A. IMPORTANT ASPECTS OF METAL SCIENCE AND TECHNOLOGY
1. Background
Most of the elements in the periodic table are metals, which is one reason why they play such an important role in materials science. Metals have been employed as useful materials since the early history of the human race. Indeed, historical eras are sometimes named in terms of the metals that had a major influence on the development of civilization—the Bronze Age, the Iron Age (Figure 8.1) and so on. What this means is that the discovery of specific metals or of methods that isolate them had a major impact on everyday life (cooking vessels, body decoration, etc.) and on warfare (swords, daggers, body armor, etc.). Our own era could well be described as the “Age of Steel and Aluminum” since these two metals dominate nearly all aspects of modern civilization, from transportation to building construction.
However, many different metals play a major role in modern materials science, including not only steel and aluminum and their alloys but also copper, silver, gold, titanium, zinc, chromium, nickel, magnesium, and tin as the most obvious examples, as well as other metals such as uranium or beryllium, which serve crucial roles in particular applications.
To a large extent, the utility of a metal depends on the availability of its ores, its ease of isolation from them, and hence its cost. Gold would be used more widely as an engineering material if it were available in quantities as large as, for example, iron or aluminum. Titanium would long ago have replaced steel or aluminum in many applications if it could be extracted more easily from its ores. The costs of metals vary from year to year, but the approximate values relative to steel (at 1, as baseline) are aluminum 7, copper 8, silver 600, titanium 1000, gold 90,000, and platinum 173,000. This will give some idea of the constraints that exist to expanding the uses of many metallic materials.
2. Advantages and Disadvantages of Metals as Materials
The widespread use of metals is a result of their obvious attributes such as strength, hardness, and high melting points. Some metals such as copper are flexible, malleable, and ductile. Most are good electrical conductors, and a few are magnetic. Many metals have surfaces that can be polished to give a high reflectivity and, although most metals have a “white” or gray surface color, some such as gold or copper have distinctive yellowish colors. Disadvantages also exist. Most metals are heavier than polymers or ceramics. Moreover, corrosion, surface oxidation, and instability to acids or bases are common defects. Many of the less common metals are expensive. In addition, the extraction of metals from their ores often involves penalties such as the expenditure of large amounts of energy and the production of atmospheric and groundwater pollution.
3. Scope of This Chapter
Although most of the elements in the periodic table are metals, a discussion of all of these is clearly beyond the scope of this book. Instead, the following sections deal with the 10 or so metals that are used most widely in modern technology: iron, nickel, chromium, aluminum, magnesium, titanium. tin, copper, silver, and gold. The following sections deal with the isolation of specific metals, corrosion, and solid-state structure with its relationship to properties, alloys, electrical and thermal conductivity, color, magnetism, and metal fabrication.
B. ISOLATION OF SPECIFIC METALS FROM THEIR ORES
General methods for the extraction of metallic elements are described in Chapter 3. Here we deal in more detail with the isolation of specific metals.
1. Iron and Steel
Iron is the fourth most abundant element in the earth’s crust, and it has played a crucial role in the development of human skills and technology since about 1500 BC. Steel is an alloy of iron with small amounts of carbon. The properties of iron and steel that underlie their widespread use include their toughness and ductility at red heat, and the low cost of production. Until the industrial revolution in the late 1700s charcoal, obtained by the pyrolysis of wood, was employed as the reducing agent to convert iron oxides to the metal (Figure 8.2).
This placed limits on the scale of manufacturing, gave rise to serious air pollution, and caused widespread deforestation. For example, even in the 1800’s, large areas of the Appalachian ridges in Pennsylvania were being clear-cut to provide charcoal for local iron furnaces. However, earlier, starting in about 1770, a new development occurred in England that revolutionized both the manufacturing process and the course of technology. This was the replacement of charcoal as a reducing agent by coke, which was readily available from plentiful supplies of coal. This resulted in a dramatic increase in the scale of production and a fivefold reduction in the price of the metal. It also initiated the industrial revolution, first in Britain and later worldwide.
