Hard capsules
Brian E. Jones
Chapter contents
Filling of powder formulations
Formulation for filling properties
Formulation for release of active ingredients
Formulation for position of release
Key points
• Hard capsules are a popular solid oral dosage form consisting of two pieces, a cap and body.
• Good patient compliance is achieved through the use of colour for identification, an easy to swallow shape and a shell that masks the taste of fill.
• Manufacture involves dipping metal mould pins into solution of polymers: films form on the mould surfaces, are dried, cut to length and two parts assembled.
• Traditionally hard capsules are made from gelatin and now also from hypromellose.
• They can be filled with formulations having a wide range of properties, from dry solids to non-aqueous liquids.
• Powder mixtures are the principal formulation type; involving a simple two-step manufacturing process, mix and fill.
• All filling machines, manual and automatic, use volumetric devices to measure the correct fill weight.
• Dosing of the powder is either ‘dependent’, using the capsule body to measure the powder, or ‘independent’ with the powder measured using a dosing mechanism, most frequently forming a soft plug of powder.
• The powder formulation objective is to produce stable mixtures of actives plus excipients with good flow and packing properties.
• Standard capsules release contents in the stomach. Release lower in the gastrointestinal tract is achieved by modifying the fill formulation or by coating the capsule.
Introduction
The word ‘capsule’ is derived from the Latin capsula, meaning a small box. In current English usage it is applied to many different objects, ranging from flowers to spacecraft. In pharmacy, the word is used to describe an edible package made from gelatin or other suitable material which is filled with medicines to produce a unit dosage, mainly for oral use. There are two types of capsule, ‘hard’ and ‘soft’; better adjectives would be ‘two-piece’ in place of ‘hard’ and ‘one-piece’ in place of ‘soft’. The hard capsule consists of two pieces in the form of cylinders closed at one end; the shorter piece, called the ‘cap’, fits over the open end of the longer piece, called the ‘body’. Soft capsules are discussed in Chapter 34.
Raw materials
Similar raw materials have been used in the manufacture of both types of capsule. Traditionally both contain gelatin, water, colourants and optional materials, such as process aids and preservatives; in addition, soft capsules contain various plasticizers, such as glycerin and sorbitol. The major pharmacopoeias (European, Japanese and US) permit the use of gelatin or other suitable material. Since late 1990s hard capsules have also been manufactured from hypromellose (hydroxypropy methylcellulose) in order to produce a shell with low moisture content.
Gelatin
Gelatin is still the major component used for capsules, and replacement polymer systems need to have the same basic properties. Gelatin possesses five basic properties that make it suitable for the manufacture of capsules:
1. It is non-toxic, widely used in foodstuffs, and is acceptable for use worldwide.
2. It is readily soluble in biological fluids at body temperature.
3. It is a good film-forming material, producing a strong flexible film. The wall thickness of a hard gelatin capsule is about 100 µm.
4. Solutions of high concentration, e.g. 40% w/v, are mobile at 50 °C. Other biological polymers, such as agar, are not.
5. A solution in water undergoes a reversible change from a sol to a gel at temperatures only a few degrees above ambient. This is in contrast to other films formed on dosage forms, where either volatile solvents or large quantities of heat are required to cause this change of state, e.g. tablet film coating. These types of film are formed by spraying and have a structure that could be described as formed of overlapping plates, whereas the gelatin films are homogeneous in structure, which gives them their strength.
Gelatin is a substance of natural origin that does not occur as such in nature. It is prepared by the hydrolysis of collagen, which is the main protein constituent of connective tissues (Jones R.T. 2004). Animal skins and bones are the raw materials used for the manufacture. There are two main types of gelatin: type A, which is produced by acid hydrolysis, and type B, which is produced by basic hydrolysis. The acid process takes about 7–10 days and is used mainly for porcine skins, because they require less pre-treatment than bones. The basic process takes about 10 times as long and is used mainly for bovine bones. The bones must first be decalcified by washing in acid to give a soft sponge-like material, called ossein, and calcium phosphates are produced as a by-product. The ossein is then soaked in lime pits for several weeks.
After hydrolysis, the gelatin is extracted from the treated material using hot water. The first extracts contain the gelatin with the highest physical properties, and as the temperature is raised, the quality falls. The resulting weak solution of gelatin is concentrated in a series of evaporators and then chilled to form a gel. This gel is then extruded to form strands, which are then dried in a fluidized-bed system. The dried material is graded and then blended to meet the various specifications required.
