Figure 9.1(a) Schematic drawing of a force–time profile that would be obtained on an eccentric tablet press, based on time calculations for a running speed of 43.6 rpm66 and general force profiles as described by Jones.113 (b) Schematic drawing of a force–time profile that would be obtained on the upper punch of a Fette P2 rotary tablet machine, based on measurements on pregelatinized starch.117 (c) Schematic drawing of the force–time profile that would be obtained on a dosator nozzle capsule-filling machine, based on traces obtained for lubricated microcrystalline cellulose.35,83 (d) Schematic drawing of the force–time profile that would be obtained on a tamp-filling machine,68 based on traces obtained using a pneumatic tamping head, installed at tamping station 3, for pregelatinized starch.38
For capsules that are to be filled at a plug density matching the maximum bulk (“tapped”) density of the powder, it is possible to predict the maximum bulk density and hence also the capsule fill weight for mainly binary powder mixtures from the volume fractions and maximum bulk densities of the individual powders.57 When filling mixtures of granulated powdered cellulose and magnesium stearate on a tamp-filling machine at a cumulative tamping distance of zero, that is, all pins were set to be flush with the upper surface of the dosing disc when at their lowest position during tamping, it was possible to predict the plug density and fill weight of the capsules from Carr’s compressibility index58 and the maximum bulk density of the mixtures.59 The decrease in one and the simultaneous increase in the other bulk property with increasing magnesium stearate concentration resulted in the plug density to go through a local minimum at 0.4% magnesium stearate. Podczeck and Newton60 reported that the maximum plug density that can be achieved on a tamp-filling machine is inversely related to the angle of internal flow,61 indicating that during the downward movement of the tamping pins inside the dosing disk bores, particle slippage and particle rearrangement are hindered by interparticulate friction.
Compression Pressure Used in Development and Manufacture
As mentioned above, during tabletting, the degree of densification of the powders is much more extensive than that achieved in capsule filling. The forces that can be applied to powders using, for example, a rotary tablet machine, are only restricted by the capacity of the load frame. For example, the Fette P2 rotary tabletting machine was able to withstand compression forces up to 35 kN,62 which translates into a theoretically possible maximum tabletting pressure of 1.2 GPa for a 6-mm punch (i.e., the plug diameter of a size 2 capsule). More recent rotary machines are able to withstand 60–80 kN of force. The reason that tabletting machines are built to withstand these high maximum compression forces is that tablet dimensions are normally larger than the diameter of a capsule plug; typical tablet dimensions are, for example, a diameter of 10 or 12 mm for round circular tablets, or 15 mm × 5 mm for capsule-shaped tablets. This is equivalent theoretically to maximum tabletting pressures of 880, 620, and 400 MPa, respectively, assuming a maximum compression force of 70 kN. The maximum compression forces and related tabletting pressures used in the mass production of tablets are, however, lower (10–15 kN;63 100–250 MPa64), depending on size and shape of the tablets, in order to produce tablets with adequate mechanical strength and disintegration as well as drug dissolution properties, and ensuring that tabletting errors such as double-pressings do not cause a breakage of the load frame.65 On an eccentric tabletting machine, a maximum compression force of 15 kN was not normally exceeded,66 but this type of machine is no longer used in mass production.
Rotary tabletting machines are also able to provide a pre-compression step, for example, to allow entrapped air to be vented and hence to reduce the risk of capping and lamination. The pre-compression pressure is typically set between 10% and 20% of the final tabletting pressure. The pre-compression step will also lengthen the time over which the compression pressure is exerted on the powder or granule formulation.67
The force used to fill powders and granules into two-piece hard capsules on a tamp-filling machine has changed over the years. Very early machines used strong springs inside the tamping heads, and these machines were able to exert forces up to 500 N to form firm plugs with defined mechanical strengths. However, in order to reduce wear and tear of the motor and all moving machine parts, in the early 90s, machines were redesigned. For example, Bosch GKF machines now provide the user with a choice of four different types of springs; the standard spring starts to deflect at about 55 N and allows filling of capsule sizes 2, 1, and 0 with tamping forces between 90 and 100 N.38 Two further sets of springs are available for lower tamping forces used for smaller capsule sizes and filling of inhalation powders. The fourth set is a “heavy duty” spring achieving theoretical tamping forces of up to 200 N,68 but in practice, 150–160 N cannot be exceeded.38,43,68,69 This type of spring is intended for the filling of size 00 capsules and when larger fill weights are required (e.g., antibiotics and high-dose non-steroidal anti-inflammatory drugs). The commonly used tamping forces for filling powders or granules on an industrial machine are between 50 and 150 N.63 The appropriate dosing discs are typically selected by compacting the powder at 20 and 50 N in a single step using a powder plug tester and measuring the plug length achieved.6 In research studies, the use of tamping forces between 50 and 250 N has been reported.38–41,70–76 In some of these studies, the tamping force was kept to a fixed value, because the aim of the work was not to study the influence of the tamping force on capsule-filling performance, but to investigate plug properties such as water penetration rates into hydrophilic polymer matrix plugs and drug release (200 N),70 or to study drug dissolution under defined conditions.75 Other studies aimed to investigate tamping forces per se; for example, Shah et al.,40 reporting on anhydrous lactose lubricated with 0.5% magnesium stearate, found that tamping forces were low at tamping station 1, at their maximum at station 2, and were similar at tamping stations 3 and 4, but slightly reduced and were lowest at station 5. Podczeck74 found that the tamping force recorded depended on the cumulative tamping distance and was material dependent. For pregelatinized starch, the highest tamping force was recorded at station 3, and at this station, a change in cumulative tamping distance also resulted in a maximum change in tamping force. For microcrystalline cellulose, however, the maximum force and the steepest slope of the force as a function of cumulative tamping distance were observed at station 4.