The main mineralogical sources of iron are Fe2O3 (hematite), FeO2H, Fe2(OH)3, and FeCO3. Geologic hydrothermal reactions probably generated these ores, perhaps from FeS2. Isolation of the impure metal is accomplished by reduction of the ore at high temperature using coke and carbon monoxide, itself formed by partial oxidation of the coke. The reduction process takes place in a vertical, thermally insulated cylinder known as a “blast furnace” (Figure 8.3).
Figure 8.2. Representation of the truncated fieldstone blast furnace at Greenwood Furnace in central Pennsylvania, which operated between 1834 and 1904. Vast tracts of trees were felled in widening circles in the surrounding forest and then slow-burned to produce the charcoal used as a reducing agent. Widespread air pollution and deforestation were typical of this era. (Courtesy of the National Parks Service.)

The iron ore is fed into the top of the furnace together with limestone (calcium carbonate) and coke. Oxygen (air) is forced into the base of the furnace, where it oxidizes carbon to carbon monoxide. As the mineralogical charge moves down the furnace increasing temperatures cause different chemical reactions, as shown in reactions 1–6.
Figure 8.3. Schematic view of a modern blast furnace. The highest temperatures are at the base of the furnace, where hot, compressed air reacts with coke to generate carbon monoxide. The solid charge is fed into the top of the furnace and works it way down, increasing in temperature as various reactions (shown in reactions 1–6 in this chapter) take place. The impure iron and slag melt between 1200°C and 1500°C and collect at the base of the furnace. The slag, which is lighter, is tapped from the top of the molten iron. The molten metal is tapped from a lower point, and is fed into channels where it solidifies.

Finally, at ~2000°C, molten iron is bled from the base of the furnace, followed by the lighter, floating slag. The latter consists mainly of CaSiO3. The molten iron is directed into channels formed in sand, where it solidifies to an impure solid known as “pig iron.” The impurities in this material, which consist of carbon, phosphates, phosphorus, sulfur, silicates, and silicon, cause it to be a brittle material, with few uses.
Refining to reduce the level of impurities, is then carried out by remelting the pig iron and blowing air or (more commonly) oxygen through it to oxidize the impurities to gaseous products or to more slag. Oxidation reduces the amount of carbon to the acceptable levels required in steel (0.5–1.5%). Further decreases in carbon content lead to the softer “wrought iron” used in decorative ironwork and similar applications. The world production of steel exceeds one billion tons per annum.
The properties of iron and steel are modified over a broad range by the addition of other metals to form alloys with Ni, Cr, Mn, or Mo (see Section D.2 later in this chapter). These alloys have improved corrosion resistance, flexibility, toughness, and impact resistance compared to pure iron or mild steel.
2. Nickel
Nickel ores include the metal sulfides and a number of mixed silicates with magnesium or iron. By far the largest known source of nickel is the sulfide deposit at Sudbury in northern Ontario, Canada, which yields more that 25% of all the nickel produced worldwide. Other sources are in Australia and Siberia. Total world production is about 1.2 million tonnes (long tons) per annum.
Nickel is isolated from its sulfide ores by the addition of sand followed by high-temperature oxidation (“roasting”), which converts iron sulfide impurities to SO2 and iron silicates (slag). The nickel sulfide is then converted to nickel oxide, which can be used directly for mixing with iron oxides for conversion to steel alloys. Alternatively, the oxide is reduced to the metal with carbon, followed by electrolysis to give pure nickel. Another process involves reduction of the oxide by a mixture of hydrogen and carbon monoxide (a mixture formed by passing water over hot coke) and conversion of the nickel to the volatile nickel carbonyl [Ni(CO)4]. Decomposition of the carbonyl at 230°C gives 99.95% pure nickel, plus carbon monoxide, which is recycled.
Nickel-containing steel alloys are used in magnets, stainless steels, armor plating, household utensils, and hospital instruments. When alloyed with copper, nickel forms the corrosion-resistant monel metal. Alloys of nickel with chromium and iron are widely used as various stainless steels, for which the coding number (e.g., type x–y) refers to the percentage of chromium (x) and nickel (y). Nickel alloyed with aluminum is used in gas turbine blades because of its ability to withstand high temperatures (~1000°C).
