Fig. 4.1
General setting of electroforming cell consisting of anode, cathode and electrolyte
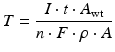
(4.1)
The transfer of matter from the anode to the cathode is realized in an electrolyte solution, which contains ions of the same metallic element that has to be deposited. Electrolyte solution plays an important role in determining the quality of the products. There are at least two typical electrolyte solutions, chloride- and sulphate-based baths. Depending on the metal being electroformed, the result might vary depending on the type of bath. Kim et al. [5] reported that chloride bath shows a higher current efficiency compared to that of sulphate bath when they are used to manufacture CoFe, NiCo and CoNiFe alloys, probably due to the catalytic activity of chloride ions in the deposition of Ni and Fe through the formation of an ion bridge between the electrode and the metallic ions being discharged [5]. Moreover, the use of chloride bath has been reported to produce a ductile deposit at higher temperatures for iron electroforming, making it a common electrolyte solution for industrial processing. However, the use of sulphate bath has been reported to produce pure iron deposit with smoother surfaces and a low amount of pitting leading to thicker layers [4]. Therefore, careful selection of electrolyte bath is highly required as a function of the material being deposited.
The shape of the deposit reproduces that of the cathode/mandrel; low adherence between the substrate and the deposit is required to easily remove the electroformed manufact. Metallic materials currently used for the realization of a mandrel are, for example, titanium and stainless steel. This can be obtained by creating a passive layer on the surface of the mandrel allowing an easier detachment of the deposit; for this reason, sodium dichromate solution is often applied on the surface of a mandrel made of stainless steel or nickel [3]. Moreover, when an insulating material is used as a mandrel, the main challenge is to make the surface conductive in order to attract the metal ions. Generally, the conductivity of such a material can be modified or improved by the application of silver film with painting or spraying [2].
Additionally, mandrels can be divided into two categories: permanent and temporary ones [3]. Permanent mandrels are made of metallic or nonmetallic materials that can be formed into a precise shape with the advantage of a high resistance against mechanical damage and/or chemical corrosion. Examples of materials used for permanent mandrels are stainless steel and photosensitive resins that are important materials for compact disc (CD) industry, since they allow the reproduction of highly accurate surface details. In contrast to permanent mandrels, temporary ones are expected to be dissolved after the electroforming process. For this reason, metals with low melting temperature such as bismuth and tin are normally chosen. Otherwise, reactive metallic materials such as aluminium can also be envisaged because they can be dissolved in concentrated basic solutions (sodium hydroxide). This procedure leaves the electroformed nickel intact because of its resistance to strong alkaline solution [2].
4.3 Industrial Applications
The final products of electroforming can be easily found in everyday life. Electroforming is involved in the making of screen-printing cylinder that gives motives to our clothes, blankets, wall papers, coffee cups and even for banknotes. Electroforming is also used to create televisions, radios and computers’ circuit boards, and also it is used in the process for the production of the holographic logo available on credit cards. The music recording industry uses electroforming in the process of CD making. The patterns on the above-mentioned final products all come from electroformed masters [2, 6].
1.
Audiovisual compact discs (CDs): a single CD consists of a helical track with 30 billion pits only 0.1 μm deep and 0.4–0.6 μm wide. Size accuracy and position precision on the track are required in order to maintain a high sound quality.
2.
Electroformed foil products: nickel thin foil is vastly used for printed circuit boards with welded connection. Nickel foil is also used to fabricate solar energy absorbers.
3.
Mesh products: electroformed mesh products with particular patterns are used for screen-printing cylinders in the typography industry to produce fabrics and carpets.
4.
Macro electroforms: macro electroforms are used to produce individual large components in the aerospace industry as well as in the automotive industry.
5.
Small electroforms: electroforming enables the development of micro engineering applications to produce micron-scale components for automotive, aerospace and biomedical industry. An innovative factual application is the production of small electric motors used in cardiovascular disease treatment. These miniaturized machines can pass arteries to scour the walls and remove the plaque deposit.
