Elapsed time (min)
% Mobile phase B
Flow rate (mL/min)
0
30
1.0
0.900
80
1.0
0.901
92
1.0
1.150
92
1.0
1.160
95
1.0
1.170
95
1.7
1.460
95
1.7
1.470
30
1.5
1.550
30
1.0
1.870
30
1.0
3.4.2 Mass Spectrometer Settings
Acquisition window
Start time: | 0.86 min | |
End time: | 1.23 min | |
Divert valve setting | Total time (min) | Position |
1 | 0.89 | B-Source |
2 | 1.20 | A-Waste |
Ionization—positive mode, APCI
Source parameters:
Collision gas | 6.00 |
Curtain gas | 35.00 |
Gas 1 | 60.00 |
Gas 2 | 60.00 |
Temperature | 300 |
Nebulizer current | 5.00 |
See Table 2—(MRM parameters)
Table 2
MRM parameters
Analyte | Q1 m/z | Q3 m/z | Dwell time (ms) | Purpose |
---|---|---|---|---|
25-Hydroxy vitamin D3 (-H2O) | 383.3 | 211.3 | 15 | D3 Quantifier |
25-Hydroxy vitamin D3 (-H2O) | 383.3 | 229.2 | 15 | D3 Qualifier |
25-Hydroxy vitamin D3-d6 (-H2O) | 389.3 | 211.3 | 15 | D3 Internal Standard |
25-Hydroxy vitamin D2 (-H2O) | 395.3 | 269.2 | 15 | D2 Quantifier |
25-Hydroxy vitamin D2 (-H2O) | 395.3 | 211.3 | 15 | D2 Qualifier |
25-Hydroxy vitamin D2-d3 (-H2O) | 398.3 | 272.3 | 15 | D2 Internal Standard |
3.5 Liquid Handler Volume Verification
Pipetting precision and accuracy for the liquid handlers was checked monthly using Orange G dye and a microplate reader [6]. Orange G was added to three different matrices: (a) pooled fresh serum, (b) 50:50 methanol:water, and (c) acetonitrile with 1 % (vol/vol) formic acid to verify pipetting performance for the serum, internal standard, and second precipitation reagent steps, respectively.
