A. OVERVIEW
1. Important Mechanical Properties
The underlying theme of this chapter is the relationship between solid-state structure and mechanical properties. To understand this relationship, it is necessary to be clear about the meaning of several key terms.
Toughness is perhaps the most important property that an engineering material can possess. It is the ability to resist breaking when struck by a sharp blow. An excellent example of a tough material is a rubber tire. When hit by a hammer, a tire deforms slightly, absorbs the energy of the impact into molecular motion and heat, and then rebounds to the original shape. In this example toughness is closely associated with elasticity and with the laminated construction of the tire (more about this later). Another form of toughness is malleability, which is the property shown by many metals to change shape without breaking when hammered or forced through a die.
Brittleness is the opposite of toughness. A sharp impact causes a brittle material to shatter into many pieces. A piece of window glass is an obvious example. However, the failure of metal components in bearings, automobile or jet engines, or bridges can often be attributed to embrittlement that often develops long after the component has been installed. Solids derived from small molecules are also frequently brittle.
Strength in a material is the ability to resist deformation or cold flow. Stone, concrete, and brick are used in building construction because they can withstand enormous pressure without buckling. Unfortunately, strength may be accompanied by brittleness, so that a strong material that withstands considerable static force may shatter on impact. Think of the effect of a sledgehammer on a concrete block or a housebrick.
Thus, materials design often revolves around attempts to maximize toughness and/or strength and minimize brittleness. These attempts may involve two distinct approaches. In the first, a solid is manipulated by heating, cooling, or percussion to change its microstructure. This is a method much used for metals and their alloys. In the second approach, two different materials are combined to generate a heterogeneous solid (a composite material) in which the useful properties of one component are combined with the advantageous properties of the other. These two approaches to materials design and optimization are discussed in the following sections. Some of the options are summarized in Figure 9.1.
2. Homogeneous versus Heterogeneous Solids
There are several different reasons for the widespread interest in alloys and composites: (1) they provide a means for combining the preferred properties of two or more different materials, while at the same time minimizing their defects; (2) it is sometimes easier to generate a desired combination of properties by mixing two materials together than by synthesizing an entirely new substance with the required combination of properties built in at the molecular level; and (3) if the combination of two different materials leads to phase separation, the possibility exists that the combined material will be stronger than the two constituents alone because one component will reinforce the other and prevent the propagation of cracks and other defects.
With respect to the last factor, an ever-present possibility in the formation of mixed materials is the inability of different metals, ceramics, or polymers to form homogeneous mixtures in the solid state. Phase separation is common, and this means that the properties of the final mixture may not be a simple linear combination of the properties of the constituents. However, as discussed, below, phase separation may provide some advantages not found in a homogeneous system. The difference between homogeneous and phase-separated materials is not always distinct. As the following discussion reveals, some materials that appear to be homogeneous at the macrolevel may in fact be heterogeneous on the micro- or nanoscale.
3. Different Types of Composite Materials
Toughness, strength, and brittleness can be controlled by several different techniques, one of which is the incorporation of two or more different materials into the same solid. Thus, some of the most useful solids, especially those used as structural materials, are mixtures of two or more different substances. The constituents of such mixtures are the types of substances discussed in the preceding chapters on polymers, ceramics, and metals. These mixtures can assume several different forms that range from homogeneous solutions of one element or compound in another (alloys), through crystallites suspended in an amorphous glassy matrix, to solids in which two different components or two different parts of the same polymer molecule segregate into separate domains. Many modern composites consist of whiskers or fibers embedded in a matrix of another material. Other type of composites takes the form of laminates in which layers of different materials, for example, a woven cloth and a crosslinked polymer, are brought together to form multilayer assemblies. The scheme shown in Figure 9.1 sketches some of the possibilities.
4. Defects in Solids
Most solids have strengths that are far less than the values calculated on the basis of chemical bond energies or the sum of all the ionic or van der Waals interactions. In a uniform solid, such as a diamond, failure or shattering of a crystal requires the breaking of millions of C—C covalent bonds—a process that would require an abnormal amount of energy. Yet diamonds can be cleaved fairly easily.
