DMFs. As the pin bars are moved to the cleaning section, a small amount of lubricant is applied to each mold pin as it passes either from a brush or from a revolving foam disc. Mold release aid is stored in a pressurized system and a pump controls the amount that is dispensed. Pins are next inserted into metal holders containing felt pads that are rotated to spread the mold release aid uniformly around them and to remove any particles on their surface. Pin bars are then assembled in groups and positioned above the dip pan for the cycle to be repeated. The cycle time is about 45 min and machines normally run 24/7.
To maintain production under control, machine operators take samples at regular intervals and check dimensions: the thickness of the shell wall near the cut open end of the capsule parts and at other places along the length of the capsule particularly at the domed end, cap and body lengths and diameters, and the unclosed joined length. Measurement gauges are now typically connected to computers, and these data are tracked and trends are displayed. These data can be used for machine validation, significantly reducing the time taken for this task.12 This allows the machine to be controlled automatically or used by operators to make manual adjustments. Samples are also inspected for visual defects and color.
Capsule Sorting
The empty capsules go through a further series of processes in order to meet customer requirements: sorting, printing, and packaging.11
Capsules on leaving the machine are passed through various sorting devices in order to remove defective capsules. First, a simple mechanical device is often used, which consists of a honeycomb plate with holes the diameter of which are made so that capsules of the correct size will readily pass through and any damaged ones are retained on the plate and can be removed. Capsules with visual defects can be removed either by manual sorting on inspection belts or by the use of electronic optical devices of varying degrees of sophistication to inspect capsules individually at high speeds either by spinning them in a beam of light or by equipment with digital cameras, which use image analysis software.
Capsule Printing
In the United States and Europe, most capsules are printed by the capsule shell manufacturer with a variety of information required by their customers’ pharmaceutical and nutraceutical companies, to help identify the product and other information such as the name and/or dose of API and the name of the manufacturer. Capsules are printed on machines based on the standard off-set printing process using edible inks11 (see Figure 4.5).

Figure 4.5Photograph of the Qualicaps printing machine.
The off-set printing process uses a reservoir that holds the printing ink. A cylindrical metal roto-gravure cylinder has the information to be printed (acid etched) onto its surface. This cylinder revolves in the reservoir of ink. A piece of metal with a straight edge, called a doctor blade, which is the same length as the cylinder, is in contact with it and excess ink is scrapped off. Next to the metal cylinder is a rubber off-set roller of the same dimensions and the two revolve in contact with one another. Ink in the etchings is transferred from the metal cylinder onto the rubber roller. Empty capsules held in a conveyor pass under this roller and contact it at a point where ink is transferred onto them.
Edible ink used in this process is mostly based on shellac. This is a natural polymer obtained as exudates from an insect, Kerria lacca (Coccideae), and is collected from trees in India and South Asia.13 These insects live on trees and feed by sucking nourishment from them. They exude the raw shellac onto the branches where it dries; pieces are collected, liquefied by heat, and filtered to remove pieces of bark and insect parts. It is also known as “confectioner’s glaze” and is widely used in the food industry. Solutions of 40% shellac in organic solvents are used as the base for ink manufacture.11 Organic solvents are used because the ink has to dry rapidly because the time between it being applied to capsules and their exit from the machine into a container is very short. If the drying is incomplete, ink will be transferred to other capsules, making unsightly marks on their surfaces. Mixtures of solvents are used to obtain the required drying rates. The solvents used are governed by regulations that have been harmonized through the International Conference on Harmonization (ICH), which rates solvents into three toxicological classes ranging from ones to be avoided to those with low toxic potential.14,15 Solvents in each class have been assigned a permitted daily exposure (PDE) limit. The level of residual solvents remaining in capsules is extremely low as the amount of ink applied to a capsule is on the order of 1 to 3 μL and the solvents are lost as the ink dries. Inks are colored using pigments, iron oxides and titanium dioxide, and the lake form of soluble dyes. High concentrations of pigment are used in order to produce relatively stable suspensions. Other additives are used to improve the functionality of the inks such as additional suspending agents, hypromellose (required to maintain the consistency of color throughout a run), and surface active agents, such as dimethicone and lecithin, to improve the fill of the etchings and its transfer to the rubber off-set roller.
