Fig. 29.1
Schematic representation of accuracy and precision. (a) High accuracy and high precision, good balance in repeatability; (b) High accuracy and low precision, measured values are wide-spread; (c) Low accuracy and high precision, good balance in repeatability; (d) Low accuracy and low precision, measured values are wide-spread. From Radwag [7] with permission
29.1.1.2 Required Accuracy and Precision
In relation to preparation in the pharmacy, weighing is used in the preparation process and in Quality Control. Firstly measurement uncertainty is dealt with in relation to Quality Control.
For Quality Control purposes the required measurement uncertainty is set by the Official Medicines Control Laboratories (OMCL) Network of the Council of Europe. The measurement uncertainty for analytical weighing is considered to be satisfactory if three times the standard deviation of not less than ten replicate weight measurements, divided by the amount weighed (at approximately 50 % of the maximum capacity of the balance), does not exceed 0.001 [8]. For comparison: USP gives a requirement for weighing tolerance (based on the requirement for repeatability as the most determining uncertainty at small weights) for “materials that must be accurately weighed” [9] which is 0.1 % for two times the relative standard deviation of 10 times weighing a test weight.
For the preparation process, no official requirement is known to the authors, so it has to be derived. Most preparation processes start with accurately weighing the required amount of active substance(s) and excipients or with measuring them by volume. Several process steps, such as transferring or mixing, may cause loss of active substance or excipients due to spillage, exhausting, adsorption. Usually this leads to a deviation of the actual content from the required content. It depends on the type of processing and the properties of the involved active substances and excipients, whether the resulting mean content will be lower or higher than 100 %. Especially in small-scale preparation any small process imperfection may lead to a noticeable deviation in content, which is acknowledged by the somewhat less rigid requirements to mean content of pharmacy preparations compared to licensed medicines. Taking this into account, one may argue that weighing and volume measuring should negligibly contribute to these deviations because it is relatively easy, especially for weighing, to perform these process steps accurately and precisely. Due to the small obtainable uncertainty in weighing and measuring, other processes can use up the ‘uncertainty budget’ [9]. It immediately follows however that they should not be executed so accurately and precisely that it hampers an efficient performance of the preparation process.
Although uncertainty in weighing and measuring can be small, it is worth knowing ‘how small’ for purposes of:
Using the right balance and the right volume measuring device;
Knowing the minimum weight (Mmin) that can be weighed on that balance and the minimum amount to be measured with the volume measuring device.
Mean content of pharmacy preparations is required to be between 90 % and 110 % (see Sect. 32.6). If one would reckon with instability during storage and the need to have a feasible shelf life, further narrowing this to 95–105 % for the mean content immediately after preparation is reasonable (see Sect. 22.4.1). This can be interpreted as there being an uncertainty range of maximal 5 % for weighing and measuring. However it may be more reasonable to leave some room for other processes contributing to the deviation of the mean content.
A maximum deviation of 5 % from the mean content would lead to a maximum allowed weighing uncertainty of 0.018, expressed as most probable standard deviation. To obtain this value all four components contributing to uncertainty (see next section) are taken into account. This requires specific mathematics and reasoning, which are explained in [10]. The value of 0.018 results from a recalculation with a 5 % deviation of the mean content instead of the original 7 % allowed. To leave some room for other processes, to be memorable and to give a clear comparison to analytical weighing a true standard deviation σ of 0.01 could be proposed. As said, OMCL requires 0.001 for analytical weighing. For comparison with the requirements for the mean content it should be realised that this standard deviation (sd) corresponds with a relative standard deviation (rsd) of 1 % at the minimum amount to be weight Mmin. This standard deviation of 1 % corresponds subsequently to most measurements being within 2–3 times that sd from the mean, so to a maximum deviation of 2–3 %. This deviation rapidly decreases with weighing larger quantities: to 1–1.5 % at weighing of two times the Mmin and so on. How to assess the Minimum weight in practice is further derived in Sect. 29.1.3.3.
Maximal measurement uncertainty at volume measurements could be calculated as well. However volume measurements are generally only performed as second choice if weighing would pose too many drawbacks for the reliability of the preparation process (see Sect. 29.1.2). Therefore, the acceptable measurement uncertainty for volume measuring depends strongly on the nature of the process in question. Usually only inaccuracy is taken into consideration. It is limited by requiring a minimum filling of the device to be used, as is explained in Sect. 29.1.7. More exact calculations would be irrelevant.
29.1.2 Weighing versus Volume Measuring
The measurement uncertainty of weighing will usually lead to a deviation due to inaccuracy and imprecision of not more than 1 % [10]. Volume measurements however, may show a deviation of 1.5 % under the most favourable conditions. Under less favourable conditions this can easily rise to 3 % or more (see Sect. 29.1.7).