In dosator-nozzle machines, the force achieved depends on a number of factors such as type of powder or granules, powder bed height and density, pre-compression and compression settings, and strength of the overload spring. In intermittent dosator-nozzle machines, the linear up and down movement of the nozzles makes the process of force application similar to that achieved on an eccentric tabletting machine. In rotary-type dosator-nozzle machines, the movement of the turret and hence the compaction cycle appears to be more similar to a rotary tabletting machine, yet the force exerted on the powder bed is only from above, as in eccentric tabletting machines. Extensive research on plug formation using dosator-nozzles has been undertaken using instrumented production machines as well as machine simulators; instrumentations and simulators used have been reviewed by Armstrong.77 Britten et al.37 studied pregelatinized starch and lactose monohydrate using pre-compression pressures between 3 and 4.4 MPa alone or in combination with an additional compression pressure to reach either a constant plug length (displacement mode) or the maximum possible compression pressure (compression pressure mode). In displacement mode, the pressures applied were between 4.6 and 6 MPa, whereas in compression mode, the maximum pressures achieved were between 8.7 and 8.8 MPa. The findings of their research will be further discussed in the “Rates of Compression and Ejection” section. The diameter of the dosator tube used was 6 mm.78 Compression pressures as high as 50 MPa were reported by Tan and Newton79 using an unlubricated size 1 nozzle in a rotary nozzle filling-simulator. Values between 5 and 8 MPa were observed by Jolliffe and Newton80 with the same simulator using a size 3 nozzle and various size fractions of unlubricated lactose monohydrate. The surface finish and cleanliness of the nozzles have an important influence on the compression pressures79,80 because of the interaction between powder and metal surfaces. Pre-compression forces between 40 and 140 N were observed by Hauer et al.81 using lactose monohydrate of two different size fractions and their mixtures, and four different powder bed heights between 30 and 50 mm and a dosing tube length between 10 and 16 mm. They found that the pre-compression forces increased with an increase in the powder bed height, but decreased with an increase in the dosing tube length. When the powder bed height remains constant and the volume in the dosing tube increases with a change in piston setting, the powder is compressed less and the pre-compression force will drop. These authors also found that for all machine settings the use of microcrystalline cellulose always resulted in the lowest pre-compression force and hence microcrystalline cellulose was classed as “easily compressible.”81 In other reports, overall achieved compression forces of, for example, 5–350 N,82 126–159 N,35 35–213 N,7 137 N,83 213 N,84 222 N,10 and 50–100 N85 are quoted, often presented as kg-force values, which, for ease of comparison, have been converted into N by multiplying them by the gravitational constant (9.81 m s−2). Similar to reports on tamp-filling machines, some workers have made use of the ability to control the compression forces applied by the piston in order to study problems such as the mechanical strength of plugs84,85 or drug dissolution.8–10 Small and Augsburger35 compared the traces obtained when filling lubricated microcrystalline cellulose, lactose monohydrate, pregelatinized starch, and dibasic calcium phosphate dihydrate. They could clearly distinguish between the forces achieved by pre-compression and compression. Differences in the forces between materials were attributed to differences in the initial powder packing density and also to differences in the ability of the materials to reduce their volume under load. When filling unlubricated pregelatinized starch at various compression settings and unlubricated microcrystalline cellulose and lactose monohydrate at the lowest compression setting, a residual force attributed to elastic rebound against the piston was detected.
It can be concluded that the maximum achieved total force, that is, the resistance of the powder against pre-compression and compression, is fairly similar in dosator-nozzle and tamp-filling machines. This force is approximately 1–2% of the compaction force used in tabletting machines, and the comparative compression pressures range between 5% and 10% of those used in tabletting. As a result, the powder plugs are soft and of substantially higher porosity, as discussed above.
Axial Force Transmission Ratio
In tabletting, especially when using eccentric machines or compaction simulators, the stress transmission from the upper punch to the lower punch is used to assess the state of lubrication and influence of powder–die wall friction on the densification of powders. To this end, Nelson et al.86 defined the axial force transmission ratio R as the ratio of maximum force at the lower punch (FL) to the maximum upper punch force (FU); (R = FL/FU). (This equation can be rewritten using the pressure equivalents PL and PU.) Under conditions of uniaxial compression, perfect lubrication would result in total axial force transmission, that is, R = 1, and R values vary with the type of lubricant and its concentration within the compact. The nature of the powder formulation, the tablet weight (effectively the dimensions for conditions of uniform material density and packing), and the type of die used all affect the value of R according to Sheinhartz et al.87 Toor and Eagleton88 and Hölzer and Sjögren89 found the value of R to vary with the applied compaction force, while Lewis and Shotton,90 using a variety of materials, noted both increased and decreased R values upon raising the “mean” compaction pressure PM, whereby PM had been defined as PM = 0.5(PU + PL).
Hölzer and Sjögren91 demonstrated that effective use of R values to study friction and lubrication requires both constant tablet dimensions and a constant maximum compaction force, because the value of R is pressure dependent even for a constant tablet height. Increased axial pressure transmission usually results from an increase in the applied pressure or a decrease of the compaction height-to-diameter ratio.89
Strickland et al.92 constructed R values versus admixed lubricant concentration curves and suggested a functional relationship of “Langmuir type” at low lubricant concentrations by assuming that the reduction in frictional force corresponds to the degree of lubricant cover of the die wall. Little increase in the values of R was obtained beyond a 1% lubricant level. After sectioning and staining compacts, the authors concluded that lubricants such as magnesium stearate and graphite coat the base material granules (starch paste granules of sulfathiazole, sodium bicarbonate, or acetyl salicylic acid) without penetrating their interior. Wolff et al.93 reported entrapment of lubricant particles within the surface features of granules, suggesting different types of behavior for different lubricants.
Strickland et al.94 divided lubricants into two groups, that is, boundary lubricants and hydrodynamic lubricants, and determined their R values for two granule formulations (i.e., starch paste granules of sulfathiazole and sodium bicarbonate). More than 70 different lubricants were tested. They concluded that the general theories of solid–solid lubrication95 are applicable to the tabletting process. Excellent lubricity was defined as having an R value above 0.9 (the unlubricated controls had R values of 0.67). Lewis and Shotton96 found that with some tabletting formulations, the axial force transmission ratio was insufficiently sensitive to distinguish between similar lubricants and that the best lubricants were those with the lowest melting point.
In capsule filling, R values cannot be obtained directly, because there is no “lower” punch or support that can be instrumented. However, R values have been obtained under low-force compression conditions similar to the capsule-filling process using compaction simulators. Heda et al.97 used an Abacus compaction simulator, fitted with a specially designed longer die and 5.71 mm tooling equivalent to a size 1 capsule. The force was applied as single-ended saw-tooth waveform at constant speeds of 1, 10, and 100 mm s−1. The speed of 100 mm s−1 exceeds the speed of a tamping pin in a GKF 330 tamp-filling machine slightly68 and is three times the piston velocity measured on a Zanasi LZ-64 intermittent dosator-nozzle filling machine.83 Heda et al.97 produced plugs of different lengths (4, 8, and 12 mm) from a coarse-grade microcrystalline cellulose, anhydrous lactose, and pregelatinized starch and determined the axial force transmission ratio R. As expected, the values for R increased with a decrease in plug length, but compared to tablet formation, the values did not reach “acceptable” magnitudes, with R = 0.77 being the highest value found (microcrystalline cellulose at 4 mm plug length). For the ductile powders, microcrystalline cellulose, and pregelatinized starch, the R values decreased in general when the compression speed is increased from 1 to 10 mm s−1. For microcrystalline cellulose, the R value remained constant when changing from 10 to 100 mm s−1, except for the smallest plug length, where the R value increased significantly. For pregelatinized starch, the change from 10 to 100 mm s−1 resulted in an increase in R value at 12 and 8 mm plug length. For anhydrous lactose, no influence of compression speed was detected, and the authors attributed this to the ability of the powder to attain a relatively higher packing density upon die filling owing to better flow properties. Guo et al.71 used a similar methodology to compare different types of microcrystalline and silicified microcrystalline cellulose, anhydrous lactose, and pregelatinized starch. The plug lengths were set to 6, 8, and 12 mm, and only two compression speeds were used (1 and 50 mm s−1). In general, the R values decreased with an increase in plug length, and as before, the R values did not reach levels seen in tabletting (0.43–0.78). At plug lengths of 8 and 12 mm, most R values were found to decrease with an increase in compression speed, but for the 6-mm plugs, the dependence on compression speed was more varied. The authors71 stated that they would have expected the R values to increase with compression speed, because the dynamic coefficient of friction between two bodies in motion relative to each other should decrease with an increase in sliding velocity. They attributed the deviations found to differences in time needed for particle packing and rearrangement, particle size distribution, particle shape and surface roughness, and particle deformation properties, which were different for the various materials studied.
