Figure 7.1A comparison of the original and modified pins of a Harro Hofliger KFM/3 capsule filling machine. (From Moolchandani V. Functionality and Performance of Different Lactose Grades in Capsule Filling: Characterization and Evaluation of Formulation and Operating Variables on Dosing Disc Machines, PhD Thesis, University of Maryland at Baltimore, 2010.)

Figure 7.2Image of one modified-instrumented and two original tamping pins mounted in a tamping pin block. (From Moolchandani V. Functionality and Performance of Different Lactose Grades in Capsule Filling: Characterization and Evaluation of Formulation and Operating Variables on Dosing Disc Machines, PhD Thesis, University of Maryland at Baltimore, 2010.)
Wheatstone Bridge
Transducers are devices that convert some physical quantity (such as force) into a more conveniently measured property (such as voltage). Electrical resistance strain gages measure strain in an object based on the change in electrical resistance of an electrical conductor as a function of the strain. Strain gauges are often connected in a Wheatstone bridge circuit, often consisting of a combination of four active gauges (full bridge), as discussed here. As stress or load is applied, resistive changes to the bonded strain gauges take place, which unbalances the Wheatstone bridge. The result is a signal output related to the stress value. As the signal value is small (typically a few millivolts), the signal conditioning electronics provides amplification to increase the signal level to 5 to 10 V, a suitable level for external data collection systems.
It is good practice to select strain gauges with a thermal expansion coefficient that matches that of the surface to which they are applied, in this case the stainless steel of the piston or tamping pins, to compensate for possible temperature changes during operation. However, a Wheatstone bridge provides an additional method to achieve temperature compensation. This technique is commonly referred to as circuit compensation with push (compression)–pull (tension) gauges. In the push–pull method, a C (compression) and T (tension) gauge are bonded side by side on the test piece (e.g., tamping pin) and wired as adjacent arms in the Wheatstone bridge (Figure 7.3).

Figure 7.3Wheatstone bridge.
The active gauges are connected in opposite arms of the Wheatstone bridge so that the contribution of each to the output could be expressed as a sum. A wire or foil element in the gauge under a positive strain (tension) will increase in length and decrease in diameter, resulting in increase in resistance. A compressive force will decrease the wire length, increase the diameter, and lower the resistance. Therefore, if strain gauge (R1) in arm 1 goes into tension, resulting in an increase in resistance, less current would flow through it. Whereas the strain gauge (R2) in arm 2 would undergo compression and the current in the circuit will take the path of least resistance, that is, more current will flow through arm 2 as compared to arm 1, causing a higher voltage potential at the junction between arms 2 and 3 than at the junction between arms 1 and 4. For that reason, the junction between arms 2 and 3 is called the positive signal. The change in voltage under compression load can be expressed by Equation 7.1:26

In the previous example of the instrumented Harro Hofliger machine, one gauge pair was bonded on each side of the thinned neck portion of the modified piston. One gauge in each pair was aligned parallel to the major strain axis to form the primary active arms of a full Wheatstone bridge circuit. This resulted in the orientation of the other two gauges perpendicular to the major strain axis, which provided not only temperature compensation but also a small but significant contribution to the bridge-unbalance voltage through the Poisson effect. The circuit diagram appears in Figure 7.4.

Figure 7.4Circuitry diagram of Wheatstone bridge on a Harro Hofliger tamping pin. (From Moolchandani V. Functionality and Performance of Different Lactose Grades in Capsule Filling: Characterization and Evaluation of Formulation and Operating Variables on Dosing Disc Machines, PhD Thesis, University of Maryland at Baltimore, 2010.)
Installation of Gauges
A great deal of care must be exercised in the proper installation of strain gauges. There are many considerations, such as cleaning, degreasing, and abrading the surface to which the gauge will be bonded, choice of adhesive, and curing. A specific procedure and technique needs to be learned and rigorously followed to assure a successful installation that exhibits reliable performance. A discussion of these details is beyond the scope of this chapter, and the interested reader is referred to major strain gauge suppliers who often provide detailed guidance on strain gauge installation.
Signal Retrieval from Rotating Components
If pistons or other transducer sites are stationary or move only in one plane, sensing devices may be mounted directly onto them and signal retrieval is straightforward. However, when the instrumented site is rotating, there is the added complication of twisting or winding up of the connecting cables. This problem is commonly encountered with rotary tablet presses where the usual method of resolving the problem is to not instrument the actual punches, but to mount the transducer on a stationary, remote site, such as the tie rod between compression rollers, the eyebolt connecting the lower compression roller with the overload mechanism, or the compression roll pins. In such cases, the farther away the transducer is from the compaction event, the smaller the proportion of the actual punch force actually recorded.
