Fig. 21.1
Elements of the risk management process and companion activities or topics
This structured approach helps to substantiate considerations and decisions. It eases documentation, and thus may help to communicate about them.
This chapter explains the basics of Risk Management applying it to the field of preparation and product care in pharmacies, that is from logistics to prescription assessment, from production to pharmaceutical care on the wards (Sect. 21.5). Essentials of frequently used methods will be described (Sect. 21.4). QRM aimed at quality of medicines has found its way to regulations (Sect. 21.6), for large-scale manufacturing as well as for preparation in pharmacies. Some guidance is given for implementation of QRM in pharmaceutical quality systems (Sect. 21.7).
21.2 Definitions
ICH Guideline Q9 is the reference document on quality risk management for pharmaceutical preparations [1]. Therefore in this chapter mostly ICH Q9 definitions are used. Many of them are identical to those of the International Standards Organisation (ISO, see also Sect. 35.7.2).
The definitions are tabulated in Table 21.1.
Table 21.1
Risk management definitions
Harm | Damage to health, including the damage that can occur from loss of product quality or availability |
Hazard | The potential source of harm |
Quality risk management | Risk management directed at the quality of the (medical) product |
Risk | The combination of the probability of occurrence of harm and the severity of that harm |
Risk management | The systematic application of quality management policies, procedures, and practices to the tasks of assessing, controlling, communicating and reviewing risk. |
Risk acceptance | The decision to accept risk |
Risk analysis | The estimation of the risk associated with the identified hazards |
Risk assessment | A systematic process of organising information to support a risk decision to be made within a risk management process. It consists of the identification of hazards and the analysis and evaluation of risks associated with exposure to those hazards. |
Risk communication | The sharing of information about risk and risk management between the decision maker and other stakeholders. |
Risk control | Actions implementing risk management decisions. |
Risk evaluation | The comparison of the estimated risk to given risk criteria using a quantitative or qualitative scale to determine the significance of the risk. |
Risk identification | The systematic use of information to identify potential sources of harm (hazards) referring to the risk question or problem description. |
Risk mitigation | Risk reduction |
Risk reduction | Actions taken to lessen the probability of occurrence of harm and the severity of that harm |
Risk review | Review or monitoring of output/results of the risk management process considering (if appropriate) new knowledge and experience about the risk |
Severity | A measure of the possible consequences of a hazard |
21.3 Risk Management Process
Risk management basically implies risk assessment (with subsequently risk identification, risk analysis and risk evaluation), risk control (with subsequently risk reduction and risk acceptance), risk communication and risk review. Figure 21.1 shows consecutive elements of the risk management process and keywords indicating companion activities or topics.
This section explains these elements and illustrates them with a simple example case of small-scale filling capsules with a powder mixture.
21.3.1 Risk Assessment
Risk assessment consists of the identification of hazards (Risk identification), followed by the analysis (Risk analysis) and evaluation (Risk evaluation) of risks associated with the occurrence of those hazards. As a simple illustration the extemporaneous preparation process of capsules according to a standard formulation is taken as to illustrate the principles involved.
21.3.1.1 Risk Identification
At first the process for which the risks have to be assessed is defined and delimited as well as its hazards that have to be focused upon.
As said the process to be assessed is limited to the extemporaneous preparation process of capsules according to a standard formulation. Let the focus be on a quality defect that will lead to not meeting the requirements for content uniformity.
Secondly the separate process steps are identified and coupled to possible deviations or ‘failure modes’ (What might go wrong?) as well as to the consequences (harms or effects) of these.
The process of the preparation of capsules is composed of several steps or unit operations. One step concerns mixing the active substances and excipients, giving the powder mixture. Another step is filling empty capsule bodies with the powder mixture. Possible deviations are: insufficient mixing and uneven filling respectively. The effect in both cases is insufficient content uniformity.
21.3.1.2 Risk Analysis
Risk analysis estimates the risk of every deviation that has been identified. The estimation consists of three aspects:
The severity of the consequences of the deviation
The probability of its occurrence
Its detectability (before it can lead to any consequences)
Insufficient mixing may be estimated (in a specific situation: operator, equipment, pharmacy setting) as a risk that probably will occur and not be detected by an in-process control. Whereas uneven filling seems a little less probable and may be noticed by the operator or easily measured by in-process control of the capsule weights. Both deviations will lead to insufficient content uniformity. Both severities are assumed to be equally large.