Weighing has three advantages over volume measuring:
Greater accuracy and precision to be achieved so smaller quantities can be handled.
The read-out of a weight is less subjective than of a volume.
The use of an electronic balance offers the possibility to record the result of a weighing objectively, by connecting to a printer or a computer programme (in-process control).
Viscous liquids can be accurately weighed but are difficult to be measured on a volume basis. Consider, for example, Chlorhexidine Digluconate Solution (Ph. Eur.), which is a rather viscous solution. In an investigation of chlorhexidine containing preparations, prepared in Dutch pharmacies, it was shown that chlorhexidine solution measured by volume often resulted in too low concentrations of this ingredient. This was caused by the adherence of the solution onto the measuring device. For instance, the average content of a chlorhexidine mouth wash (Table 29.1) in samples prepared by volume measuring was 3 % lower than in those prepared by weighing. This formula of Chlorhexidine mouth wash was then redesigned so as to give the weight of the required amount of chlorhexidine solution instead of the volume.
FNA | |
---|---|
Chlorhexidine digluconate solution | 10.65 g |
Ethanol (96 % V/V) | 70 g |
Peppermint oil | 3 dr |
Sorbitol liquid, crystallising | 535 g |
Water, purified | 493 g |
Total | 1109 g (= 1000 mL) |
For some steps of the preparation processes, however, weighing is not or hardly possible or volume measurement has advantages for reasons that outweigh inaccuracy. Examples include: the adjustment to volume of large amounts of solutions, working in a laminar flow cabinet, and preparing parenterals prior to administration on the ward.
If a preparation is carried out in a small working space with conditioned airflow (laminar flow cabinet, safety cabinet, isolator), a balance cannot be too big and must be protected to weigh free from draft. Those balances are suitable to weigh ingredients but not to determine the final weight of a preparation, for instance a measuring cylinder with eye drop solution. The final step will therefore be filling up to volume and not to weight.
If a large vessel (e.g. 50–100 L) is used for a preparation process, this may be carried out on a volume basis. In that case the volume is determined using a calibrated vessel with volume marks or by using a calibrated rod. Newly bought vessels are equipped with load cells (transducers that convert force into an electrical signal) so that weighing can be performed.
The nurse who prepares parenterals prior to administration to a patient sometimes only needs a small part of an injection solution from an ampoule or has to take the appropriate amount from the ampoule for further dilution to achieve the appropriate dose. She will take out the desired volume from the ampoule with a syringe and probably use other syringes for further dilution (see also Sect. 29.1.7).
In pharmacy preparation, volume and weight of liquids sometimes have to be converted into each other through the relative density.
Syrups do not contain active ingredients. They are not administered as such but serve as a vehicle because of their flavouring and sweetening properties. Since the density of syrups is high, the volume in mL will not equal the weight in grams. Syrup BP contains 667 g sucrose and purified water to produce 1,000 g. The density is 1.315–1.333 g/mL, yielding a sucrose concentration of about 64.6 %.
Benzalkonium chloride is available as Benzalkonium Chloride Solution (Ph. Eur.) which contains a mixture of alkylbenzyldimethylammonium chlorides in water at a concentration of 500 g/L (50 % w/v). If the final concentration of benzalkonium chloride in a product has to be 0.01 % (either w/v or w/w), for 1,000 mL of the preparation 100 mg of benzalkonium chloride is required. Volume measuring would require 0.2 mL of the Benzalkonium Chloride Solution (50 % w/v) to be taken which cannot be performed with adequate accuracy because of its high viscosity. For weighing instead, the density of the solution has to be known. Density may be taken from the product certificate issued by the manufacturer or it has to be measured. If the density would be 0.9805 g/mL (as measured) one should weigh 196 mg of the 50 % Benzalkonium Chloride Solution for 1,000 mL of the solution to be prepared.
If minor amounts are to be used of an excipient, such as an essence or an essential oil in liquid oral preparations, the required weight should be known as well, regardless of the fact that a limited variation in quantity has no essential influence on product quality. A pharmacist can convert the weight into droplets if such small quantities of the product are prepared that weighing is not practical. In such cases the required quantity on a preparation worksheet can be stated in droplets instead of weight.
Other examples from practice are the preservation of eye drops and the addition of a vitamin solution.
The combination of benzalkonium chloride and betaphenylethanol in final concentrations of 0.05 g/L and 4 g/L, respectively, is sometimes used to preserve eye drops (but with care and restrictions as betaphenylethanol often causes irritation). In that case, for the preparation of 10 mL of 0.5 % Atropine sulfate eye drops, 0.5 mg of benzalkonium chloride and 40 mg of betaphenylethanol are required. The preservatives can be added to the prepared solution by droplets as follows: the amount of 40 mg of betaphenylethanol corresponds to two drops of this liquid preservative; benzalkonium chloride is used as a 0.5 % stock solution: five drops (100 mg of the stock solution) are needed.