The earliest reports (Table 7.1) of the instrumentation of automatic capsule filling machines have involved intermittent motion dosator machines in which the dosators rotate through 180° from the plug formation to the plug ejection stations and then back again (e.g., Zanasi LZ-64). Cole and May3,4 reported on the modification of a Zanasi LZ-64 machine by the addition of a planetary gear system to prevent damage to the lead wires from an instrumented piston during such rotation. The planetary gear system keeps the same face of the instrumented dosator forward at all times by causing the dosator to rotate one full turn in the opposite direction for each rotation of the dosator assembly.
Small and Augsburger5,6 used a mercury pool swivel to circumvent the problem of dosator rotation on an intermittent motion Zanasi machine. The mercury pool swivel is a form of slip ring. The swivel consists of a stationary plate, which is connected to the monitoring equipment, and a rotating wheel, which is connected to the rotating piston assembly. The complete bridge is assembled on the rotating component. Electrical conductivity through the swivel is by means of platinum-tipped electrodes that dip down from the stationary plate to individual mercury-filled canals in the rotating wheel. In instrumenting a Zanasi LZ-60 machine, Greenberg8 used a traditional (non-mercury) slip ring assembly to connect the bridge to the power supply and recording instrument. The rings are mounted on a shaft attached to the rotating component such that the axis of the shaft coincides with the axis of rotation of the rotating component. The shell of the assembly usually carries several brushes or sliding contacts for each ring. Lead wires from the bridge rotate with the specimen and are connected to the rings. Lead wires from the power supply and recording equipment are connected to the brushes. Later, the potentially hazardous mercury swivel of the earlier instrumented Zanasi LZ-64 was replaced with a similar instrument quality slip ring assembly (Figure 7.5).22

Figure 7.5Zanasi dosator mounted to a slip ring assembly. During capsule filling, the vertical shaft keeps the slip ring in position while the dosator rotates.
Hauer et al.15 also bonded strain gauges to the piston of a Zanasi LZ-64 filling machine. They resolved the problem of dosator rotation by mounting a differential condenser in the shaft about which the dosators rotate that links the signal from the bridge with the cables to the recording system. Dosing disc machines (e.g., Hofliger-Karg and Harro Hofliger) do not require such considerations since the tamping pin assemblies move up and down in a vertical plane and do not rotate.
Calibration
In all cases, calibration is essential to establish the relationship between the actual force or displacement being monitored and the output signal. The overall quality of the instrumentation depends on the accuracy and precision of the calibration and the institution of a periodic recalibration checking program. Instrumented pistons may be removed and installed in-line with a load cell of known output between the platens of a physical testing machine (e.g., Instron). The load cell thus functions as a primary standard. The outputs from the load cell and the instrumented piston or punch are monitored simultaneously during loading and unloading, preferably using a microprocessor-based digital data acquisition system (DAQ). Displacement transducers may be calibrated by direct comparison of the output against actual displacement measurements.
Following the previous example, Figure 7.6 illustrates the assembly used to calibrate instrumented tamping pins for the Harro Hofliger (H&H) filling machine using an Instron physical testing machine.18 The test was performed in blocks. In the first block, the instrument was run in “position control” wherein the position of the hydraulic actuator was lowered at a rate of 60 mm/min until the specified load (end point) is reached. Once the specified load (e.g., 50 N) on the tamping pin was attained, the instrument would switch to the second block. In the second block, the instrument was run in load control, where the specified load would be maintained for 30 s (end point for the second block). After 30 s, the instrument would switch to the third block. In the third block, the instrument was run in position control, where the hydraulic actuator retracts back to about 15 mm above the tamping pin. The force was increased up to 300 N with the increment of 50 N per stage. Later, calibration force was reduced in a similar manner in order to check whether there is any hysteresis. During calibration, each tamping pin was checked for torsion loss by rotating the centering position of the pin.

Figure 7.6Calibration of instrumented tamping pins for the Harro Hofliger (H&H) filling machine using an Instron physical testing machine. (From Moolchandani V. Functionality and Performance of Different Lactose Grades in Capsule Filling: Characterization and Evaluation of Formulation and Operating Variables on Dosing Disc Machines, PhD Thesis, University of Maryland at Baltimore, 2010.)
Monitoring/Data Handling
The output of these types of transducers is generally a DC voltage proportional to the magnitude of the property measured (force or distance). In selecting the voltage measuring and display instrument, the first criterion to be met is the frequency response. If the signal is static, the time available for recording is relatively long, and simple direct reading indicators or strip-chart recorders can be used. With dynamic signals, the time available to measure the output voltage may be very short, thus making recording more difficult.
