A. PERSPECTIVE
Surface science, like the field of membranes discussed in Chapter 13, is a subject that is important to many different areas of materials science. These areas include biomedical materials, semiconductors, adhesion, optics, and membrane science, to name only a few. Virtually all the applications of polymers and metals depend in some way on their surface behavior. Aspects of surface science have been introduced in other chapters, and the objective here is to consider the subject in general terms. Thus, in this short chapter we bring together a number of these different aspects and summarize some of the underlying principles.
In order to understand the behavior of surfaces, it is necessary to know something about the chemistry and physics of a given interface. Materials that have surfaces that are similar in chemical composition to the bulk material, may generate surface properties that can be understood from a knowledge of the internal structure. For example, the crystal structure of a metal may be the key to its behavior as a heterogeneous catalyst. However, for most materials the surface composition differs from that of the bulk material, and the chemical nature of the interface is a key to the properties. For example, a metal oxide or hydroxide layer at the surface of a metal will control the sensitivity to further oxidation, the extent of continued corrosion, the adhesion of surface coatings, and the wear of bearings and other sliding surfaces. For ceramics, the presence of surface hydroxyl groups will allow particles to coalesce when heated and will be responsible for the separation behavior of compounds passing through a chromatography column. A wider variety of surface groups are present on polymers, and these are discussed later in this chapter.
Surface properties that underlie many applications include the hydrophobicity or hydrophilicity of the material, as well as its acidity, basicity, and coordination power, all of which are connected with the presence of interfacial groups such as hydroxyl, amino, oxide, nitride, alkyl or aryl, acidic units such as COOH or SO3H, and the character of the interface. By “character” we mean the thickness of a surface layer, the degree to which it adheres to the underlying material, and its porosity and permanence.
The important surface characteristics of a material are only rarely the con sequence of a single layer of atoms at the interface with the environment. More often they depend on structural features that lie buried below the surface layer. Thus, it is important to know the depth of the interfacial layer, whether expressed in the range of Angstrom units, nanometers, or micrometers. This information may be obtained by optical microscopy of sections, by XPS, or by TIR-IR methods.
B. SUMMARY OF CHARACTERIZATION METHODS
Surface science is heavily dependent on analytical characterization methods. Some of these techniques are described in Chapter 4. For example, the surface of a metal can be explored by techniques that range from X-ray photoelectron spectroscopy (XPS) to scanning electron microscopy (SEM) (see Chapter 4). Polymer surfaces may be investigated by the same methods plus total internal reflectance infrared spectroscopy (TIR-IR). Surfaces of ceramics, which often bear Si—OH or Al—OH groups, and the surfaces of polymers can be examined by reaction chemistry, XPS, or SEM methods. Surface planarity, which is an important aspect of both integrated circuit semiconductor technology and nanotechnology, can be addressed by the use of ellipsometry. Of particular importance are optical microscopy, scanning electron microscopy (SCM), X-ray photoelectron spectroscopy (XPS), scanning tunneling microscopy (STM) and atomic force microscopy (AFM), and contact angle investigations. The application of theory to the study of surfaces has also been productive. Optical microscopy is applicable to surfaces of all materials. XPS, SEM, STM, and AFM methods are particularly useful for metal and semiconductor surfaces, powders, and micro- and nanofibers of ceramics and polymers.
1. Important Aspects
What are the surface characteristics that play such a significant role in metal science and technology? The sensitivity of a metal surface to oxidation, corrosion, or adhesion to coatings plays a dominant role in applications such as automotive, marine, or architectural engineering. The resistance of a metal surface to corrosion is a key property in electrical switches, dentistry, and catalysis. Questions that need to be answered for metals are the chemical nature of any surface layer (the presence of oxides, nitrides, hydroxides, etc.) and the depth and stability of the interfacial layer. Is the surface layer electrically conductive or insulating? Does it coordinate to molecules of the types found in surface coatings? If a second metal is deposited on the surface of the first by vapor deposition, sputtering, electrodeposition, or dipping the first metal into a bath of the molten second metal, is the crystal structure of the second metal influenced by the crystal structure at the surface of the first? What is the strength of adhesion between the two?
2. Etching of Metal Surfaces
The process of removing metal from a surface by immersion of the metal in an acid bath has for many years been the basis of both artistic techniques (intaglio printing) and metal surface cleaning. In addition, valuable information about the surface of a metal can be obtained by etching. By this we mean treatment with a reagent, such as an acid, that will dissolve the outer regions of the surface. Ideally, the attack on the surface will be selective so that grain boundaries or other morphological features will be revealed. Metal surfaces can also be studied by reactive-ion etching, in which ions derived from a plasma remove both surface oxides and the metal beneath.
