Nanofabrication Techniques and Their Applications in Drug Delivery |
19.2 Top-Down Micro- and Nanofabrication Techniques
19.3 Nanoscale Characterization
19.3.1 Scanning Electron Microscopy
19.3.2 Atomic Force Microscopy
19.4 Applications of Nanotechnology in Drug Delivery
19.4.1 Micro- and Nanotopography to Overcome Epithelial Barriers
19.4.1.2 Nanostructures for Enhancing Paracellular Transport
19.4.1.3 Nanodevice Interactions with the Mucus Layer
19.4.1.4 Gecko-Inspired Nanotopography for Improved Adhesion
19.4.2 Nanotechnology in Controlled-Release Drug Delivery
19.4.2.1 Nanochannels in Membrane-Controlled Drug Delivery Devices
19.4.2.2 Nanochannels in Cell Encapsulation
The National Nanotechnology Initiative defines nanotechnology as any technology conducted or containing features at 1–100 nm. Nanodevices are systems designed on the micro- or nanoscale, with nanoscale features. When attempting to design features in the nanometer range, not only is fabrication a challenge, but verification and visualization of the results is a hurdle in itself. As this chapter will discuss, both micro- and nanoscale features offer a range of possibilities for improving medical technologies and drug delivery, but it is only with advances in fabrication technologies and analytical techniques that we are able to design, control, and characterize these features.
Nanoscale features confer unique and tunable properties to materials that can be leveraged by scientists and engineers to design materials and devices with novel properties and functions. For example, relative to their mass, materials with nanoscale features have much higher surface areas and a greater potential for surface interactions and for significant intermolecular forces than standard materials. When considering bulk material properties, physical and chemical properties are independent of size; aluminum will have the same material properties whether it is 1 in.2 or 1 ft2. However, nanosized particles exhibit properties such as electrical conductivity, chemical reactivity, and melting point, among others, which can depend on the particle size. Scientists can leverage these size dependencies to fine-tune material properties by controlling particle size.
In drug delivery and targeting, a multitude of barriers must be overcome to successfully deliver a therapeutic to its site of action. While the physicochemical properties and intended target of a drug often dictate these challenges, drug delivery systems (DDS) mitigate these obstacles to improve efficacy and bioavailability. Through their unique properties, micro- and nanofeatures bolster drug delivery systems by increasing membrane permeation, improving mucoadhesion, controlling drug release, and minimizing immune response. Because molecular and cellular biology occurs primarily at the nanoscale, utilizing nanoscale features allows scientists to interact precisely and directly with key components in biological systems. For example, nanopillar arrays can interact with individual cells to change cell morphology and increase drug permeability through a cell layer.
In this chapter, we will describe top-down micro- and nanofabrication techniques, outline some challenges in drug delivery that are being addressed through micro- and nanofabrication, and give examples of some specific applications of nanotechnology to drug delivery.
19.2 TOP-DOWN MICRO- AND NANOFABRICATION TECHNIQUES
Here we describe the fabrication and analytical technologies that have made manipulation and measurement at the nanoscale possible. Micro- and nanofabrication leverage materials and techniques originating in the microelectronics field to offer new approaches for overcoming traditional challenges in drug delivery. As a “top-down” process, micro- and nanofabrication provides a high level of control over size, shape, and surface features. Modifications of basic techniques such as lithography, molding, and extrusion allow for micro- and nanoscale manipulation of a range of materials, including polymers, as well as metals and metal oxides. The development of new fabrication techniques and materials with novel properties continues to expand the application of micro- and nanofeatures in drug delivery systems, but here we will cover only the basic fabrication techniques that are most relevant to creating nanotechnologies for drug delivery.
Solvent casting is a technique to form uniform layers of a material, most often a polymer, on a surface. The general idea behind solvent casting is to dissolve the material of interest in an organic solvent, to cast the solution into the desired shape, and to allow the solvent to evaporate, leaving behind the material of interest in its solid form. This technique typically works best with materials that in their solid state have structural integrity and using volatile solvents. A key component is finding a compatible solvent for the material of interest. Solvent casting is utilized in micro- and nanolithography in a number of ways. It is often used in conjunction with spin-coating systems to create uniform thin films. Spin-coating systems use centrifugal force to coat a substrate with a solution, by spinning the substrate. Solvent casting can also be used to fill molds to form materials into specific shapes. Templates and molds, especially on the micro- and nanoscale, can be combined with spin-coating systems, to create thin films with topographies defined by the template or mold over which the solution is cast.
Etching is a process by which a material is removed or degraded. When controlled, etching is a powerful technique in fabrication processes to selectively remove materials, leaving protected areas of the same material, or compatible materials, behind. There are a number of different types of etching that are important in micro- and nanofabrication, including wet etching, photoetching, and reactiveion etching. The type of etching is defined by how the material is being removed. In wet etching, a material is in contact with a solution that either dissolves the material or chemically attacks it, causing it to degrade. In photoetching, material is removed by exposure to UV light, and in reactive-ion etching, chemically reactive plasma is generated by an electromagnetic field that when directed at the substrate surface, removes the material that it contacts. Etching is most useful when combined with lithographic techniques that protect regions and patterns of a material, leaving only the exposed areas for etching. Etching can also be useful in fabrication processes to remove sacrificial templates or scaffolds. The etching process can be controlled by the duration and strength of exposure to the etchant.
