Figure 8.1The parameters studied for optimization of the formulation and process variables (18) and a representative response surface* (Q10 = percent dissolved in 10 min). (Courtesy of L. Augsburger.) *Response surface plotted from data generated under University of Maryland–Food and Drug Administration collaborative agreement No. 223-91-3401.
Filling Technology
Automatic Capsule-Filling Machines
The various types of filling machines available to the pharmaceutical industry may be conveniently categorized according to the manner in which the dose of the formulation is measured into the capsule body. The methods of dosing for dry powders can be divided into direct and indirect types.19,20 In the direct type, the capsule body is used as the volumetric chamber in which the dose of the formulation is measured. In the indirect type, the quantity to be filled is measured in a chamber completely independent of the capsule body. There is a great variety of capsule-filling equipment available, which ranges in output from 1000 to more than 200,000 capsules per hour. The machines can also be grouped into two distinct types based on their motion, those that operate in an intermittent fashion (Hofliger-Karg, Harro-Hofliger [H&H], Zanasi A Z-2 0, AZ-40, Macolar, and Dott.Bonapace RC-530) and those that have a continuous motion (MG2, Zonasi Z5000, Farmatic, Osaka). However, despite these differences, all machines have the following operational steps in common:
Orientation and separation of the shell into its components—body and cap
Dosing the material into body
Rejoining the cap and body
Capsule-filling equipment has been previously discussed in detail by Lightfoot in Chapter 6. Three main dosing methods may be identified, and these are briefly reviewed in the subsequent paragraphs to support a discussion of their formulation requirements.
Auger Fill Principle
At one time, nearly all capsules were filled by means of semiautomatic equipment, wherein the powder is driven into the capsule bodies by means of a rotating auger. This type of filling machine is exemplified by the Capsugel/Type 8 machine. The empty capsule bodies are held in a filling ring that rotates on a turntable under the powder hopper. The fill of the capsules is primarily volumetric. Because the auger mounted in the hopper rotates at a constant rate, the delivery of powder to the capsules tends to be at a constant rate. Consequently, the major control over fill weight is the rate of rotation of the filling ring under the hopper. A faster rate produces lighter fill weight because bodies have a shorter dwell time under the hopper.
Vibratory Fill Principle
The Osaka machines employ a vibratory feed mechanism. In this machine, the capsule body passes under a feed frame that holds the powder in the filling section. In the powder, a perforated resin plate is positioned that is connected to a vibrator. The powder bed tends to be fluidized by the vibration of the plate, and this assists the powder to flow into the bodies through holes in the resin plate. The fill weight is controlled by the vibrators and by setting the position of the body under the feed frame. The process affords only slight compression of the powder against the resin plates.
Piston-Tamp Principle
Today, most capsules are filled on what may be described as piston-tamp machines. These are fully automatic encapsulators in which pistons or tamping pins are employed to lightly compress the individual doses of powders into plugs (sometimes referred to as “slugs”) that often resemble soft tablets in consistency and eject them into empty capsule bodies. There are two types of piston-tamp encapsulators: (1) the dosing disc type and (2) the dosator type.
Dosing Disc Machines
This type of machine is exemplified by the Bosch (formerly Hofliger Karg) GKF models and the H&H, KFM models. The dosing disc, which forms the base of the dosing or filling chamber, has a number of holes bored through it. A solid brass “stop” plate slides along the bottom of the dosing disc to close off these holes, thereby forming openings similar to the die cavities of a tablet press. The powder is maintained at a relatively constant height over the dosing disc, though the powder bed is not actually leveled. Five sets of tamping pins (in GKF machines) compress the powder into the cavities to form plugs. The dose is controlled by the thickness of the dosing disc (e.g., cavity depth), the powder depth, and the tamping pressure. These machines generally require that formulations be adequately lubricated for efficient plug ejection to prevent filming on tamping pins and to reduce friction between any sliding components that may come into contact with powder. A degree of compactibility is important, as coherent plugs appear to be desirable for clean, efficient transfer at ejection. However, there may be less dependence on formulation cohesiveness than exists for dosator machines. The H&H machine is similar to GKF machines, except that it employs only three tamping stations. However, at each station, the powder in the dosing cavities is tamped twice before rotating a quarter turn to the next station. One other difference between them is that the powder in the filling chamber of H&H machines is constantly agitated to help in the maintenance of a uniform powder bed depth.