This discrepancy is due to the fact that solid materials frequently “fail” because of the presence of defects. By “defects,” we mean discontinuities in the structure that favor crack propagation when pressure or an impact is applied. Three types of defects are particularly important:
1. The existence of slip planes in a regular, three-dimensional structure can result in crack propagation. These are the planes that can be drawn between sheets of spherical atoms or molecules in even the most perfect crystalline solids (Figure 9.2). Slippage along these planes provides a natural mechanism for the shape of the solid to change under the influence of pressure. Slip planes can be very useful because they provide a means for a metal to deform slowly under pressure—a property that underlies ductility.
2. If the solid consists of two different, incompatible components segregated into microdomains, crack propagation may occur along interfaces between the two components (Figure 9.3). Thus, in a heterophase solid the strength depends on the cohesion between different domains, which can be either chemical or mechanical. Mechanical strength may arise when the domains are locked together physically by shape, even if the chemical affinity of the two surfaces is low. If the domains do slide past each other when pressure is applied, then the material will fail, sometimes suddenly. This concept applies to metal alloys where one phase has crystallized inside another.
3. Crack propagation can be arrested if a spreading defect encounters a separate domain that anchors the two sides of the crack together (Figure 9.4). That second domain may be in the form of crystallites embedded in a polymeric or inorganic glass, or it could be micrometer- or nanometer-sized domains of rubbery polymer embedded in a glassy matrix. The rubbery material absorbs the energy that would otherwise continue to tear the material apart, and converts that energy into harmless molecular motion. The crack-stopping phase can also be a rigid material such as carbon or ceramic powder or a fibrous material such as glass fiber or carbon fiber. Such additives are collectively known as “fillers.” Ideally, a good filler should form a strong adhesive bond to the matrix material.
4. Defects at the surface of a solid may also have an important influence on strength. Even a homogeneous solid, such as an inorganic or polymeric glass, will shatter on impact more easily if scratches exist at the surface. These defects serve as sites for the concentration of stress and impact energy and they initiate cracks, which then propagate rapidly through the solid (Figure 9.5). Thus, an obvious way to strengthen a glass is to ensure that the surface is free from imperfections. This may be accomplished by “flame polishing” to melt the outer surface.
Figure 9.4. Propagation of a crack through a material can be stopped by the presence of a second phase, which can be either an elastomeric domain that absorbs the impact energy or a nonflexible material or crystal that is embedded in the glassy matrix.

B. PURE MATERIALS AND HOMOGENEOUS SOLID SOLUTIONS
1. Slip Planes, Dislocations, and Grain Boundaries in Metals
Slip planes are an inherent characteristic of metals, even those that have a relatively homogeneous structure. The nature of slip planes is illustrated in Figure 9.2. Different crystal structures give rise to different numbers of slip planes. For example, copper, silver, and gold have cubic close-packed (face-centered cubic) crystal structures, which generate many slip planes. Slip planes are important because the binding forces that hold successive layers of metal atoms together are weak (assuming that covalent bonds are absent), and it requires relatively little force to induce planes of atoms to slide past each other. As mentioned above, this process is the basis of ductility. If a metallic crystal structure that has many slip planes is stretched or bent, the material will deform without shattering as the whole structure readjusts to the new shape by movement along the slip planes. This can be compared to the manner in which geologic forces are relieved by slippage along a geologic fault, except that in a metal it may not occur so abruptly. This property underlies the processes of extrusion of wires and tubes, and fabrication process that depend on metal bending. However, this behavior may be detrimental to the strength of the material under extreme pressure or tension. For example, suspension bridges built entirely from copper might not retain their viability for as long as those constructed from steel or aluminum alloy.
Figure 9.5. Crack formation is facilitated if scratches or other indentations exist at the surface. These sites act as the focus of impact energy, triggering the separation of grain or domain boundaries and even facilitating the cleavage of covalent bonds.