3. Chromium
The main producers of chromium ores are Australia, the countries of the former Soviet Union, and South Africa. The principal ore is chromite (FeCr2O4). This is reduced by coke in an electric furnace to yield the alloy “ferrochrome,” which may be added directly to steel to produce stainless steel. Alernatively, chromium(III) oxide (Cr2O4), formed by alkaline air oxidation of chromite at elevated temperatures, is reduced to chromium by carbon, and is then dissolved in sulfuric acid and electrolytically deposited on steel or nickel-plated steel give corrosion-protected objects.
4. Aluminum
The metals mentioned above are typical “heavy” metals. However, lighter metals such as aluminum, magnesium, and titanium offer many advantages where weight is a crucial factor such as in aircraft, bicycles, automobile engines, electrical transmission lines, construction beams and joists, and ships and boats. Although once considered to be a semiprecious metal, aluminum is now produced in such large quantities and at such a low cost that it has replaced steel in many applications.
The principal ore from which aluminum is extracted is bauxite—a general name for a range of minerals that contain a mixture of iron oxides or hydroxides and aluminum oxide and hydroxides such as Al2O3 or Al(O)OH. The first step in aluminum production is extraction of the aluminum oxide or hydroxide from the ore using aqueous sodium hydroxide, followed by precipitation of Al(OH)3 and dehydration at 1200°C to alumina (Al2O3). The alumina is then dissolved in hot synthetic cryolite (Na2AlF6), itself produced from Al(OH)3, HF, and NaOH. This solution is then electrolyzed at ~950°C to yield pure aluminum.
The isolation of each ton of aluminum requires about 15,000 kilowatt-hours (kWh) of electricity, which explains why the mineral and the alumina are often produced in one location, while the electrolysis is carried out in another. Australia is the biggest supplier of ore (38%), followed by Papua New Guinea (13%) and Jamaica (11%), while regions with plentiful hydroelectricity, such as China, Russia, Canada, and the United States, are the principal producers of the metal. In principle, the largest potential source of aluminum is kaolin and related clays (see Chapter 5). In practice, the cost of extracting the metal from this source is not economically viable.
Aluminum is often alloyed with magnesium, zinc, silicon, manganese, or copper to generate the most favorable combinations of properties for different applications. The pure metal is lightweight, highly reflective, malleable, and flexible in the form of thin foils. However, it has only limited strength. It is one of the best electrical conductors. The metal has good corrosion resistance in spite of its high inherent reactivity, and this is due to the presence of a tough surface coating of the oxide. However, the oxide coating is penetrated by salt water or strong base, and these liquids cause corrosion.
5. Magnesium
Magnesium is another metal that is prized for its lightness of weight (density 1.74g/cm3). It is, in fact, lighter than aluminum. Hence the widespread use of magnesium and its alloys in aircraft, bicycles, rockets, and automobile components. Many mineralogical sources of magnesium exist, including dolomite (calcium magnesium carbonate), magnesite (MgCO3), and brucite [Mg(OH)2], plus a range of water-soluble halides, nitrates, and carbonates found in salt deposits and seawater. Isolation of the metal is either by electrolysis of molten MgCl2 at 750°C or by heating dehydrated (“calcined”) dolomite above 100°C in the presence of ferrosilicon.
6. Titanium
Titanium is often described as a “wonder metal” because it combines many of the most prized attributes of a metallic material. It is tough, has a very high melting point (1660°C), is only half as heavy as steel, and has excellent resistance to corrosion and aggressive chemicals. Unfortunately, it is also one of the more difficult metals to isolate from its ores, which explains its high cost and its relatively low volume of production.
The main mineralogical sources are rutile (TiO2) and ilmenite (TiFeO3) found in Brazil, Switzerland, the United States, Russia, and Africa. Conventional reduction of these by heating with carbon is not feasible because titanium forms a very stable carbide rather than being reduced completely to the metal. Instead, the ore is heated with carbon and chlorine to form either TiCl4 or a mixture of TiCl4 and FeCl3 (from ilmenite). The TiCl3 is then isolated by fractional distillation, and is reduced to the metal by reaction with metallic magnesium or sodium. Finally, extraction of the product with water or hydrochloric acid removes magnesium chloride or unreacted magnesium, and the titanium is recovered as a porous “sponge.” Fabrication of the metal requires the use of challenging conditions such as melting in an unreactive vessel under an atmosphere of argon or under vacuum. Powder fabrication techniques are complicated by the fact that powdered titanium, like powdered magnesium or aluminum, ignites when heated in air, which is an indication of its strong affinity for oxygen. Uses for titanium include golf clubs, armor, aerospace components, camera exteriors, and chemical reactors or autoclaves.