When studying the low-compression properties of commercially available Hypericum perforatum extracts, Kopleman et al.73 found that the axial force transmission ratio R decreased significantly when increasing the plug lengths at both 50 and 150 N maximum compression force as a result of loss of force attributed to plug-die wall friction. They found that overall the punch speed did not affect the R values. As the R values were again comparatively low (0.2–0.7), they suggested that addition of a die wall lubricant such as magnesium stearate would be beneficial.
Shaxby and Evans98 reported that when applying a downward force to the top of a column of sand confined into a tube, it was not fully transmitted to the bottom if the height of the column exceeded its diameter. The force decay was described as approximately exponential:

where FL and FU are as defined earlier, h and d are the final powder column height (i.e., plug length) and diameter, respectively, and Km is a material constant related to the coefficient of friction between the wall of the tube and the powder. In developing this equation, Shaxby and Evans98 made the assumption that the vertical (axial) pressure applied is uniform across the diameter of the powder column at any point along its length and that the frictional force per unit area at the outer vertical surface of the column at a given depth is given by the product of the coefficient of friction and the horizontal (radial) pressure acting on the tube wall at that position. They also pointed out that the force transmitted is a function not only of the length of the powder column but also of the initial packing of the powder bed and one should not expect that variations in the packing state will be reflected in a measurable change in powder density, because powders behave in line with continuum theory, that is, are highly incompressible.
A number of equations have been developed from that of Shaxby and Evans,98 notably those by Spencer et al.99 and by Toor and Eagleton.88 Spencer et al.99 studied powders confined into a tube and compressed by a piston. Under the assumption that the powder bed remained static and interparticulate friction was absent, they considered force transmission through the compact to be essentially hydrostatic, with a constant density of particle point contacts. The authors related the die wall friction coefficient, μd, to the initial powder column height h0, the column diameter d, and the axial force transmission ratio R:

Toor and Eagleton88 found deviations from this equation owing to the dependence of R on the axial pressure applied and the influence of particle size on the relationship. They introduced a correction factor α to take account of the structural rigidity of the particle bed. The value of α was defined as the ratio of radial to axial force on any particle situated at the interface to the tube wall. Assuming α to be constant, their equation took the form of

The values of μd were influenced by the amount of lubricant used and the previous history of the die in terms of duration of use and cleaning. Small amounts of lubricant (0.01–0.2%) were found to reduce the value of R, but a further increase in lubrication increased the axial force transmission ratio. Similarly, the value of μd increased initially and then decreased with increased amount of lubrication. Maximum R and minimum μd values were obtained after 8–10 successive compactions of polystyrene particles lubricated with zinc stearate powder without cleaning of the tooling. It was suggested that a gradual coating of the die wall with lubricant had occurred, reducing die wall friction.88
Heda et al.97 fitted their compression data to Equation 9.1 and found that their data could be fitted fully. The proposed exponential reduction in force along the length of the powder plug was found for all three powders studied (coarse-grade microcrystalline cellulose, anhydrous lactose, and pregelatinized starch). The slopes for pregelatinized starch and anhydrous lactose were almost identical, whereas that for microcrystalline cellulose was less steep. This could be the result of a different particle size of microcrystalline cellulose, but the actual values were not reported and the authors did not discuss the outcome of their model fitting procedure further. Kopleman et al.73 also reported excellent fit of their data, obtained with herbal extracts, to Equation 9.1. Guo et al.71 also used Equation 9.1, but their data from microcrystalline and silicified microcrystalline cellulose, anhydrous lactose, and pregelatinized starch did not fit the model as well as described by Heda et al.,97 and they concluded that the less favorable outcome was the result of differences in the maximum compression force used (250 N instead of 500 N), the use of a lower axial force, and their data maybe being more sensitive to small variations in the initial bulk density of the powders when filled into the die, which agrees with the remarks on the limitations of Equation 9.1 made by Shaxby and Evans.98
Ejection Forces
In the development of tablet formulations, the recording of ejection forces is very important, as it permits optimization of lubricant concentrations in the formulation. Compaction simulators are preferred for this work because of the more accurate instrumentation, but the use of piezo-electric load washers mounted directly on the lower punch of a rotary machine was reported to produce equally high-resolution force measurements with the advantage of having the data recorded on a production machine.100 This is important because ejection forces can increase with running time of the machine owing to buildup of materials around the punch tip and at the die walls.101 The maximum ejection force Fe and the pressure equivalent Pe will hence be modified by frictional conditions at the die wall and by the magnitude of the residual radial pressure across the compact-die interface. A linear relationship between the ejection force Fe and the ratio between loss of axial force to the die wall during the final stage of the tablet formation Fd (Fd = FU − FL) and the force recorded at the lower punch FL was reported by Nelson et al.,86 who also found a linear dependency of Fe on the apparent area of compact-die contact Aa, estimated from the tablet thickness. Train102 related the maximum ejection force to the maximum compaction pressure exerted from the upper punch (PU) via a power law equation (Fe = c(PU Aa)n). The constant c is related to the surface condition of the die wall and the power law constant n is related to the physical character of the compacted material. Lewis and Shotton90 confirmed that this relationship was obeyed by crystalline materials. They also found that some materials exhibited an increase in value of Fe with a decrease in particle size and that this effect was eliminated by lubrication. They concluded that the effect of a lubricant on die wall friction depends on the deformation properties of the crystalline powders to be compacted.
A reduction in the value of Fe can be interpreted as an indication of lubricant efficiency, and lubricants have been assessed in this way.94,96,103 The effectiveness of metallic stearates as boundary lubricants was shown to vary with the stearic acid content using this type of data.104 Juslin and Krogerus105,106 compared a range of admixed lubricants by measuring the value of Fe on an eccentric tablet press. In one experiment, the punches and die were cleaned between successive compactions, and in a second experiment, the compaction tooling was left unclean after the initial preparation. A significant difference between the two protocols was observed, with the average maximum upper punch force and ejection force values increasing when repetitive cleaning was omitted. Successive compactions exhibited decreasing values of Fe, which the authors interpreted as evidence for an accumulation of lubricant at the die wall, increasing the ratio of lubricated to unlubricated die wall contact. The ejection force was found to be dependent on the melting points of the organic lubricants, and this physical parameter was taken to represent indirectly the ability to form and retain a coherent film of lubricant at the die wall.
For capsule filling, to date, instrumentations to determine an ejection force have mainly been reported for dosator-nozzle machines, for example, by Cole and May,107 Small and Augsburger,35 Mehta and Augsburger,83 Botzolakis et al.,10 Jolliffe et al.,36 and Hauer et al.,81 typically with strain gauges mounted on opposing sides of the dosator piston shank and using intermittent motion machines to enable wiring of the instrumentation. Shah et al.108 described the instrumentation of a tamp-filling machine with two tamping pins equipped with strain gauges, one kept at the ejection station to monitor plug ejection forces.