Lithography was first developed as a printing technique in the late 1700s, that involved creating a template stamp (by creating a grease-based image on lithographic limestone and subsequently etching the stone that was not protected by the grease-based image), which could then be used to transfer ink onto paper. In micro- and nanofabrication, lithography typically refers to photolithography, one of the most commonly used techniques.
Photolithography uses a similar approach to print lithography, but with different materials and more precision (Figure 19.1). Photolithography is made possible by the development of photopatternable materials called photoresists. Photoresists are polymeric materials that cross-link, polymerize, or cleave, when exposed to UV light. Photoresists that polymerize or cross-link upon UV exposure are called negative photoresists because the areas exposed to UV light are the areas that are retained in the final template, leaving the inverse of the UV-blocking photomask. Positive photoresists are degraded with UV exposure, leaving only the areas of photoresist that were blocked from exposure by the photomask pattern.
To create patterns using photoresists, exposure to UV radiation is limited by a micropatterned photomask with the desired features. Photomasks can be designed for either positive or negative photoresists to achieve the desired patterns. For example, when using a negative photoresist, the desired pattern will be clear with all other areas blocked out, and for a positive photoresist, the desired pattern will be blocked out, with all other areas transparent.
The photoresist pattern can be the final template, or the photoresist can be used to transfer the pattern to an underlying substrate in a subsequent etching step. In the latter case, the photoresist is first coated over the substrate of interest before UV exposure. The negative pattern of the photoresist (i.e., the areas where the photoresist is absent) allows the underlying substrate to be exposed for etching, resulting in a final pattern on the substrate that reflects the positive photoresist pattern from the areas blocked to etching by the photoresist. Lithography is often applied in a layer-by-layer approach, leveraging solvent casting and spin coating to deposit each layer and create complex patterns of multiple materials. For example, after depositing and lithographically patterning one material onto a substrate, a second material may be deposited through solvent casting on top of the first layer and lithographically patterned with a different pattern. In such a way, one is able to produce hierarchical features with multiple materials.
Photolithography is the basis for many microfabrication procedures and leverages additional techniques such as solvent casting and etching in the process. Depending on the materials being used and the precision of the masks, photolithography can be applied in various approaches to create a breadth of designs, structures, and devices, limited only by the creativity of the designer. The resolution of photolithography is limited by the wavelength of the light used to treat the photoresist. While standard photolithography can achieve at best 1 μm resolution, special light sources such as deep ultraviolet light can improve resolution to as small as 50 nm.
While photolithography allows the designer precise control over shapes and sizes, it can only be applied to a flat substrate and is not flexible enough to create geometric shapes that are not flat on the ends, such as spheres or arches. A further limitation of photolithography is the need for a cleanroom environment, free of particles and dust.
While photolithography is the most commonly used lithographic technique in micro- and nanofabrication, there are a number of other lithographic approaches, and modifications of existing approaches, that are also being used. Techniques such as multibeam interference lithography, probe lithography, electron-beam lithography, and nanoimprint lithography complement photolithography, to increase patterning capabilities by expanding the range of materials that can be patterned, as well as the sizes and shapes of patterns that can be achieved.
Molding is a technique that uses a stamp or a mold to transfer a pattern onto a surface. There are a number of different molding techniques utilized in micro- and nanofabrication. Hard-pattern molding uses a micro- or nanopatterned template as a stamp or mold for repeated patterning of polymer surfaces. Micro- and nanofeature hard mold templates are created by using other techniques such as reactive-ion etching or electron-beam lithography to transfer a pattern into a hard substrate. A monomer, polymer, or prepolymer is then applied to the mold and cross-linked or cured. There are several techniques such as nanoimprint lithography and step–flash imprint lithography that use hard-pattern molds to transfer patterns in the lithographic process.
Soft-pattern molding, also known as soft lithography, uses a micropatterned elastomeric material as the stamp or mold. Replica molding transfers a patterned master to polydimethylsiloxane (PDMS) and then solidifies a photocurable or thermally curable prepolymer against the PDMS mold to produce a replica of the original master. Solvent-assisted micromolding uses a solvent to swell or dissolve a polymer against a PDMS mold. Upon evaporation of the solvent, the polymer substrate solidifies around the PDMS mold and is thus inversely patterned with the mold features.
Hard-pattern and soft-pattern moldings are the broadest categories of molding techniques, but in recent years a number of more specialized molding techniques have been developed to overcome challenges in specific applications. For example, in order to prevent thermal degradation of drugs incorporated directly into polymer devices, a low-temperature vacuum-molding technique was developed to cure the molded polymer without the need for elevated temperatures.
