A. OVERVIEW
1. Passive versus Responsive Optical Materials
The optical properties of materials have been important almost from the beginnings of civilization. Windows, decorative glass, and jewelry are well-known examples. However, optical materials became the subject of intense interest when telescopes, binoculars, and eyeglasses came into general use, and they moved into mainstream technology with the burgeoning manufacture of camera lenses and prisms. Optical materials have also played a dominant role in the more recent changeover from electronic communications based on copper wiring to optical communications through optical fibers and photonic switches. Thus, materials with useful optical properties have now become a major area of research and technology based firmly in materials science in ways that are summarized in this chapter.
It is convenient to consider optical materials in two categories, which we will call “passive” and “responsive.” The category of passive optical materials includes substances whose optical properties change relatively little when an electric field is applied or when the light intensity changes. However, the optical behavior of passive materials, like that of all substances, does vary with temperature and with the wavelength of light being transmitted. Responsive optical materials undergo a significant change in color, transparency, or refractive index under the influence of an electric field or a change in light intensity. This is superimposed on the changes due to variations in temperature or the wavelength of light.
Nearly all common optically useful materials are transparent—that is, they must transmit light rather than block or scatter it. Scattering results from a heterogeneous composition—for example, crystallites dispersed throughout an amorphous material or a mixture of any two or more materials that have different refractive indices. Materials that are transparent include single crystals (assuming the absence of imperfections), amorphous inorganic and polymeric glasses, and heterogeneous substances in which the domain size is smaller than the wavelength of light.
2. Importance of Refractive Index
The refractive index (RI) of a material (n) is defined by the speed of light in a vacuum divided by the speed through the transparent solid. It is also defined by the square root of the dielectric constant. Because the transmission of light in a vacuum is always faster than in a solid, the refractive index is a number larger than 1. However, refractive index values of zero or even negative values are becoming possible. The refractive indices of some typical optical materials and liquids are given in the Table 14.1.
In general, the refractive index depends on the density of electrons in the material. Solids that contain heavier elements have higher refractive indices than do those consisting of lighter elements. Thus, inorganic glasses that contain lead or other heavy elements, or polymeric glasses that contain chlorine, bromine, or iodine, have high n values. So too do organic materials with double or triple bonds.
TABLE 14.1. Refractive Indices
Compound | RI at ~600 nm and 20–25°C |
Liquids | |
Water | 1.33 |
Methanol | 1.33 |
Octane | 1.40 |
p-Dioxane | 1.42 |
Ethylene glycol | 1.43 |
Benzene | 1.50 |
Toluene | 1.50 |
Nitrobenzene | 1.55 |
Aniline | 1.59 |
Carbon disulfide | 1.63 |
Inorganic Glasses | |
Fluorite (CaF2) | 1.43 |
Crown glass (soda–lime glass) | 1.52 |
Quartz | 1.54 |
Flint glass (lead glass) | 1.67 |
Polymeric Glasses | |
Poly(methyl methacrylate) | 1.49 |
Poly(ethylene terephthalate) | 1.58 |
Polystyrene | 1.59 |
Polycarbonate | 1.59 |
Poly(o-chlorostyrene) | 1.61 |
Various polyphosphazenes (depending on side groups and architecture) | 1.38–1.76 |
Two important consequences of the refractive index are the phenomena of refraction and total internal reflection. These can be understood in terms of Snell’s law, n1sinθi = n2sinθrefr, and Figure 14.1. When a beam of light passes from a low RI medium into a high-RI solid two processes occur—reflection and refraction. Reflection may be minimized by the presence of an anti-refraction coating with a thickness similar to the wavelength of light (see discussion later). The refracted ray passes through the solid and emerges from the material such that the angle of incidence θi equals the final angle of refraction. If the two interfacial surfaces are not parallel (as in a prism or a lens), the direction of the emergent beam will differ from that of the entering beam, but θi will be the same (Figure 14.2).
High-RI glasses are of special importance in lens manufacture because the focal length of the lens can be shortened without the need to use surfaces with a high degree of curvature. Moreover, the correction of color dispersion becomes easier. However, the higher the curvature, the more acute are the manufacturing challenges.