The ejection force of unlubricated microcrystalline cellulose was found to be approximately half of that of unlubricated pregelatinized starch.35 For unlubricated pregelatinized starch, Small and Augsburger7 reported that the ejection force slightly decreased when the filling setting was changed from using pre-compression force alone to using an additional small amount of compression force. A further increase in the compression force resulted in an increase in ejection force. The ejection force was also related to the length of the plugs produced, increasing with an increase in plug length, similar to the observations made by Nelson et al.86 with respect to tablet thickness. When adding 0.005% magnesium stearate, the ejection force was greatly reduced. At lower compression forces, the effect of plug length on the ejection force was less pronounced, but at higher compression forces, the effect was again distinct, similar to that seen using unlubricated powder. The ejection forces were significantly higher for a powder bed height of 50 mm compared to that of 30 mm, and the authors stated that the influence of the powder bed height on ejection forces was greater than the influence of the plug length. Similar findings were made for microcrystalline cellulose and anhydrous lactose lubricated with 0.2% magnesium stearate, but the effect of plug length at the 50-mm powder bed setting was less pronounced with microcrystalline cellulose. They concluded that if uniform fill weights can be achieved at lower powder bed heights and the required compensatory increase in piston height does not negate this effect, the decrease in powder bed height might provide a means of reducing the plug ejection forces without the need for an increase in lubricant concentration. For pregelatinized starch, it was also observed that a magnesium stearate level of 0.1% resulted in the lowest ejection forces, and a similar reduction was observed for microcrystalline cellulose lubricated with 0.5% magnesium stearate. A minimum amount of 1% of magnesium stearate was required to lower the ejection forces for anhydrous lactose. The alternative lubricants magnesium dodecyl sulfate and stearic acid required comparative lubricant levels of 3% and 1%, respectively, to reduce the ejection force of anhydrous lactose to values achieved with the optimum magnesium stearate concentration. When using 0.1% of stearic acid with microcrystalline cellulose and 0.1% of stearic acid or magnesium dodecyl sulfate with pregelatinized starch, the ejection forces were only marginally larger than those obtained with magnesium stearate, but when using 0.1% of magnesium dodecyl sulfate with microcrystalline cellulose, adequate reduction of the ejection forces was not achieved, presumably because of the higher specific surface area of this powder.
For various size fractions of unlubricated lactose monohydrate filled with an instrumented mG2 simulator and size 1 nozzle, Jolliffe and Newton80 reported ejection stresses between 0.4 and 4 MPa. The ejection stresses increased with an increase in particle size and doubled (larger size fractions) or trebled (smaller size fractions) when an initially clean nozzle received a powder coating during filling. For pregelatinized starch filled with the same simulator but a size 3 nozzle, Tan and Newton79 found that ejection stresses dropped from 5 MPa to just above 1 MPa above a threshold particle size of 23 μm, whereas for microcrystalline cellulose, the ejection stresses decrease from 3 to 0.5 MPa with an increase in particle size from 11 to 23 μm.
Hauer et al.81 also reported that with anhydrous lactose, the ejection force increased with an increase in powder bed height and an increase in the length of the dosing tube owing to higher piston position, and that in general, because of the stickiness of this powder, ejection forces were rather large. With microcrystalline cellulose, they observed for a powder bed height between 40 and 50 mm and a piston height of 14 and 16 mm that the ejection force increased steeply. Hauer et al.109 also found that for anhydrous lactose and lactose monohydrate, stickiness and ejection forces could be significantly reduced with the addition of 0.5% magnesium stearate, and its addition reduced the effect of the piston height on the ejection force. A further increase in the magnesium stearate concentration did not further reduce the ejection forces but resulted in insufficient powder arching and loss of powder from the dosator-nozzle during plug transfer. These authors also investigated the addition of Precirol (a mixture of mono-, di-, and triglycerides of palmitic and stearic acid), stearic acid, and talcum powder on the ejection force of lactose monohydrate plugs. Only Precirol at concentrations between 1% and 2% was deemed a useful alternative to magnesium stearate, especially as this lubricant did not affect the dissolution properties of a model drug (anhydrous caffeine).
Guo and Augsburger85 likewise pointed out that a reduction in the ejection force is not only a sign for reduced powder plug-wall friction but could also be due to insufficient plug formation. When filling different types of microcrystalline and silicified microcrystalline cellulose on an instrumented intermittent dosator-nozzle machine in comparison to anhydrous lactose and pregelatinized starch, they confirmed that ejection forces generally increase with an increase in compression force. They also found that anhydrous lactose required substantially more magnesium stearate to lower the ejection forces than the other powders tested, but that the ejection resistance decreased more rapidly once a threshold concentration of lubricant had been reached. More lubricant was also required for powders with smaller median particle size because of the larger surface area to be covered. When hydrophilic sodium stearyl fumarate was used as lubricant, for pregelatinized starch and an experimental grade of silicified microcrystalline cellulose, the ejection force was reduced more than when using the same concentration of magnesium stearate. For these two powders, sodium stearyl fumarate was deemed to be more effective in reducing the ejection force than magnesium stearate, but for the majority of powders at equal concentrations, the former was less effective than the latter.
Heda et al.72 observed that ejection forces were higher for smaller particle sizes because of their greater specific surface area and more particle-dosator-nozzle wall contact points. When filling binary powder mixtures of anhydrous lactose, coarse-grade microcrystalline cellulose, pregelatinized starch, and ascorbic acid on both an instrumented dosator-nozzle and an instrumented tamp-filling machine, Heda et al.72 were able to compare directly the ejection forces on both types of filling mechanism. In general, the ejection forces increased with an increase in the applied compression force. When using an intermittent dosator-nozzle machine, the ejection forces decreased with increasing concentrations of magnesium stearate of 0.25%, 0.5%, and 1%. However, when filling the same formulations on the tamp-filling machine, the ejection force remained constant. Based on findings reported by Ullah et al.110 and Desai et al.,111 Heda et al.72 concluded that this was attributed to the presence of an Auger screw-feeder, which supposedly led to increased mixing of the lubricant and hydrophobic film formation, which, in turn, masked the influence of increasing concentrations of magnesium stearate on ejection forces. The absolute values of the ejection forces for unlubricated single powders as well as lubricated binary powder mixtures were always higher on the dosator-nozzle machine. This was attributed to differences in the elastic recovery of the plugs before ejection. As discussed by Britten et al.,37 a larger amount of elastic recovery in axial direction is thought to lower the residual radial forces acting on the walls of a confined space such as a dosator-nozzle or dosing-disk bore, thereby reducing the ejection force, and the findings by Heda et al.72 therefore imply that elastic recovery of plugs in axial direction is larger in tamp-filling machines compared to dosator-nozzle machines.
Rates of Compression and Ejection
The initial and final powder bulk density achieved are important for a low coefficient of fill weight variability, but the rate with which the powder is densified has also been identified as a major factor in successful capsule filling and plug formation.112 In order to compare rates of compression and ejection between tabletting and capsule-filling machines, it is necessary to compare force–time profiles obtained on these different machines and to parameterize them.
