Coating of tablets and multiparticulates
Stuart C. Porter
Chapter contents
Description of the film-coating process
Types of film-coating polymers: immediate-release coatings
Types of film-coating polymers: modified-release coatings
Ideal characteristics of film-coated products
Ideal characteristics of sugar-coated tablets
Description of the sugar-coating process
Description of the compression-coating process
Overview of coating of tablets
Mechanisms of drug release from multiparticulates
Processes for coating multiparticulates
Key points
Introduction
Coatings may be applied to a wide range of oral solid dosage forms, including tablets, capsules, multiparticulates and drug crystals. While tablets represent the class of dosage form that is most commonly coated, coated multiparticulates are also popular.
Definition of coating
Coating is a process by which an essentially dry, outer layer of coating material is applied to the surface of a dosage form in order to confer specific benefits that broadly range from facilitating product identification to modifying drug release from the dosage form.
Reasons for coating
The reasons for coating pharmaceutical oral solid dosage forms are quite varied. The more common reasons include (no order of importance implied):
Types of coating processes
Three main types of process are used in the pharmaceutical industry today:
Film coating is the most popular technique and virtually all new coated products introduced to the market are film coated. Film coating involves the deposition, usually by spraying a liquid coating system, of a thin film of a polymer-based formulation onto the surface of a tablet, capsule or multiparticulate core.
Sugar coating is a more traditional process closely resembling that used for coating confectionery products. It has been used in the pharmaceutical industry since the late 19th century. It involves the successive application of sucrose-based coating formulations, usually to tablet cores, in suitable coating equipment. The water evaporates from the syrup, leaving a thick sugar layer around each tablet. Sugar coats are often shiny and highly coloured.
Compression coating, although traditionally a less popular process, has gained increased interest in recent years as a means of creating specialized modified-release products. It involves the compaction of granular material around a preformed tablet core using specially designed tableting equipment. Compression coating is essentially a dry process.
Each of these processes will now be considered in turn and an overview of relevant coating processes and materials will be given.
Film coating
Film coating is the more contemporary and thus commonly used process for coating oral solid dosage forms. As described above, it involves the application of a thin film to the surface of a tablet, capsule or multiparticulate core. Now all newly launched coated products are film coated rather than sugar coated, often for many of the reasons given in Table 32.1.
Table 32.1
Major differences between sugar and film coating
Features | Sugar coating | Film coating |
Tablets | ||
Appearance | Rounded with high degree of polish | Retains contour of original core Usually not as shiny as sugar coat types |
Weight increase due to coating materials | 30–50% | 2–3% |
Logo or ‘breaklines’ | Not possible | Possible |
Other solid dosage forms | Coating possible but little industrial importance | Coating of multiparticulates very important in modified-release forms |
Process | ||
Stages | Multistage process | Usually single stage |
Typical batch coating time | 8 hours, but easily longer | 1.5–2 hours |
Functional coatings | Not usually possible apart from gastro-resistant (enteric) coating | Easily adaptable for controlled release |
Types of film coatings
Film coatings may be classified in a number of ways but it is common practice to do so in terms of the intended effect of the applied coating on drug release characteristics. Hence film coatings may be designated as either:
Immediate-release coatings are usually readily soluble in water, while gastro-resistant coatings are only soluble in water at pH values in excess of 5–6 and are intended to either protect the drug while the dosage form is in the stomach (in the case of acid-labile drugs) or prevent release of the drug in the stomach (in the case of drugs that are gastric irritants). More recently, gastro-resistant coatings have been employed as an integral part of colonic drug delivery systems (Alvarez-Fuentes et al 2004). For the most part, extended-release coatings are insoluble in water. They are designed to ensure that the drug is released in a consistent manner over a relatively long period of time (typically 6–12 hours) and thus reduce the number of doses that a patient needs to take in each 24-hour period. Additionally, extended-release film coatings are used to modify drug release in such a way that desired therapeutic benefits can more easily be achieved and thus drug efficacy improved.
Description of the film-coating process
Film coating involves the application of liquid, polymer-based formulations to the surface of the tablets (for the sake of brevity, the term ‘tablet’ will be used here to represent any form of dosage unit that is to be coated). It is possible to use conventional panning equipment but more usually specialized equipment is employed to take advantage of the fast coating times and high degree of automation possible.