A range of ink colors is used, but the palette is much more limited than for the colors used for the hard capsule shells. The reason for this is that the print designs mostly consist of very narrow lines as large areas of ink are not good practice because chance of its transfer to other capsules increases. The human eye is less capable of distinguishing between colors of fine lines against another colored background and hence only basic colors tend to be used.
Print can be applied to the capsules in a number of ways, either axially or radially. The surface area that can be covered depends on the hardness of the rubber transfer rolls: the softer the role, the greater the potential coverage. The printing machines can rectify the capsules before printing so that specific information can be printed on caps and bodies: if not rectified, the print placement will be randomly assigned, if two designs are used. Advanced machines have systems that enable two different colors to be printed on a capsule.
Packaging and Storage
Empty hard capsules have to be packaged for shipment to customers unlike the soft capsules that rarely exist as an empty entity. Manufacturers pack their products into cardboard cuboid outer cartons with the capsules sealed inside an inner liner that is preferably heat sealed: the material of the latter ranges from polythene to aluminum foil laminates.11 The choice is governed partly by the environmental conditions the packages are exposed to in transit from the shell manufacturer to the capsule filler and cost constraints. The packages are designed to maintain the moisture content of the capsules within their moisture content specification: for gelatin capsules, most manufacturers use a limit of 13.0% to 16.0% w/w. Empty capsules gain and lose water depending on the conditions to which they are exposed, and this causes a slight change in dimensions. For gelatin capsules, a simple rule-of-thumb calculation is that between 13% and 16% for every 1% change in moisture, there is a 0.5% change in dimensions. The packages as received from the manufacturer should not be opened until they are about to be used. This is particularly important for heat-sealed packs as resealing facilities are often not available at sampling points. Quality requirements can be met if the manufacturer sends separate sealed samples to the purchaser following supplier audits and approval.
The most important factors in storing empty capsule packages are to avoid extremes of temperature and humidity. The ideal conditions are between 15°C and 30°C, and care should be taken to maintain them at an even temperature. Temperature fluctuations will cause moisture movement inside a sealed container and, in the worst cases, could cause distortion and failure to separate on a filling machine. A potential problem often overlooked in warehouses is that capsule packages are comparatively light for their size and, as a result, are often stored at high levels on racking systems. In the rooves of warehouses, there are often space heaters or windows, which are heat sources that could cause localized heating inside a carton and moisture migration within the package.
Hard Capsule Quality
Capsules are produced on machines that operate 24/7, and like all such industrial processes, there will be a small proportion of defective capsules produced. Over the years, there has been a continuous improvement in the quality of capsules. This process has been mainly driven by the development of higher-speed capsule filling machines.16 Up to the mid-1960s, the machines used were semiautomatic or manually operated. The operator had time in which to rectify capsule faults as the machine was running without having to stop it and filling was almost continuous. The introduction of automatic machines highlighted these capsule quality issues because they needed to be stopped to rectify blockages or other faults, and while this was being done, no capsules could be filled.
For systems that have defect levels at low levels, statistical sampling plans based on probability theory are used to reduce sample size to give an acceptable level of control. To make plans more specific, three types of capsule faults are defined: Major A, Major B, and Minor, which are sometimes named as Critical, Major, and Minor17,18 (see Tables 4.1 through 4.3). Major A faults affect the capsule as a package for the final product or could cause a major filling problem; Major B faults cause problems on a filling machine; Minor faults are slight surface blemishes that make them visually imperfect but do not affect the performance of capsules as a package or cause filling machine problems. Each type of fault is assigned an acceptable quality level (AQL), which is defined in Military Standard MIL-STD-105E18 as the maximum percent defective that for the purposes of sampling inspection can be considered satisfactory as a process average. A typical set of AQL values used by capsule manufacturers are Major A 0.010%, Major B 0.040%, and Minor 0.25%. In the past, a lot of time was spent in the visual inspection of capsules. However, it was realized that quality levels are not improved by this and that the way for the manufacturers to improve quality has been by concentrating on the parts of the process that produces them so that they could be eliminated by improving machine design and/or maintenance schedules.