Reading a meter or a line on a chart paper introduces a source of error and also demands a large amount of operator time and skill in transcribing the analog readout to digital numbers. Inexpensive, powerful digital microprocessors now available make unnecessary such laborious data handling and enhance the quality and quantity of the data produced. The analog signals are often multiplexed to an electronic analog-to-digital converter. The digital data may then be stored in a temporary “buffer” memory or permanently recorded on hard drive or disc. The data may be recalled for manipulation or display in either graphical or tabular form on a video monitor and/or hardcopy printer or plotter.
The mechanism that allows the interaction, via the computer, between the strain gauges and the operator is commonly referred to as a data acquisition system (DAQ). The DAQ collects and translates the signals from the different transducers mounted on a capsule filling machine, bringing these signals to a computer ready for processing, examination, storage, and other data processing. In the previous example of the instrumented Harro Hofliger machine,18 the compression and ejection events detected by the instrumented tamping pins were monitored by measuring the bridge unbalance voltage using a carrier preamplifier SCXI 1000 chassis block and SCXI-1321 module (National Instruments, Austin, Texas), which also serves to activate the bridge. A NI-DAQ 7 PCI card (National Instruments) was the data acquisition device. The compression and ejection events were recorded continuously by means of Labview 7 software (National Instruments). A schematic of the DAQ system operation is shown in Figure 7.7.

Figure 7.7Signal conditioning and data acquisition schematic for the instrumented Harro Hofliger KFM/3 capsule filling machine. (From Moolchandani V. Functionality and Performance of Different Lactose Grades in Capsule Filling: Characterization and Evaluation of Formulation and Operating Variables on Dosing Disc Machines, PhD Thesis, University of Maryland at Baltimore, 2010.)
Signal conditioning involves primarily an amplifier that provides the excitation voltage, as well as gain (a factor used in converting millivolt output of the strain gauge bridge to the volt-based range of the input of the data acquisition device). For example, the output of the Wheatstone bridge is normally expressed in millivolts per volt of excitation per unit of applied force. The sensitivity of 0.2 mV/V/kN means that, on application, a 10-kN force and a 10-V excitation will produce a 20-mV output. To utilize such output, it usually needs to be amplified several hundred times to reach units of volts. In the present example,18 the SCXI 1000 chassis with NI SCXI-1321 module was used as a signal conditioning device.
Labview software controls the measurement system, telling the DAQ when and from which physical channels to acquire or generate data. This SCXI-1321 module supports the monitoring of four signals from the instrumentation at any one time.
Application of Instrumented Automatic Capsule Filling Machines in Research and Development
Dosator Machines
Plug Compression and Ejection
The instrumentation of an automatic capsule filling machine was first reported by Cole and May3,4 who bonded strain gauges directly to the piston of a Zanasi LZ-64 dosator machine; however, they did not make use the piston compression feature of this machine. Small and Augsburger5,6 also instrumented the piston of a Zanasi LZ-64, but their use of the compression mechanism provided a more complete evaluation of the role of the dosator in plug formation. The diagrammatic representation of the force–time traces shown in Figure 7.8 show the generation of a precompression force that typically occurs when the dosator plunges downward into the powder bed to capture a plug of powder. When the piston compression feature of the machine is utilized to apply more force to the plug, this precompression force is immediately followed by a spike, which results from the active compression of this plug by the piston when the dosing tube is at its lowest point of travel. Plug formation is then followed by a sharp spike, indicating the ejection force required to initiate the movement of the plug as it is pushed by the piston into the receiving capsule. Although plug compression forces (typically not greater than 200 N) are far lower than normally achieved in tableting, sufficient force may be developed to increase the density of the powders above their maximum tapped bulk density.

Figure 7.8Representation of various features that may be found in dosator force–time traces.
For a given formulation, the development of a precompression force depends on the piston height and the powder bed height.28,29 For a given powder bed height, precompression force increases with decreases in the piston height. This apparently is the result of forcing smaller and smaller volumes through the same powder depth. Similarly, for a given piston height setting, the deeper the powder bed is, the greater the precompression force. Interestingly, increasing the magnesium stearate added to pregelatinized starch from 0.005% to 0.02% increases the precompression force, all other things being equal.28,29 Two factors may contribute to this latter finding. First, an increase in the lubricant level may increase the packing density of the powder bed through the glidant effect of the lubricant. Second, the greater precompression force may in part also be attributable to reduced friction at the dosing tube wall, thereby causing less force to be lost in overcoming friction at the dosing tube wall, and more force to be transmitted to the piston during precompression.