An oily concentrate of vitamin A contains 1,000,000 IU/g of the active substance, corresponding to 34,500 IU in one drop. If 25 g of an ointment should contain 120,000 IU, it means that four drops of the concentrate should be added. If better precision is required the concentrate should be diluted with an appropriate oil and added to the ointment by weight.
In the case of the preservation of eye drops this may be an acceptable approach especially because it may decrease the number of process steps in aseptic handling, although using a sterile stock solution with accurately weighted substances is definitely to be preferred. For active ingredients such as vitamin A, for which a content of 90–110 % is required, it may result in the final product not meeting the requirements.
29.1.3 Physical Principles of Weighing
For weighing in the pharmacy a balance is used. Two types of balances exist: electronic (principle: comparison of force) and mechanical (principle: comparison of mass). Most balances in European pharmacies are electronic balances.
29.1.3.1 Electronic Balance
The principle of an electronic balance is electromagnetic force compensation: the force of the mass to be weighed is compared with an electromagnetic force. The electronic balance has a magnet, a coil and a load carrier that is mechanically connected to the coil. Under the influence of load on the load carrier the coil drops into the magnet and the current through the coil must be amplified to reach the starting position (equilibrium) again (see Fig. 29.2).


Fig. 29.2
Principle of a balance with electromagnetic force compensation. The structure is based on a lever. Typically, the weighing pan with the item to be weighed is attached to one end of the lever. A coil that generates an electromagnetic force is attached to the other end of the lever. Source: Recepteerkunde 2009, ©KNMP
Two types of electronic balances exist. For the first, the difference in current between the loaded and unloaded state is a measure for the weight, the working of the second is based on electrical resistance.
Most electronic balances are provided with an adjustable integration time and stability indicator (that releases the weighing result). These functions decrease the influence of draft and vibrations on the weighing result. The integration time is the duration of the measurement cycle of the balance, and the result of the measurement is read out when the balance indicates ‘standstill’. This is indicated by means of a signal lamp or the passing on of the read-out result to a printer. A longer integration time may occur if the weighing is disturbed by draft and vibrations.
29.1.3.2 Mechanical Beam (Equal Arm) Balance
The principle of a mechanical balance is based on comparison of mass. The mechanical beam balance may be present in the pharmacy as a back-up. The equal arm balance is three-knife yoke balance (see Fig. 29.3). The object to be weighed is placed on one scale and it is brought into balance with different calibrated weights on the other scale.
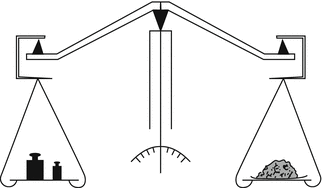
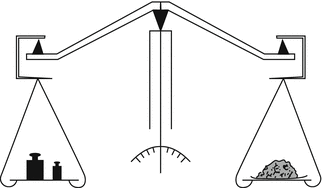
Fig. 29.3
Principle of a mechanical beam balance. Source: Recepteerkunde 2009, ©KNMP
Before use, levelling and zero position should be checked. Levelling can be set using the adjusting screws. If the scales are clean but the pointer does not indicate zero in the unloaded state, the balance should undergo service. Such deviation should never be abrogated with the adjusting screws or by pieces of paper put on the weighing scales.
After use, the weighing scales should be cleaned when necessary. Maintenance consists of cleaning the knives, the pans and the loose weights and checking whether parts that are worn by the (mechanical) use should be replaced. The set of weights, when used regularly, should be recalibrated regularly, depending on applicable national laws. If the balance is used for emergencies only, it is recommended that the weights be sealed after recalibration and stored under dry conditions to avoid corrosion occurring.
When using a beam balance the extent of any deviation is not known. At the end of the weighing the pointer should be positioned exactly in the middle of the scale. If this is not the case, the extent of the deviation is unclear.
29.1.3.3 Weighing Uncertainty at Preparation
To obtain the allowed weighing uncertainty the contribution of all components that are related to the weighing at preparation have to be summed up. Four components are contributing to weighing uncertainty [10]:
1.
Intrinsic inaccuracy and imprecision of the balance
2.
Imprecision due to the imperfect placement of the balance in practice
3.
A difference between the value at which the weighing is read out and the quantity to be weighed according to the preparation worksheet
4.
Reading out before the balance has stabilised sufficiently
The intrinsic inaccuracy and imprecision of an electronic balance will be given by the manufacturer’s balance specifications, see further Sect. 29.1.4.