Figure 9.1a shows a schematic drawing of a force–time profile that would be obtained on an eccentric tablet press. In order to draw this graph, it was assumed that the tablet press would run at a tabletting speed of 43.6 rpm, as then numerical data published by Konkel and Mielck66 could be used to construct the graph in line with the shape of a general force–time profile as described by Jones.113 The consolidation time (distance between points A and B) is defined as the time for the force to rise almost linearly with time, whereby the punch speed remains fairly constant.67,114 The beginning of the slowdown of the punch movement can be detected by the stronger bend of the curve just before point B. Upper and lower punch are at their closest distance at point C; that is, the force has already dropped to a slightly lower value when the maximum upper punch displacement has been reached. This time shift was first reported by David and Augsburger115 and has been attributed to the viscoelastic behavior of tablet formulations.116 The time span between points B and C is classed as the dwell time.67 Other authors prefer the determination of the time difference between the maximum force value and the maximum upper punch displacement.66 The contact time is the time where the upper punch is in contact with the powder and/or formed compact (points A to D). At point E, the tablet is ejected and the ejection force can be measured if the lower punch is instrumented, and at point F, the tablet has been removed from the die table. For the rate of compression, the velocity of the upper punch between points A and B is determined. For example, on a Manesty F 3 eccentric tablet press running at 60 rpm, this is approximately 100 mm s−1,67 and the corresponding contact time is approximately 100 ms.114
Figure 9.1b shows a schematic drawing of a force–time profile that would be obtained at the upper punch of a rotary machine. It was constructed from data obtained using pregelatinized starch compressed on a Fette P 2 rotary machine.117 Again, there is an initial steep rise in force with time (point A to point B), followed by a dwell time (point B to point C) and a gradual decrease in force until there is no further contact between the compact and the upper punch (point C to point D). The length of the dwell time depends on various machine-related and powder-related parameters,117,118 whereas the decompression phase is very much a function of the elastic properties of the formed compact.119 Compression rates of approximately 20–70 mm s−1 and 40 mm s−1 have been reported;67,117 that is, the compression rate on a rotary tablet machine is slower despite a much higher production output.
In an intermittent dosator-nozzle machine (e.g., Zanasi AZ 20; LZ 64; Macofar), the nozzle and plunger are pushed in a vertical direction into the powder bed. In a continuous dosator-nozzle machine, the movement of the nozzle is controlled by the cam tracks of the machine as the nozzles rotate, similar to a rotary tablet machine. A schematic drawing of the force–time profile that would be obtained on an intermittent dosator-nozzle capsule-filling machine is shown in Figure 9.1c. The drawing is based on reports by Small and Augsburger35 and Mehta and Augsburger83 who recorded such traces for lubricated microcrystalline cellulose, anhydrous lactose, and pregelatinized starch. When the dosing tube starts to dip into the powder bed, forces are only recorded once the powder bed height and the piston inside the dosing tube are at the same level (point A), and any further downward travel of the dosing tube results in pre-compression of the powder. The maximum pre-compression force is reached at point B. After a lag time of approximately 100 ms, at point C, the piston starts to compress the powder and consequently there is a further increase in force up to the maximum compression force, which is reached at point D and coincides with the maximum displacement of the piston. For some powders and compression settings, there is also a short and finite dwell time,35 and as with eccentric tablet presses, the maximum force recorded and the maximum piston displacement can be shifted, and in this respect, values of about 40 ms have been observed.83 The force then drops, depending on the elastic properties of the powder, more or less rapidly back to zero (points D to E) before an ejection force (not shown) is applied to push the powder plug out of the dosing tube into the capsule body. Due to the quasi-linear movement of the piston, compression rates are higher compared to tabletting machines, and values of 120–160 mm s−1 (Zanasi AZ 20) and 220–505 mm s−1 (Macofar MT 13/2) have been recorded.120 The pre-compression rates are even higher, that is, 242–350 mm s−1 and 301–600 mm s−1 for Zanasi AZ 20 and Macofar MT 13/2 machines, respectively.120 On a continuous dosator-nozzle machine (e.g., mG2), the force–time profiles recorded36 appear similar, but there is a lack of accurate time scales to allow exact comparisons. Values for rates achieved on these machines are not available.
Finally, Figure 9.1d shows a schematic drawing of the force–time profile obtained on a single tamping head. The drawing is based on numeric data obtained using a pneumatic tamping head installed at tamping station 3 with pregelatinized starch,38 but the trace has been smoothed similar to traces observed using strain gauges.68 Again, there is a rapid rise of the tamping force (point A to point B) followed by a short dwell time (point B to point C, approximately 10–20 ms, depending on the tamping station and powder), followed by a drop in force owing to the deflection of the overload spring (point C to point D), a second dwell time (point D to point E, approximately 40–50 ms), and then the final drop of the tamping force to zero owing to the retraction of the tamping pin (point E to point F).38 On a GKF 330 tamp-filling machine, depending on the pin penetration setting, Cropp et al.68 found times to peak force between 54 and 117 ms, which is similar to compression rates of 9 to 74 mm s−1.
A special situation is found when using compaction simulators. While these can, in theory, reproduce any force–time and force–displacement profile recorded on eccentric or rotary tablet machines, they are usually used in the so-called “saw-tooth” profile mode; that is, the force is applied linearly with displacement, which results also in a linear compaction rate up to a point where the moving punch has to slow down and come to a standstill in order for the travel to be reversed (unloading phase). Using the saw-tooth profile, compaction simulators can achieve speeds up to 3000 mm s−1,121 but in capsule-filling studies, only compaction rates between 10 and 100 mm s−1 have been used39,97 to mimic more closely the compaction rates achieved in such machinery.
To date, ejection rates have only be reported for dosator-nozzle machines and range from 453 to 653 mm s−1 and from 272 to 834 mm s−1 for Zanasi AZ 20 and Macofar MT 13/2 machines, respectively.120 On a rotary tablet machine, the full ejection force is applied within less than 50 ms.100 Using a physical testing instrument, Anuar and Briscoe122 achieved a tablet ejection rate of 167 μm s−1.
Mechanical Strength
The determination of the mechanical strength of tablets forms an essential test procedure in development and production, in-process, and quality control. The USP 38/NF33,123 method 1217 “Tablet Breaking Force” describes the mechanical testing of tablets in great depth and is very thorough in providing exact requirements for the design of tester to be used, load cell requirements, test speed and loading configurations, and the development of an adequate test procedure for a given product. To date, the shape of tablets is no longer simply round and cylindrical, requiring different test configurations, which have been reviewed recently.124 For the time being, the USP restricts the recommended test configurations to two, namely, the diametral compression test125–127 and a flexural bending test,128,129 and the USP also encourages researchers to calculate a value of tensile strength rather than simply to record failure loads. For the tensile strength of standard tablets, an optimum value of 1.5–2.5 MPa has been suggested as a rule of thumb.27
In capsule filling, the mechanical strength of the powder plugs is important for their transfer from the die into the capsule body. Poor mechanical plug strength has been identified as one major reason for underfilling of hard capsules, and it was observed that plugs made from powders are generally weaker than those formed from granules.130 Empirically, plugs are visually inspected for their integrity and lightly handled with, for example, a tamping pin to see whether they crumble easily, or whether they are firm enough to break into two halves.131 This is illustrated in Figure 9.2.


Figure 9.2Empirical testing of the mechanical strength of powder plugs produced under defined conditions. (a) Plug after ejection from the die. (b) Plug with sufficient mechanical strength. (Courtesy of Robert Bosch Inc., Utah, USA.)
Mehta and Augsburger84 reported the development of equipment sensitive enough to subject powder plugs to a flexural bending test in order to determine their mechanical strength, similar to the three-point bending test reported for tablets.129 They modified a commercially available benchtop tensile-strength tester. The powder plugs were collected directly from an intermittent dosator-nozzle machine by removing the capsule bodies from the bushings and were placed into the tester on two supports, mounted 8 mm apart. A blunt stainless steel edge (25 × 0.9 mm) was suspended from a load cell and lowered very slowly onto the powder plug at a rate of 4.4 μm s−1. On contact, the blunt edge’s further downward movement caused the plug to bend, and the breaking force was reported. However, there was no indication as to the mode of failure. They found that when filling capsules with a lubricated microcrystalline cellulose-based drug formulation (1% and 2% magnesium stearate) at a compression force of 213 N, the powder plugs were too weak to be tested for their mechanical strength despite filling well into the capsules. Varying the magnesium stearate concentration between 0.05% and 0.75% significantly decreased the mechanical strength of the plugs from 824 to 18 mN. Between 0.05% and 0.1%, the strength reduction was only about 10%, but a further increase in lubricant concentration to 0.2% decreased the plug strength by a further 45%, and the resistance to bending became negligible for 0.5% and 0.75%. With anhydrous lactose, the mechanical strength of the powder plugs was low (170–125 mN), but an increase in magnesium stearate concentration from 0.05% to 0.75% only reduced the values by less than 30%.