21.3.1.3 Risk Evaluation
Risk evaluation is the comparison of the estimated risks.
It can be concluded that insufficient mixing poses a larger risk than uneven filling.
Risk evaluation will make risk prioritising possible. The use of a (semi-) quantitative scale can make risk evaluation more sophisticated. The determination of a risk criterion for risk acceptance is another addition. See Sect. 21.4.2.
21.3.2 Risk Control
The purpose of risk control is the reduction of the risk to an acceptable level, followed by a check to consider if any new risks, introduced by the introduction of the control of identified risks, are acceptable. Risk control consecutively exists of the elements: risk reduction (some sources use the term: risk mitigation) and risk acceptance.
21.3.2.1 Risk Reduction
Risk reduction investigates all critical process steps to draw up measures that reduce the occurrence of the risks or improve the detectability. But any measure should not lead to the introduction of new risks.
For the reduction of the risk of an inhomogeneous powder mixture, the mixing process needs more attention. The operator can be taught to perform mixing correctly (see Sect. 29.4 about mixing quality), monitor their way of operating from time to time by observation or by assaying content uniformity of pilot batches, or introduce personal qualification and requalification for the preparation of capsules. In large-scale preparation an in-process control by Near Infra Red (NIR) is used to detect inhomogeneity (see Sect. 17.7), however for small-scale preparation NIR is not commonly used.
For the improvement in the capsule filling technique, teaching, observation and monitoring may be used as well. An in-process control on capsule weights after filling will increase detectability substantially. Ultimately each batch may be analysed before release.
Would these measures introduce new risks? Probably any interruption of an operation for an in-process control can lead to mix-ups. And weighing may cause a risk of cross contamination.
21.3.2.2 Risk Acceptance
Risk acceptance requires decisions about how much effort to reduce risks is feasible in terms of cost and benefit.
Analysis of each batch will take too much time and money (excess active substance needed) to be an option for extemporaneous preparations. The qualification of operators for the preparation of capsules, by validation and monitoring may be feasible. This may lead though to specialisation of operators and thereby to a decrease of flexibility.
The amount of effort used for risk control should be proportional (“commensurate” is the Q9 terminology) to the significance of the risk. In pharmacy preparation it will generally lead to more quality investments in stock preparation compared with extemporaneous preparations due to the higher number of patients that will be exposed.
In pharmacy preparation other elements will contribute to the balance that has to lead to acceptance (or not) of specific risks. These elements are, for instance, availability and the pharmacologic qualities of the active substance.
The standard operating procedure for extemporaneous preparation of capsules should reflect the decisions on quality risk management of that process. The level of quality risk management should be accounted for in the quality manual of the pharmacy.
21.3.3 Risk Communication and Documentation
Communication with stakeholders about the risk assessment’s results is important to give account of one’s professional decisions. By ensuring that key stakeholders are engaged in both the data collection process for the risk assessment and the decision-making for risk control, the decision-maker will get commitment and support for his QRM. Documentation will make communication easier. There should be a report for every risk assessment, of which the level is proportional to the level of risk.
Section 2.2.3. depicts models for a structured risk assessment of a prescription for extemporaneous preparations. The physician and the patient will be the most important stakeholders in that situation, the latter also represented by the competent authority. But the insurance company may be stakeholder as well because of the resources.
21.3.4 Risk Review
The experience and results of measures taken to diminish risks should be monitored and reviewed to decide if the chosen approach works. As with other elements of QRM, the level and formality of the review should be proportional to the level of risks.
Knowledge about mixing and filling being critical steps in capsule preparation are well known from professional education or literature and the effects of the efforts can be anticipated. Monitoring the actual effects however may confirm knowledge or sometimes may reveal unforeseen aspects. Moreover it will usually contribute to the motivation of the operators.