Dosator Machines
The dosator machines are exemplified by the Zanasi, MG2, Dott.Bonapace, and Macolar machines. The dosator consists of a cylindrical dosing tube fitted with a movable piston. The end of the tube is open, and the position of the piston is preset to a particular height to define a volume that would contain the desired dose of powder. In operation, the dosator is plunged down into a powder bed maintained level at a constant preset height by agitators and scrapers. The powder bed height is generally greater that the piston height. Powder enters the open end and is slightly compressed against the piston (sometimes termed “pre-compression”).21 The dosator, bearing the plug, is withdrawn from the powder hopper and is moved over to the empty capsule body where the piston is pushed downward to eject the plug. The primary control over fill weight (for a given set of tooling) is the initial piston height in the dosing tube. A secondary control of weight is the height of the powder bed into which the dosator dips.
Formulation Requirements for Plug-Forming Automatic Capsule-Filling Machines
Usually, automatic capsule filling is carried out on either the dosator or the dosing disc types of machines. The basic requirements of a powder formulation for clean and efficient filling on these machines are as follows:
Good fluidity
Ability to form a cohesive plug
Sufficient lubricity
A reasonable bulk density
The basic requirements for a dosator type and dosing disk machine are summarized in Table 8.6.
Requirements | Dosing Disk | Dosator |
---|---|---|
Lubricity | Adequate lubrication is required for efficient plug ejection, to prevent filming and reduce friction of sliding components | To ensure clean ejection |
Compactibility | Coherent plugs are desirable for clean plug ejection | Necessary to ensure that the plug does not break up when the dosator is withdrawn from powder bed Since lubricants are generally hydrophobic, a poorly wettable plug may result if too much compression force is used The plug should not protrude above the capsule Overfilling of capsule |
Flowability | Auger feed in hopper aids filling of formulations with poor flow | To ensure weight uniformity |
Good flow is necessary to produce a working powder bed that can reform adequately after doses have been removed. A degree of compactibility or cohesiveness under pressure is important to prevent loss of material from the end of the plug during transport to the capsule shell. Sufficient lubricity in a formulation is needed to permit easy and efficient ejection of the plug and prevent or minimize adhesion to the tooling and other surfaces in contact with the formulation. The necessity for a reasonable bulk density becomes important when dealing with active ingredients that are administered in large doses, since the formulation is limited by the available or preferred capsule sizes.
The instrumentation of capsule-filling machines, which is discussed in detail in Chapter 7, has provided new insights into the interplay of formulation and machine operating variables that can affect both the manufacturability of capsules and their performance as drug delivery systems. The basic formulation requirements of the automatic capsule-filling machines operating on the piston-tamp principle as reported in the literature to date are reviewed in this section.
Flowability
Repeated extraction of powder from a previous dosing site is a common problem on automatic capsule-filling machines because of inadequate replenishment or remixing of the powder bed. This could be overcome by either mechanical or formulation means. In most machines, the powder bed is reformed by mechanical devices such as static agitators and active-stirring devices or by the application of suction to the base of the powder to densify it at the dosing point. An alternative method that is used on continuous motion dosator machines is the rotation of the dosator assembly and the powder hopper being maintained at different speeds and out of synchronization so that the dosator enters the bed in the same position only after a few rotations.