To keep inaccuracy and imprecision of a balance to their intrinsic (or ideal) values, a balance should be placed completely free from disturbances. However in pharmacy preparation imperfect placing is the rule. By using a stability indicator the additional imprecision due to imperfect placement can be restricted but it is generally acknowledged that the additional imprecision due to imperfect placement has to be monitored (see Sect. 29.1.6).
The third deviation is caused by the fact that the weighed out quantity never exactly equals the quantity that should be weighed according to the preparation worksheet. It is therefore important to determine what deviation is allowable. For instance, weighing out to meet exactly the target amount will take a lot of time. With a maximum deviation of 1 % from the target amount, weighing in small-scale preparation can be executed conveniently. Setting this deviation is also necessary for programming the stability control for accepting the weighing result and releasing it for the printer.
The fourth deviation is usually an operator’s deviation; impatience may lead to reading out before the balance has stabilised sufficiently. If the balance is connected to a printer, this impatience will be to no effect as the printer will only accept results between ± 1 % (or any other set value). If impatience occurs the reason for it should be checked as it may be due to technical problems (see also Sect. 29.1.5). If the balance is not connected to a printer the operator has to calculate the maximum allowed deviation of the result from the target amount. It is safer, however, to express it in the number of decimal figures in the amount on the preparation worksheet. If, for instance, the amount to be weighed is specified as 7.0 g, the weighing can be stopped when the weighing result lies between 6.95 and 7.05 g. Within that range the deviation from the quantity to be weighed will be less than 1 %. If a deviation of less than 0.5 % is desirable, the target amount in the protocol should be specified as: 7.00 g. For example, ‘1.00 kg’ implicates that a larger deviation is permitted than for ‘1,000 g’ (5 g and 0.5 g respectively). Thus, the number of decimals places has a practical meaning [12].
The BP describes the accuracy requirements as follows: Quantities are weighed or measured with an accuracy commensurate with the indicated degree of precision. For weighings, the precision corresponds to plus or minus 5 units after the last figure stated (for example, 0.25 g is to be interpreted as 0.245 g to 0.255 g). For the measurement of volumes, if the figure after the decimal point is a zero or ends in a zero (for example, 10.0 mL or 0.50 mL).
To find out if the total influence of these deviations on the mean content is still within the set amount of 5 %, all deviations have to be accumulated. Weighing deviations may compensate for each other so straightforward totalling limit values will reflect an extremely worst case. Combining deviations that have a different mathematical type is essentially an addition of quadratic standard deviations (variances), but only after limit values have been turned into standard deviations according to their specific statistical distribution. This propagation (or accumulation) of uncertainties is elaborated in Sect. 5 and Annex E.4 of [4] and applied to small-scale preparation in [10].
Intrinsic measurement uncertainty, as has been said (Sect. 29.1.1), can be differentiated in inaccuracy and imprecision. The intrinsic inaccuracy of an electronic balance is caused by deviations from sensitivity, linearity and eccentricity. Sensitivity is defined as the change in weighing value divided by the change in load, usually measured between zero and the capacity of a balance. Linearity is the ability of a balance to follow the linear relationship between a load and the indicated weighing value. Eccentricity is the deviation in the measurement value caused by eccentric loading (asymmetrical placement of the load). Figure 29.4 illustrates these uncertainties.
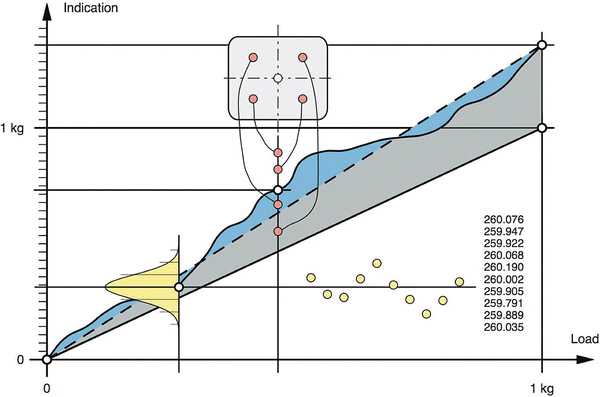
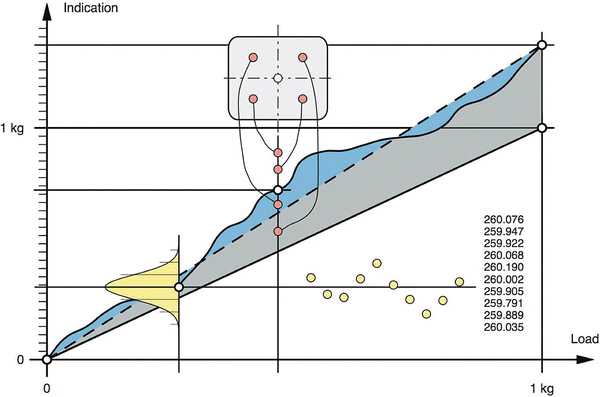
Fig. 29.4
Properties of weighing instruments: The dashed line with the associated grey area represents the sensitivity offset of the instrument, superimposed is the nonlinearity (blue area, indicating the deviation of the characteristic curve from the straight line). The red circles represent the measurement values caused by eccentric loading, and the yellow circles represent the distribution of the measurement values due to repeatability, from Mettler-Toledo [13] with permission
Intrinsic imprecision is also called repeatability and is usually determined included in total repeatability. Intrinsic measurement inaccuracy is checked by calibration.