Augsburger’s research group improved the bending tester so that it had a greater measurement range and higher precision.40 When using a tamp-filling machine, they found that an increase in tamping force resulted in an increase in plug strength, with the fill weight remaining constant. The mechanical strength of individual segments did not increase further when an additional segment was compressed over them using the same tamping force. They showed that with microcrystalline cellulose, the addition of 0.1% magnesium stearate was the optimum concentration for both fill weight and mechanical strength of the plugs, whereby the mechanical strength of the plugs varied from approximately 2 to 26 mN, depending on the compression forces applied.
Guo et al.71 measured the breaking force of size 1 powder plugs of 12 mm length made on a compaction simulator at a saw-tooth speed of 50 mm s−1 and an approximate force of 250 N. Similarly to tabletting,132 the use of a compaction simulator enabled the recording of the “work of plug formation” (i.e., area under the force–displacement curve).71 Pregelatinized starch did not form plugs of measurable mechanical strength and anhydrous lactose plugs were found to have a mechanical strength of 160 mN, whereas various microcrystalline and silicified microcrystalline cellulose batches formed plugs of mechanical strengths between 240 and 820 mN. The work of plug formation was similar for pregelatinized starch, anhydrous lactose, and silicified microcrystalline cellulose with a median particle size of 50 μm, yet the mechanical strength of the plugs of the latter material was significantly greater than that for anhydrous lactose. Equally, the work recorded for microcrystalline cellulose, median particle size of 90 μm, was approximately the same as that recorded for the equivalent high-density silicified microcrystalline cellulose, but the mechanical strength was only about half that for the plugs made from the silicified powder. As in tabletting, the work put into plug formation not only is translated into interparticulate adhesion but also reflects losses attributed to interparticulate and particle-die wall friction as well as loss attributed to emission of heat.133 As silicification changes the surface topography of microcrystalline cellulose,134 one reason for the increase in plug strength might be an increase in interparticulate forces and a reduction in interparticulate and particle-die wall friction owing to the silicon dioxide particles that are mainly located on the surface of the microcrystalline cellulose particles.135 Another explanation could be the higher density of the silicified powders and the formation of less porous plugs.71 The difference in surface topography and its effect on friction could also explain the differences in the mechanical properties observed for pregelatinized starch compared to anhydrous lactose plugs, but differences in particle density and plug porosity achieved are equally likely. Presumably, both mechanisms will contribute to these findings, but to a varying degree depending on the powders tested.
Heda et al.72 reported values for the mechanical strength of plugs made from binary powder mixtures. They presented plug breaking force as a function of the ratio between the two mixture components, that is, for mixtures of anhydrous lactose and pregelatinized starch, anhydrous lactose and coarse-grade microcrystalline cellulose, and direct-compression ascorbic acid and coarse-grade microcrystalline cellulose. The breaking force–mixture ratio profiles showed a remarkable similarity to those obtained in tabletting when compressing mixtures of brittle lactose monohydrate and ductile sodium chloride;136 that is, the development of the plug strength is neither synergistic nor additive for the three types of mixtures studied. Fell136 attributed the non-synergistic, non-additive behavior of binary mixtures to the differences in particle deformation under load; the increase in the number of lactose monohydrate particles in the binary mixture attributed to brittle fragmentation was stated as the reason for the drop in mechanical strength when lactose monohydrate was used in higher proportions than the ductile sodium chloride. However, the powder plugs were made with a compression force of only 200 N,72 which should not cause significant particle deformation other than from the elastic type and hence the reasoning proposed by Fell136 does not apply here. Heda et al.72 unfortunately did not comment further on their findings.
Guo and Augsburger85 compared the maximum breaking force of plugs made with a dosator-nozzle machine at 50 and 100 N. They found that when doubling the compression force, the maximum breaking force of a variety of microcrystalline and silicified microcrystalline cellulose powders trebled or even quadrupled, but no explanation was provided for this effect.
In the articles cited above published by Augsburger’s research group, the breaking forces were determined with an in-house apparatus. It appears equally possible to use dynamic mechanical analysis (DMA). DMA equipment is very versatile, and one of the attachments is a three-point bending rig. DMA can test the samples using a defined stress or strain ratio and can apply forces in a constant and increasing fashion until the sample fails, similar to the equipment used by Augsburger’s group. However, DMA also allows the use of dynamic nondestructive test methods; it can measure creep and relaxation and can provide temperature–time and frequency scans.137 For purposes of research, DMA has been used as a nondestructive test alternative in investigations of the mechanical strength of tablets138,139 and hence could provide useful information about the structure and mechanical behavior of powder plugs.
Low-Pressure Compression
Modeling of Low-Force Compression
In 1999, Heda et al.97 proposed that classical compression physics routinely used in the development and optimization of tablet formulations should be extended to the development of powder/granule-filled hard capsule formulations by adapting the models to the much lower pressures used in both dosator-nozzle and tamp-filling machines. This approach has since been called “low-force compression physics.” In adapting standard tabletting models for this purpose, Heda et al.97 employed a compaction simulator equipped with a die that was much longer than usual tabletting dies to facilitate the formation of the comparatively long powder plugs used for capsule filling. The use of this simulator is a scientific approach that allows the precise control of applied stresses and strains as well as their rates, which can affect the outcome of such studies. Unfortunately, compaction simulators are rather expensive and not generally accessible. In 1988, Jones25 reported the use of a powder plug simulator, a low-cost benchtop equipment to study plug formation as a function of applied pressure and/or achieved plug length. In 1998, Jones6 reported that after 10 years of experience with this equipment, the results obtained had demonstrated that this simulator could be successfully used to assess the filling performance of formulations for both tamp-filling and dosator-nozzle machines. In this paper, he demonstrated how this equipment could be used to optimize formulations in terms of excipients used, optimum lubricant concentration, and mixing time. By then, he had developed a fully digitized prototype of the powder plug simulator, which was used as a template for the development of the commercially available Bosch capsule plug simulator (Figure 9.3). This apparatus can be used in a similar way to the compaction simulator, but it relies more on the skill of the operator to ensure an even stress or strain rate.


Figure 9.3Digital powder plug tester (Robert Bosch Inc). (a) Digital powder plug tester. (b) Electronic control panel of the digital powder plug tester.
Low-force compression physics is based on the parameterization of the relationship between plug properties such as length, volume, and density, and the force or pressure applied. The model parameters obtained have to be interpreted in line with solid-state physics principles, which can be problematic. As discussed by Lüdde and Kawakita,140 low-force compression can be applied to a powder by means of a compaction machine (e.g., tablet press, compaction simulator, and powder plug simulator) or by tapping the powder in a jolting volumeter. Models for the parameterization of the low-force compression profiles can hence be resourced from the literature on powder compaction and flow. In the following sections, several of these models will be studied for their power and meaningfulness when used to parameterize low-force compression profiles related to capsule filling.