Figure 14.1. The path of a light beam through a slab of transparent material depends on the refractive index of the surrounding (lower refractive index) medium ( n1) and that of the slab ( n2), where the angle of incidence (θi), the identical angle of reflection (θrefl), and the angle of refraction (θrefr) are related by Snell’s law, n1sinθi = n2sinθrefr.
Figure 14.2. Curved surfaces, as in a lens, follow the same refraction rules as flat slabs, but bring about focusing of an inverted image of an object.

Total internal reflection is a phenomenon that occurs when a beam of light traveling in a high-RI material impinges at a grazing angle on an interface with a lower-RI material, for example the interface between glass and air. This behavior is the basis for retention of a light beam within an optical fiber, as is discussed later in this chapter.
3. Optical Dispersion
Because the refractive index of a substance varies for the different wavelengths that constitute white light, the passage of a white light beam through a solid with non-parallel faces results in the separation of the beam into the different colors of the spectrum (Figure 14.3). Blue-violet light is refracted most, and red light, the least. For a single lens this means that there is no common point of focus for the different colors. Hence, an image focused by a single lens suffers from color fringing, which degrades the image. This is a major reason for the use of multilens assembles in camera and telescope systems.
Chromatic dispersion is defined in terms of the Abbe number νd, as given by the equation
where nD, nF, and nC are the refractive indices of the material for light at three wavelengths that are usually chosen from the D, F, and C Fraunhofer (Far-Field) emissions at 589.2, 486.1, and 656.3 nm, respectively. The D line corresponds to the main yellow emission from sodium. The F and C lines are the blue and red emissions that are part of the hydrogen emission spectrum. Thus, the Abbe number is a measure of the degree to which the different wavelengths of light are spread out as polychromatic light passes through a material. A higher Abbe number indicates a lower chromatic dispersion. Glasses with an Abbe number above 80 are considered to be low-dispersion materials.
Figure 14.3. The focus point of a lens (a) differs for the different wavelengths that make up white light due to the variation of refractive index with wavelength. This leads to color fringing of an image, which degrades overall sharpness. For a prism (b), the splitting of white light into the colors of the rainbow is a well-known phenomenon. (see color insert).

For some optical applications, such as high-quality camera, binocular, or telescope lenses, it would be advantageous to have a high-RI lens that has a low chromatic dispersion. As shown in Figure 14.4, inorganic glasses are more likely to provide this combination of properties than are organic polymeric materials. Polymer glasses have refractive indices that typically range from 1.33 to 1.73, although specialized polymers, such as polyphosphazenes, sometimes exceed these values, but with high dispersions. Fluorinated polymers have low refractive indexes and low dispersions.
Low-dispersion inorganic glasses may be based on fluorite (CaF2), which is both mechanically fragile and soluble in water, or on silicate glasses that contain barium or lanthanide cations. The addition of thorium to a silicate glass gives a high-RI material with low dispersion, but the radioactivity of thorium has limited the use of this material in more recent years. It is said that 99% of the approximately 2000 different optical glasses available for lens manufacture are used to correct for chromatic dispersion.
Figure 14.4. Schematic plot of refractive index versus chromatic dispersion for a wide range of glasses. Note that for most glasses, chromatic dispersion rises with increasing refractive index. Inorganic glasses cover a wider span of optical properties than do polymer glasses. Fluorinated polymers tend to have low refractive indices and low chromatic dispersions.

4. Optical Birefringence
A birefringent material is a transparent substance that has different refractive indices associated with the passage of light through different directions within the solid. When this situation exists, a beam of light entering the solid is split into two polarized beams—the “ordinary” (faster) beam no, and the extraordinary (slower) beam ne. A well-known consequence is the formation of a double image when an object is viewed through a crystal of calcite (CaCO3), quartz (SiO2), sapphire (TiO2), sodium nitrate (NaNO3), or even ice. This is called “double refraction.”
The phenomenon arises when the distribution of atoms and bonds, and hence the electron density, differs along different axes of the crystal. Because different axes have different refractive indices, one fraction of the light will proceed directly through the low-RI path through the crystal (no), while a second fraction will take a longer (slower) higher refractive index path before emerging (Figure 14.5).