3.6 Preventative Maintenance Intervals
LC autosampler and pump preventative maintenance by the vendor (PM) was originally scheduled for once/year, but was eventually increased to four times/year. The stream select, loading, and divert valves did not have a scheduled PM; eventually a PM twice/year was scheduled. ALH PM was originally scheduled for twice/year, eventually increased to four times/year. MS/MS PM was scheduled for twice/year and no change was necessary.
4 Notes
1.
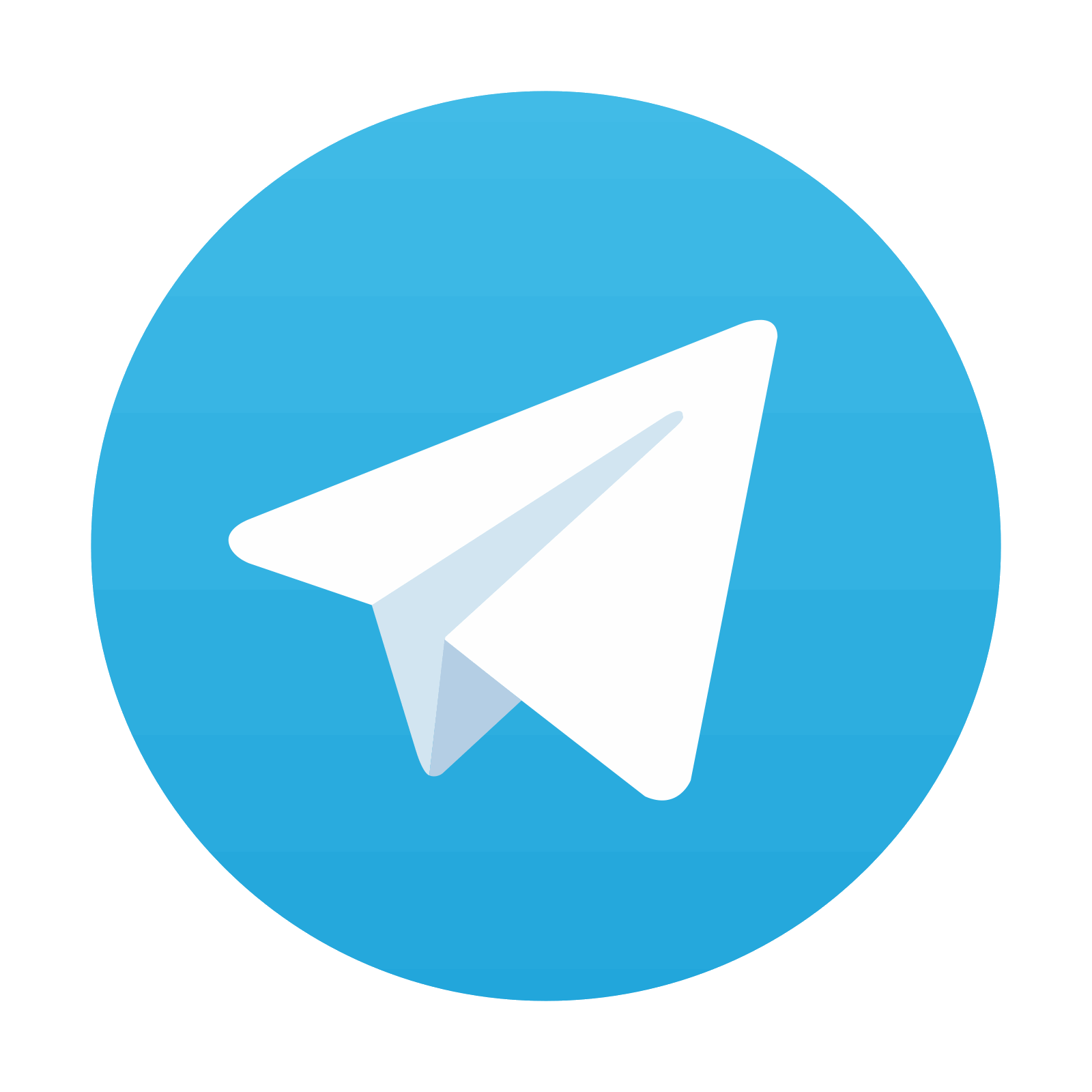
Methanol concentrations <50 % for the working internal standard matrix were associated with decreased internal standard recovery (lower peak areas) as compared to methanol concentrations between 50 and 100 %. The goal for the working internal standard matrix was to minimize precipitation of serum proteins when adding internal standard to serum and to reduce the evaporation rate from the internal standard container (residing on the ALH deck for several hours) by using the lowest feasible methanol concentration. To further minimize evaporation of the working internal standard during the 4–6 h necessary to process 10–15 plates, Hamilton Co. designed and manufactured a custom lid for the internal standard container that could be removed and replaced as needed by one of the 8 pipettor channels on the Hamilton STARlet model ALH.