Cracked | Body or caps with many splits |
Double cap | Capsule with additional cap covering body |
Double dipping | Extra thick cap due to double dipping |
Failure to separate | Cap and body may not separate properly |
Hole | Irregular opening in cap or body |
Joined in lock | Capsule in locked position |
Long cap/body | Length cap or body 1 mm more than specification |
Mashed | Mechanically damaged, squashed flat |
Pinched | Cap or body damaged in collets, pinch > 3 mm |
Short body | Length 0.4 mm less than specification |
Short cap | Length 1 mm less than specification |
Split | Split in wall starting from cap or body edge |
Telescope | Closed capsule with protruding piece of cap or body |
Thin spot (shoulder) | Thin area, may rupture when capsule filled |
Trimming | Whole or piece of trimmed end cap or body inside capsule |
Uncut cap/body | Untrimmed cap or body |
Unjoined | Single cap or body |
Damaged edge, large | Cap edge poorly trimmed, >1 mm into length |
Dye speck | Colored spot of pigment, different from cap or body color |
Grease | Visible spots of mold release aid on inside of capsule |
Inverted end | Cap or body with end pushed inward |
Long joined | Capsule not closed enough to engage prelock |
Pinched (small) | Cap or body damaged in collets, pinch < 3 mm |
Thin spot | Thin area cap or body wall may rupture when capsule filled |
Turned edge | Folded over edge on body cut edge |
Black speck | Noncontaminant black spot |
Bubble | Air bubble in cap or body wall, with diameter > 0.4 mm |
Chips, tails, string | Small fragments of shell, still attached to wall or free |
Crimp | Collet damage, outside cap or body < 3 mm |
Damaged edge (small) | Cap edge poorly trimmed, damage V shaped, < 1 mm into specification |
Dent | Depression in end cap or body, < half diameter of part |
Grease (light) | Small spots of mold release aid on inside of capsule |
Scrape | Scratch mark on surface of cap or body |
Starred end | Multiple small imperfections of ends of cap or body |
To understand why faults are produced, it is necessary to understand how each is caused. The first part of the process is mold dipping and faults produced are as follows: Major A, thin spot; and Minor, bubble and speck. A thin spot can be attributed to either a poor distribution of the mold release aid on the pin or insufficient wetting agent being present, both resulting in an uneven coverage of the pin with a wet film of polymer. A bubble in the shell wall is attributed to one being present in the solution in the dip pan. The removal of air bubbles from this solution is a critical part of its manufacturing process, and when it is dispensed from the stock manufacturing tanks, it should be free of them. However, bubbles could be reintroduced during the addition of colorant solution or pigment suspension to this stock solution. All the mechanical operations by parts of the dip pan are designed to ensure that air entrapment is reduced to the bare minimum. A colored speck is most likely to occur as the result of small fragments of shell walls generated during the trimming process getting into the dipping area. The next part of the process is film drying and faults caused are as follows: Major A, split; and Minor, starred end. A split in a shell starts from the cut edge of the cap or body and spreads away from this point. It is caused by uneven drying or an uneven film thickness at that point. A starred end is produced when there is an excessive amount of gelled solution on the end of the pin. When the mold pins emerge from the drying kilns, they pass to the automatic section. The first operation is removal of dried films from the mold pin and faults caused are as follows: Major A, hole, caused by the stripper jaws touching the shell as it moves forward to strip it off and is attributed to mechanical problems or a poor machine setup. The second operation is the transfer of shells to the split leaf collets and faults caused are as follows: Major A, short body, large pinch > 3 mm; and Major B, minor pinch < 3 mm. A short body is caused by insufficient entry into the collet and pinches are caused by a section of the film becoming trapped in between the leaves of the collet as it is closed. This could be attributed to a drying problem, that is, a wetter area of the shell or a mechanical problem with the collet. The third operation is the cutting of the dried films to the correct length and faults caused are as follows: Major A, short body, uncut body, uncut cap; and Major B, short cap, long cap, long body, damaged edge (cap). The short cap and body are caused by insufficient penetration of the dried film into the collet for the position of the knife, the long cap and body are caused by a missing knife or a broken knife, and the damaged edge (cap) is caused by a blunt knife. The fourth operation involves joining of the two parts together and the faults caused are as follows: Major A, bad join (telescope), cracked, mashed, trimming; Major B, inverted end; and Minor, dent. The first three Major A faults are caused by mechanical problems in the joining block, the first by a misalignment of the cap and body parts and the other two by capsule parts being incorrectly transferred and the push rods distorting their shapes or breaking pieces off. The trimming inside a capsule happens if there is a problem with the extraction system to remove them or with the cutting operation and it becomes trapped in the body. Major B and Minor faults are lesser problems of the previous explanation where shells are unable to move sufficiently in the joining block and their end is dented. After being ejected from the joining block, the capsules pass along a moving belt, exit from the machine and pass through inspection systems and printing machines, and are packed for transport. During this process, faults caused are as follows: Major B, unjoined and double cap; both of these are symptoms of the same problem, with the cap separating from the body because they were joined to longer than their correct unclosed length in the joining block, and if this loose cap fits over the body of another complete capsule, a “double cap” is produced.
Modern Hard Capsule Manufacturing Machines
There are currently few specialist manufacturers who make the associated equipment used in hard capsule manufacture or supply the machinery, for example, Technophar Equipment and Services Ltd, part of the Qualicaps group (www.technophar.com), in Canada and Safrroys Machines Pvt Ltd (www.safrroys.com) in India.
The limitations to increasing the speed of output of the process are twofold. First, there are the mechanical problems of moving sets of pin bars around the machine and the precise coordination of this with the other mechanical activities such as cutting the dried films and assembling the two parts. Second, limitations are attributed to the properties of the polymers used. Drying is a significant part of the process, and typically in other fields of manufacture, to reduce drying times, higher air temperatures are used. This cannot be used in this case because at the start of the process, higher temperatures will cause the films to revert to the sol state and move out of shape and the mold pins have to be back to their dipping temperature when they have completed the cycle around the machine. There is also a limitation to the speed of drying because if it is too rapid, there will be case hardening of the surface of the films that would slow the drying process.
Mechanical problems have been overcome by changing the methods of moving bars through the drying kilns from mechanical pushers to hydraulic systems controlled by servo-motors, which can be better controlled and prevent the bars rising up over the sets in front causing a jam. As the machine speed increases, the next part of the process to cause a bottleneck is the automatic head where the shells are stripped from the mold pins and trimmed to the correct length. This has been solved by installing two automatic heads on a machine to cope with the extra throughput of pin bars.
The limitation of the maximum speed at which capsules can be dried has been solved by changing the machine design by increasing the lengths of the drying kilns and hence the overall length of the machine. This increases the passage time of the molds through the kilns, allowing the correct drying conditions to be maintained.
The original machine design of Colton relied on the use of cams to perform certain movements of the pin bars, such as during dipping or the spinning of the bars after this when they are transferred to the upper deck of the machine. Cams work well but are inflexible, because if changes are required, new cams need to be machined, which is a time-consuming process. Technophar has solved this by using servo-motors with computer control: these enable the process to be easily changed to accommodate any variations in material properties.
Gelatin Alternatives for Hard Capsule Manufacture
Gelatin has been the material of choice since it was first mentioned in an addition to Lehuby’s patent in 1848. However, since that time, there has been a search for an alternative material for both types of capsule, prompted first by the need to avoid existing patents, and second to find a material that had more reproducible properties than gelatin made from natural materials and more recently to improve on the pharmaceutical properties of gelatin to meet current demands. Gelatin alternatives must possess similar properties, must be widely acceptable for use in foods and medicines, must gel on a mold pin to film caused by a temperature change to enable the same manufacturing machinery to be used with minor modifications, should be stable and nonreactive, and must have similar in vivo release properties. A variety of substances have been used: hypromellose, methyl cellulose, and pullulan.
