OUTLINE
Desired Properties of a Liquid Emulsion
Compounding Basic Emulsion Types
Compatibility, Stability, and Beyond-Use Dating
Special Labeling Requirements for Emulsions
I. DEFINITIONS
A. Emulsions: “Emulsions are two-phase systems in which one liquid is dispersed throughout another liquid in the form of small droplets” (1).
1. All emulsions for oral administration are liquids, but emulsions for topical administration may be either liquid or semisolid. This chapter covers liquid emulsions; semisolid emulsions are discussed in Chapter 30, Semisolids: Ointments, Creams, Gels, Pastes, and Collodions.
2. It should be noted that general terms, such as lotion, liniment, and liquid, have been used to name topical liquids, which could be solutions, suspensions, or emulsions. As was discussed in Chapter 27, in 2002, USP formed a group to clarify pharmaceutical dosage form nomenclature. In 2006, FDA revised its dosage form terminology to help users of drug products in differentiating between topical dosage forms such as lotions, creams, ointments, and pastes (2). According to the 2006 FDA CDER Data Standards Manual, the following definitions apply:
a. Lotion: “An emulsion, liquid dosage form. This dosage form is generally for external application to the skin” (2). A footnote states that this term will be restricted to emulsions and will no longer be used for solutions or suspensions (2).
b. Liniment: “A solution or mixture of various substances in oil, alcoholic solutions or soap, or emulsions intended for external application” (2).
B. Miscible/immiscible: When two liquids are completely soluble (that is, molecularly dispersed) in each other in all proportions, they are said to be miscible; examples include water and alcohol, and olive oil and cottonseed oil. Some liquid pairs, such as castor oil and alcohol, are partially miscible, which means that they are soluble in each other in definite proportions. Immiscible liquid pairs are imperceptibly soluble in each other in any proportion; examples include water and mineral oil, and alcohol and mineral oil. Specific miscibility information for common pharmaceutical solvents is given in Chapter 15, Pharmaceutical Solvents and Solubilizing Agents; for a general discussion of miscibility, see section IV. C. 2. in Chapter 27, Solutions.
C. Emulsification: Emulsification is the process of creating an emulsion from two immiscible liquid phases. It can be accomplished when energy is applied to the system (e.g., trituration or homogenization) to create small droplets and cause a physical and/or electrostatic barrier to form around the droplets to prevent them from coalescing. This is accomplished by the use of emulsifying agents. The dispersed droplets are collectively termed the internal phase, and the continuous liquid is called the external phase.
D. Emulsifying agents: Emulsifying agents are surfactants that concentrate at the interface of the two immiscible phases, reduce the interfacial tension between the immiscible phases, provide a barrier around the droplets as they form, and prevent coalescence of the droplets. Some emulsifying agents also increase the viscosity of the system, slowing aggregation of the droplets and decreasing the rate of creaming. Surfactants and emulsifying agents commonly used for compounding purposes are described and discussed in Chapter 20, Surfactants and Emulsifying Agents.
E. Creaming: Creaming is the migration of the droplets of the internal phase to the top or bottom of the emulsion. The migration is caused by the difference in density between the two phases, and the direction of the movement depends on whether the internal phase is more or less dense than the continuous or external phase.
F. Coalescence: Coalescence is the merging of small droplets into larger droplets with eventual complete separation of phases so that the droplets cannot be re-emulsified by simple shaking of the preparation. With coalescence, the barrier formed by the emulsifying agent(s) is broken or destroyed. This irreversible coalescence of the droplets is also called cracking.
II. USES OF LIQUID EMULSIONS
A. Oral emulsions: As discussed in the chapters on solutions and suspensions, there are times when oral liquid preparations are needed. Generally, oral liquid emulsions are less acceptable to patients than are solutions or suspensions because of the objectionable oily feel of emulsions in the mouth. Therefore, an oral emulsion is formulated only when it is necessary to make a liquid preparation of an oil or when the solubility or bioavailability characteristics of a drug make this dosage form clearly superior.
B. Topical emulsions: Topical emulsions are more common. Emollient (soothing of the skin) or protective properties are often desired of topical preparations, and oils can serve these functions. When the oils are emulsified, they feel less greasy and are more aesthetically appealing to patients.