Simple powder flow measurements such as angle of repose, Hausner’s ratio, flow rate, and minimum orifice diameter, although limited to the study of free-flowing powders, have been used successfully to predict the capsule-filling performance for powders. Schatz22 characterized powders by measurements of angle of repose and changes in bulk density using a jolting volumeter. These properties were used to compare their filling performance on a dosator machine, Zanasi RV-59, and a dosing disc machine, Hofliger-Karg (H&K) GKF 70. Various blends of lactose, talc, and magnesium stearate were tested. The blends with poorest flow properties gave the worst filling performance and the more free-flowing ones gave the best fill weight uniformity. An angle of repose of less than 42° was proposed as the value to be used for achieving satisfactory filling. However, free-flowing powders required a higher degree of compaction to achieve satisfactory filling on the dosator machine. According to this study, the inclusion of starch in the mixture overcame this aforementioned problem because it allowed reasonable compression to be employed successfully.
Kurihara and Ichikawa,23 working on an H&K machine, reported that variation in fill weight was closely related to the angle of repose of the formulation; however, a minimum point appeared in the plots of the angle of repose versus coefficient of variation of fill weight. Apparently, the powders with higher angles of repose did not have sufficient mobility to distribute well under the acceleration of the intermittent-indexing motion. At lower angles of repose, the powder was apparently too fluid to maintain a uniform bed. However, the investigators did not appear to make use of powder compression by tamping, and this complicates the interpretation of their findings.
Some researchers have examined the relation between formulation flow properties and weight variation on Zanasi machines. Irwin et al.24 compared the weight variation of capsules filled on a Zanasi LZ-64 machine from formulations composed of different diluents and lubricants. The formulations had different flow properties, as judged in a recording flow meter. He showed that greater uniformity of fill weight could be achieved with powders that were more free flowing or having better flow rate. This was explained by the superior replenishment and mixing of the powder extraction sites in the powder bed. Chowhan and Chow25 compared powder consolidation ratio with the coefficient of variation of capsule weight and found a linear relationship for a test formulation containing 5% or 15% drug, 10% starch, and 0.5% magnesium stearate, and lactose q.s. The capsules were filled on a Zanasi machine.
The bulk density (loose and tapped) of the powder has been linked to flowability, as measured by the “angle of internal flow”26 and Carr’s CI.27 The latter parameters have significant advantage over other methods of measuring flow, such as angle of repose, and so on, because they are not limited to free-flowing powders. Carr’s CI is defined as follows:

where TBD = tapped bulk density and LBD = loose bulk density.
Powders with values less than 15% are considered to have excellent flow and those with CI values greater than 40% have very bad flow.27 The angle of internal flow is also calculated from the bulk density data. Verthalis and Pilpel26 described a method of obtaining a straight line from the graph of bulk density as a function of the number of taps. By plotting the expression K = E2n/(1 − E), where E is the porosity versus the number of taps n. If Ko is the y-intercept of this plot, a straight line passing through the origin can be obtained by plotting K − Ko as a function of n. The slope of the line passing through the origin is termed as the angle of internal flow, <p. This angle effectively reflects the rate of change of bulk density with the number of taps.
Tan and Newton28 using the instrumented MG2 capsule-filling machine simulator developed by Jolliffe et al.29 studied the capsule-filling performance of five pharmaceutical excipients, Starch 1500, Avicel PH 101, calcium carbonate, maize starch, and Lactose B 170. They found a significant correlation between the coefficient of variation of the fill weights and a number of flow parameters such as Carr’s CI, Hausner’s ratio, angle of repose, Kawakita’s constant a, and Jenike’s flow factor.
The flow properties of a formulation can be improved by the addition of a glidant. Glidants are fine particles that appear to coat the particles of the bulk powder and enhance fluidity by one or more of several mechanisms:30,31
Reducing roughness by filling surface irregularities
Reducing attractive forces by physically separating the host particles
Modifying electrostatic charges
Acting as moisture scavengers
Serving as ball bearings between host particles
Glidants include the colloidal silicas, cornstarch, talc, and magnesium stearate. Usually, there is an optimum concentration for flow, generally less than 1% and typically 0.1–0.5% when colloidal silicas are used. The optimum concentration may be related to the concentration sufficient to coat host particles.32 Exceeding this concentration will usually result in no further improvement in flow and may even cause worsening of flow.