An especially valuable technique for the etching of metal surfaces is oxidative electrochemical etching, which involves using a metal as an electrode in an electrochemical cell. As described in Chapter 13, aluminum can be oxidatively etched in acidic solution to form aluminum oxide nanotubes. The reaction begins at the surface and extends deep into the metal. A similar process using titanium metal foil generates a layer of semiconductive columnar titanium dioxide nanotubes at the surface.
3. Heterogeneous Catalysis by Metals
Many chemical processes are catalyzed by metal surfaces. Classical example reactions include hydrogenations of alkenes to give alkanes or reduction of nitro com-ponds to amines. Metals that are commonly used in heterogeneous catalysis include finely divided nickel, iron, and platinum. Because of the economic impact of heterogeneous catalysis by metals, considerable research effort is devoted to understanding the mechanisms of these processes. A common feature of nearly all these catalyses is the coordination of reactant molecules to the metal surface, followed by reactions that are mediated by the surface features. Thus, the surface of a metal particle often contains ledges and steps that represent the emergence of crystal structure features at the interface (Figure 15.1). These steps may present unsatisfied valences or unused coordination sites to the external environment such that unsaturated molecules or hydrogen will be held on the surface in orientations that are favorable for reactions. Grain boundaries and dislocations that emerge at the surface may also participate in these processes. Clearly, the smaller the metal particle, the greater is the ratio of surface to volume and hence the more effective is the catalysis for a given weight of metal. Catalyst “poisoning” can occur when impurity molecules that have a strong affinity for the coordination sites are preferentially adsorbed and block the catalytic reaction.
4. Metal Surfaces and Vapor Deposition, Sputtering, or Solution Reactions
The process of chemical vapor deposition has been mentioned in earlier chapters, particularly in connection with semiconductor fabrication and optical materials. In this process volatile organometallic compounds are decomposed at elevated temperatures in vacuum, and the metal atoms are allowed to impinge on a surface. This process allows very thin films of a metal to be deposited to form wires, coatings, mirrors, and a wide range of other features. “Sputtering” is a related process in which a metal is vaporized at high temperatures and allowed to deposit on a surface. The preparation of gold coatings for SCM imaging uses this method. An advantage of the sputtering method is that contamination from nonmetallic species in the vacuum chamber is avoided. Finally, some thin metallic surfaces can be deposited on other materials by chemical processing. The best known of these is the deposition of silver mirrors by the exposure of glass surfaces to an aqueous solution of a silver salt that contains a reducing agent such as formaldehyde or glucose. Finally, use of a metal electrode in an electrochemical cell allows a second metal to be electrodeposited on the first. A well-known example is chromium plating on steel or nickel, and of silver plating on nickel.
Figure 15.1. Heterogeneous catalysis at metal surfaces often involves coordination of reactant molecules to specific sets of metal atoms that emerge at the surface and present unused coordination sites to reactant molecules.

A characteristic of deposited metal surfaces is their high reflectance, which results from the uniform thickness of the metal. However, an important additional characteristic is that most of these methods can be used to coat three-dimensional objects such as complex surfaces being prepared for SEM analysis.
1. Oxide Ceramic Surfaces
The surface chemistry of oxide ceramics is usually dominated by the presence of Si—OH or Al—OH groups. Both of these are hydrophilic, acidic units, which can be neutralized by exposure to aqueous base. The presence of surface hydroxyl groups is responsible for the ability of powders of many oxide ceramics to undergo sintering by condensation crosslinking when they are compressed at moderate temperatures. As discussed in Chapter 7, the same surface groups determine the behavior of clay particles in media with different pH values. The surface structure is also important for the functioning of alumina powder to separate compounds dissolved in organic media in chromatography procedures, because of the differential interaction of organic molecules with acidic surfaces.
2. Chemical Modification of Glass Surfaces
The same acidic hydroxyl groups that dominate the surface chemistry of many ceramic particles also play a role in the behavior of glass surfaces. For example, many chemical reactions carried out in glass equipment suffer from side reactions that arise from hydrolysis-type processes at the glass–solvent interface. This can be avoided by prior treatment of the glass with molecules such as trimethylchlorosilane to give hydrophobic, pH-neutral surfaces. This process is shown in reaction 1. A dramatic illustration of the effectiveness of this procedure is to compare the pH of water in contact with fiberglass. Material with untreated surfaces will slowly dissolve in water to give a basic solution. The same material surface treated with trimethyl-chlorosilane will not. Related chemical reactions are employed to covalently bind bioorganic molecules to glass, processes that are important in micro-separations technology, and for the adhesion of surface coatings to glass.