However, the existence of slip planes does not by itself explain the ease with which metal lattices can be deformed or cleaved. Another reason is connected with the fact that crystal lattices are seldom perfect, and the packing of spheres frequently yields discontinuities that result from the random absence of atoms where they should be. This is illustrated in Figure 9.6.
These discontinuities, called dislocations, provide a physical pathway for a facile reorganization of the lattice when slow pressure is applied. The existence of dislocations may be the result of errors in the atomic deposition sequence when the crystalline regions are growing from the melt.
Another feature of a pure metal is the existence of grain boundaries (Figure 9.7), which reflect the existence of different crystallites growing simultaneously in the molten metal. When these crystals meet as the metal solidifies completely, the different crystalline domains are mismatched at the boundary in terms of the atomic arrangements. Individual crystallites are physically locked in position with their neighbors. The presence of interlocking crystalline domains can increase both strength and hardness, and possibly brittleness as well. Ductility is correspondingly reduced. The size of the crystallites is important. Many small grains (crystals) provide multiple pathways for crack propagation along grain boundaries and low stress resistance. Fewer, large interlocked grains will give the maximum strength and impact resistance. This type of structure can be induced by “cold-rolling” sheets of the metal, a process that also orients the grains along one axis.
Figure 9.6. (a) Defects in a crystal lattice caused by the absence of an atom, which causes a reorganization of the nearby atoms and the presence of a dislocation. (b) Dislocations may also be generated by the presence of a larger atom that disrupts the local packing arrangement.

Figure 9.7. (a) Schematic representation of grain boundaries that arise from mismatch between the crystal structures of adjacent domains. The parallel lines represent crystal planes. (b) Optical micrograph of grain boundaries in a metal such as titanium.

From a practical viewpoint, impact- or temperature-induced stress applied selectively to the surface of a metal can harden the surface (“case hardening”) without destroying the ductility or impact resistance of the sub-surface material. Moreover, dislocations may be eased out of a metal by heating to just below the melting point, a process known as annealing, which allows the internal structure to reorganize and reduces the number of dislocation sites. On the other hand, rapid cooling of a hot metal may harden the surface of a material by generating many interlocked small crystalline regions. This is what happens when a blacksmith hammers an iron horseshoe into shape at red heat, and then plunges it into a bath of cold water. Modern engineering practice also requires that this “quenching” process is carried out routinely on metal components.
Discontinuities may also arise from stresses (impact, stretching, or bending) applied to the metal after it has cooled below its melting point. They are responsible for the failure of metals by “metal fatigue,” a process in which repeated bending or stressing of a metal leads to catastrophic failure.
Impurities in a metal also have a profound effect on strength and ductility. The presence of small amounts of impurity atoms, especially those with atomic radii that are markedly different from the host material, will cause discontinuities and dislocations, and this could bring about an increase in brittleness. On the other hand, larger amounts of a second element may lower the melting point by disrupting the overall crystal structure.
Note that the imperfections described here also emerge at the surface of metals and their alloys, features that, together with “steps” and “ledges,” play an important role in catalysis (see Chapter 15).
2. Homogeneous Metallic Alloys
Metallic alloys were mentioned briefly in Chapter 8, and much of the foregoing comments in this chapter apply to metallic alloys as well as to other materials. Metal alloys are produced by melting the components together and cooling. The speed of cooling often determines the properties of the final material. A characteristic of a true alloy is that the different atoms are distributed uniformly throughout the volume of the solid rather than occurring as separate domains or phases. However, this is composition-dependent, and phase separation often occurs beyond some concentration limits. Typical alloys are those formed by small amounts of carbon in iron (steel); iron, chromium, and nickel in stainless steel; silver and mercury in dental “silver amalgam”; copper and gold in jewelry; and copper, gold, and nickel in coins. A key requirement for the formation of a homogeneous mixture of metals is that the atomic radii of the participating metals should be similar, so that one type of metal atom can replace another in the solid without serious disruption of the crystal structure. However, if a second metal has a larger atomic radius, it will create discontinuities at the slip planes and prevent movement along those planes. Hence the alloy will become harder.