Hogan et al.9 investigated the relationship between drug properties, filling parameters, and release of drugs from hard gelatin capsules using multivariate statistical analysis. They concluded that the optimum concentration for Aerosil (colloidal silica) appears to be 1%, with respect to both coefficient of fill weight variation and flowability, as measured by Carr’s CI.
Nair et al.33 investigated the comparison between the Carr index, Johanson flow rate, and critical orifice diameter of lubricated excipients and drug blends. The Johanson flow rate appeared to be a more discriminating method among the tests used to compare.34,35
More recently, Nalluri et al.36 investigated the co-relation between powder avalanching and shear cell parameters of drug–excipient ratios to design minimal weight variation into the capsules. They concluded by running a series of binary blends of paracetamol and microcrystalline cellulose that the flow property increased until it reached a percolation threshold when abrupt changes in flow behavior were observed. This correlated well with the capsule weight variability and the angle of internal friction. On the basis of the results, they proposed a strategy to design minimal weight variability into powder-filled capsules by using the powder avalanching as a control strategy.
Osorio and Muzzio37 investigated a wide array of powder flow measurement techniques using the more recent Freeman Technology Rheometer V.4 (FT4). Their methods have used flow parameters such as gravitational displacement rheometer, flow index, powder rheometer compressibility, basic flow energy, cohesion, and ffc measurements in a shear cell on the FT4. Their results show good co-relation between the measured parameters and weight and weight variability in the filled capsules.
Faulhammer et al.38 recently used a predictive statistical model for filling of low–fill weight inhalation products using dosator nozzles. Using the Quality by Design Paradigm, they were able to determine the effect on the critical quality attribute (CQA), fill weight, and weight variability. They identified critical material attributes (CMAs) and critical process parameters (CPPs) that affected the CQA. The model developed was able to predict the fill weight and weight variability for the inhalation product. They validated the model and established a design space for the performance of different types of inhalation grade lactose on filling based on the CMAs and CPPs.
Lubricity
Fully automatic capsule-filling machines apply a significant amount of compression (though well below that applied in tableting), usually up to 100 N, but values as high as 300 N have also been reported. The powder is compressed into a coherent or apparently (partially) coherent plug. Apart from increasing the density of the powders above their maximum tapped bulk density, this compression may necessitate the addition of anti-adherents to the formulation to prevent the powder adhering to the metal surfaces of the tooling (dosators and pistons) used in dosing. The powder plug must also be removed cleanly from the dose-measuring device, which necessitates the inclusion of a “true lubricant” in the formulation.
Plug ejection force measurements make possible objective decisions on type and level of lubricant to be included in formulations. The earliest reported work on an instrumented capsule-filling machine by Cole and May39 included an examination of the effect of a lubricant, magnesium stearate, on the compression and ejection forces on a dosator machine, Zanasi LZ-64. They demonstrated a considerable reduction in the forces when 0.5% magnesium stearate was added to a lactose mixture. Small and Augsburger40 later reported a detailed study of the lubrication requirements of the Zanasi-LZ 64. Three fillers were studied (microcrystalline cellulose, pre-gelatinized starch, and anhydrous lactose). Powder bed height, piston height, compression force, and lubricant type and concentration were studied to determine their effects on ejection force. In general, anhydrous lactose exhibited higher lubrication requirements than either pre-gelatinized starch or microcrystalline cellulose. Comparing several concentrations of magnesium stearate, minimum ejection forces were recorded at 1% with anhydrous lactose, at 0.5% with microcrystalline cellulose, and at 0.1% with pre-gelatinized starch. Magnesium lauryl sulfate compared favorably with magnesium stearate for pre-gelatinized starch but was not as efficient as magnesium stearate for the other two fillers. Also, the magnitude of the ejection force was affected by machine-operating variables. Ejection force increased with the compression force. However, at a given compression force, ejection force also increased with an increase in either the piston height or the powder bed height. These results suggest the possibility of manipulating machine-operating variables to reduce the lubricant requirements in a formulation.