The properties of gelatin that are most important to capsule manufacturers are the Bloom strength and viscosity. The Bloom strength is a measure of gel rigidity. It is determined by preparing a standard gel (6.66% w/v) and maturing it at 10 °C. It is defined as the load in grams required to push a standard plunger 4 mm into the gel. The gelatin used in hard capsule manufacture is of a higher Bloom strength (200–250 g) than that used for soft capsules (150 g) because a more rigid film is required for the manufacturing process.
Many materials used in the manufacture of pharmaceuticals are manufactured from raw materials of bovine origin, e.g. stearates and gelatin. The outbreak of Bovine Spongiform Encephalopathy (BSE), which started in the UK, has led to strict rules being introduced by the EU to minimize the risks posed by animal Transmissible Spongiform Encephalopathy (TSE) agents. The European Pharmacopoeia has included a general chapter on minimizing the risk of transmitting TSE agents via medicinal products and guidance on products at risk. Manufacturers of relevant materials have to submit data to the European Department of the Quality of Medicines (EDQM) who will review it and issue a certificate of suitability for their product. This must then be submitted to the national regulatory authorities for medicinal products that contain these materials. The Scientific Steering Committee of the EU has collected data from many countries and has assigned to each a Geographical BSE Risk (GBR). There are four categories ranging from GBR I, which is a country in which BSE has never been detected and has in place a surveillance programme, e.g. New Zealand, to GBR IV which is a country in which the disease is prevalent, e.g. as was the case in the UK. Currently, gelatin for use in pharmaceuticals in the EU is sourced from bovine bones obtained from GBR I countries.
Colourants
The colourants that can be used are of two types: water-soluble dyes or insoluble pigments. To make a range of colours; dyes and pigments are mixed together as solutions or suspensions. The dyes used are mostly synthetic in origin and can be subdivided into the azo dyes (those that have an —NN— linkage) and the non-azo dyes, which come from a variety of chemical classes. Most dyes used currently are non-azo and the three most widely used are erythrosine (E127), indigo carmine (E132) and quinoline yellow (E104). Two types of pigment are used: black, red and yellow iron oxides (E172) and titanium dioxide (E171), which is white and is used to make the capsule opaque. The colourants that can be used to colour medicines are governed by legislation, which varies from country to country despite the fact that it is based on toxicological testing (Jones 1993). In the last 20 years there has been a move away from soluble dyes to pigments, particularly the iron oxides, because they are not absorbed on ingestion.
Process aids
The USNF describes the use of gelatin containing not more than 0.15% w/w of sodium lauryl sulfate for use in hard gelatin capsule manufacture. This functions as a wetting agent, to ensure that the lubricated metal moulds are uniformly covered when dipped into the gelatin solution.
Preservatives were formerly added to hard capsules as an in-process aid in order to prevent microbiological contamination during manufacture. Manufacturers operating their plants to GMP guidelines no longer use them. In the finished capsules, the moisture levels, 13–16% w/v, are such that the water activity will not support bacterial growth because the moisture is too strongly bound to the gelatin molecule.
Manufacture
The process in use today is the same as that described in the original patent of 1846. Metal moulds at room temperature are dipped into a hot gelatin solution which gels to form a film. This is dried, cut to length, removed from the moulds and the two parts are joined together. The difference today is that the operation is now fully automated, carried out as a continuous process on large machines housed in air-conditioned buildings. There is a limited number of specialist companies that manufacture empty capsule shells for supply to the pharmaceutical and health food industries, who fill them with their own products.
The first step in the process is the preparation of the raw materials. A concentrated solution of gelatin, 35–40%, is prepared using demineralized hot water, 60–70 °C, in jacketed pressure vessels. This is stirred until the gelatin has dissolved and then a vacuum is applied to remove any entrapped air bubbles. Aliquots of this solution are dispensed into suitable containers and the required amounts of dye solutions and pigment suspensions added. The viscosity is measured and adjusted to a target value by the addition of hot water. This latter parameter is used to control the thickness of capsule shells during production: the higher the viscosity, the thicker the shell wall produced. The prepared mixes are then transferred to a heated holding hopper on the manufacturing machine. Hypromellose solutions can be converted into a gelling system by the addition of a gelling agent, such as carrageenan, and a co-gelling agent, such as potassium chloride, and used to manufacture capsules on standard unmodified machines.