The approaches introduced here are not an exhaustive representation of fabrication techniques used in micro- and nanofabrication, but rather an overview of the basic techniques that are critical to fabrication processes. Many specialized and novel techniques are emerging based upon these basic approaches. Most advanced fabrication procedures do not simply utilize a single technique but rather combine approaches in multistep processes to create complex systems. In Section 19.4, we will discuss specific examples of micro- and nanotechnologies in drug delivery that utilize these approaches in their fabrication processes.
19.3 NANOSCALE CHARACTERIZATION
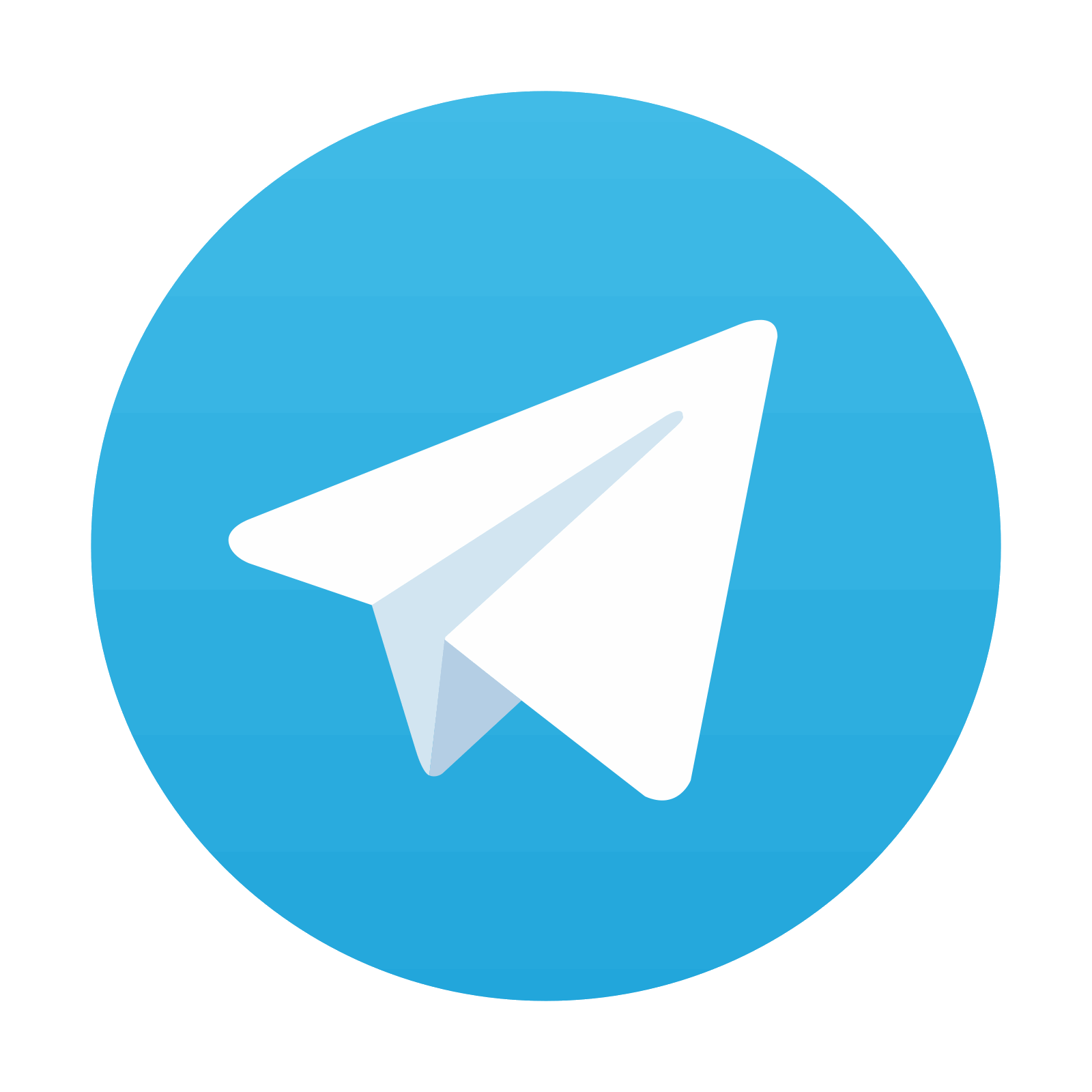
Stay updated, free articles. Join our Telegram channel
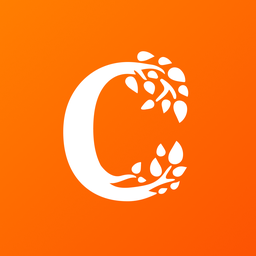
Full access? Get Clinical Tree
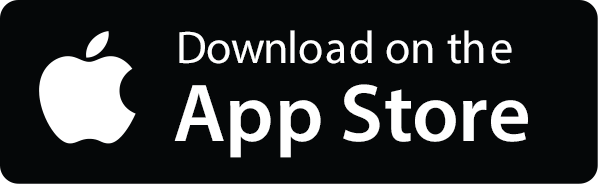
