A. OVERVIEW
Two of the largest areas of materials chemistry involve polymers and ceramics, and both of these areas share similarities at the fundamental science level. A consideration of polymers as a prelude to the study of other materials has some important advantages. For example, many of the principles that govern the chemistry of ceramics can be understood in terms of polymer science. Thus, the underlying concepts of condensation reactions, molecular and materials flexibility, crosslinking, composites, and optical properties follow naturally from a knowledge of macromolecules and their behavior. Moreover, polymers are now widespread in technology, where they are used to enhance the properties of ceramics, metals, semiconductors, and optical materials. The differences between classical polymers and ceramics arise from the behavior of carbon compounds compared to those of the other main-group elements. Hybrid inorganic–organic polymers represent a halfway stage between classical polymers and ceramics, with some of the property advantages of both. Here we focus on the organic and inorganic–organic systems, as a prelude to a consideration of ceramics in Chapter 7.
Polymers are important materials because they are the basis of a large part of modern science and technology. Applications as diverse as lenses, housings for computers and telephones, photographic film bases, paint, thermal insulation, textile fibers, membranes, automobile and aircraft interiors and structural components, and a host of biomedical devices are based on polymers. The main reasons why polymers represent such an important part of materials science is that they can be fabricated easily, are corrosion-resistant and lightweight, and are generally inexpensive. They are designed and synthesized to give properties that range from elastomers to glasses, from soluble to insoluble materials, and from totally inert substances to reactive solids. They can also be colored by the introduction of dyes, and reinforced by the addition of other polymers or ceramics. Polymers are also key materials in the fabrication of semiconductor integrated circuits and in the development of optical devices (see Chapters 9 and 12).
In the following sections we consider first the main methods used for the synthesis of polymers, and then review structure–property relationships in these materials. Once the relationship between structure and properties is understood, it becomes possible to design new polymers with better combinations of properties. Finally, the characteristics of some example polymers are summarized at the end of this chapter. The ways in which polymers are utilized in important applications are considered in later sections of this book.
1. General Principles
Polymerization processes constitute one of the most remarkable aspects of modern chemistry. For many years, prior to the 1930s, the existence of macromolecules was believed to be impossible. Yet, today an enormous range of different polymers exists, all produced via relatively straightforward processes. These synthetic pathways begin with the linking together of large numbers of small-molecule monomers to form long polymer chains.
Three general types of monomers are utilized for the synthesis of polymers: (1) small molecules with double or triple bonds that can undergo addition–polymerization reactions; (2) molecules with two functional end groups that allow condensation reactions to take place; and (3) cyclic compounds that undergo ring-opening polymerization processes. The monomer and polymers to be mentioned in this chapter are shown in Table 6.1. In addition to these polymerization methods, some polymers are modified by subsequent reactions—the so-called macromolecular substitution reactions. The crosslinking of polymer chains can also be accomplished by secondary processes. These aspects are discussed in turn.
2. Addition Polymerization
Addition polymers represent the largest class of synthetic macromolecules in terms of total volume produced. This class includes materials such as polyethylene, polypropylene, polystyrene, poly(methyl methacrylate), polyisobutylene, styrene–butadiene copolymers (SBR rubber), poly(vinyl chloride), and poly(tetrafluoroe-thylene) (Teflon®) (see Table 6.1). Thus, addition polymerization is one of the main methods for the production of organic polymers.
a. The Overall Polymerization Mechanism.
Addition polymerization processes can be understood in terms of the following general steps:
1. Initiation. An unsaturated organic monomer is treated with an initiator compound to give a reactive species that will initiate the polymerization process. The action of heat or radiation on the monomer may also yield an activated species.
2. Chain Propagation. The initiated monomer adds to an unactivated monomer, and the resultant active dimer adds to another monomer to start an addition chain reaction. The polymer chains continue to grow until side reactions terminate the chain growth process or the monomer is depleted.
3. Chain Termination. This is a process in which the active chain ends are deactivated to bring chain growth to a halt.
4. Chain Transfer. The active end of a growing chain attacks the middle units of another chain or a residual monomer molecule to produce a new activated site and simultaneously terminates the original chain. If the attack takes place at a middle unit of another polymer, it may generate a branched structure.
These steps are summarized in reactions 1–4, where the asterisk (*) indicates an activated unit such as a free radical, anion, or cation, and T is a terminator molecule. The overall course of a polymerization depends on the chemical structure of the monomer, the type of initiator used, and the reaction conditions (solvent, dilution, temperature, etc.). The following discussion revolves around the different types of initiators.
b. Free-Radical Initiators.