4.4 Electroforming of Pure Iron
Pure iron has been proposed as a biodegradable metal due to its superior mechanical properties when compared to those of its counterpart—magnesium alloys. Various fabrication methods have been applied to produce iron as a biodegradable implant including casting [7], powder metallurgy [8] and electroforming [9]. From the processing point of view, electroforming is associated with a low production cost and a simpler manufacturing process compared to other ones. Electroforming was then considered as an interesting fabrication method to be explored for biodegradable implant application. The first electroformed iron application for biodegradable cardiovascular stents was reported by Moravej et al. [9]. It is considered to be an ideal process for stent making, since a precise dimension is required to produce a thin-walled bulk material with superior purity and adjustable microstructures.
Some parameters need to be optimized during the electroforming process such as electrolyte composition, current density, pH and temperature. The electrolyte is a very important factor, since it is the source of metallic ions. Several electrolytes such as iron sulphate, iron chloride, iron sulphate–chloride, iron sulfamate, iron fluoborate or alkaline solutions [4] are currently used in industrial applications. Furthermore, the electrolyte composition has a significant influence on the properties of deposited iron. As previously reported [9], an electrolyte with 400 gL−1 FeCl2 and 80 gL−1 CaCl2 in de-ionized water was selected to produce electroformed iron. The solution known as Fischer–Langbein is a common electrolyte used to produce a ductile electroformed iron. Moreover, additives such as saccharin and sodium dodecyl sulphate are added, respectively, as stress-reducing and wetting agents (anti-pitting), enhancing the quality of the deposits.
Other important parameters about iron electroforming are pH, temperature, current density and cathode material. The pH is controllable by the addition of HCl, H2SO4 or NaOH. It was shown that for 0 ≤ pH ≤ 3, iron chloride baths have a significant effect on mechanical properties of electroformed iron. Electrolytes with pH < 0 produce highly stressed and brittle deposits compared to those obtained with pH ≥ 3. The temperature of the electrolyte has an effect on electrodeposits’ grain size and texture, as well as on the mechanical properties. Higher temperatures are associated to ductile deposits, but they tend to produce larger grain size layers with reduced hardness, tensile strength and internal stress [5].
Current density can control the nucleation rate during the electroforming process. Increasing the current density increases the difference in the electrode potential between its equilibrium potential and its operating potential—overpotential—thus increasing the nucleation rate [4]. Cathode chemical composition and surface state are also important parameters, influencing the microstructure and properties of the deposits. In electroforming process, less adhesive cathode is preferred since the deposited film has to be separated from the cathode after deposition. The selection of cathode depends on the desired shape and material dimension. The material of cathode needs to be conductive in order to transfer the electrical current required for electrodeposition [3].
In the work carried out by Moravej et al. [10], the deposition was carried out with a pH = 1, a bath temperature of 90 °C and a current density of 2 A dm−2. These parameters have been proved to produce an electroformed foil with high ductility and a lower surface roughness. Commercially pure titanium was selected as cathode material due to its reduced adherence to iron, allowing a rapid mechanical removal from the cathode. Foils produced with these parameters were studied to compare their microstructure, mechanical properties and corrosion behaviour with those of rolled iron and stainless steel 316 L. The results showed that grain size and texture were the main factors influencing mechanical properties and corrosion behaviour in simulated biological solution. Electron back-scattered diffraction (EBSD) revealed that electroformed iron showed a highly oriented (111) fibre texture, and it has columnar grains with an average size of ~4 μm (Fig. 4.2). From the mechanical point of view, the yield strength of electroformed iron was comparable to that of 316 L SS, even though its ductility was lower because of the internal stress. Therefore, annealing was performed to induce recrystallization due to the presence of residual stresses in microstructure of the material, which has a higher concentration of structural defects. The elongation at break changed significantly from 8 % as produced to 18 % after annealing at 550 °C for 1 h and 30 % after annealing at 600 °C for 1 h. The average grain size after heat treatment at 550 °C was ~6 μm, significantly smaller than that of iron produced by melting, which after recrystallization-induced heat treatment presented an average grain size of ~25 μm. Static and dynamic degradation test on electroformed iron showed a faster degradation rate compared to that one produced by melting. The enhanced corrosion behaviour of the former was correlated to its finer structure, while the latter has a lower density of grain boundaries that makes the material less susceptible to chemical attacks. Another cause of the higher rate corrosion of electroformed iron is the high density of structural defects [10].