Lubrication Requirements
A great deal of information about the state of lubrication can be learned by studying the traces produced using instrumented pistons. For example, a compression force–time trace that does not recover fully to the baseline before ejection (illustrated in Figure 7.8) may be seen with some formulations. This retention force is apparently attributed to expansion of the plug back against the end of the piston, and is mostly likely to be observed under conditions of marginal lubrication, particularly with materials that have substantial potential for elastic recovery.4,6 With adequate lubrication, retention forces are negligible or do not appear, probably because the lubricant allows the plug to slip to relieve the residual pressure. Occasionally, a “negative trace” occurs after ejection and as the piston spring recovers to retract the piston to its initial position, as illustrated in Figure 7.8.4,6This negative trace indicates tension on the strain-gauged piston during its retraction and can only be caused by excessive frictional drag. This drag force is attributed to inadequate lubrication and/or excessive accumulation/adhesion of powder particles on the piston and dosator wall.
Small and Augsburger demonstrated that instrumentation can be used to help select the type and level of lubricants.25 They found lubricants to be effective, sometimes at unusually low concentrations: minimum ejection forces were observed at 1% with anhydrous lactose, 0.5% with microcrystalline cellulose, and 0.1% with pregelatinized starch. Moreover, they showed that, within certain limits, it may be possible to manipulate plug compression force, powder bed height, and piston height to reduce the hydrophobic lubricant requirement of a formulation while still achieving the target fill weight. Although ejection force increases directly with compression force as expected, this increase was found to be dependent on the powder bed height and piston height. At a given compression force, an increase in either the piston height or the powder bed height increases the magnitude of the ejection force, and vice versa.
Mehta and Augsburger mounted a linear variable displacement transducer (LVDT) on the Zanasi LZ-64 previously instrumented by Small and Augsburger.9 This modification permitted the simultaneous measurement of both force and piston displacement. As expected, no displacement of the piston was observed at precompression. During piston compression, actual displacement was less than that set by adjustment of the compression knob owing to the deformation of the overload relief spring mounted in the compression knob holder. Generally, ejection force was found to rise to a maximum at the onset of the ejection displacement, indicating that sufficient force must be developed before the piston can displace the plug. In certain cases, a slight further compaction of the plug can be observed to occur during the development of the peak ejection force. Mehta used this instrumentation to estimate the work of plug ejection from the area under ejection force–piston displacement profiles.30 Five formulations consisting of common fillers (anhydrous lactose, dicalcium phosphate, and microcrystalline cellulose) lubricated with either stearic acid or magnesium stearate were studied. Compression force and lubricant level were varied to yield similar peak ejection forces (P = 0.05). Yet, in most cases significant differences in the work of ejection were observed, suggesting that work measurements may be more informative than peak ejection force measurements.
It is well known that lubricants such as magnesium stearate can interfere with bonding and soften compressed tablets. Similarly, capsule plugs can also be softened, and this could adversely affect weight variation if it leads to powder loss during plug transfer. Powder could be lost from the end of the dosing tube during rotation to the ejection position or could result from plug collapse and breakup during ejection. It is interesting, however, that at certain limits, drug dissolution may be enhanced in certain formulations, presumably by a reduction in plug cohesion, as a result of increasing the magnesium stearate level21,31 or by extending the mixing time of a given concentration magnesium stearate.32 In one example, Mehta and Augsburger found that as the concentration of magnesium stearate increased from 0.05% to 0.75%, the time required for 60% dissolution of hydrochlorothiazide (T60%) decreased from 55 to 12 min and the breaking strength of these microcrystalline cellulose-based plugs measured using a three-point bending test was markedly reduced, from 85 to about 2 g.21 The capsules were produced on an instrumented Zanasi LZ-64 machine with a standardized compression force. Interestingly, in a parallel study with the same range of magnesium stearate concentrations in a lactose-based formulation, hydrochlorothiazide T60% increased slightly with the lubricant level (from 12 to 18 min) while the plug breaking force decreased slightly, although not significantly (P = 0.05), from 18 to 13 g.21 In the case of microcrystalline cellulose, the initial increase in hydrophobicity with increase in magnesium stearate level may be more than offset by reduced plug cohesiveness in the concentration range studied, which probably improves moisture penetration and plug disintegration. Since dissolution markedly slowed when the magnesium stearate concentration was further increased to 2%, the hydrophobic effect of the lubricant apparently becomes overwhelming at higher levels.