3. Nonoxide Ceramic Fiber Surfaces
As discussed in Chapter 7, several of the nonoxide ceramics produced by pyrolysis of inorganic polymers are sensitive to reaction with atmospheric oxygen to form silicon oxide materials. This problem is particularly acute for thin fibers or whiskers of silicon carbide or silicon nitride. In the case of silicon carbide fibers, this surface oxidation process is utilized to protect the interior of the fibers from further reaction with the atmosphere. For this type of surface reaction to be useful, the oxide coating must be strongly adherent to the core of the fiber.
4. Ceramic Decomposition by Pollutants
A final example of the importance of surface chemistry in ceramic technology is the ability of a masonry surface to withstand the effects of atmospheric pollutants. Architecturally important buildings throughout the world are crumbling because of attack by acidic atmospheric pollutants on the stone. The two most sensitive masonry materials are sandstone and limestone. Sandstone consists of silica particles cemented together by calcium carbonate. Limestone is mainly calcium carbonate. Sulfurous and sulfuric acids are major atmospheric pollutants, and these dissolve the calcium carbonate and initiate the materials breakdown. Attempts to retard these processes include coating the ceramic with transparent hydrophobic polymers.
1. General Aspects of Polymer Surfaces
The ability of a polymer surface to resist the ingress of water, organic solvents, bacteria, gas molecules, and the overall hydrophobicity or hydrophilicity are crucial properties in automotive or marine engineering, biomedicine, electrical engineering, membrane design, and microelectronics.
The surface of a polymer depends on the chemical composition of the component macromolecules, the physical state of the surface (glass, elastomer, etc.), and the method used for processing and fabrication. For example, different polymer surfaces may contain a wide variety of chemical species that range from hydrophobic alkyl, aryl, and fluorinated organic units, to hydrophilic hydroxyl, amino, or carboxylate units, and they may also bear the products of atmospheric oxidation such as carbonyl, hydroperoxide, or epoxy units. However, the property-determining groups that actually populate a surface often depend on the method of fabrication, as discussed below. An understanding of the factors involved in polymer surface behavior is an essential requirement for designing new polymers in a rational way.
2. Unusual Characteristics of Polymer Surfaces
Because polymer molecules are in constant motion, especially above the glass transition temperature, the surface of a polymer may change over time in response to the environment with which it is in contact. For example, dry air is considered to be hydrophobic, and hydrophobic components of the polymer molecules may migrate to a polymer/air surface. The converse happens if the surface is in contact with water. It is this feature of “surface turnover” that distinguishes polymers from other materials.
One of the main methods for studying surface turnover is to measure the contact angle of water droplets or a hydrophobic liquid on the surface. The technique is described in Chapter 4. Thus, a material that is experiencing surface turnover may undergo a change in contact angle while a water drop is sitting on the surface. Note that there is a rough correlation between the contact angles and the hydrophilicity or hydrophobicity of the polymer side groups or skeletal units. Thus, chemical intuition is a good starting point for understanding polymer surface behavior.
Note also that the process of surface turnover has both positive and negative aspects for technology. A positive aspect is that it provides a method to fine-tune a surface by bringing it into contact with a hydrophilic or hydrophobic medium. The drawback is that a process such as adhesion may be compromised by a change in surface character after a bond has been formed between two different materials.
3. Chemical Modification of Polymer Surfaces
The surface of a polymer clearly depends on the molecular stucture of the component macromolecules, and the most obvious way to change the surface character is to use a different polymer derived from a different monomer. However, it often happens that an ideal target material needs to have two different sets of properties—one for the materials interior and another for the surface. For example, a biomedical material may require a hydrophobic interior to discourage water absorption or bacterial colonization, but a hydrophilic surface for interaction with specific proteins or cells. It is usually unwise to depend on surface turnover to generate these composite properties. Moreover, the application of surface coatings is a relatively short-term solution. However, chemical reactions that alter the covalently bound groups at the surface, while leaving the interior unchanged, may provide the require combination of properties. The process is illustrated schematically in Figure 15.2.
Figure 15.2. Illustration of the process of surface modification by wet chemistry in which a reagent in solution displaces polymer side groups at the interface, thus changing the surface character.