The work on parameterization of low-force compression profiles has mainly been conducted by three research groups, that is, Augsburger’s at Maryland University in Baltimore, Sonnergaard’s at the Royal Danish School of Pharmacy, and Podczeck’s at University College, London. They favored different models and also used different types of equipment, which makes an objective comparison of their work difficult. Hence, a small study was undertaken to obtain low-force compression profiles for a set of powders and granules of different particle sizes. Basic information of the powders and granules used is collated in Table 9.1, and the low-force compression profiles are shown in Figure 9.4. The low-force compression models are in fact pressure relationships; the force values, which ranged from 10 to 150 N, were converted into pressures. Plugs were formed with size 0 tooling.
Powder | Manufacturer | Median Particle Size (μm) | Material Density(g cm−3) | Plug Weight (mg) | Plug Formation |
---|---|---|---|---|---|
MCC 105 | FMC, Little Island, Cork, Ireland | 19 | 1.52 | 200 | Firm |
MCC 101 | FMC, Little Island, Cork, Ireland | 50 | 1.52 | 180 | Firm |
MCC 102 | FMC, Little Island, Cork, Ireland | 90 | 1.52 | 180 | Firm |
LM fine | Borculo Whey, Saltney, UK | 6 | 1.54 | 330 | Firm, sticky |
LM Medium | Borculo Whey, Saltney, UK | 43 | 1.54 | 330 | Firm |
LM Coarse | Borculo Whey, Saltney, UK | 101 | 1.54 | 330 | Crumbling |
Sorbitola | Merck, Darmstadt, Germany | 375 | 1.49 | 240 | Firm |
Sorbitolb | Merck, Darmstadt, Germany | 980 | 1.49 | 215 | Firm |

Figure 9.4Plug density as a function of tamping pressure for a series of pharmaceutical excipients, obtained using the digital powder plug tester first described by Jones.6
The models are studied in the order of (1) models taken from powder flow studies using tapping devices, (2) models that have been applied to both tap and compression data, and (3) models that require powder compression in a punch and die system. Within these categories, the models are investigated in the order of the year of their first recorded use.
Angle of Internal Flow61
Varthalis and Pilpel61 studied powder flow using a jolting volumeter. They plotted a term, K (K = E2n/(1 − E), with E being the porosity of the powder bed after n taps), as a function of the number of taps n and found that for a number of powders and powder mixtures, this resulted in a straight line of the form K = bn + K0. They ignored the intercept K0 and only used the slope b, from which they obtained the angle of internal flow θ (θ = tan−1b). For use in low-force compression, the number of taps has to be replaced by the compression pressure P, that is,

The application of Equation 9.4 to the data introduced in Figure 9.4 is illustrated in Figure 9.5. The model does not provide a set of straight lines for low-force compression using the powder plug simulator. Instead, there is an initial nonlinear phase, followed by a linear part, which starts approximately at 1.29 MPa. The relationships have been treated statistically using linear regression analysis, including only data between 1.29 and 2.76 MPa. The results are summarized in Table 9.2. For the powders, the angle of internal flow θ increases with particle size, while for the granules, it decreases. As values for this model have not been reported for low-force compression in the literature, a direct comparison is not possible. According to Varthalis and Pilpel,61 the value of θ is an indirect measure of interparticulate friction during powder flow. In terms of low-force compression, this would mean that the value represents interparticulate friction during particle rearrangement enforced by the applied pressure. The values (Table 9.2) imply that there is more interparticulate friction between microcrystalline cellulose particles than between lactose monohydrate particles, which could be explained by differences in their surface morphology, with microcrystalline cellulose particles being much rougher than those of lactose monohydrate. This can be inferred from scanning electron micrographs for microcrystalline cellulose141 and lactose monohydrate.142 Equally, Sorbitol granules have a fairly rough surface structure, which could explain their comparatively higher values of θ, but here, the relationship with particle size is inverted. The difference in particle size is almost three times and might have resulted in very large differences in initial powder porosity, which might be easier to densify with a low force than an already densely packed powder bed with no room for free movement.

Figure 9.5Parameterization of the data presented in Figure 9.4 using Equation 9.4, that is, a modification of the model described by Varthalis and Pilpel.61
Powder | K0 (MPa) | tan θ | θ (°) | R2 | RMS |
---|---|---|---|---|---|
MCC 105 | 0.704 | 0.974 | 44.2 | 0.999 | 1.39 |
MCC 101 | 0.979 | 1.220 | 50.7 | 0.999 | 1.74 |
MCC 102 | 0.821 | 1.377 | 54.0 | 0.999 | 1.96 |
LM fine | 0.268 | 0.435 | 23.5 | 1.000 | 0.62 |
LM medium | 0.214 | 0.577 | 30.0 | 1.000 | 0.82 |
LM coarse | 0.207 | 0.600 | 31.0 | 1.000 | 0.86 |
Sorbitola | 0.452 | 0.897 | 41.9 | 0.999 | 1.28 |
Sorbitolb | 0.546 | 0.586 | 30.4 | 0.997 | 0.84 |
When determining the angle of internal flow from powder packing studies, Newton and Bader143 found a decrease in its value with increasing particle size of lactose monohydrate and acetylsalicylic acid, but the values had similar magnitudes ranging from about 20° to 50°. They reported linear relationships between the angle of internal flow and capsule fill weight and drug dissolution time when filling acetylsalicylic acid alone using a tamp-filling machine simulator. The fill weight decreased and the drug dissolution time increased with an increase in the value of θ. Similarly, there was a linear relationship between the angle of internal flow and capsule fill weight for mixtures of the drug with lactose monohydrate, but the relationship with the drug dissolution time was no longer present. When using an instrumented mG2 dosator-nozzle machine simulator, no relationships between particle size and the values of θ were found.112 Nikolakakis et al.144 also did not observe any significant relationships between θ values obtained with tapping experiments and the coefficient of fill weight variability when filling powders on a dosator-nozzle machine. When filling herbal powders, Podczeck et al.69 found that the coefficient of fill weight variability was directly related to the angle of internal flow when using a tamp-filling machine and inversely related when using a dosator-nozzle machine. Tan and Newton112 defined a powder having an angle of internal flow of 45° as “relatively free flowing,” while powders with values higher than 50° were classed as “cohesive.” When using low-force compression, such interpretation is less straightforward. Microcrystalline cellulose type 102 is free flowing, as are coarse lactose monohydrate and Sorbitol granules, yet the values for θ range between 54° and 30.4°, and the non-free-flowing powders have values in between this range. Similar powders except for fine and medium lactose monohydrate and microcrystalline cellulose type 105 could be successfully filled into hard capsules using a tamp-filling machine without addition of a lubricant.55,60 The relevance of the angle of internal flow determined from low-force compression values for the filling of powders and granules into two-piece hard capsules hence requires further investigation.