This is one of the easiest ways to carry out an addition polymerization. Monomers such as styrene, methyl methacrylate, or ethylene are polymerized on a large scale by free-radical processes. The monomer is used undiluted, or it may be dissolved in an organic solvent or be part of an emulsion of water and an organic medium. Introduction of a small amount of an initiator, often followed by heating, then starts the polymerization process.
The initiator is a compound such as a peroxide or azo derivative that can decompose under mild or moderate conditions to generate free radicals as shown in reaction 5.
Typical free-radical initiators are aliphatic azo compounds, such as azo-bis-isobutyronitrile (AIBN) or peroxides such as benzoyl peroxide. Different initiators are chosen for use at different temperatures. Alternatively, ultraviolet light or γ rays may be employed to initiate polymerization because these sources of energy can generate free radicals from the monomer, the solvent, or added photosensitizers. Radiation polymerization has the advantage that it minimizes the number of impurities that are formed in the polymer—for example, from initiator residues.
The radicals formed will attack a few of the monomer molecules to convert them to free radicals, and these, in turn, will add to other monomer molecules to initiate a chain reaction as in reactions 6 and 7. Termination can occur via several different mechanisms, but radical recombination (reaction 8) is an ever-present possibility. Chain transfer, which can lead to branching, may occur by hydrogen radical abstraction from a nearby polymer molecule (reaction 9).
Emulsion polymerizations are free-radical reactions that take place in an emulsion of water and monomer, or water and an immiscible organic solvent. The initiator (typically a metal ion redox system) is soluble in the aqueous component. The monomer in the organic phase is initiated at the organic/water interface. Emulsion-polymerized polymers often consist of spherical particles that grow within the aqueous medium.
Free-radical polymerizations have certain characteristics: (1) they are generally accelerated by increases in temperature; (2) unless special initiators are used, they give very broad molecular weight distributions, because not all the initiator molecules decompose to free radicals at the same time, so some chains are started sooner than others; and (3) free radicals are so reactive that they undergo side reactions such as abstracting hydrogen radicals from monomer, polymer, or solvent molecules. This will terminate a growing chain and generally start a new one. This same process leads to chain branching and sometimes to crosslinking. Hence, most free-radical processes do not give clean products but generate a broad mixture of linear and branched species. Nevertheless, this is a process widely used in industry to produce polymers such as polyethylene, polystyrene, poly(methyl methacrylate) (Plexiglas®), poly(vinyl chloride) (PVC), and many others. A more recently developed method to overcome the problems described above uses initiators that induce “atom transfer radical” processes. This process can be traced through references given at the end of this chapter.
b. Anionic Initiation.
Compounds such as n-butyllithium or sodium naphthalenide also initiate addition chain reactions, but via a different mechanism. The process is shown in reactions 10 and 11.
The organometallic reagent adds across the double bond of a vinyl compound to generate an anion that attacks another monomer molecule, and then another, and so on. Anionic polymerizations, particularly when carried out in solution at temperatures below 25°C, are much cleaner than free-radical reactions. It is essential that the solvent, glassware, and the atmosphere above the reaction mixture be free from impurities such as water or carbon dioxide, which would react with the active site at the growing chain end.
These reactions are described as “living” because, in the absence of an added terminator, they proceed without side reactions to give linear polymer chains that are still active even when all the monomer has been consumed. The consequences of this are quite profound:
1. The initiation process is very rapid, and all the chains begin to grow at the same time. Thus, by the time the monomer has been consumed, all the chains have approximately the same length. In other words, the molecular weight distribution, given by Mw/Mn, is close to 1. Imagine this being like a footrace where all the runners start simultaneously when the gun is fired, run at exactly the same speed along a straight track, and all burst through the finish-line tape at exactly the same instant.
2. Because each initiator molecule starts only one chain, it is possible to control the chain length of the polymer with some precision. Thus, the length of each polymer chain is given by the number of monomer molecules in the reaction vessel divided by the number of initiator molecules. The fewer initiator molecules present, the longer will be the chains.
3. Because the chains are still active after the monomer has been consumed, it is possible to add more of the same monomer to continue the process and grow longer chains. Alternatively, a different monomer may be added to generate a diblock copolymer (reaction 12).