The lubricants may not always be beneficial to filling performance. Takagaki et al.41 found in a study using a dosator machine that fill weight uniformity decreased at higher lubricant levels. This was explained by the loss in cohesiveness of the plug by the addition of lubricant.
Mehta and Augsburger42 reported the effect of magnesium stearate on plug hardness and the dissolution of hydrochlorothiazide from capsules filled on a Zanasi LZ-64. The fillers were microcrystalline cellulose and anhydrous lactose. They concluded that it might be advisable to sometimes exceed the minimum lubricant concentration requirement of a capsule-filling machine with fillers such as microcrystalline cellulose. The mechanical strengths of the plugs produced in a dosator may be reduced by the amount of lubricant used, and this could have a beneficial effect on drug dissolution. Small43 showed similar results with pre-gelatinized starch, using acetaminophen as a model drug. A similar finding was also reported by Stewart et al.44 for the dissolution of riboflavin from microcrystalline cellulose plugs. Interestingly, hand-filled rifampicin capsules also exhibited a similar phenomenon. Nakagawa et al.45 found that up to a limit, increasing the blending time of magnesium stearate (tantamount to increasing the concentration) improved the dissolution rate of rifampicin. The effect was most marked at the lowest lubricant levels studied.
The minimum lubricant concentration requirement of one type of filling machine might be too much for another type and could affect the final product specification (dissolution requirement). Ullah et al.46 encountered an in vitro dissolution problem during scale-up of cefadroxil monohydrate, a water-soluble drug product. Initial formulation development had been carried out on a Zanasi LZ-64 with a blend containing 1% magnesium stearate as lubricant. Scale-up on a Hofliger-Karg GKF 1500 (H&K) showed a significantly slower dissolution rate for the drug when compared to the capsules produced on a Zanasi LZ-64. Analysis of the problem indicated that powder was being sheared during encapsulation on the H&K filling machine, leading to overcoating of the drug particles by magnesium stearate and a slower dissolution rate. Shear simulation studies were conducted to select the level of magnesium stearate appropriate for encapsulation on the H&K that would maintain a satisfactory in vitro capsule dissolution rate. A 0.3% w/w level of magnesium stearate was selected on the basis of the simulation studies. At this lubricant level, capsules were routinely produced on the H&K machine with satisfactory dissolution and encapsulation characteristics.
Tattawasart and Armstrong,47 using the simulator developed earlier by Britten and Barnett, studied the effect of lubricant concentration on plug formation. They found that 0.5% level of magnesium stearate provides adequate lubrication for lactose plugs. The simulator was designed to simulate the operating principle of the dosator machines. Shah et al.,48 working on an H&K GKF 330, found that the optimum level of the lubricant, magnesium stearate, was 0.1%, resulting in maximum plug strengths and fill weights, regardless of the number and intensity of the tamps used.
Compressibility, Compactibility, and Cohesiveness
Conflicting powder properties are required for processing on automatic capsule-filling machines. A free-flowing powder is needed for a homogeneous powder bed but a cohesive powder is preferable for powder retention during transfer of the powder to the capsule shell.
Compression is applied during the capsule-filling process to consolidate the powder for a couple of reasons: (i) to increase powder density and hence maximize the amount filled into a desired capsule size, and (ii) to aid powder retention as the plug is transferred from the dosing cavities to the capsule body. The latter could be more important on dosator machines and to a somewhat lesser extent on the dosing disc machines because the plug is supported underneath until the moment of transfer on the latter.