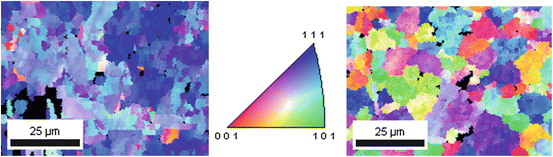
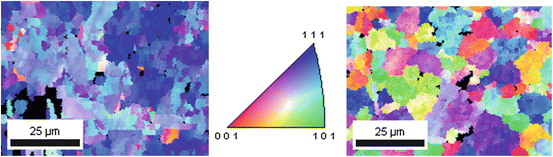
Fig. 4.2
Orientation map of electroformed iron surface. Left: electroformed; right: after annealing at 550 °C (Reprinted from Ref. [10], Copyright 2010, with permission from Elsevier)
4.5 Electroforming of Binary and Ternary Alloy
Metal alloying was used to improve mechanical properties and to accelerate corrosion rate, especially for iron. Hermawan et al. [8] were the first who introduced Mn as an alloying element for iron-based alloys cardiovascular stent. The results showed that Fe-35Mn has superior mechanical properties close to those of 316 L SS, the gold standard for cardiovascular stents. The corrosion rate of Fe-35Mn doubled compared to that of rolled pure iron. Furthermore, Schinhammer et al. [11] developed a new alloy with Mn and Pd. These elements create a noble intermetallic phase (Fe, Mn) Pd which is responsible for both an increased degradation rate and enhanced mechanical properties. Liu et al. [12] studied Fe–X binary alloys with another approach. They studied the effect of Mn, Co, Al, W, Sn, B, C and S on pure iron. They concluded that C, S, W and Co could be successfully used as potential alloying elements for biodegradable iron-based biomaterials. In another study, Wegener et al. [13] produced Fe–C, Fe–P, Fe–B and Fe–Ag alloys. The effect of P was beneficial for density and strength and useful to increase the degradation rate.
Mechanical properties and corrosion behaviour of electroformed iron still need to be improved and fully understood. Another suitable strategy for the modification of electroformed material properties is the deposition of layers with an alloying element that shows a gradual amount variation over thickness. This deposition system could create different phases and microstructures influencing the mechanical properties and corrosion behaviour. The electroforming of binary and ternary alloys has been explored in several publications [4, 14–21]; at least 22 elements have been proposed by Schlesinger et al. [4] for the realization of iron-based alloys. In biodegradable metal applications, it is important to choose a nontoxic element for the human body. For this reason, some elements that are safe to be alloyed with iron by electroforming include carbon, phosphorus, zinc, boron and cobalt. Table 4.1 shows some data about binary and ternary alloys, which have been applied for various purposes.
Table 4.1
Various applications of Fe-based alloys
Bath composition (g/ml) | pH | Temp (°C) | Current density (A/dm2) | Application | |
---|---|---|---|---|---|
Fe | FeCl2 0.4 | 1–3 | 86–198 | 10 | Protective shield |
[14] | CaCl2 0.08 | ||||
Fe–Co | FeCl2 11.8 | 0.3 | 25–90 | 6 | Micro electro mechanical system |
[15] | CoCl2: balance | ||||
CaCl2 9 | |||||
Fe–Ga | Ga2(SO4)3 1.5 | 3 | 25 | N/A | Magnetostriction material |
[16] | FeSO4 0.19 | ||||
H3BO3 8.1 | |||||
C6H5Na3O7 0.58 | |||||
HC6H7O6 0.23 | |||||
Fe–Ni | FeCl2 400 | 0.5 | 95 | 5–20
![]() Stay updated, free articles. Join our Telegram channel![]() Full access? Get Clinical Tree![]() ![]() ![]() |