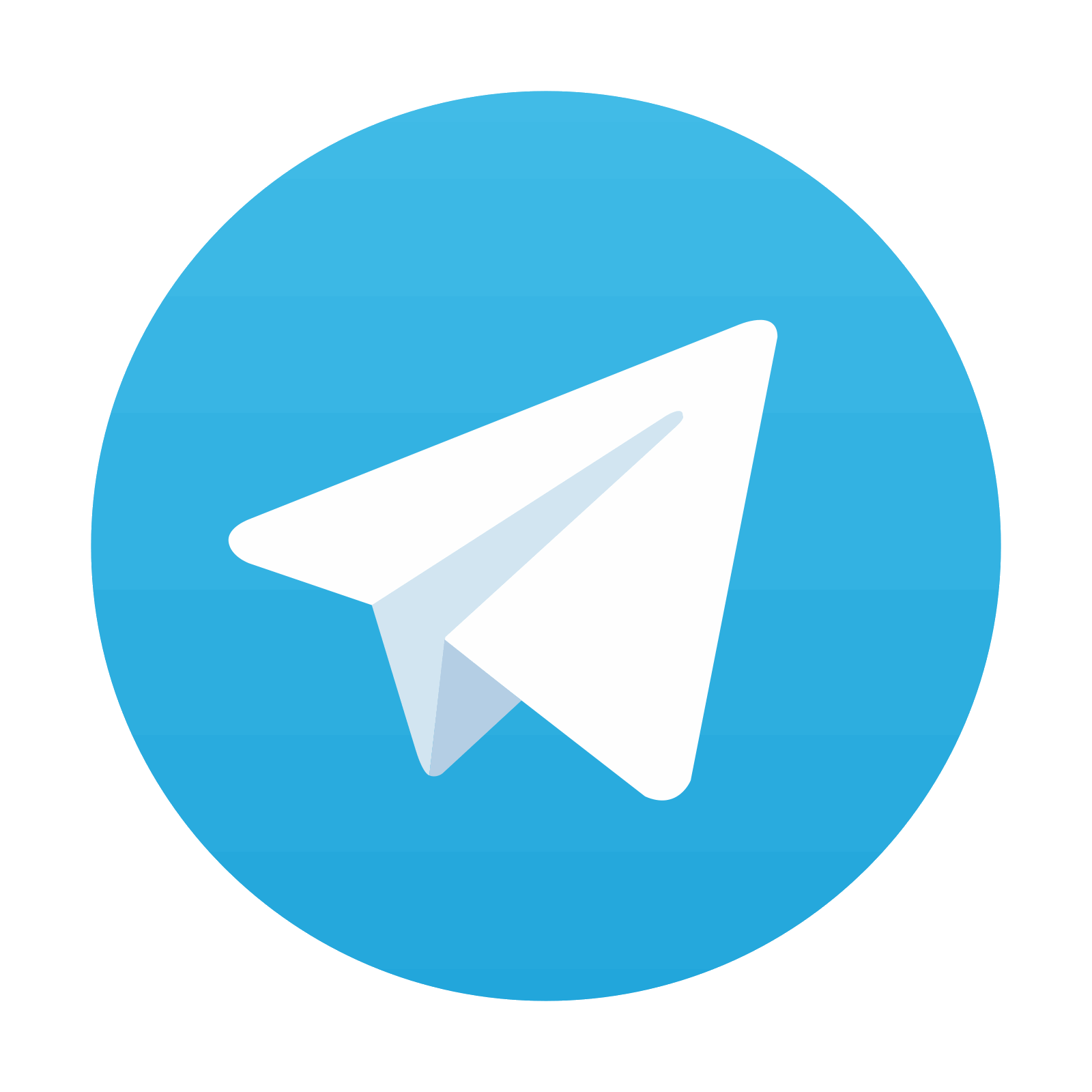
Stay updated, free articles. Join our Telegram channel
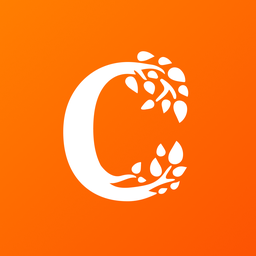
Full access? Get Clinical Tree
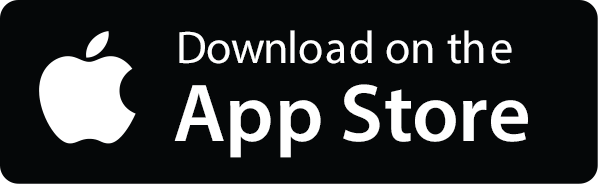