4. A living chain end can be deliberately terminated by the addition of a reagent that puts a functional site at the chain terminus. For example, treatment with carbon dioxide places a carboxylate group at the chain terminus. This may then be employed to couple that chain to another polymer molecule by, for example, a condensation reaction.
A variant of the classical anionic polymerization method is provided by the use of sodium naphthalenide as an initiator. This initiator is a radical anion (reactions 13 and 14).
In the presence of an unsaturated monomer, the initiator transfers an electron to the monomer to convert it to a radical anion. The radical end of the initiated monomer then combines with its counterpart on another initiated species to form a dimer, both ends of which bear an anion. Monomer molecules are then polymerized from both ends of the initiated species, and all of the characteristics described above for anionic polymerizations are retained. The only structural difference is that there is a discontinuity (a “tail to tail” structure) in the middle of the final chain. The existence of two active chain ends on the final polymer molecule means that the addition of a different monomer then leads to the formation of a triblock copolymer.
Many different monomers can be polymerized by anionic initiation, but the technique works best for unsaturated organic compounds that have electron-withdrawing side groups such as phenyl, cyano, or ester units. Thus, narrow-distribution polystyrene, polyacrylonitrile, and poly(methyl methacrylate) are synthesized by anionic initiation. The monomer should not have a side group such as chlorine, bromine, iodine, hydroxyl, or amino that reacts with organolithium compounds.
c. Coordination Initiation.
Other organometallic-type initiators also play a major role in the synthesis of addition polymers. Two of the best known are Ziegler–Natta and metallocene initiators. Ziegler–Natta initiators are prepared by the reaction of a metal halide such as titanium or vanadium chloride with an aluminum alkyl such as triethylaluminum (structure 6.1 in Figure 6.1). The structure of these catalysts and their reaction mechanisms are a subject of ongoing debate. One proposed mechanism is shown in Figure 6.1 in which an olefin coordinates to a vacant site on the transition metal and then inserts itself into the adjacent metal-carbon bond (structures 6.2 and 6.3 in Figure 6.1). Some Ziegler-type catalysts are soluble in organic solvents, but others are microparticulate materials that function as heterogeneous initiators. For these last species, the surface structure of the particles is crucial to their function. Ziegler–Natta initiators have one marked advantage over classical anionic initiators, namely, that they generate stereospecific polymers. For example, in a Ziegler–Natta reaction, propylene can enter a growing polymer chain with the pendent methyl group on only one side of the polymer skeleton (isotactic). The importance of this is that, whereas the analogous polymer formed by free-radical methods, with a random disposition of side-group configurations (atactic), is a gum, the isotactic form of polypropylene is the tough solid material that is widely used in technology. Different initiators and different monomers may generate polymers in which a side group alternates regularly from one side to the other along each chain. This is called a syndiotactic configuration. The importance of these ste-reoregular polymer structures is that they allow the chains to become oriented and crystallize. A disadvantage of Ziegler–Natta initiators compared to the classical anionic reactions is that the polymer molecular weights are usually not as high, and the molecular weight distributions may be broad. High-density (unbranched) polyethylene is produced by the Ziegler–Natta technique. Acetylene is also polymerized by this technique to give the metal-like polyacetylene. This polymer is discussed in Chapter 10.
Metallocene initiators are related to Ziegler–Natta catalysts, but they contain metals such as zirconium, titanium, or hafnium sandwiched between two 5-membered aromatic rings. Example catalysts are shown as 6.4–6.6. Cocatalysts such as organoaluminum compounds are also employed. The use of metallocene catalysts has had a major impact on the production of polyethylene and polypropylene. The advantage of metallocene catalysts over Ziegler–Natta initiators is their ability to give pure isotactic or syndiotactic polypropylene and to allow better control over the chain length and molecular weight distribution.


d. Cationic Initiation.
Unsaturated organic compounds with electron-supplying side groups close to the double bond, such as 1-butene, isobutylene, isoprene, 1,3-butadiene, vinyl ethers, α-methylstyrene, or aldehydes undergo addition polymerization when treated with Lewis acid or protonic acid initiators. Some examples are shown in Table 6.1. The active species at the chain ends are carbonium ions. The overall reaction sequence is shown in reactions 15 and 16.