The coating liquid (solution or suspension) contains a polymer in a suitable liquid medium, together with other ingredients such as pigments and plasticizers. This solution is sprayed on to a rotating, or fluidized, mass of tablets. The drying conditions employed in the process result in the removal of the solvent, leaving a thin deposit of coating material around each tablet core.
Process equipment
The vast majority of film-coated tablets are produced by a process which involves the atomization (spraying) of the coating solution or suspension on to the surface of tablets.
Modern pan-coating equipment is of the side-vented type (as shown in Fig. 32.1) and some typical examples include:
• Accela Cota – Thomas Engineering (USA)
• Premier Coater – Bosch-Manesty (UK)
• Hi-Coater – Freund-Vector (Japan and USA)
• Driacoater – Driam Metallprodukt GmbH (Germany)
Manufacturers of units that operate on a fluidized-bed principle include:
Depending on the particular film-coating application involved, fluidized-bed equipment may be further divided into one of the three operating principles shown in Figure 32.2.
The coating formulation is invariably added as a solution or suspension via a spray gun. The design and operation of film-coating spray guns are similar in both perforated-pan and fluidized-bed coaters, although differences in the performance of spray guns provided by different vendors, especially in perforated-pan processes, have been noted (Macleod & Fell 2002). A typical example of spray coating in a pan coater is shown in Figure 32.3.
Basic process requirements for film coating
The fundamental requirements of a film-coating process are more or less independent of the actual type of equipment being used and include:
Film-coating formulations
Currently, the majority of film-coating processes involve the application of a coating liquid where a significant proportion of the main component (the solvent/vehicle) is removed by means of a drying process that is concurrent with the application of that coating liquid. Film-coating formulations typically comprise:
There are certain types of coating process that differ from this common approach. For example, some processes involve the application of hot-melt coatings that congeal on cooling (Jozwiakowski et al 1990), while others take advantage of recent developments in powder application technologies (Porter 1999).
It should be mentioned that all ingredients used in film-coating formulations must comply with the relevant regulatory and pharmacopoeial requirements current in the intended marketing area.
Film-coating polymers
The ideal characteristics of a film-coating polymer are discussed below.
Solubility
Polymer solubility is important for two reasons:
Film coatings that are used on immediate-release products should utilize polymers that have good solubility in aqueous fluids to facilitate the rapid dissolution of the active ingredient from the finished dosage form following ingestion. Such coatings are usually applied as solutions in an appropriate solvent system (with a strong preference being shown for water). However, film coatings used to modify the rate or onset of drug release from the dosage form tend to have limited or no solubility in aqueous media; such coatings are usually applied either as polymer solutions in organic solvents or as aqueous polymer dispersions (discussed later in this chapter).
Viscosity
Viscosity is very much a limiting factor with regard to the ease with which a film coating can be applied. High viscosity (typically that exceeding about 500 mPa s) complicates transfer of the coating liquid from the storage vessel to the spray guns, and subsequent atomization of that coating liquid into fine droplets. Ideally, therefore, polymers applied as solutions in a selected solvent should exhibit relatively low viscosities at the preferred concentration. This will help to facilitate easy, trouble-free spray application of the coating solution, especially in production-scale film-coating equipment.
Permeability
Appropriate permeability (to which the chosen polymer makes a significant contribution) is a key attribute when considering the various functional properties that film coatings are expected to possess. For example, coating permeability is of significant importance when the film coating is intended to:
• mask the unpleasant taste of the active ingredient in the dosage form
• modify the rate at which the active ingredient will be released from the dosage form.
These properties vary widely between the various polymers that might be considered for film-coating formulations.
Mechanical properties
In order to perform effectively for the purpose intended, a film coating must exist as a discrete, continuous coating around the surface of the product to be coated, and must be free from defects typically caused by the stresses to which the coating is likely to be exposed during the coating process, during packaging and during the subsequent distribution of the final product.
Consequently, film-coating polymers should possess suitable characteristics with respect to:
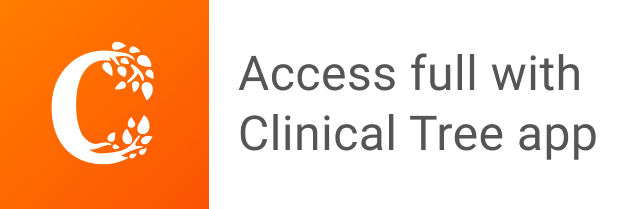