The two beams will be polarized at right angles to each other (see later section in this chapter). The polarization effect can be seen easily if a film of Polaroid material is rotated between the eye and the crystal. First one component of the doubled image and then the other will be extinguished. Moreover, because of the different refractive indices and different path lengths, if the two emergent beams are combined, they will be subjected to constructive or destructive interference, depending on the thickness of the sample and the difference between the two refractive indices. Hence, for certain applications, like “quarter-wave plates” (discussed later), the precise thickness of the material becomes crucial for its utilization in optics. Thin plates of birefringent material can convert linear to circularized polarized light, or vice versa, as described in a later section.
Figure 14.5. Optical birefringence occurs when the electron density in a solid differs for different spatial axes. This situation occurs most frequently for crystalline materials, but it may also occur with oriented liquid crystalline compounds or oriented noncrystalline polymers. A single beam entering the solid is split into two beams, one of which takes the most direct pathway (the “ordinary” faster, low-refractive-index path), and the other follows the slower, “extraordinary” high-refractive-index route (a). The result is a doubling of the image (b).

Crystals are not the only materials that exhibit birefringence. Many polymers behave similarly, especially if they have been oriented by stretching. Regenerated cellulose films (cellophane), rigid-rod polymers, and liquid crystalline polymeric materials are examples. Small-molecule liquid crystalline phases often show the same behavior, again due to the different electron densities along different directional axes.
Birefringence also explains the brilliant colors that arise when crystals, many polymers, and liquid crystalline substances are rotated between crossed polarizers on a microscope stage. The different colors are a consequence of the constructive or destructive inteference effects for different wavelengths of light after passage through a birefringent material. On the other hand, totally amorphous glasses or elastomers give only a dark-field image when rotated between crossed polarizers.
1. Materials and Devices for Passive Optical Applications
These represent by far the majority of optical materials used in technology. As discussed above, they range from transparent single crystals like quartz or mica to inorganic and organic amorphous polymeric glasses. The choice of a specific material depends, of course, on the demands of the application. However, in general, single crystals are employed where small size and limited fabrication options are acceptable. Inorganic glasses are best when thermal and radiation stability are primary requirements. Polymers are preferred for applications where ease of fabrication into unusual shapes, low cost, or lightness of weight are primary considerations. The disadvantages of single crystals revolve around size, shape, and fabrication problems. Inorganic glasses must be fabricated at elevated temperatures and can be engineered to precise shapes only by meticulous grinding and polishing. Problems often encountered with polymeric glasses are their relatively low Tg values and the consequent possibility of shape changes at elevated temperatures, and their tendency to generate colored decomposition products under intense ultraviolet irradiation. This last problem is especially acute for the adhesives used to cement lens or prism components together. The naturally occurring polymeric adhesives used in older lenses or laminates have also proved susceptible to microbial colonization and clouding.
2. General-Purpose Optical Materials
Windows in houses, automobiles, and aircraft represent one of the largest-volume uses for transparent materials. Silicate soda–lime glass (Chapter 7) is by far the most widely used window material for buildings and automobiles. It is produced in “annealed” and “tempered” modifications. The annealed material (cooled slowly) fragments into shards on impact and is thus dangerous for use in automobile or laboratory fume hood windows. Automobile windshields use laminated glass, with two glass layers cemented together with a thin film of poly(vinylbutyrate) adhesive, which limits the dispersion of glass fragments in an accident. Automobile side windows are tempered to place the two surfaces in tension (see Chapter 7), which causes the glass to crumble into polygonal fragments on impact, with less potential for passenger injury. Polymer glasses are used in aircraft windows because of their impact resistance and lightweight characteristics. “Bulletproof” glass is made from a thick polymer such as polycarbonate, often laminated. Modern laboratory glassware is produced from borosilicate glass (Chapter 7) because of its superior thermal shock and chemical resistance.
3. Lenses and Prisms
Lens design, hitherto an art, is now a computerized science. As described above, single lenses are unsuitable for precision applications because of chromatic dispersion and the resultant color fringing of the image. It is also difficult to design and shape a single lens to eliminate optical aberrations, which are focus problems that are caused by the spherical profile of most normal lenses. For these reasons, good quality lenses for cameras, microscopes, binoculars, and telescopes are “compound” systems with several lenses clustered in the optical path or cemented together.