Compaction Constant T according to Mohammadi and Harnby145
When determining the minimum bulk density of a powder using the standard measuring cylinder method, it is very difficult to derive at an exact value and success depends on the skills of the operator. Mohammadi and Harnby145 suggested overcoming this problem by fitting tap density data obtained with a jolting volumeter to a model equation describing the relationship between volume reduction and number of taps. By exchanging the number of taps with the pressure applied, the following model equation can be obtained:

Here, dP is the plug density at pressure P, d0 is the theoretical powder (plug) density at zero pressure, and dP∞ is the plug density at the maximum pressure applied, and T is the compaction constant. In order to obtain the model constants, nonlinear regression analysis is required. The results obtained from the low-force compression profiles shown in Figure 9.4 are listed in Table 9.3. The values for dP∞ are equivalent to the maximum pressure of 2.76 MPa applied. The start values for the nonlinear regression analysis were 0.4, 0.6, and 5 for d0, dP∞, and T, respectively, and for fine and medium lactose monohydrate as well as size fraction 300–500 μm of the Sorbitol granules, a constraint model with d0 and dP∞ set to ≥0 had to be used. For microcrystalline cellulose and lactose monohydrate, maximum values for T are observed for the medium particle size grades, and in general, the values are very small. When using tap density data, the values for T reported were in the range of 5–4060 and 12–2143 for powders, 75–136 for granules,55 and 18–135 for powdered herbs.69,146 As expected, when applying an axial pressure to powders in a die, densification is much more rapid than when using a tap volumeter. Aling and Podczeck146 filled herbal leaf powders into size 1 hard capsules using a tamp-filling machine and found that a larger fill weight could be achieved for powders with smaller values of T, whereby T was determined from parameterization of powder plug density–pressure profiles according to Equation 9.5. The T value was also predictive of the coefficient of fill weight variability at higher compression settings. This is, however, the only report on the use of Equation 9.5 to parameterize low-force compression data to date.
Powder | T | d0 (g cm−3) | dP∞ (g cm−3) | R2 | RMS |
---|---|---|---|---|---|
MCC 105 | 1.425 | 0.345 | 0.560 | 0.998 | 1.06 |
MCC 101 | 2.107 | 0.312 | 0.525 | 0.997 | 0.93 |
MCC 102 | 1.728 | 0.315 | 0.486 | 0.998 | 0.91 |
LM fine | 1.340 | 0.595 | 0.777 | 0.999 | 1.58 |
LM medium | 4.995 | 0.607 | 0.846 | 0.999 | 1.49 |
LM coarse | 2.328 | 0.610 | 0.731 | 0.997 | 1.48 |
Sorbitola | 4.997 | 0.447 | 0.719 | 0.982 | 1.15 |
Sorbitolb | 1.060 | 0.357 | 0.653 | 0.999 | 1.25 |
Note: LM, lactose monohydrate; MCC, microcrystalline cellulose; R2, linear determinant; RMS, root–mean–square deviation (residual analysis).
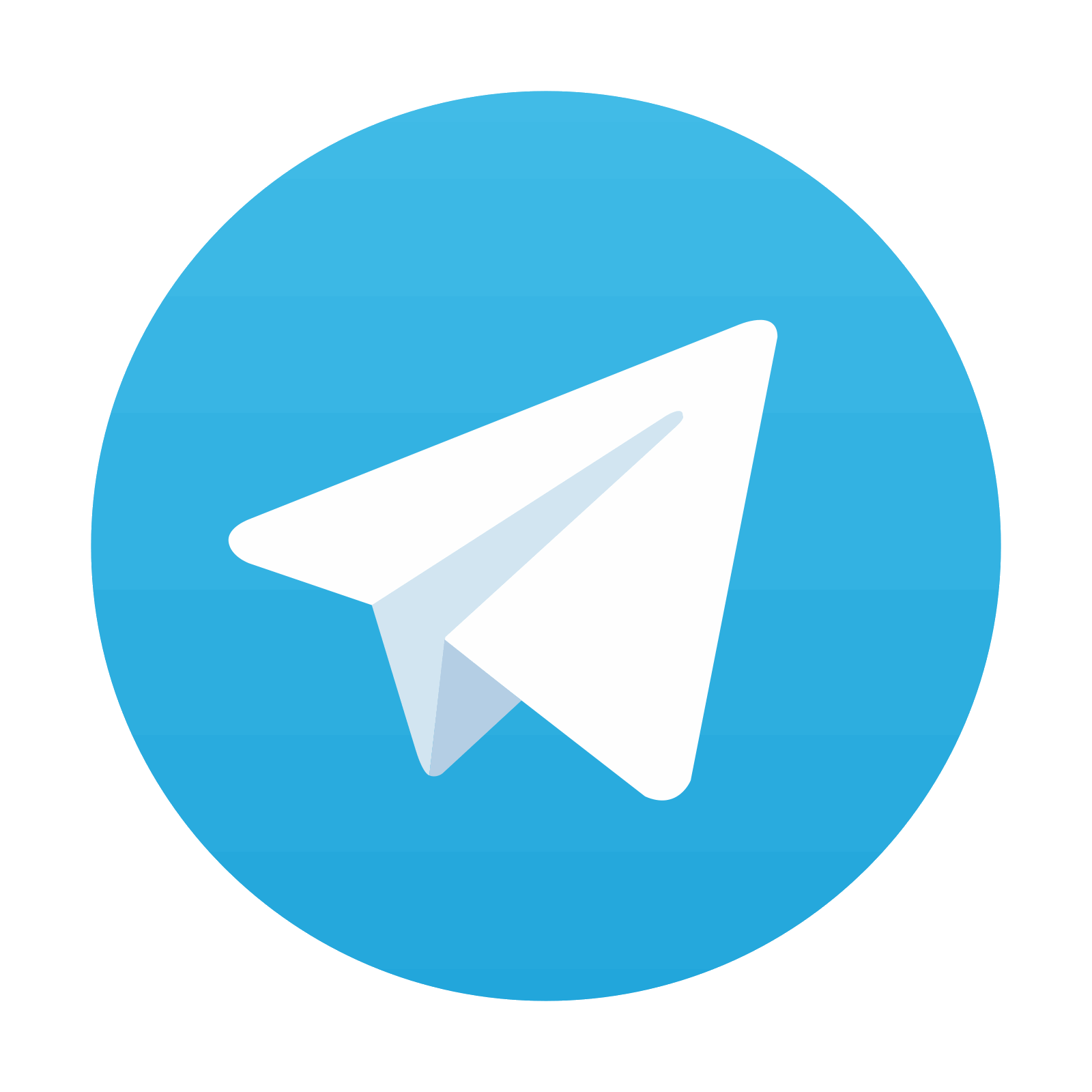
Stay updated, free articles. Join our Telegram channel
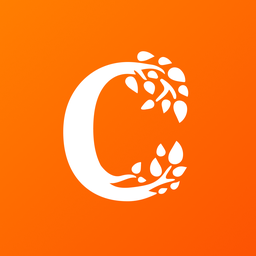
Full access? Get Clinical Tree
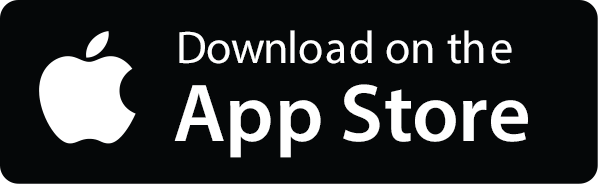

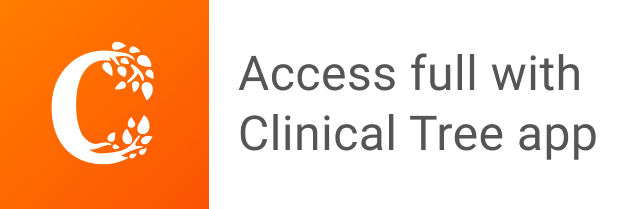