For analytical balances and microbalances the contribution of the components to measurement uncertainty are very different. For the lower weighing range, repeatability is by far the most important. For precision balances and industrial scales, this is less prominent. But testing frequencies (see Sect. 29.1.6) are, via risk assessment, for these balances are largely determined by checking repeatability and sensitivity.
29.1.4 Selection of an Electronic Balance
29.1.4.1 General Selection Criteria
The relevant classes of balances for pharmaceutical purposes are: semi-micro-balances, analytical balances, precision balances and platform or industrial balances [14]. They are categorised by their capacity and readability (Table 29.2):
Table 29.2
Categorisation of balances for pharmaceutical purposes
Type | (typical) Capacity | (typical) Readability | Remarks |
---|---|---|---|
Semi-micro | 30 g | 0.001 mg or 0.002 mg | With an enclosed draft shield |
For quantitative analysis in the laboratory only | |||
Analytical | 500 g | 0.1 mg or 0.01 mg | With an enclosed draft shield |
For small-scale preparation and for quantitative analysis | |||
Precision (or top pan) | 20 kg | 0.001 g or greater | For production, and for general weighing in the laboratory |
Platform | 1,000 kg | 0.1 g or greater | For industrial production |
The selection of a balance may be determined by:
Weighing range
Required precision and accuracy
Metrological approval of the model
The shape and area of the weighing pan
The area and height of the weighing chamber, e.g. are containers to be weighed on the balance
The power supply required, e.g. 115 V, 240 V or battery powered
All balance types for pharmacy preparation preferably have an automatic internal calibration option and can operate in connection with software functions, e.g. for in-process control. The balance should be equipped with a stability indicator so that the weight is only registered or printed after stabilisation of the balance. Draft shields are important, especially for weighing in controlled (ventilated!) environments. Special functions such as piece counting (for counting tablets or capsules; the so-called ‘pill counter’) may be advantageous.
29.1.4.2 Metrological Approval
For pharmacies (as opposed to industries) it is legally required [1] to use balances under metrological control of the model. So when buying a balance, it should be verified if the model can be supplied under metrological control.
The manufacturer produces the instrument in accordance with the product specification. The CE marking and the supplementary metrology marking are affixed by, or under the responsibility of, the manufacturer onto the instrument during the fabrication process as proof of conformity with the EU directives. The manufacturer must have had such a metrological control carried out by one of the competent authorities of the Member States of the European Union, called a notified body. Details are described in [1, 15]. Balances used in pharmacies are defined as ‘non-automatic weighing instruments’ according to the European law, meaning that they require the intervention of an operator during weighing [1, 15].
Measuring instruments subject to metrological control undergo metrological inspections by the competent authorities: a notified body. The specific requirements have been entered in the regulations.
The EU directive distinguishes four accuracy classes for balances: I (special), II (high), III (medium) and IIII (ordinary). The balances used in pharmacies’ practice usually belong to the accuracy classes I and II. In the pharmaceutical industry (for large-scale preparations) also technical balances (platform balances) of class III may be used [1].
The accuracy classes are characterised by their corresponding measurement uncertainties, expressed in specific parameters:
The verification scale interval “e”, representing the operational deviation limit in the lower parts of the weighing range.
The actual scale interval “d” (readability, the smallest digit that can be read out from the display).
The minimum capacity “Min”, the metrological lower limit of the weighing range.
The maximum weighing capacity “Max”, being the upper limit of the weighing range. Weighing of a quantity exceeding the maximum weighing capacity may damage the balance.
A typical e-value for an analytical balance (accuracy class I) is 0.001 g, indicating an operational inaccuracy limit of ± 0.001 g in the lower part of the weighing range. For less sensitive precision balance (accuracy class II) a typical e-value is 0.1 g.
The measurement uncertainty these parameters are applying to is the ‘intrinsic’ one: based on an ideal, disturbance-free placement of the balance. Ideal placement may be attained in a laboratory situation but usually not in a pharmacy production environment. For selection of the appropriate balance these parameters may be helpful, although there is not much advantage above the usual categorisation as is reflected in Table 29.2.