Chromatic abberation can be controlled by the use of two or three lenses in series. A doublet system consists of a convex lens with high refractive index (and thus a high chromatic dispersion) followed by a concave lens with a lower refractive index, as illustrated in Figure 14.6a. So-called apochromatic triplet lens systems provide an even better correction for all colors of the visible spectrum. Extra-low-dispersion glasses are used increasingly in high-performance lens systems.
Optical aberrations can be corrected in one of two ways: (1) by the use of complex, multilens assembles of the types shown in Figure 14.6b; or (2) by the incorporation of aspheric lenses. An aspheric lens has a surface that deviates from normal spherical geometry. By using aspheric elements, such as the one shown in Figure 14.6c, it is possible to bring about a high degree of optical correction with fewer lens elements than would normally be required. This reduces the weight of the overall lens assembly. A reason why this technique has only relatively recently become common is the difficulty of grinding inorganic glasses to aspherical profiles in a high-volume manufacturing environment, although complex profiles can be produced by diamond turning on a computer-controlled lathe. However, polymer glasses can be molded into aspherical lenses using a mold with the correct profile that has been produced by meticulous shaping. Thus, polymeric aspherical elements are now becoming increasingly common in high-performance lens systems.
An additional aspect of lens manufacture is the application of thin coatings of materials such as magnesium fluoride or zirconium oxide to the surfaces to minimize reflections and thereby increase light transmission to as much as 99.9%. Such coatings are applied by vapor deposition techniques to thicknesses that are close to the wavelengths of light.
Lenses in eyeglasses are now almost exclusively produced from polymers such as poly(methyl methacrylate) or polycarbonate because of their lightness of weight and safety considerations. Photochromic lenses, which change opacity with different light levels, are discussed in a later section of this chapter.
Many of the challenges in lens design also apply, to a lesser extent, to prism manufacture. Prisms are used in nearly all laboratory optical equipment. They are found in binoculars, telescopes, and single-lens-reflex cameras. For laboratory equipment, stability to intense visible and ultraviolet radiation usually mandates the use of inorganic glasses rather than polymers. The optical transmission window is often a critical factor in materials choice. For example, fused-silica prisms are required for the transmission of ultraviolet light. Both inorganic and polymeric glasses are used in binoculars and cameras, with the choice often depending on quality, cost, and the need to minimize weight.
Figure 14.6. (a) Correction of chromatic dispersion can be accomplished by a combination of a high-refractive-index, high-dispersion convex lens coupled with a low-refractive-index concave lens. (b) Complex lens assemblies used to correct both chromatic and optical aberations such as coma. (c) Aspheric lenses, often made from polymers, are employed increasingly to avoid the distortion problems associated with the use of spherical profile lenses, especially in wide-angle and zoom lenses used in photography. The aspherical profile allows correction for crucial “edge effects” in which those rays passing through the outer regions of a spherical profile lens are difficult to focus when wide apertures are employed. (see color insert).

4. Optical Waveguides
The subject of optical waveguides was introduced briefly in Chapter 7. Here, we emphasize that the prime requirements for long-distance optical signal transmission are freedom from color or microcrystallinity that would limit transparency in the near-infrared region, optical and chemical stability over periods of many years, and ease of fabrication into extremely long, thin, fibers. Fused silica is the material used almost exclusively, and is obtained synthetically rather than directly from sand.
The synthesis process is as follows. Silica sand is first converted to SiCl4 by reaction with chlorine, and the SiCl4 is purified by fractional distillation, before conversion back to SiO2 by reaction with oxygen at high temperatures. The overall chemical sequence is shown in reaction 1.
The fiber fabrication process begins with the extrusion of the ultrapure silica into a tube (a preform). Then, pure silica, doped with GeO2, is vapor deposited on the inside of the fused-silica tube. This “preform” is then passed through a furnace, and the softened material is drawn out into thin fibers. The SiO2 doped with GeO2 collapses to a monolith during the hot drawing process to give a solid central core of germanium oxide–doped silica surrounded by the pure silica “cladding.” After being drawn, each fiber has a core diameter of approximately 10μm (Figure 14.7).