Cellulose compounds have been used the most and solutions of these do not gel when they are cooled. To convert them into a gelling system, two methods have been proposed, either by including network-forming additives in the polymer solution or by modifying the process to use different temperature conditions to form a film by thermal gelling of the solution.
Eli Lilly & Co. was the first large-scale manufacturer of a non-gelatin hard capsule in the early 1950s.19 They utilized a property of cellulose solutions, the viscosity of which increases as the temperature rises (so-called thermal gelling). They reversed the conditions used for the standard process. Hot mold pins at c. 65°C were dipped into methyl cellulose (low viscosity grade) solutions at temperatures <20°C. Film formed rapidly on the pins, which were then transferred to drying kilns; in the first section, the temperature was 40°C and progressively rose to 60°C. The air was heated by infrared lamps and the transit time was about 50 min. The capsules were allowed to cool to ambient conditions before they were stripped from the pins. They were in widespread use for several years, sufficiently long enough for US Federal Specification 285A20 to introduce a test to distinguish them from gelatin capsules: “Water resistance,” in which a capsule should show no signs of disintegration when immersed in purified water at 25°C ± 1°C for 15 min. Under these conditions, only methyl cellulose capsules will dissolve, readily distinguishing them from gelatin ones. These capsules were withdrawn from use later in the 1950s after in vivo tests showed that capsules did not dissolve in the stomach if a patient was suffering from hypochlorhydria (lack of acid).
From the late 1980s onward, most of the work has centered on the use of hypromellose, which is widely used by the pharmaceutical industry for tablet coating and formulating tablets with prolonged-release properties. The first company to propose a successful solution was Japan Elanco (Qualicaps), which started a study in the late 1980s to try and produce hard capsules that did not have the same drawbacks as gelatin ones, namely, their high moisture content and brittleness when dried.21 They used hypromellose and converted it into a gelling system by the addition of carrageenan, which is a network former, and potassium chloride, which is a network promoter.22,23 The capsules were made on standard machines and were demonstrated to be less brittle than gelatin ones when stored at low humidities. The temperature of the solution at dipping was 50°C to 52°C and they commented that the speed of gelling was slower than that for gelatin. The properties of the capsules were improved by using blends of lower-viscosity hypromellose, and the disintegration time was satisfactory even in the presence of calcium ions, which form a strong network with carrageenan.24 In a further improvement, they modified the method of dissolving hypromellose.25 It was dispersed it in hot water at 65° to 80°C and then allowed to cool to room temperature to allow it to dissolve. The solution is then reheated to bring it to the machine dipping temperature. Solutions of carrageenan and potassium chloride were added to it either at the start of warming or when the solution has reached the correct operating temperature. This procedure improves the gelling properties of solutions, resulting in improved control of capsule formation.
Capsugel proposed an alternative gelling for hypromellose capsule production. They proposed the use of various gums as a gelling agent, gellan being the preferred one, and a sequestering agent such as ethylenediaminetetraacetic acid or citric acid and their salts as the gel promoter.26 This solution was used in the standard hard capsule manufacturing process. In further patents, they improved the process by using a heating and cooling method for the preparation of the hypromellose solutions before dipping.27 Hypromellose powder and solutions of the various additives were added to water at 70°C; this was stirred to mix, with the speed of the mixer reduced to allow air bubbles to be removed, and then allowed to cool to 47°C with constant mixing. This process resulted in a solution with the correct viscosity for mold pin dipping in the temperature range of 43° to 48°. If the solutions were not stirred during cooling, the solution viscosity would be too high to form capsule shells of the correct dimensions.