But measurement uncertainty in practice has to be checked by investigating the actual repeatability leading to a Minimum weight Mmin in practical circumstances, as opposed to the metrological minimum capacity ‘Min’ (see Sect. 29.1.5).
29.1.5 Installation and Minimum Weight
29.1.5.1 Installation
In order to work under optimal conditions a balance should stand stable, preferably in a weighing room or on a weighing bench, on a solid, level, nonmagnetic surface that minimises the transmission of vibration. A balance should be shielded from big changes in airflow or draft (laminar flow, air exhaust, radiator, open door or window, passage area) and temperature (direct sunlight, radiator). Humidity must be constant, preferably between 40 and 60 % RH. A low humidity will increase the effect of static electricity. The positioning should be free from electromagnetic fields, static electricity (due other equipment) and vibrations, e.g. by construction work or traffic passing [9, 16].
Prior to installation and release for use, it is recommended to check all the requirements set during the selection of the instrument. Secondly a full calibration (involving sensitivity, linearity, eccentricity and repeatability over the entire operation range of the balance) should be performed before putting into service. This is done at the location where the balance is used [9].
A balance should be adjusted for each location where it is used. Weight varies slightly according to latitude, altitude, temperature and pressure. A measuring instrument must therefore be adjusted for the particular part of the country (gravitational area) where it will be used. In a small country like the Netherlands, eight gravitational areas are distinguished. When moving to another part of the country or the world, a balance may enter into a different gravitational area and requires re-adjustment. By using an internal calibration this adjustment is not necessary.
Finally, the minimum weight in practical circumstances Mmin should be assessed.
29.1.5.2 Concept of Minimum Weight
The Minimum weight Mmin describes the lower limit of the balance below which the required weighing tolerance (accuracy) is not adhered to [9]. Or put differently: one has to weigh at least this amount of material in order to meet a limit of uncertainty that satisfies the weighing accuracy requirements specific to the process involved [12]. The Minimum weight Mmin is specific for the process for which the weighing is used. Mmin is to be distinguished from the metrological Min = Minimum capacity (see Sect. 29.1.4), which is a technical specification of the balance itself.
With regard to Quality Control the Mmin can be derived from the allowed measurement uncertainty given by OMCL or USP.
USP uses the following equation for the minimum weight [9]:
Mmin = (k × s)/required weighing tolerance; k being a ‘coverage factor’ and s being the standard deviation of 10 weighings.
Using 0.10 % as the weighing tolerance for materials that have to be accurately weighed (see Sect. 29.1.1) the equation amounts to: Mmin = 2,000 × s. Note that repeatability is taken as the measure for uncertainty. This is allowed at low loads as repeatability is dominating the contributions of non-linearity, sensitivity or eccentricity [9].
For preparation processes, the required weighing uncertainty was derived in Sect. 29.1.1 and expressed as a maximum standard deviation γw of 0.018. Via γw = σw/Mmin and σw = 1.59sw (n = 10) this leads to a Mmin of about 100 × s; s being the standard deviation of 10 replicate measurements of a practical and relevant load. For an approach that leaves more room for other processes contributing to deviation from the mean content, as said (Sect. 29.1.1), γw of 0.01 could be used. This would result in a Mmin of about 150 × s.
As a conclusion, Mmin for preparation purposes is to be determined by performing 10 replicate weighings of a practical, relevant object such as usual receivers: a mortar, a flask, a paper with a large surface. After calculating the standard deviation s10, multiplication by a factor 100 − 150 will lead to the Mmin


However, theoretically Mmin should never be less than about 80 × d, d being the scale interval, see Sect. 29.1.1. Due to rounding of the digital indication, the lower limit smin of the standard deviation of a weighing is calculated as being 0.41 × d for technical reasons [13]). This fact of a lower limit of s, is also taken into account in [17]. It will lead in the case of preparation to a minimal Mmin of about 80 × d.
An alternative approach could be that the Mmin is determined by an experienced operator and multiplied by a safety factor of 2 (or even a higher number) to account for all future variations [13].
29.1.6 Operation and Maintenance
29.1.6.1 Operation of a Balance for Pharmacy Preparation
A clean balance that is in a completely level position should be used. In all cases the balance chosen should be appropriate for the quantity to be weighed and for the accuracy needed.
The first step is to switch on a balance. Depending on the type of balance a warming-up period should be taken into account. The balance should reach thermal equilibrium after being connected with the power supply. If the balance is in the standby mode (which is generally recommended when a balance is used regularly) the electronics are still energised and no warming-up period is necessary.
It should be checked to see if the balance is levelled. If this is not the case, the balance should be aligned using the adjustable feet while monitoring the level indicator. It should be checked that the balance displays exactly zero at the start of each weighing (stability indicator, Sect. 29.1.3.1). The balance can then be tared.