Because of the presence of the germanium, the central core has a higher refractive index than does the cladding (germanium contains more electrons than silicon does). Hence, total internal reflection of a light beam at the interface between the core and the cladding keeps the optical signal inside the core. The use of “synthesized” ultrapure germania–silica in this way allows the core to transmit more than 95% of the light over a distance of one kilometer, thus reducing the need for closely spaced amplifier devices for long-distance communication. Undersea cables, in particular, are critically dependent on simple, trouble-free amplifiers to help transmit signals over thousands of miles. The internal “amplifiers” consist of short regions of the fiber doped with erbium or yttrium. A light source outside the fiber causes a laser-like amplification process, which effectively amplifies the signals passing through. An advantage of this system is that, when different wavelengths are being transmitted down the same fiber, all are amplified simultaneously by passage through the device.
Figure 14.7. Fabrication of optical waveguides. A tube of pure silica is heated and drawn out into a fiber as a mixture of SiCl4 and GeCl4 together with water vapor or oxygen vapor, depositing a mixture of SiO2 and GeO2 on the inside of the tube. As fiber extension continues, a core of higher-refractive-index glass is formed surrounded by the lower-refractive-index silica.

Polymers have been suggested as replacement materials for optical waveguides, especially where weight is a serious consideration. The lower transparency of most polymers limits their use to short-distance applications, such as in aircraft or automobiles. However, their incorporation into optical switching devices or optical integrated circuits is now well established. For these applications, slab or channel waveguides (Figure 14.8) are preferred configurations, and the ease of fabrication of polymers into thin sheets or as crosslinkable liquid monomers into channels is a significant advantage.
Figure 14.8. (a) Typical fiberoptic waveguide with a core of higher-refractive-index glass. (b) A slab waveguide often fabricated with a polymer slab as the high-refractive-index core. (c) A channel waveguide typically formed by microlithographic etching of a channel in a low-refractive-index material, followed by filling of the channel with the monomer of a high-refractive-index polymer and subsequent polymerization.

5. Waveguide Multiplex/Demultiplex Devices
Broadband digital information transmission over optical waveguides is practical only if more than one “information channel” is transmitted simultaneously over each fiber. This is accomplished by using as many as 50 different wavelengths of infrared light to carry digital signals down each waveguide. A typical situation uses eight or more different frequencies per fiber, with each wavelength separated by 1.6 nm. Each channel then carries 2.5 gigabits (Gb) of digital information per second, for a total of 20 Gb per eight-channel fiber. This is the equivalent to transmitting the words from 5000 average-length novels down each fiber every second.
A multiplexer is a device that combines the different wavelength signals from several sources into one fiber. This is accomplished by feeding 8, 16, 32, or more light beams from incoming fibers into a slab waveguide that has only one output.
Separation of the different carrier wavelengths with their individual signals at the receiving end is accomplished by a passive device known as a wavelength-division demultiplexer. The acronym DWDM denotes dense wavelength-division multiplexing, in which the maximum feasible number of different wavelengths are used. A passive demultiplexer is based on the principle that different optical path lengths within the device are used to separate the different incoming wavelengths and their signals. Figure 14.9 shows the general layout of such a device. A single fiber bearing the incoming signals on, say, eight different wavelengths leads into a slab waveguide. This divides (“lances”) the beam into eight different, curved channels that require the beams to traverse different path lengths. At the output of each channel all the beams spread out to encompass the eight output waveguides, but interference between the beams channels a particular carrier wavelength into a specific output channel. This arrangement separates the wavelengths and directs their signals uniquely into one of the eight receiver circuits.
Figure 14.9. Optical multiplexers are passive devices for channeling several different wavelength signals from a number of optical fibers into one optical fiber. The demultiplexer (shown here) uses eight channel waveguides with different path lengths to separate the incoming signals into the different wavelength signal components.