G.S. Technologies applied the hot mold dipping technique for the production of hypromellose capsules and were granted patents for modifications to a standard Colton-type machine.28,29 They were able to realize the following: a method to heat pin bars to different initial temperatures to compensate for the difference in time between leaving drying kilns and entering the automatic section before dipping; a method to heat pins after dipping to aid film formation; a method to dry wet films on pins by first using humid air to slow the rate of drying and then less humid air to dry them down in closed kilns to avoid air escaping in to the machine room; a method of heating mold pins to dry films from the inside to the outside; and a modification of the machine to increase space around the dip pan to allow for a pin reheating station using isolated heating elements below the base of the pin bars. They commented in their first patent that the capsule walls were less strong than gelatin and stripping them from the mold pins was difficult. To overcome this, they increased the wall thickness of the caps and bodies to make them stronger and reduced the mold pin diameters to make shells with the same external dimensions as gelatin ones.28 To remove the films from the mold pins, they modified the stripper mechanism to grip around the shell away from the piece to be cut off and the jaws themselves were provided with small studs to increase grip. These capsules were called Vegicaps and marketed for filling with nutraceutical products. Their literature commented that they were only suitable for running on semiautomatic machines because their dimensional control was not as good as conventional capsule shells.
Capsugel further developed the hot mold process to make pharmaceutical quality capsules, Vcaps Plus.30 Solutions of hypromellose, USP type 2906 or 2910, were prepared by dispersing 17% to 23% w/w in water at >70°C, reducing stirrer speed to allow the removal of bubbles and then cooling it to <15°C and then stirring to dissolve. Various additives that could be added at the start or at the end of this preparation process were listed. The preferable concentrations of these were 0.01% to 3.0% w/w of a plasticizer such as glycerine or propylene glycol and 0.01% to 