21.4 Methods
More can be said about methods for risk identification, risk analysis and risk evaluation. In Sect. 21.3 these phases were defined, and, as the capsule preparation example, executed in an informal, rather simple way. That section was meant as an introduction to the phases of risk management and the terminology. It also meant to convey the idea that defining and delimiting the process steps and thinking about risks with all staff concerned will already lead, halfway, to a proper result.
If risk management applies to a more complex or a less well-known process, some experience and methods may be helpful for a more formal risk assessment. They will be discussed following the sequence of: risk identification, risk analysis, risk evaluation. They also facilitate proper documentation, which is essential for being transparent about decisions.
21.4.1 Risk Identification
For any risk assessment method it is crucial that the problem or risk issue is well defined, described and understood. A common mistake is to start the risk analysis before the process to be analysed is well defined and well delimited. Such an approach is easy to imagine because a problem often creates a sense of urgency that tempts one into action though the framework is not yet understood. This mistake will most likely result in waste of time and personnel frustration.
A risk assessment can be performed retrospectively or prospectively. If an adverse event – whether a complaint, a deviation or adverse effect – happens it will be analysed retrospectively. Staff will be convinced about the necessity for any action. When staff do not report incidents however or do not qualify them as important the improvement process may be missed. For risk assessment a blame-free culture in the organisation is very important.
Prospective methods look at which risks may occur and assess the severity of these risks, in order to subsequently choose which actions should be taken to prevent errors and deviations. In the preparation of medicines prospective methods can be used for the initiation of new activities or purchasing a new equipment (see Sect. 21.5.2), as part of change control (see Sect. 35.6.10) and in planning of qualification and validation activities (see Sect. 34.14).
In practice a mixed approach of a retrospective and prospective method is often encountered. The capsule-filling example in Sect. 21.3 may appear to be a pure prospective method but by using process knowledge it also has, in fact, retrospective elements.
A ‘brainstorm’ is a useful technique to start risk identification. This may start with a presentation of a problem using preliminary information or already processed data. A preliminary evaluation of the possible harms to the patients may be presented to increase motivation. The brainstorm may be rather informal or more structured depending on the issue, the participants and traditions in the organisation. The goal is achieving, within short time, as many ideas as possible and engaging and focussing the participants.
Any risk identification may include a compilation of observations, trends and other available information. For more complex issues, a suitable presentation of background information and relevant data together with a targeted review of literature is advisable. Collecting and depicting this knowledge in a way that also can be used by other professionals may be very helpful in an expected rather long QRM process. Furthermore, depictions as these may facilitate handling of new knowledge or understanding. For listing and depicting the results flowcharts and process mappings are commonly used, if possible with marking of already known critical steps. As easy to use tools the Fishbone/Ishikawa diagram, flowcharts and mind maps are mentioned. Reference is made to [2] for further information about these tools.
21.4.2 Risk Analysis and Evaluation
When the problem or risk issue is well understood an appropriate tool for risk analysis has to be chosen. For the hazards identified during the brainstorm the associated risks has to be estimated. This may be a qualitative description eventually using semi-quantitative descriptors, as “high”, “medium” or “low” or it may be a quantitative analysis with scores according to a pre-defined scale. The estimation of risks in Sect. 21.3 occurred following a qualitative method. It enabled the prioritisation of two risks within a rather simple process and no comparison to a fixed value was felt to be necessary.
The numerical scores to be used in a (semi-) quantitative risk analysis have to apply to the factors severity, probability and detectability. The scale may be linear or non-linear, for instance logarithmic. Addition or multiplication of these scores will lead to risk scores. These can be put in a priority sequence: the harm with the highest scores should be dealt with the highest priority (efforts and formalities). And the score can also be compared with a fixed limit, for instance in case of a decision if any action has to be taken at all.