Jolliffe et al.49 have studied the aforementioned problem on dosator machines theoretically by the application of hopper design theory. The retention of powder during transfer requires the formation of a stable powder arch at the dosator outlet, and this depends on the angle of wall friction. Generally, theory predicts that cohesive materials will be retained with minimal compressive stress on rough dosator walls and that smoother walls provide the best conditions for retaining more freely flowing powders. On the basis of this theory, Jolliffe and Newton50 later demonstrated that for free-flowing particles to be retained, more compressive force is needed than for cohesive particles, which sometimes could be retained with no compression.
Jolliffe and Newton,51 using the MG2 simulator developed earlier,29 showed that capsule fill weights obtained using fine, cohesive powders are relatively insensitive to the compression applied by the piston and are able to give uniform fill weights over a wide range of compression settings. Coarse, free-flowing powders require a minimum compression to be uniformly filled and fill uniformity will only occur for small increases in compression above this. For both types of powders, compression above an optimum limit, that is, beyond its ability to pack more tightly by rearrangement, resulted in poor fill uniformity. This occurs at lower compression forces for coarse, free-flowing powders because of their lower compressibility. They validated their results obtained with the simulator using a production-scale MG2 machine. Shah et al.,48 working on a Hofliger-Karg GKF 300 filling machine, evaluated several compression parameters and concluded that, aside from station # 1, all tamping stations and all piston positions within a station contribute equally to plug formation. The nearness of station # 1 to the scrape-off bar results in nonuniform powder bed height and a high degree of compression force variability. They also showed that increases in tamping force resulted in harder plugs, as measured with a plug mechanical strength tester. However, plug strengths did not increase in mechanical strength when additional segments were compressed over them using the same force. The authors also found that target fill weights could be achieved using as few as three tamps.