Examples of such initiators include BF3OH−H+, H2SO4, HCl, AlCl3, or SnCl4.The characteristics of many classical cationic polymerizations are as follows: (1) exposure of the monomer and solvent to water must be controlled carefully because minute traces of water serve as cocatalysts and change both the rate of polymerization and the average molecular weights; (2) temperatures below 25°C are preferred for these reactions to minimize chain transfer and premature termination of active chains and also, paradoxically, to speed up the rate of polymerization; (3) although the copolymerization of two or more different monomers is possible, the monomers must be of similar reactivity; (4) although “living” cationic polymerizations are possible, they are not as common as in anionic polymerizations; and (5) cationic polymerization is used on a large scale to produce a variety of synthetic rubber materials.
3. Condensation Polymerization
a. General Features.
Close similarities exist between organic polymer synthesis by condensation reactions and the synthesis of oxide ceramics. Condensation reactions take place when difunctional monomers react and split out a side product, which is usually water. Organic monomers such as diols, diamines, dicarboxylic acids, amino alcohols, and amino acids undergo these reactions. Several diverse examples are shown in Table 6.1. The earliest synthetic polymers such as Nylon 66 and poly(ethylene terephthalate) (Dacron® or Mylar®) were made by condensation reactions, and many of the most advanced modern polymers such as Kevlar®, Nomex®, and polyimides, are also produced by this technique. Condensation reactions involve initiation, propagation, chain transfer, and termination steps, but are also capable of undergoing the reverse process—hydrolytic depolymerization. Removal of the water formed by the condensation minimizes this reverse process. Catalysts such as acids or bases are often used to accelerate the reactions. The overall steps are shown in reactions 17–19.
To summarize, the key characteristics of condensation reactions are as follows:
1. The driving force for condensation is the removal of water (or another small molecule such as hydrogen chloride or a salt) from the polymerization reaction mixture. Unless this is accomplished, an equilibrium system will be established between condensation and chain cleavage (depolymerization), severely limiting the chain lengths that can be achieved.
2. The molecular weight distributions are generally broad because of the multiplicity of reactions that can take place. For example, not only do the end units of monomers react with other monomers; monomers also react with polymers, polymers react with other polymers, rings react with monomers and polymers, and so on.
3. The maximum molecular weights attainable are usually well below those obtained in addition or ring-opening polymerizations. Moreover, deliberate limitation of the chain lengths is possible by the addition of monofunctional reagents, such as alcohols or amines that cap the chain ends.
4. The highest molecular weights can be achieved only by ensuring an exact 1:1 ratio of the functional groups (i.e., equimolar amounts of diacid and diamine or diacid and diol), or by fixing this ratio within the monomer as in the case of an amino acid or a hydroxy acid. If one functional group predominates in the reaction mixture, the growing chains will be terminated at an early stage in the reaction.
5. Crystalline polymers are accessible, especially when the polymers contain aryl groups in the backbone.
6. Chain branching and crosslinking are accomplished by the presence of trifunctional reagents such as triols or triamines.
Condensation polymers are synthesized via the reactions of a wide variety of monomers (Table 6.1). Examples include the reactions of dicarboxylic acids with diamines (polyamides), dicarboxylic acids with diols (polyesters), elimination of hydrogen chloride from diols and phosgene (polycarbonates), elimination of sodium chloride from aromatic dichloro compounds and sodium salts of diols (polysulfones), self-condensation of amino acids (polyamides), self-condensation of silane-diols (silicones), or elimination of trimethylchlorosilane from phosphoranimines (polyphosphazenes). Examples of specific condensation polymers are given later in this chapter.
4. Ring-Opening Polymerization
The third general polymerization technique involves the opening of organic, organo-metallic, or inorganic rings under conditions that lead to polymerization. Examples are given in Table 6.1. In many cases, ring-opening polymerizations of cyclic esters, ethers, or amides give polymers that might otherwise be produced by condensation reactions. The advantages and disadvantages of ring-opening polymerizations are as follows:
1. Unlike condensation polymerizations, this process involves no loss of a side product as the reaction proceeds. Thus, the need to remove water or another side products throughout the polymerization to drive the reaction to completion does not apply. This is a significant advantage.
2. Especially when catalysts or initiators are present, the polymer molecular weights can be significantly higher than from condensation reactions.
3. It is a characteristic of many ring-opening polymerizations that polymerization and depolymerization occur at the same time. This means that if the reaction is allowed to proceed long enough to allow an equilibrium to be established, the molecular weight distribution may be very broad. This problem arises because, unless there is appreciable ring strain in the cyclic monomer, no strong driving force exists that favors polymer chains over small rings, and so the forward and back reactions may be almost equally preferred. However, the initial kinetics of the process frequently favor polymerization, so that in the early stages of the reaction the product mixture contains mainly unreacted cyclic monomer and a high polymer. Only during the later stages, when thermodynamic equilibration takes over, does the depolymerization process become significant. Thus, a knowledge of when to terminate the polymerization is the key to generating the highest molecular weights.