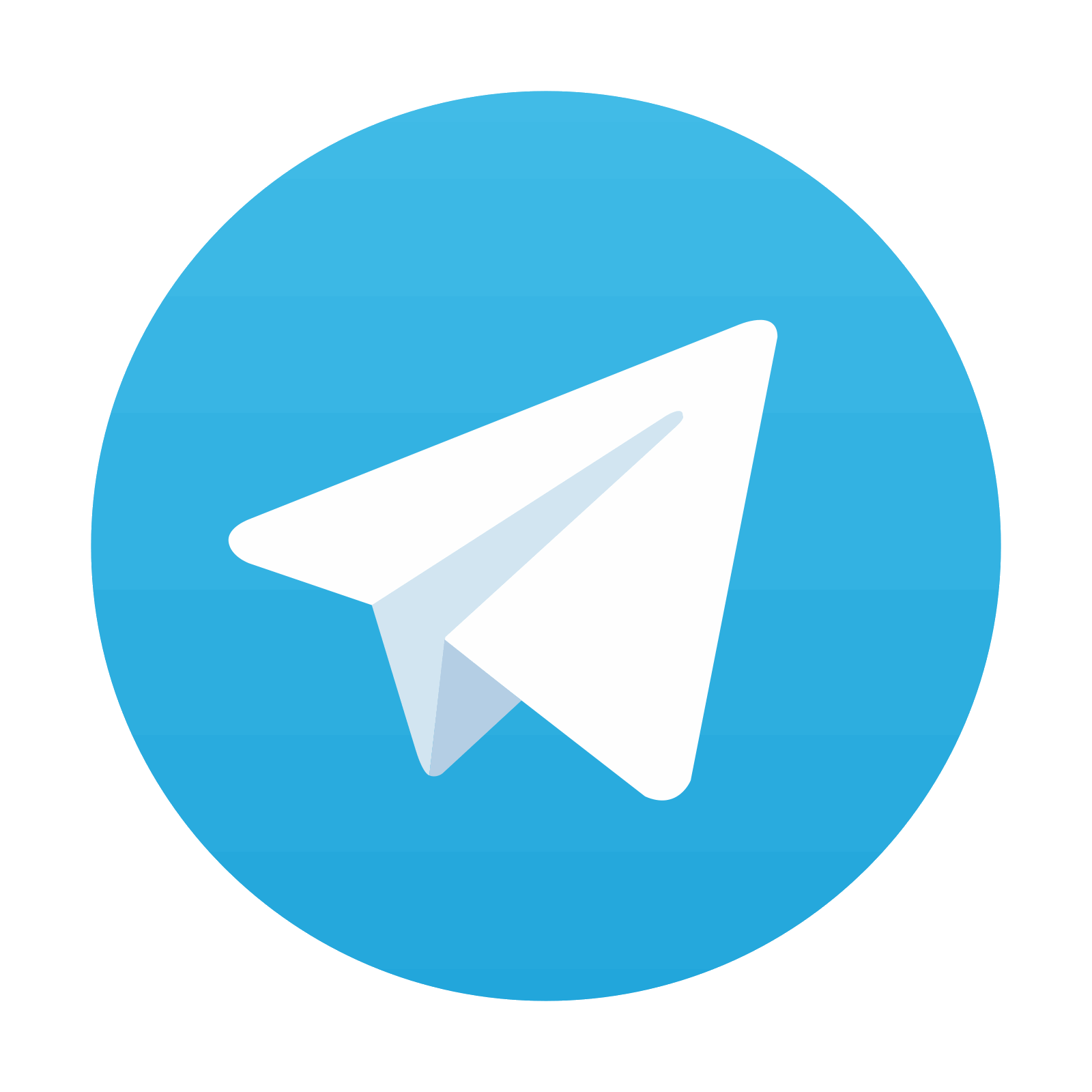
Stay updated, free articles. Join our Telegram channel
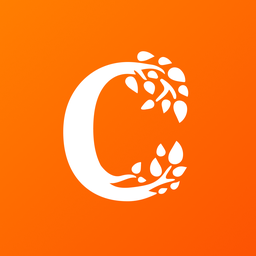
Full access? Get Clinical Tree
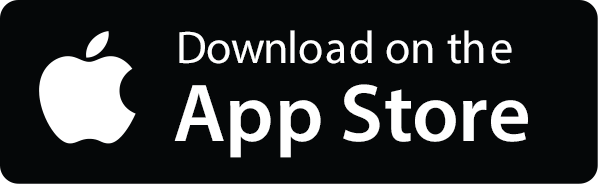