7. Tin
The main source of tin is SnO2 (cassiterite), with Malaysia as the largest supplier of the ore. Metallic tin is obtained from the ore by carbon reduction at 1200–1300°C. Subsequent heating in the presence of oxygen oxidizes iron impurities to oxides, which are then removed. The principal manufacturers of the metal are China, Indonesia, and Peru.
Tin is a low-melting-point metal (mp 232°C) used for making “tin plate” (a steel sheet coated by molten tin). Tin is also a component of solder (a tin–lead alloy). Bronze is a copper-tin alloy, and white pewter is an alloy of tin with small amounts of antimony and copper. A bath of molten tin is used as the casting surface for the fabrication of float glass, as described in Chapter 7.
8. Copper
Copper is found in geological formations in the form of sulfides such as Cu2S or CuFeS2, and as the oxide, Cu2O and the carbonate, Cu2CO3(OH)2. The main sources of the ores are in North and South America, Russia, and Africa. Chile, the United States, and Peru are the largest refiners of the metal. Some very pure metallic copper is found in geologic formations.
The traditional method for extraction of the copper from sulfide ores involved grinding to a powder, froth flotation. Heating in air (“roasting”) to partially convert Cu2S to Cu2O, which then react to form impure copper. The overall process is illustrated by reactions 7 and 8.
During this reaction sequence iron sulfide impurity is also oxidized and is removed as slag. The sulfur dioxide liberated by this process is an environmental problem. Some copper oxide ores can be converted directly to the impure metal by heating with coke. Final purification is accomplished by dissolution in sulfuric acid and electrolysis.
However, a more modern method that now accounts for at least 20% of all copper production employs a solvent extraction process. The crushed ore is leached with dilute sulfuric acid in the presence of ferrous salts. Sulfide ores undergo bacterial oxidation, while the acid dissolves the resultant copper oxide. The acidic solution is then extracted with kerosene that contains a copper “extractant” (presumably a chelating agent). The chelated copper is captured from the chelate using concentrated sulfuric acid, and the resultant solution is electrolyzed to give 99.99% pure copper at the cathode. Only this purest copper is suitable for electrical applications such as household wiring, electric motor and generator windings, or long-distance power lines. However, copper has been largely replaced by aluminum for this last application. Note that large amounts of copper are alloyed with zinc to form brass, and lesser amounts with tin to form bronze.
9. Silver
Copper, silver, and gold are known as the “coinage metals” because of their use in currency. Silver is less expensive than gold, but more valuable than copper. Metallic silver is sometimes found in geologic formations in association with silver sulfide from which it was presumable formed. Deposits of silver chloride are found in Australia and Chile. However, much of the silver in circulation today is recycled metal or material recovered from photographic processing laboratories. Most new silver (10,000 metric tons per annum) is obtained as a byproduct of lead manufacture or from the insoluble material deposited below the anodes in electrolytic copper purification cells. This material (known as “anode slime”). It is dissolved in acid and electrolyzed to give pure silver. The main producers of silver are Peru, Mexico, Australia, and China.
Apart from its use in jewelry and coinage, large amounts of silver are still used in traditional photography after conversion to light-sensitive silver halides. This use is declining rapidly with the growth of digital photography, but will probably remain significant for the foreseeable future. Silver is also used in batteries, mirrors, and electrical devices.
10. Gold
The traditional sources of gold are in regions with histories of volcanic activity—Central America, California, Alaska, and New Zealand—but the major producers today are South Africa, Australia, the United States, China, and Russia. “Placer” gold is the metal in the form of nuggets or grains that, being heavier than the eroding rock, sink to the bottom of streams and are isolated by “panning.” However, most gold is obtained from crushed rock by extraction with aqueous solutions of sodium cyanide coupled with air oxidation (reaction 9).