A wide variety of polymers are produced by ring-opening reactions, including poly(ε-caprolactam) (Nylon 6), poly(ethylene oxide) (PEO), polyesters from lactones, polynorbornenes, poly(organosiloxanes) (silicones), polysilanes, polyphosp-hazenes, and poly(ferrocenophanes) (Table 6.1). Examples of polymers produced by ring-opening polymerization are given later in this chapter.
An increasingly important form of ring-opening polymerization is ring-opening metathesis polymerization (ROMP) shown in reaction 20. This is a process in which an unsaturated organic cyclic compound such as norbornene is treated with an organometallic catalyst such as those shown in structures 6.7–6.9 to give a polymer that retains unsaturation in the skeleton.

5. Electrochemical Polymerization
Yet another method for the synthesis of polymers involves electrochemical oxidation or reduction. Electronically conductive polymers such as polythiophene, polypyrrole, and polyaniline are produced by this technique. Typically this is a method for the linkage of organic rings to give linear, cyclolinear or cyclomatrix polymers. As an example, the formation of polypyrrole is described in Chapter 10.
6. Secondary Reactions
a. Modification of Polymer Structure.
In addition to the direct methods of polymer synthesis just described, the possibility also exists that preformed polymers can be altered by chemical reactions carried out on their side groups (reactions 21–25). This process at is not widely applicable to most organic polymers because of the unreactivity of their side units. However, polystyrene can be nitrated or sulfonated, poly(vinyl acetate) can be hydrolyzed to poly(vinyl alcohol), and cellulose may be acetylated or nitrated. Reactions carried out on the surfaces of solid organic polymers are more common. However, in one polymer system, the polyphosphazenes, macromolecular substitution constitutes the main method by which a wide variety of different polymers are produced (see discussion later).
b. Crosslinking.
The utilization of polymers as useful materials frequently requires that the macromolecules be crosslinked to reduce their solubility, improve their strength, or enhance their thermal stability. This is usually accomplished by secondary reactions (reaction 22). For example, polymers that bear unsaturated aliphatic side groups, such as vinyl or allyl units, become crosslinked when exposed to free radicals. Similarly, polymers with saturated aliphatic side groups undergo hydrogen radical abstraction in the presence of decomposing peroxides or azo compounds, and the resultant radical-bearing side groups react with their counterparts on other chains to form covalent crosslinks. Exposure of polymers to ultraviolet, X-ray, or gamma radiation has the same effect.
Alternatively, a polymer may be synthesized with a side group that reacts with water to form crosslinks (reaction 23). Poly(dimethylsiloxanes) with acetyl side units hydrolyze in the atmosphere to give acetic acid and a polymer with a few hydroxyl side groups. These cross-condense with similar units on other chains to form cross-links. Polymers with side groups that bear the sodium salts of acidic side groups (SO3Na, COONa, etc.) become crosslinked when exposed to di-or trivalent cations such as Ca2+ or Al3+ (reaction 24).
c. Surface Reactions.
The surface character of a solid polymer has a profound influence on its uses. For example, the biomedical compatibility of an implantable material frequently depends on whether the surface is hydrophobic or hydrophilic. Adhesion is highly dependent on surface character. So, too, are abrasion resistance, frictional properties, membrane behavior, and the compatibility of one polymer with another in polymer laminates. It often happens that a specific application requires one set of properties for the bulk material and another set for the surface. This can be accomplished by selection of a polymer for its bulk properties and then modifying the surface by chemical reactions—usually reactions on the polymer side groups (reaction 25). As an example, fluorination of polymer surfaces is an important process for converting hydrocarbon-swellable polymers such as polyethylene to materials that are unchanged in the presence of gasoline or oil. However, such modification reactions should not penetrate deep into the material in order to preserve the bulk properties.
C. STRUCTURE–PROPERTY RELATIONSHIPS AND POLYMER DESIGN
1. Influence of Molecular Architecture
The properties of a polymer depend not only on the skeleton and side groups but also on the architecture of the polymer chains (Figures 6.2 and 6.3).