0.5% w/w of a preservative or flavoring agent. For use, the solution was heated to between 2°C and 6°C below its gelling temperature of approximately 34°C. The standard mold pins before dipping were heated, and their temperature was dependent on the capsule size; the smaller the size, the higher the temperature: for size 4, 80°C to 90°C, and for size 00, 70°C to 80°C. The drying process was carried out in two steps. First, the wet films were exposed to temperature between 60°C and 85°C and an RH of 20% to 60% for about 2 to 4 min and then 35°C to 55°C for 30 to 60 min. During this process, the films were dried from a moisture content of c. 80% to 7% w/w.
Pullulan is the other gelatin substitute that has been used for marketed hard capsules, originally named31 NPcaps and afterward renamed Plantcaps by Capsugel.32 Pullulan is made by fermentation of tapioca by the polymorphic fungus, Aureobasidium pullulans.33 It has GRAS status and has been widely used in Japan since the 1980s. It has no setting properties, and to manufacture hard capsules, solutions require additives. The material recommended for use was desalted pullulan (Japanese pharmaceuticals excipient grade).34 The preferred hydrocolloid gelling agents were kappa-carrageenan or gellan gum at a concentration of 0.03% to 1%.35 These require the addition of a cation, and the preferred salt was potassium chloride at a concentration of 1.32%; in addition, the patent gave examples using 0.25% potassium acetate. A sequestering agent, such as ethylenediaminetetraacetic acid or citric acid and their salts, was recommended if gellan gum was used to improve the solubility of the resulting capsules. To aid the manual handling of the capsules and their performance on filling machines, a surfactant, such as sodium lauryl sulfate or sorbitan oleate, was recommended to improve their surface properties: to delay the rapid remoisturizing of the capsules when handled, which makes the capsules feel tacky, and by providing a temporary water-repellant surface to reduce the sliding friction on filling machines.36
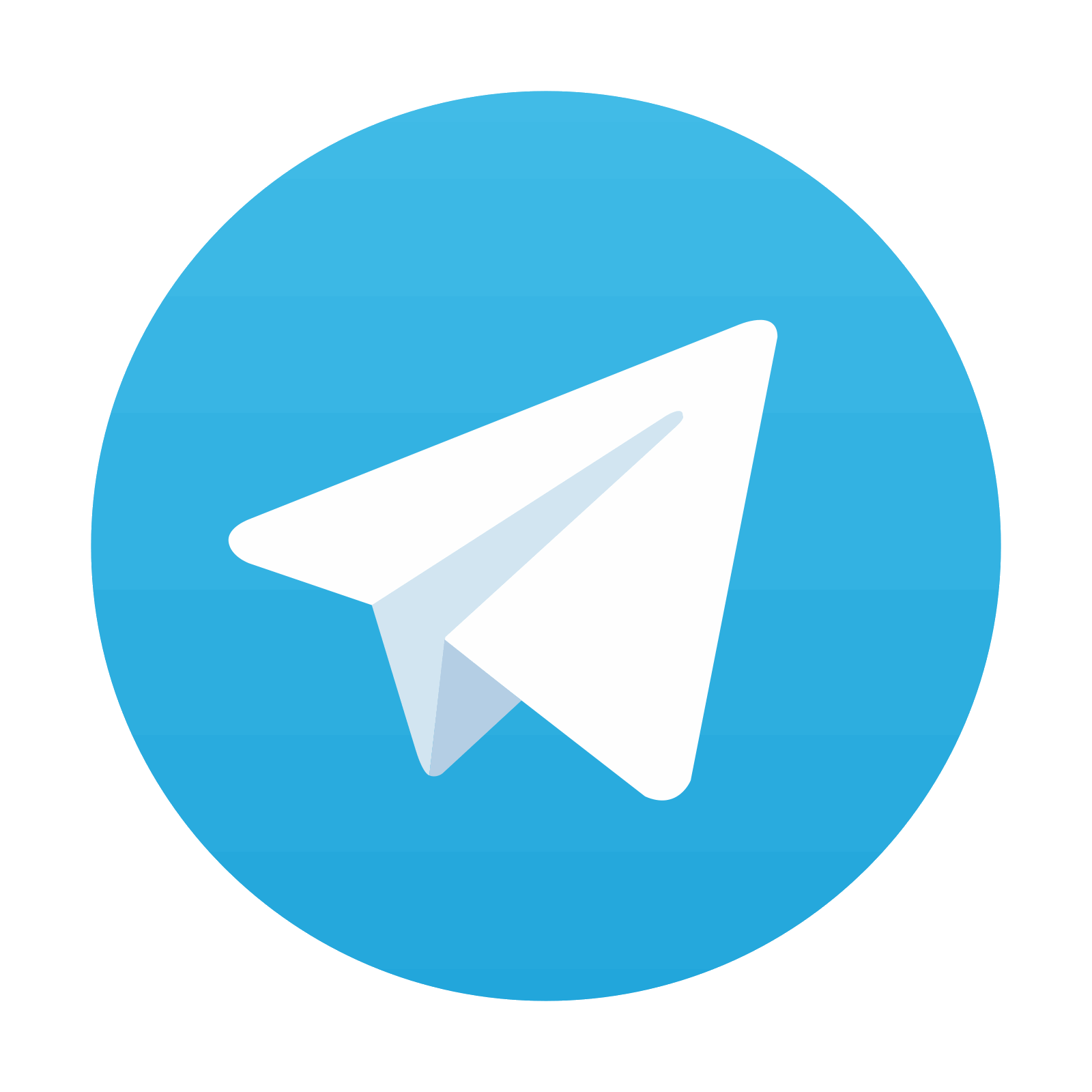
Stay updated, free articles. Join our Telegram channel
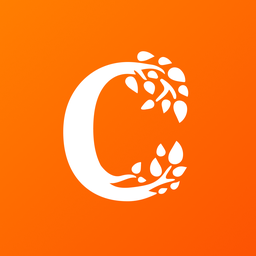
Full access? Get Clinical Tree
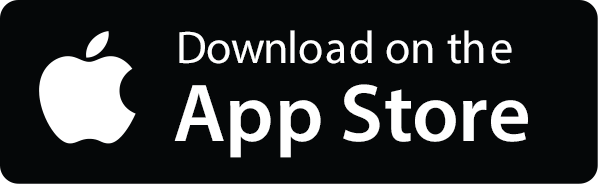