The addition of zinc dust causes precipitation of the gold, which is then refined electrolytically to give 99.95% pure metal. One of the main advantages of gold as a technological material is its resistance to surface oxidation and corrosion; hence its use in electrical switches, contacts, and other devices. Its inertness is also the main reason for its widespread use in dentistry. Among the few reagents that attack gold are cyanide ion plus a source of oxygen and aqua regia, which is a 3:1 mixture of concentrated hydrochloric and nitric acids. Mercury readily forms an amalgam with gold, which is the reason why gold jewelry must be protected against mercury in the laboratory or in dental work.
One of the main defects of metals as materials is the tendency of many of them to corrode in contact with water, brine, polluted air, or strong chemical reagents. Metals such as gold, chromium, or titanium are much more resistant than iron, magnesium, or lithium. Why are some metals prone to corrosion while a few are apparently immune, and what can be done to protect the most sensitive metals from this problem?
Two major factors determine how a metal behaves in contact with air, water, or other reactive reagents. First, it should be recognized that very few metals actually present a metallic surface to the environment. Common metals such as aluminum, iron, or magnesium undergo almost instant surface oxidation when exposed to air. Lithium, the lightest of all metals, forms a surface coating of lithium nitride in nitrogen or a mixture of oxide, hydroxide, and nitride when exposed to air. A thin layer of surface oxide can either protect against further reaction, as in the case of aluminum, or sensitize the surface to a deeper reaction, as in the case of iron. To a large extent, the outcome depends on the strength of adhesion between the surface oxide later and the metal, and on the resistance of the oxide to dissolution in weak acids, bases, or other chemicals found in the environment. For example, aluminum is quite stable in a neutral, dry atmosphere owing to the protection by the oxide layer, but that layer is removed by aqueous acid or base or by prolonged exposure to seawater.
TABLE 8.1. Galvanic Series of Common Metals
Metal | Approximate Voltage with Seawater as the Electrolyte |
Magnesium | –1.6 |
Zinc | –1.0 |
Aluminum | –0.8 |
Cast iron | –0.66 |
Steel | –0.65 |
Brass | –0.35 |
Copper | –0.32 |
400-series stainless steel | –0.28 |
Silver | –0.12 |
Titanium | 0.00 |
Hastelloy C-276 a | +0.06 |
aAn acid-resistant alloy of Mo, Cr, Fe, W, and Ni.
The second factor comes into play when galvanic cells are formed at the point of contact between two different metals or a metal and a conductive oxide or hydroxide. A trace of an electrolyte at the interface, such as aqueous salts or sulfurous acid from pollution, sets in motion a corrosion reaction. The behavior of a metal in a galvanic cell can be understood in terms of a “galvanic series,” a list of metals listed in an order of the voltage generated by a metal versus a saturated calomel electrode. Some values are listed in Table 8.1. Those metals listed the bottom of the table are the most resistant to galvanic corrosion. For a cell formed between two dissimilar metals, the one that is higher in the series will be the one that is corroded.
A galvanic cell is responsible for the corrosion of iron. Iron reacts with a moist, oxygen-containing atmosphere to form a coating of Fe(OH)3 and/or FeO(OH). In the absence of an electrolyte, the surface reaction is limited, but an electrolyte such as aqueous sodium chloride or sulfurous acid (from SO2 and water) cause ever-deepening corrosion through the series of electrochemical reactions (shown in reactions 10–13 below). In these reactions the metallic iron functions as the anode of the electrochemical cell.
Anode reaction:
Cathode reaction:
Overall reaction:
Corrosion can be inhibited or prevented in four different ways:
1. If a steel sheet is coated with a metal that is higher in the electrochemical series than iron, such as zinc, the zinc will form the anode of a galvanic cell and will corrode in a sacrificial manner in preference to corrosion of the steel. This is the basis for the widespread use of galvanized steel.
2. It is also possible to protect a metal against corrosion by the application of an electric current that counteracts the potential of a galvanic cell. Thus, the corrosion of iron in bridges and underground oil and gas pipelines is inhibited by the application of a negative electrical potential. The electric power for this process is often generated by solar cells (see Chapters 10 and 14).
3. However, corrosion protection is often achieved by the use of special alloys such stainless steels that contain iron, nickel, and chromium or, for example, Hastelloy C276, which is an alloy of iron, molybdenum, chromium, tungsten, and nickel. The high cost of such alloys is a reason why they are not used more widely in automobile bodies or bridges.