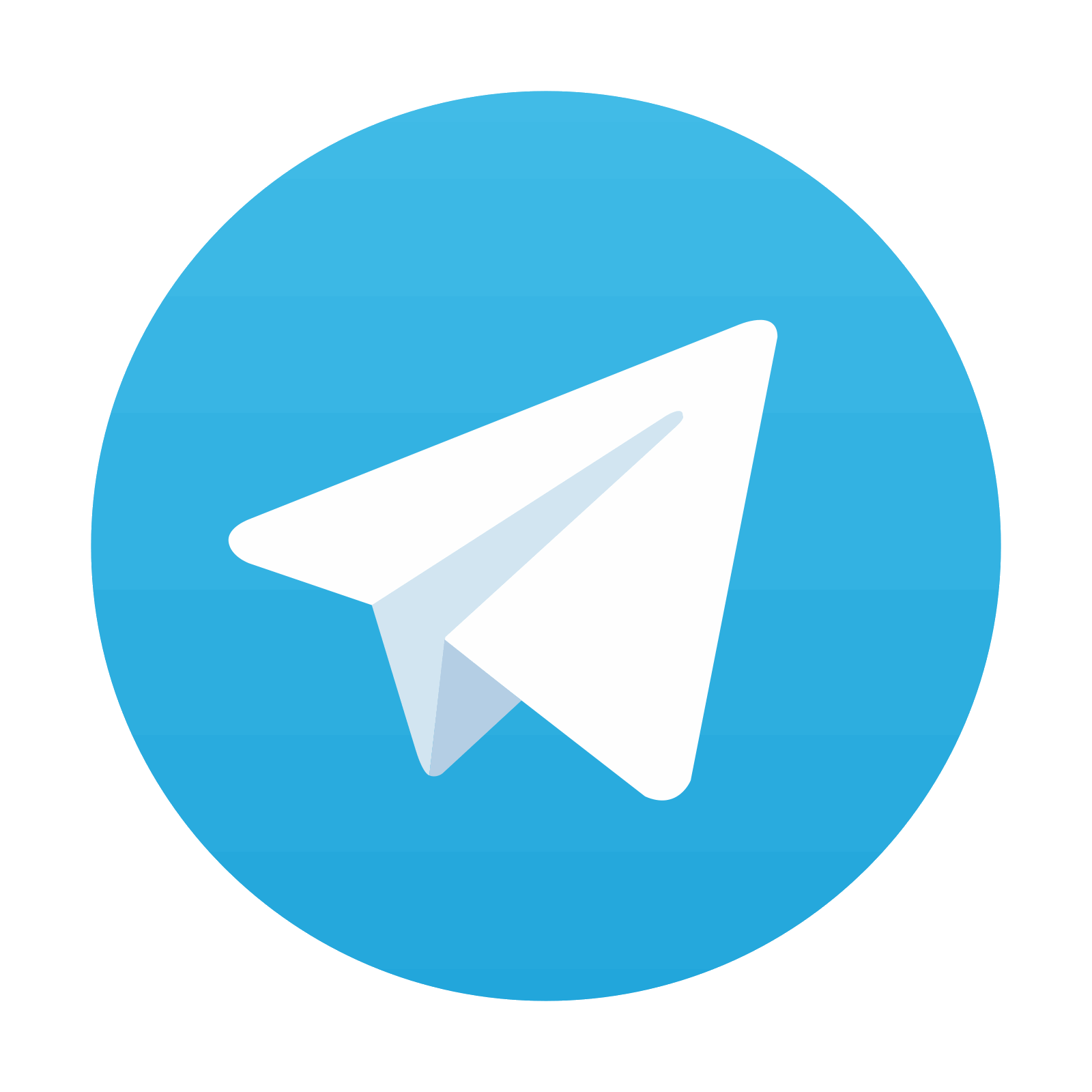
Stay updated, free articles. Join our Telegram channel
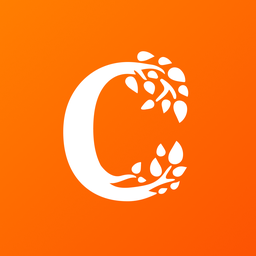
Full access? Get Clinical Tree
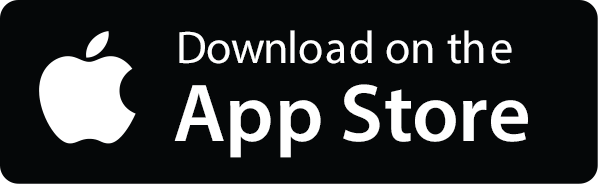