The allowed difference between the quantity to be weighed and the actual weighed quantity, for instance 1 % (see Sect. 29.1.3.3), can be incorporated into a weighing programme. It may also be indicated in the worksheet by the number of decimals of the quantity to be weighed (see Sect. 29.1.3.3).
Strong (electro) magnetic fields and static electricity may disrupt the operation of an electronic balance. For example, Plexiglas draft shields, protective plastic covers or plastic weighing trays can be charged to such an extent that it influences the weighing result. In that case there is a large fluctuation of the figures that indicate the weighing result, especially when moving the charged object above the weighing scale. Avoid weighing vessels made of plastic when atmospheric humidity is below 30–40 %. The risk of electrostatic charges is greater under these conditions. This leads to inaccurate weighing results.
A deviation may be caused by the presence of a stir bar in the vessel into which the weighing is done. Therefore, a stir bar should preferably be removed from the vessel before weighing. If any deviation is remaining despite sensible actions, consultation of the supplier is necessary to be able to undertake the proper corrective action.
Temperature is one of the most important factors of a weighing process. For balances equipped with an automatic adjustment system, the balance precision restoring process is carried out automatically, with consideration of temperature as time changes. However, this concerns only temperature of the environment. One must not weigh hot or very cold objects on the balance. Hot objects will give erroneously low readings due to buoyancy of hot air, while cold objects will give high readings. Therefore, after removing the weighing vessel from a drying oven or dishwasher, allow time to cool before placing it on the balance. Analogously products taken out of the refrigerator should adjust to room temperature before they can be properly weighed.
A beaker taken from a water bath should be dried on the bottom before it can be placed on a balance scale.
Weighing vessels must be put in the centre of the weighing pan to prevent influence of eccentricity.
Finally, health and safety precautions at weighing procedures generally brings with it the wearing of gloves as a measure that is easy and good practice for all materials, but especially for the toxic ones (see Sect. 26.4.3). Because usually powdered substances are weighed, decreasing the exposure by inhalation is relevant. The use of an exhaust at the back of the balance is preferred, but expensive. The use of a safety cabinet or isolator could even be necessary. As an alternative in specific situations qualified nose-mouth masks or respirators can be worn. The best measure to decrease exposure is to use fluid or semisolid triturations of the active substance instead of the powder form (see Sect. 29.5).
29.1.6.2 Utensils for Weighing
For weighing out ingredients, a range of paper sheets, vessels and containers, spatulas and spoons are available. All receivers must be clean, dry and inert. The total weight of the receiver plus the substance to be weighed must not exceed the maximum capacity of the balance. If the repeatability and hence the Mmin has been determined (see Sect. 29.1.5.2) with the usual, probably large, receivers (as is recommended), small quantities can be weighed from Mmin, if necessary also in those receivers.
The choice of the receiver is mostly determined by the ease for the preparation process concerned. Solids are often weighed on (paraffin) paper or in the processing vessel itself. Weighing polystyrene boats, antistatic weighing canoes or greaseproof paper are used as receivers as well. After transferring the solid from a weighing paper, hardly visible residues may still remain. By re-weighing the receiver and residuals the loss can be controlled to an acceptable level. The actual quantity added can also be determined through weighing the original container before and after the extraction. By weighing directly into the preparation vessel no loss occurs through transfer. Small amounts of powder can eventually be weighed on filler substance, but this harbours the risk that an excess cannot be removed in the case that too much of the substance is weighed. It is a matter of skills and experience.
Semisolids are weighed on greaseproof paper or cellophane. To prevent loss, a small amount of a substance can be weighed on a bit of the ointment base into which it will be incorporated (see above).
Compatibility with the receiver should be checked especially with fluids. Spatulas and spoons made of stainless steel may interact with substances such as chloral hydrate or iodine. But for the short contact time involved in the weighing procedure these interactions don’t appear to be relevant. Plastic spatulas may cause a problem with electrostatic charge. Also with some substances discolouration of the plastic occurs so disposable spoons are increasingly used.
For liquids that are best weighed droplet-wise, vials with a drop dispenser (dropper) are suitable. By varying the position of the vial, the droplet size can be easily adjusted.
An accurate weighing of volatile solvents or solutions (alcohol, ether, methylene chloride) is still an unsolved problem. Evaporation occurs and the readings change constantly showing decreasing weight. The read-out of the weight should be performed only if the vial is closed.
29.1.6.3 Maintenance
Balances should be protected from damage, cleaned with great care and checked periodically. The weighing chamber and weighing pan should be kept clean (using conventional window-cleaning fluids, lint-free cloths), only clean weighing vessels should be used, contaminants should not be brushed into potential openings and all removable parts should be removed before cleaning.
