30 This chapter deals with some of the practical aspects of dispensing, concentrating on the small-scale manufacture of medicines from basic ingredients. This process is called compounding or extemporaneous dispensing. Additionally, good practice which applies to all aspects of dispensing will be considered. The pharmacist undertaking extemporaneous dispensing has a responsibility to maintain equipment in working order, to ensure that the formula and dose are safe and appropriate and that all materials are sourced from recognized pharmaceutical manufacturers. There are also requirements concerning calculations, maintaining good records and labelling. Any staff involved in the process should be adequately trained. These requirements should all be incorporated within standard operating procedures (SOPs, see Ch. 11). The working environment needs to be organized, with well trained, efficient staff. A safe system of working is essential for a dispensary and the development and use of SOPs should be followed. Additionally, health and safety regulations must be applied in the dispensary. Weighing equipment can be divided into non-automatic and automatic weighing equipment. Non-automatic weighing equipment requires an operator to place and/or remove the items from the balance pan. Such weighing equipment can be a mechanical beam balance, which has a pan on one end of the beam for weights and a pan on the other end of the beam for the material to be weighed (Fig. 30.1) or it can be an electronic top-pan balance, in which case the substance to be weighed is placed on the pan and an electronic display gives the weight. Automatic weighing equipment is designed to automatically fill a package to the required weight without the intervention of an operator. Such equipment is used in the pharmaceutical industry, and nowadays for extemporaneous dispensing. Whichever type of weighing equipment is used, it must be suitable for its intended use and be sufficiently accurate. In the UK, weighing equipment must be calibrated in metric units and must be marked with maximum and minimum weights that can be weighed. The following points are important to ensure accurate weighing:
Dispensing techniques (compounding and good practice)
Practical aspects of dispensing
The working environment and procedures
Extemporaneous dispensing equipment and its correct use
Manipulative techniques used in dispensing and compounding
Ingredients and their selection
Introduction
Products no longer on the market or unavailable from the manufacturer
Products requiring an individualized dose, e.g. for paediatric or geriatric patients
Products requiring an individualized formulation for a patient, e.g. the removal of colouring agents
Veterinary products, e.g. formulations for different species.
The working environment and procedures
Organization
Equipment
Weighing equipment
General rules for the use and maintenance of weighing equipment
Balances must be placed on a level surface; most will incorporate a level indicator device to allow adjustment for a non-level surface
Balances’ readings must indicate zero, before use. If zero is not indicated, then incorrect readings, and hence weights, may be obtained
Strong draughts, caused by air conditioning or a breeze, can affect some balances and make a correct reading impossible. Therefore always site a balance in a draught-free area
Always keep the balance pan clean and free from debris
Regular checks with stamped weights should be made to ensure the balance is working correctly
If possible keep a record of when, and by whom, the check was carried out, as well as the result
Never weigh less than the declared minimum weight or more than the maximum weight declared on the balance
Do not weigh ingredients on a piece of paper, as this introduces a potential inaccuracy. The exception is when weighing greasy or semi-solid materials, e.g. white soft paraffin, when a counterbalanced piece of paper should be used
Always read the manufacturer’s instructions before using an electronic balance
Use tweezers to handle weights, if used. Never handle weights, as this will affect their accuracy and risks contamination.
Stay updated, free articles. Join our Telegram channel
Full access? Get Clinical Tree
Dispensing techniques (compounding and good practice)
Only gold members can continue reading. Log In or Register a > to continue
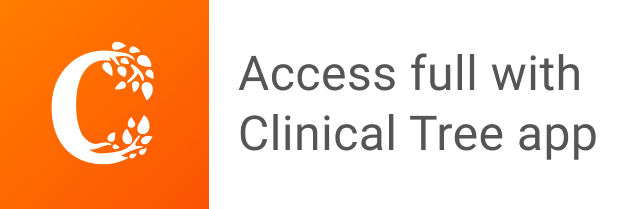