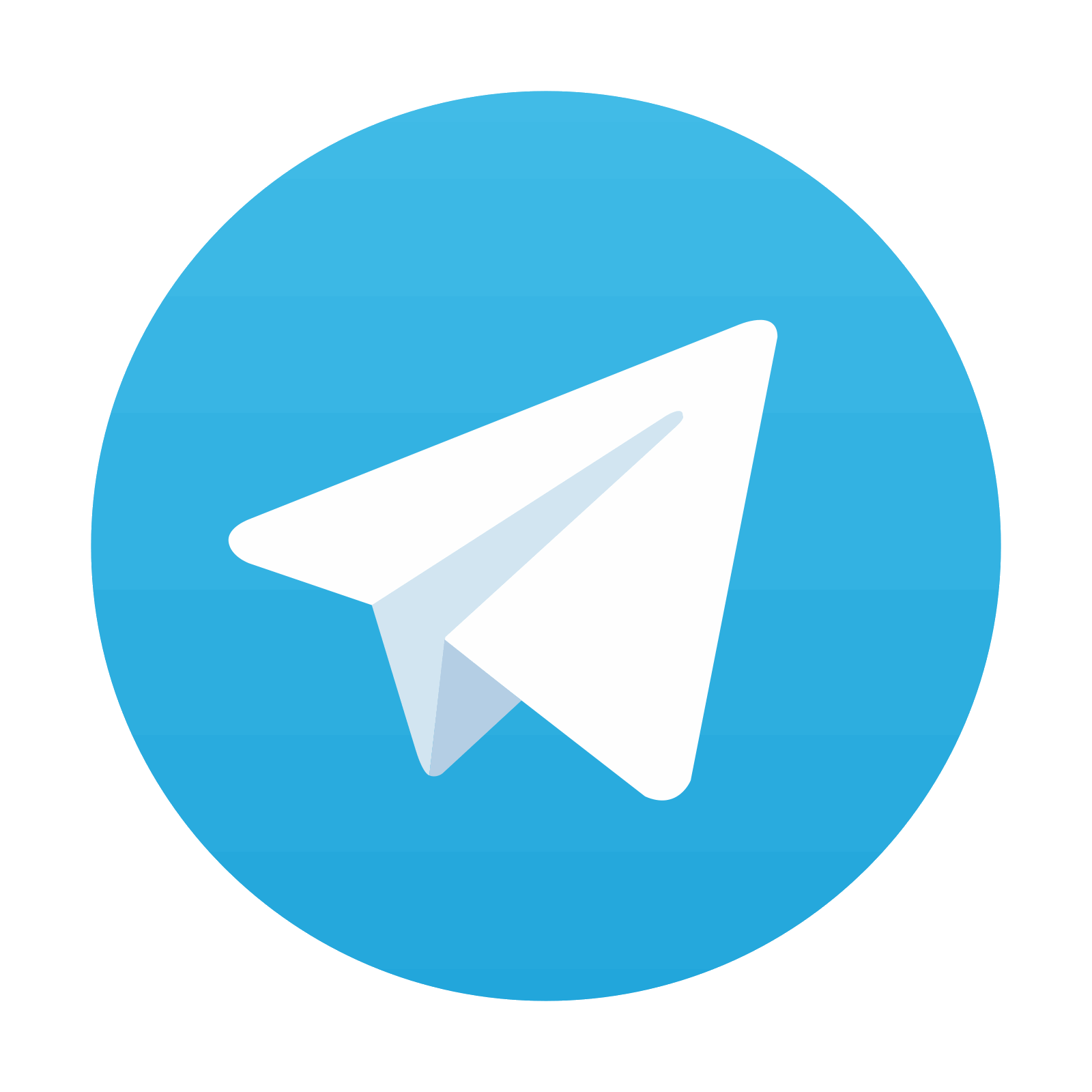
Stay updated, free articles. Join our Telegram channel
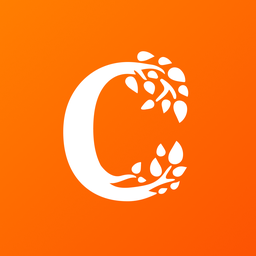
Full access? Get Clinical Tree
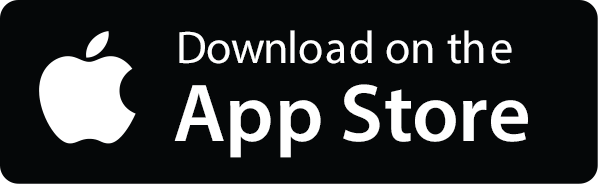