4. In the absence of galvanic protection or special alloys, the main defense against corrosion is to plate the sensitive metal with a corrosion-resistant metal such as chromium or to coat it with an impervious polymeric film (paint) to exclude water, often with the use of an undercoat that contains a corrosion inhibitor such as chromate. Clearly, this last option is the least expensive solution and the one that is most widely used.
D. SOLID-STATE STRUCTURE OF METALS AND ALLOYS
Many of the properties of different metals can be ascribed to differences in solid-state structure. Some of these properties and structural features are summarized in Table 8.2.
TABLE 8.2. Properties of Selected Metals

1. Packing of Spheres
The structure of a solid metal can be visualized as a series of spheres (nuclei plus inner electrons), all with the same diameter, packed together in a regular three-dimensional array, and held together by a “sea” of mobile electrons. This type of arrangement differs markedly from the structure of solids that contain molecules or of molecular solids, where the disposition of atoms in the structure depends on the orientation of covalent bonds rather than on the packing of spheres, and where electron mobility is generally restricted. However, it does bear a superficial resemblance to the structures of inorganic ionic solids, which are also based on the packing of spheres, but spheres that have different diameters as required for most anions and cations. Moreover, the electrons in ionic solids are not delocalized throughout the whole structure as they are in metals.
Thus, the solid-state structure of a metal is relatively simple compared to those of other solids. Because there are only a small number of different ways in which spheres of the same size can be packed efficiently in three dimensions, relatively few packing patterns are found in different metals. These include the three common arrangements known as hexagonal close packed (HCP), body-centered cubic (BCC), and cubic close-packed (CCP) found in the metals listed in Table 8.2. The differences between these three structures is perhaps initially best understood through a consideration of the way in which different layers of spheres can be organized. This is illustrated in Figure 8.4.
Starting with a single layer of close-packed spheres (the A layer), and placing the atoms of the second layer in the depressions between the atoms in the first layer, we generate an AB two-layer structure. Now it is possible to construct a third layer in two alternative ways. First, spheres in the third layer can be placed over the available depressions in the second layer such that they lie above the atoms in the first layer to give an ABAB arrangement. Alternatively, they can be placed in depressions in the second layer that do not lie above atoms in the first layer, to give an ABCABC sequence. Note that they cannot occupy both of these positions in the same layer because insufficient space exists for this to be possible. An ABAB structure is described as a hexagonal close-packed (HCP) arrangement. An ABCABC system is called a cubic close packed (CCP) arrangement. A third structure is called a body-centered cubic (BCC) arrangement. It has an atom at the corner of each cube and one at the center of the cube. This is a structure that contains more open space than the other two, and is hence less dense.
The packing structure of a metal controls a number of properties, including density, electrical and thermal conductivities, and the way in which layers of atoms slide past each other under tension, pressure, or impact. The sliding planes are called “slip planes” or “shear planes.” The existence of many potential slip planes in a structure leads to the property of ductility, the ease with which a metal can be extruded into wires. In this sense, BCC and CCP systems, such as Cu, Ag, Au, Al, and Fe, tend to be ductile, but HCP metals, such as Zn or Mn, are generally more brittle because their structure provides fewer slip planes.
The influence of the crystal structure of a metal on thermal or electrical conductivity (see the next section) is less clear-cut. Some of the metals with the highest electrical conductivities (Al, Au, Cu, Ag) have cubic close-packed lattices, which suggests that a high packing density is important for good conductivity. However, Pb and Pt have the same packing arrangement but low conductivities. Titanium, which has a low electrical conductivity, exists in a hexagonal close-packed (dense) structure. So there is clearly more to understanding electrical conductivity than knowing the packing density.
Figure 8.4. Illustration of how close packing of atoms in a metal can yield either a cubic close-packed (a) or a hexagonal close-packed (b) structure.