The manufacturing machines are approximately 10 m long, 2 m wide and 3 m high. They consist of two parts, which are mirror images of each other: on one half the capsule cap is made and on the other the capsule body. The machines are also divided into two levels, an upper and a lower. The moulds, commonly referred to as ‘pins’, are made of stainless steel and are mounted in sets on metal strips, called ‘bars’. There are approximately 50 000 mould pins per machine. The machines are housed in large rooms where the humidity and temperature are closely controlled.
The sequence of events in the manufacturing process is shown in Figure 33.1. At the front end of the machine is a hopper, called a ‘dip pan’ or ‘pot’. This holds a fixed quantity of gelatin at a constant temperature, between 45 and 55 °C. The level of solution is maintained automatically by a feed from the holding hopper. Capsules are formed by dipping sets of moulds, which are at room temperature, 22 °C, into this solution. A film is formed by gelling on the surface of each mould. The moulds are slowly withdrawn from the solution and then rotated during their transfer to the upper level of the machine, in order to form a film of uniform thickness. Groups of ‘pin bars’ are then passed through a series of drying kilns, in which large volumes of controlled humidity air are blown over them. When they reach the rear of the machine, the bars are transferred back to the lower level and pass through further drying kilns until they reach the front of the machine. Here, the dried films are removed from the moulds, cut to the correct length, the two parts joined together and the complete capsule delivered from the machine. The mould pins are then cleaned and lubricated for the start of the next cycle. Hypromellose solutions behave in a similar way to gelatin, except that the speed of gelling is slower and thus the machine output is reduced.
The machines are normally operated on a 24-hour basis, 7 days per week, stopping only for maintenance. The output per machine is over 1 million capsules per day, depending upon the size: the smaller the capsule, the higher the output.
The assembled capsules are not fully closed at this stage and are in a ‘prelocked’ position, which prevents them falling apart before they reach the filling machine. The capsules now pass through a series of sorting and checking processes, which can be either mechanical or electronic, to remove as many defective ones as possible. The quality levels are checked throughout the process using standard statistical sampling plans based on the Military Inspection Standards. If required, capsules can be printed at this stage. This is done using an offset gravure roll printing process using an edible ink based on shellac. The information printed is typically either the product name or strength, a company name or logo, or an identification code. The capsules are finally packed for shipment in moisture-proof liners, preferably heat-sealed aluminium foil bags, in cardboard cartons. In these containers they can be stored for long periods without deterioration in quality, provided they are not subjected to localized heating or sudden temperature changes that will affect their moisture content and dimensions.
Empty capsule properties
Empty gelatin capsules contain a significant amount of water that acts as a plasticizer for the film and is essential for their function. During industrial filling and packaging operations, they are subjected to mechanical handling and because the gelatin walls can flex, these forces can be absorbed without any adverse effect. The standard moisture content specification for hard gelatin capsules is between 13% and 16% w/w. This value can vary depending upon the conditions to which they are exposed: at low humidities they will lose moisture and become brittle, and at high humidities they will gain moisture and soften. The moisture content can be maintained within the correct specification by storing them in sealed containers at an even temperature. The standard moisture content for hypromellose capsules is 3% to 6% and when they lose moisture they do not become brittle.
Gelatin capsules are readily soluble in water at 37 °C. Their rate of dissolution decreases when the temperature falls below this. Below about 26 °C they are insoluble and simply absorb water, swell and distort. This is an important factor to take into account during disintegration and dissolution testing. Because of this, most pharmacopoeias have set a limit of 37±1 °C for the media for carrying out these tests. Capsules made from hypromellose have a different solubility profile, being soluble at temperatures as low as 10 °C (Chiwele et al 2000).
Capsule filling
Capsule sizes
Hard capsules are made in a range of sizes; the standard industrial ones in use today for human medicines range from size 0 to 4 (Table 33.1). To estimate the fill weight for a powder, the simplest way is to multiply the body volume by its tapped bulk density. The fill weight for liquids is calculated by multiplying the specific gravity of the liquid by the capsule body volume multiplied by 0.9.