All balances should be regularly calibrated and monitored for their performance. The applicable frequency of such tests should be based on risk assessment: the higher the impact of deviations, the more often testing should take place. Calibration is to be performed by the user either manually (with an external calibration weight) or using the internal calibration.
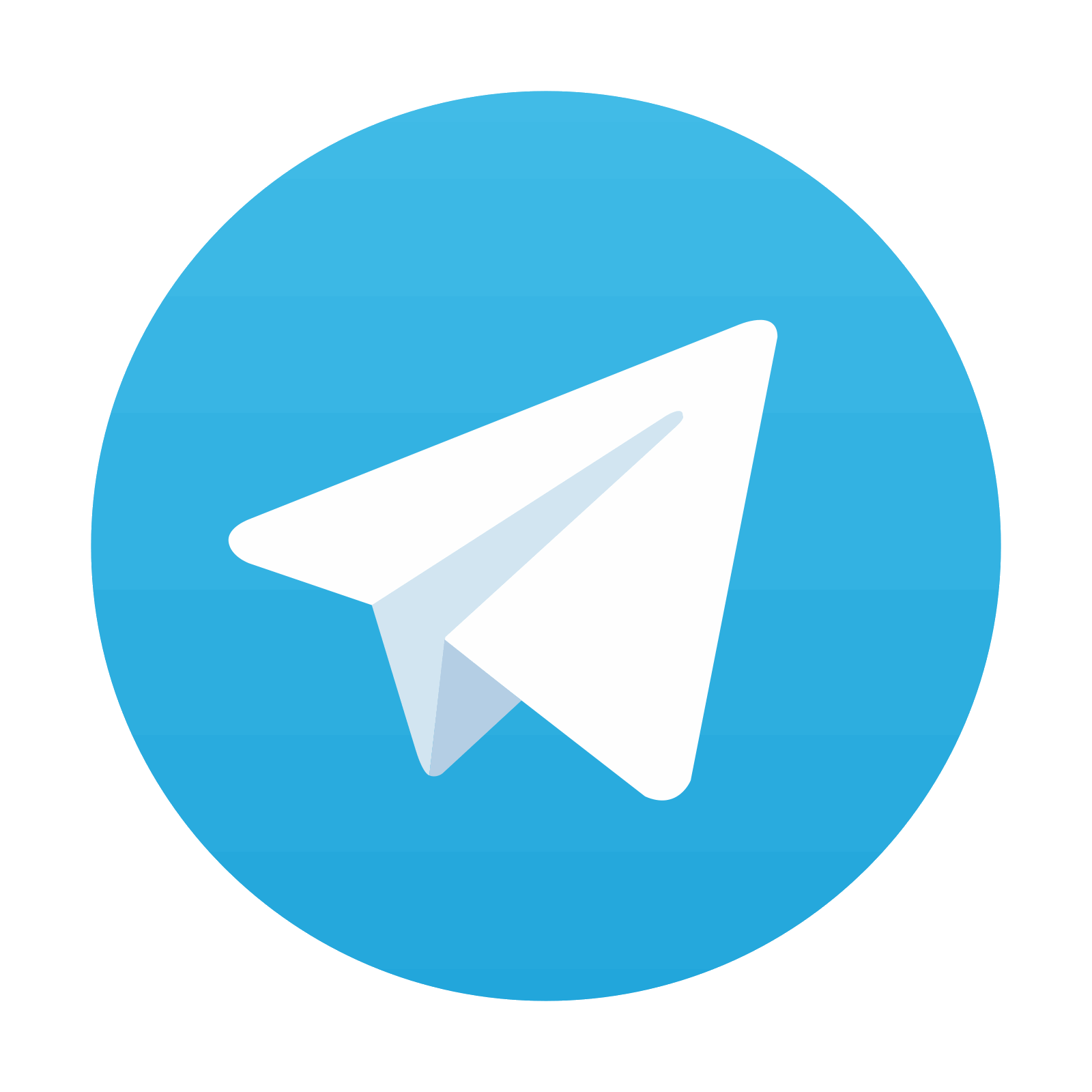
Stay updated, free articles. Join our Telegram channel
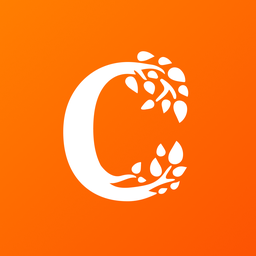
Full access? Get Clinical Tree
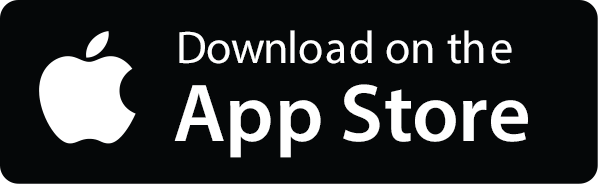