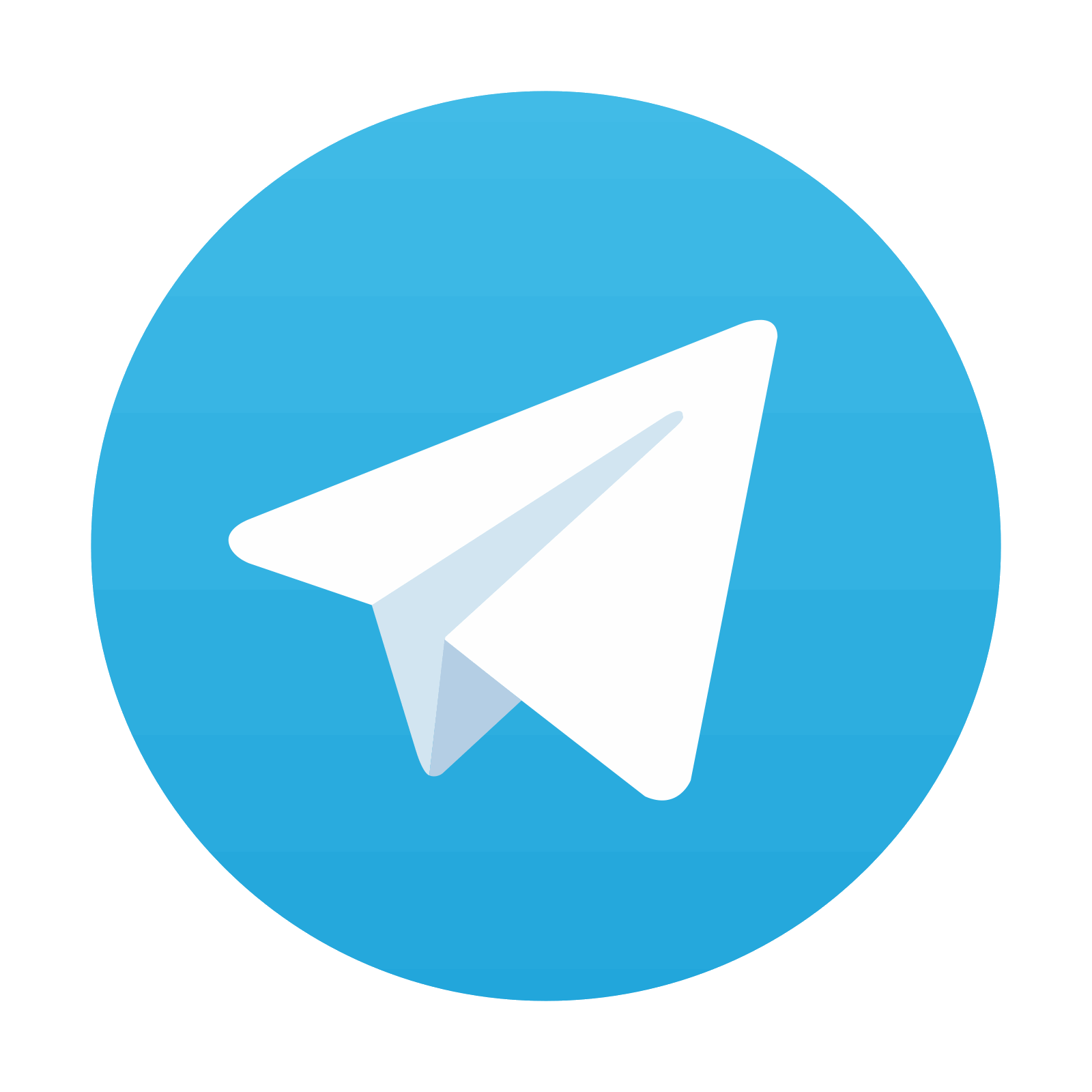
Stay updated, free articles. Join our Telegram channel
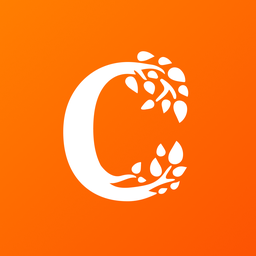
Full access? Get Clinical Tree
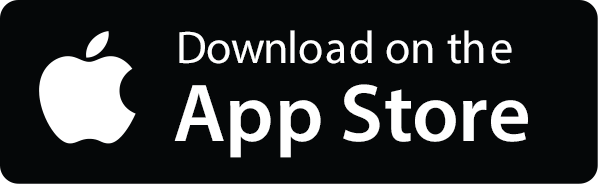