Table 33.1
Capsule size and body fill volumes
Capsule size | Body volume (mL) |
0 | 0.69 |
1 | 0.50 |
2 | 0.37 |
3 | 0.28 |
4 | 0.20 |
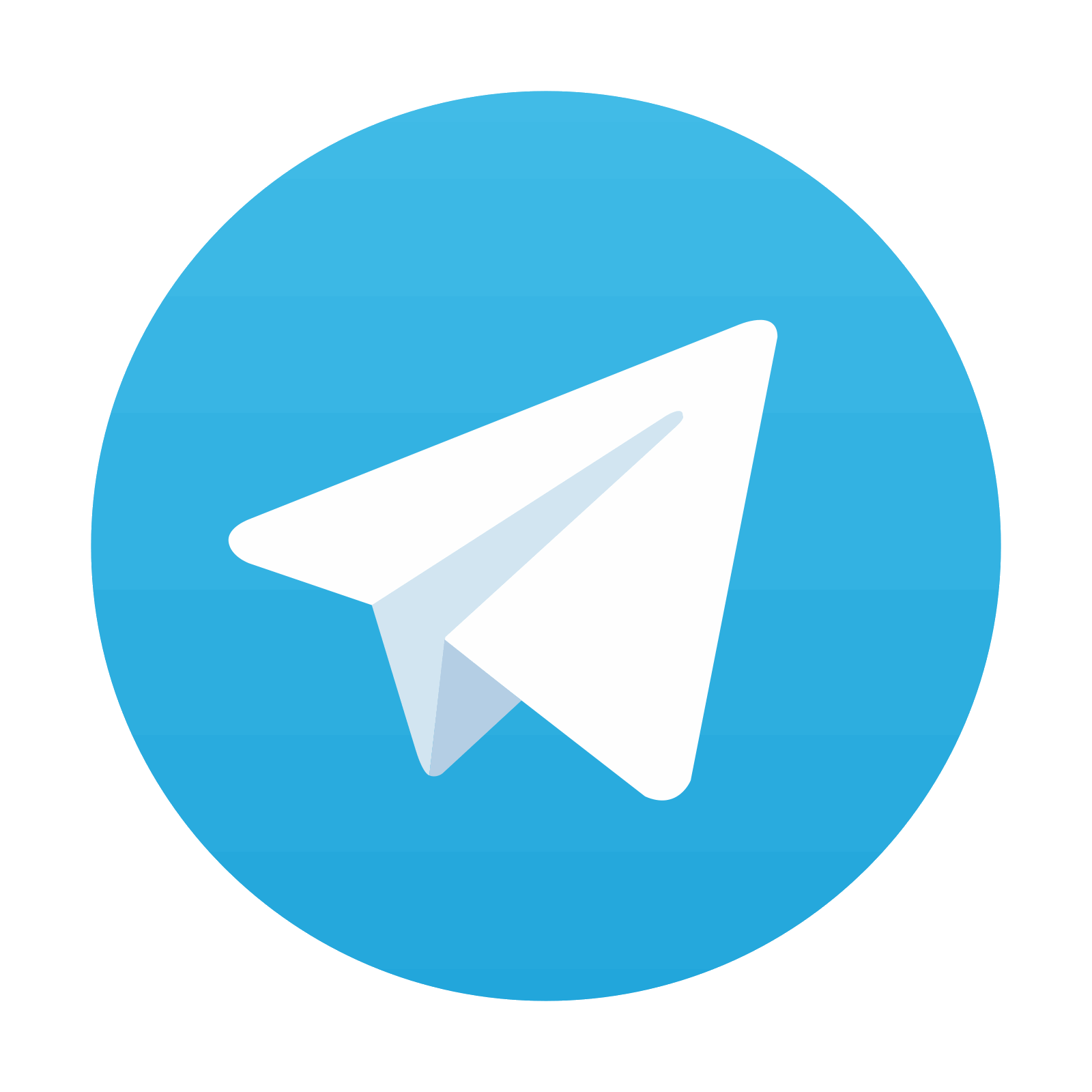
Stay updated, free articles. Join our Telegram channel
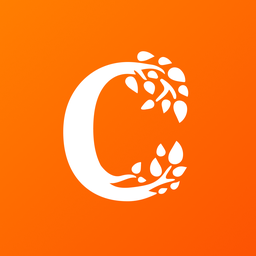
Full access? Get Clinical Tree
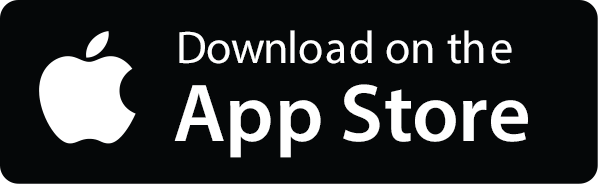