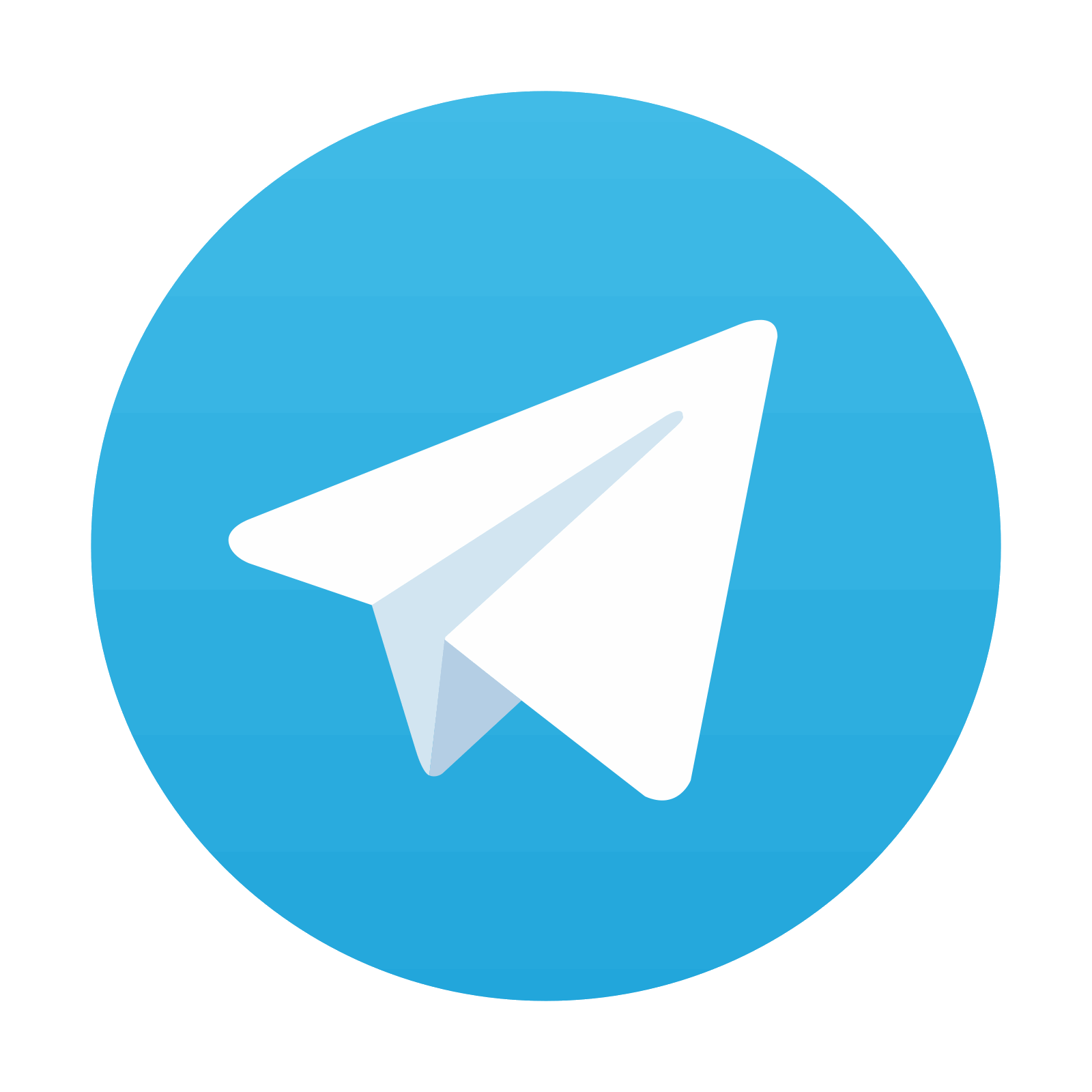
Stay updated, free articles. Join our Telegram channel
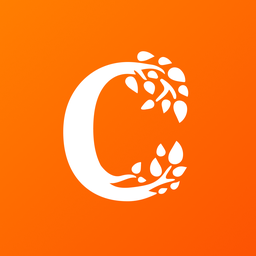
Full access? Get Clinical Tree
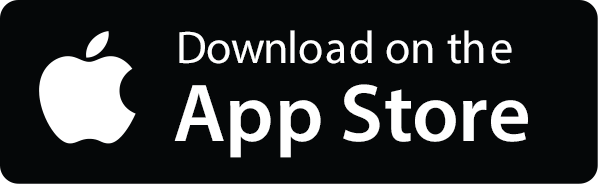