Shah et al.,52 in a related study, observed the effects of number of tamps and tamping force on drug dissolution on the same machine, using hydrochlorothiazide as a model low-dose, poorly soluble drug. With increasing number of tamps, the dissolution rate was slower, the effect being most marked with dicalcium phosphate dihydrate as the filler. Inclusion of a disintegrant, 4% croscarmellose sodium, tended to nullify the effects of number of tamps or tamping force regardless of the filler used. Table 8.7 shows the quantitative comparison of the fluidity, lubricity, and compactibility requirements of a dosator and dosing disk encapsulation machine.
Formulation Characteristic | Dosator Type | Dosing Disc Type |
---|---|---|
Fluidity | The optimum values if Carr’s Index (CI) lies between 25 and 35 for best % CV of fill weights. | The optimum range of CI for efficient encapsulation is 18 < CI < 30. |
Lubricity | The amount of lubricant necessary for clean encapsulation may be around 0.5–1% depending on the formation. | The amount of lubricant required for successful encapsulation could be as low as 50% of the level used on a dosator machine. |
Compactibility/compressibility | Higher CIs produced stronger plugs and better % CV of fill weights. In a formulation with lower CIs (<20), higher compression forces about 150–200 N could pride better retention ability of the powder in the dosator tube. | Formulations with higher CIs tend to flood near the ejection station. Although this damming of powder may not affect the overall % CV, the process is certainly not very clean. Even though strong cohesion in a formulation is not required for successful transfer of the plug from the dosing disc to the capsule body, for certain very free-flowing formulations (granulations), moderately higher compression forces around 150 N would be beneficial. |
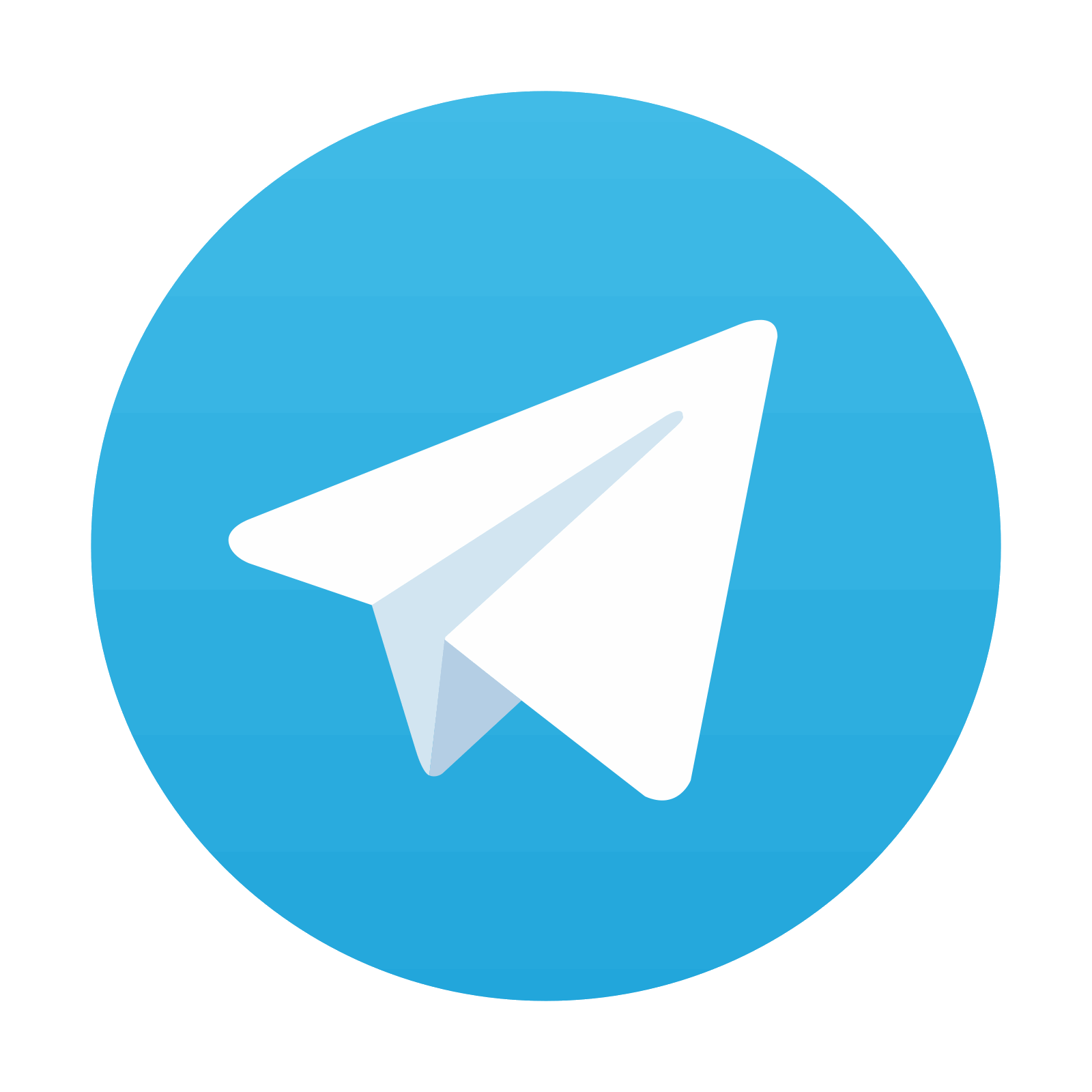
Stay updated, free articles. Join our Telegram channel
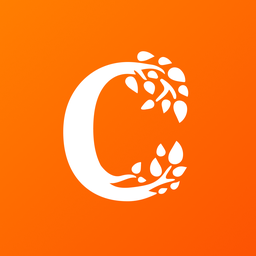
Full access? Get Clinical Tree
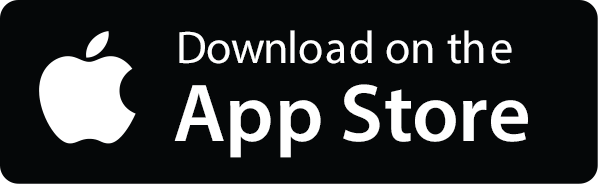