3. Polymer Alloys—Blends
Homogeneous mixtures of two or more different polymers are important because they, too, provide a method for combining the diverse properties of two different materials, especially when the attributes of one compensate for the deficiencies of the other. These materials are also known as polymer blends. One advantage of homogeneous polymer alloys is that the properties of the blend change in a predictable way with the ratio of the two constituents. Alloys of macromolecules may be produced by dissolving two or more different polymers in an organic liquid, followed by evaporation of the solvent. Alternatively, the two molten polymers can be mixed mechanically, and the mixture cooled. As with metals, the final morphology may depend on the speed of cooling and the subsequent thermal history.
Tentative evidence that the product is a homogeneous blend is its transparent appearance. This means that segregation into two phases has not occurred (there is no light scattering from separate domains with different refractive indices). By contrast, if the solid mixture is opaque, this suggests that phase separation has occurred. A fairly common situation is the initial formation of a homogeneous, transparent material, which slowly becomes opaque over time as a result of phase separation. Transmission and scanning electron microscopy (Chapter 4) are tools that are widely used to probe the morphology of polymer alloys.
In addition, the detection of only one glass transition temperature (by DSC analysis) intermediate between those of the two constituent polymers is evidence for the existence of compatible mixtures. Whether this homogeneity persists at the nanostructure or molecular level is a matter for debate.
Some scientists believe that true homogeneous alloys of two or more polymers may not exist. Nevertheless, many examples exist of mixtures of two different polymers that appear to be homogeneous at the level of optical microscopy or even scanning electron microscopy. For two polymers to be miscible, the free energy of mixing must be less than zero. This can be accomplished in one of three ways: (1) the entropy of mixing should be high, (2) the enthalpy of mixing should be negative, or (3) there should be some favorable balance between these two factors. If the two polymers are both high-molecular-weight species, the entropy of mixing will be relatively small, because the two separated polymers will already be in a highly disordered state and have little to gain by mixing with another polymer. Thus, unless there is a strong interaction between the two polymers that lowers the enthalpy, they will be incompatible. A significant decrease in enthalpy can occur if the two polymers have complementary functional groups. For example, homogeneous mixture may be formed if one polymer bears OH, COOH, or NH2 groups that can form hydrogen bonds with the oxygen or nitrogen atoms in the second polymer.
An alternative way to improve the compatibility of two different macromolecules is to add a polymer compatibilizer, which is another polymeric component that interacts well with the two main constituents. An example is the use of a block copolymer of polyisobutylene and poly(dimethylsiloxane) to convert heterogeneous mixtures of the two highly incompatible polymers to a homogeneous polymer blend. Presumably the two components in the compatibilizer associate with their counter-parts in the individual polymers to lower the enthalpy of the final elastomer.
4. Interpenetrating Polymer Networks
An important type of polymer alloy is an interpenetrating polymer network (IPN) (Figure 9.8).
Figure 9.8. Schematic representation of (a) a partial and (b) a full interpenetrating polymer network (IPN). The partial IPN consists of an uncrosslinked polymer that permeates the crosslinked matrix of a second macromolecule. In a full IPN, both polymers are crosslinked within the matrix of each other.