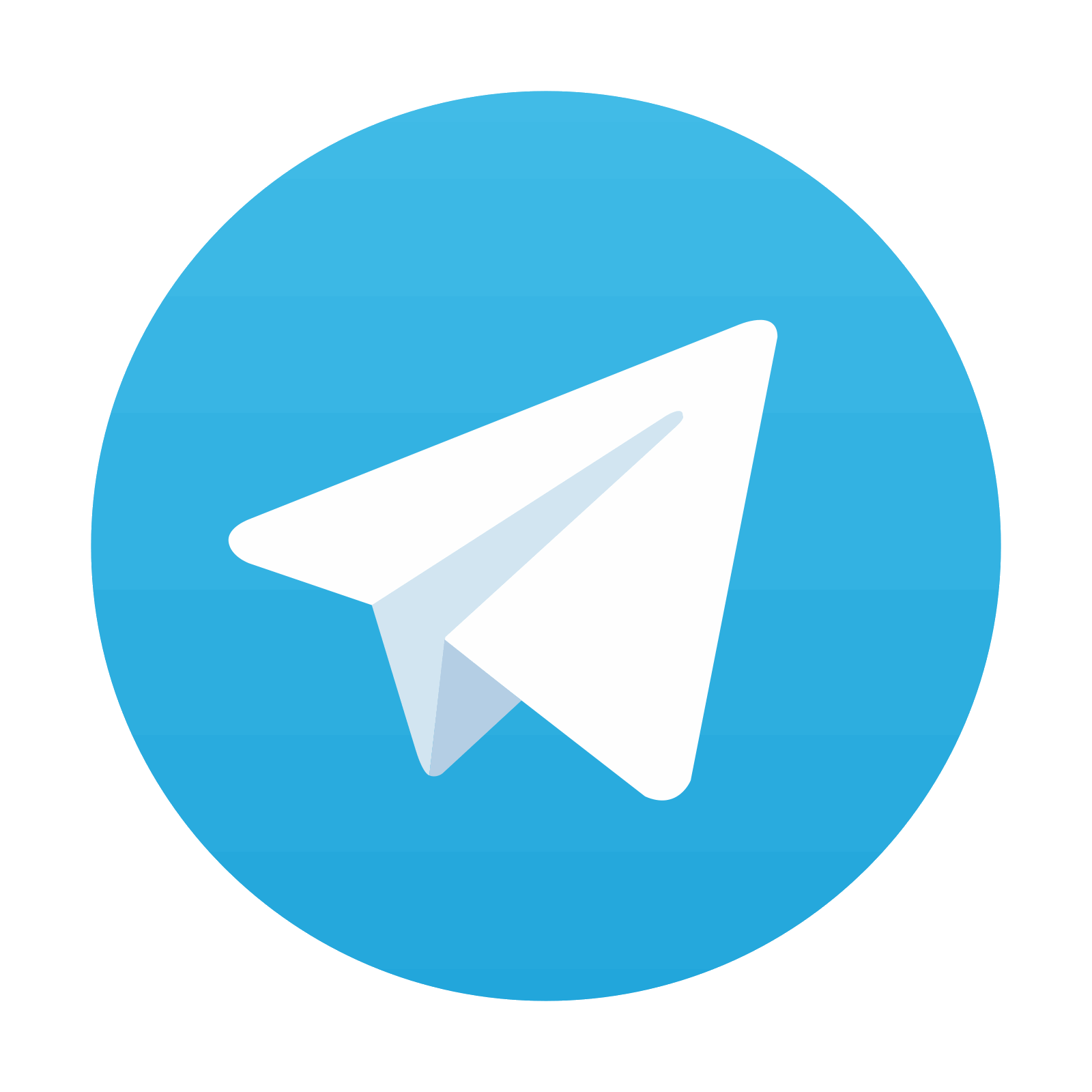
Stay updated, free articles. Join our Telegram channel
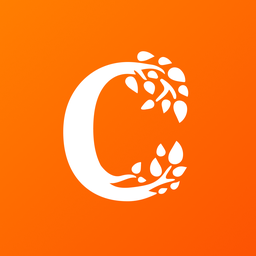
Full access? Get Clinical Tree
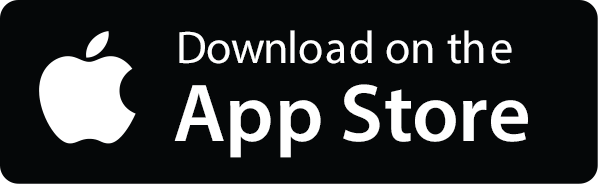

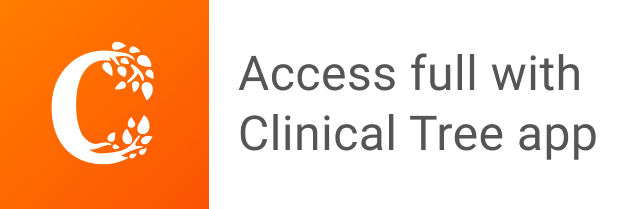