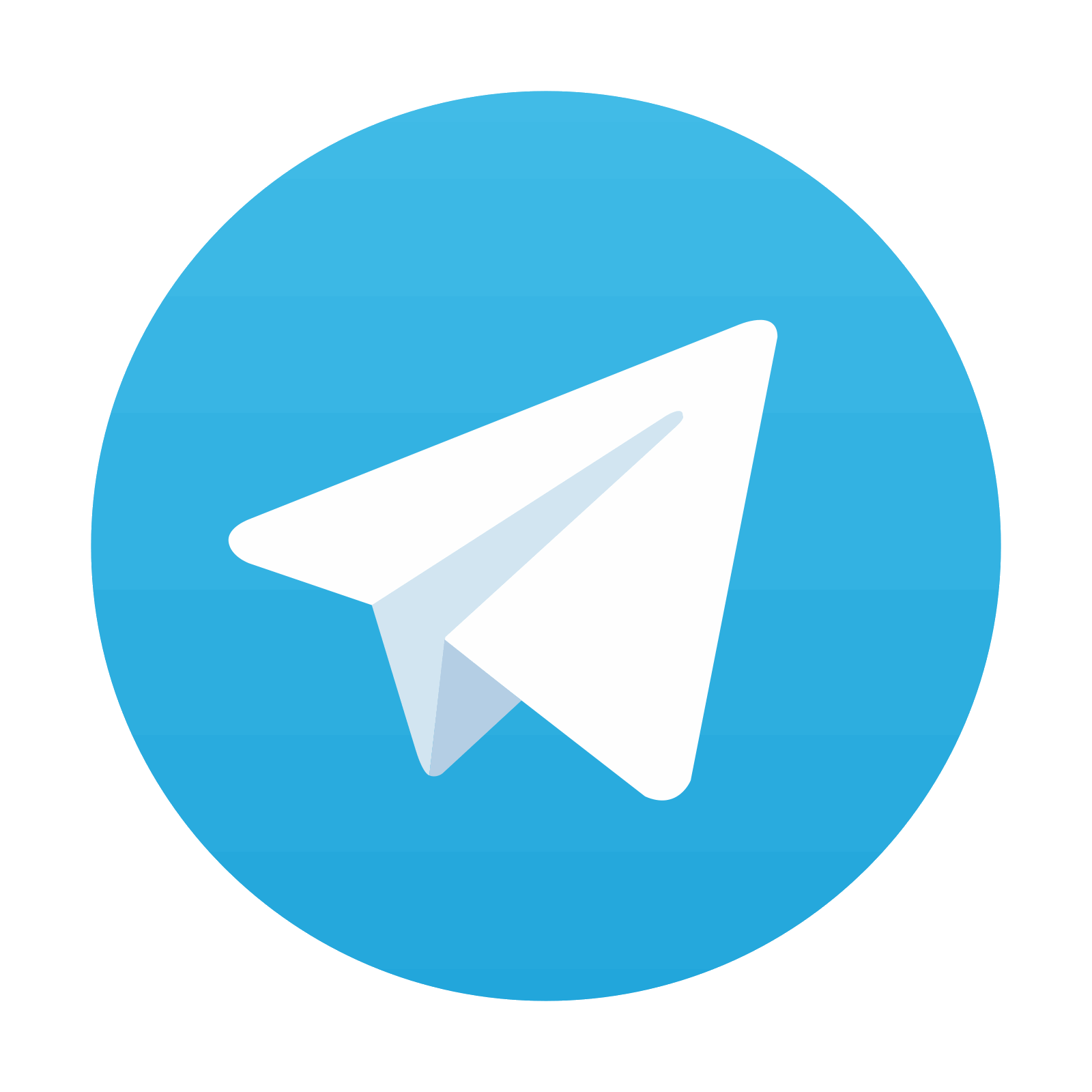
Stay updated, free articles. Join our Telegram channel
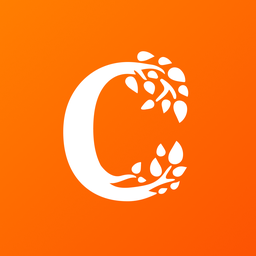
Full access? Get Clinical Tree
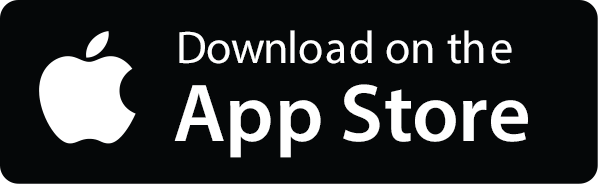