III. EMULSION TYPE
A. Oil-in-water(o/w): In this type, the oil is dispersed as droplets in an aqueous solution. This is the most common emulsion type. It is always preferred for oral preparations where an oily feel in the mouth is objectionable. It is also used for external preparations when ease of removal and/or a non-greasy-feeling preparation is desired.
B. Water-in-oil(w/o): In this type, the water is dispersed as droplets in an oil or oleaginous material. This type is used for external preparations when emollient, lubricating, or protective properties are desired.
C. Factors that determine emulsion type
1. Emulsifier
As described in Chapter 20, some emulsifiers will form either w/o or o/w emulsions; others form only one type.
2. Phase ratio (that is, relative amounts of oil and water)
All other things being equal, the phase that is present in the greater concentration tends to be the external phase, but an emulsifying agent that strongly favors a particular emulsion type and that forms a good barrier at the interface can overcome an unfavorable phase ratio.
3. Order of mixing
Because the phase that is present in the greater concentration tends to be the external phase, the phase that is being added, usually by portions, tends to be the internal phase. The bulk external phase will continue to accommodate added internal phase as small droplets until either the bulk phase becomes completely packed or there is no longer sufficient emulsifying agent to serve as a barrier to coalescence. Then, if more internal phase is added, either it will fail to be emulsified and will remain as separate droplets or the emulsion will coalesce; or, if the emulsifier will allow it, phase inversion will occur. The external phase, which was the continuous phase, now becomes the dispersed droplets, the internal phase.
IV. DESIRED PROPERTIES OF A LIQUID EMULSION
A. Fine droplets
Emulsions with fine droplet size are desired. Many factors can contribute to small droplets.
1. One factor is the mechanical method used for mixing and shearing the two immiscible liquids. The pharmaceutical industry has specialized equipment for this task. For extemporaneous compounding, a rough-sided Wedgwood mortar is usually used for the emulsification process. Simple, relatively inexpensive hand-homogenizers and high-speed blenders are available, which may give finer and more uniform droplets.
2. Certain techniques, such as phase inversion, can be used to give fine, uniform-sized droplets.
3. Finally, some emulsifying agents give finer emulsions. For example, amino-soaps are better-balanced emulsifiers than are the alkali soaps and give more stable emulsions of finer droplet size (3).
B. Slow aggregation of the droplets and creaming of the preparation
1. Though almost all emulsions eventually cream, the rate of creaming should be slow enough to ensure accurate measurement of a dose or application of a uniform preparation.
2. Aggregation and creaming can be slowed through proper emulsification and through the use of various additives, such as viscosity-increasing agents. To control the rate of creaming, you can adjust some of the parameters found in Stokes’ Law. Though this equation was developed for particles settling in a suspension, many of the same factors affect the rate of creaming for droplets in an emulsion. These include droplet size, viscosity of the continuous phase, and relative density difference of the droplets and the continuous phase. For a more complete discussion of Stokes’ Law, see section III. C. in Chapter 28, Suspensions.
C. Ease of redispersion when shaken
Though aggregation and creaming are usually unavoidable, the preparation should be formulated so that the internal phase readily redisperses to give a uniform emulsion when the preparation is shaken. Furthermore, coalescence should not occur.
V. COMPOUNDING BASIC EMULSION TYPES
A. Acacia emulsions: Acacia is unique among the polymer emulsifiers in its ability to form emulsions using only a Wedgwood mortar and pestle. It is therefore a useful ingredient for extemporaneous compounding of emulsions and is usually the first emulsifying agent considered when a compounded emulsion is needed.
1. The emulsification process for acacia emulsions requires the formation of a primary emulsion. The term primary emulsion is used to describe the initial emulsion formed with a prescribed ratio of ingredients. This prescribed set of ingredients gives a system of optimal viscosity and consistency so that the shearing force exerted in the mortar is maximized to allow the formation of an emulsion.
2. Ingredient ratio for primary acacia emulsions
a. For fixed oils, such as vegetable oils, and for mineral oil, the oil-to-water-to-acacia ratio (o:w:a) is 4:2:1. In general, fixed oils (e.g., vegetable oils) form acacia emulsions more readily than does mineral oil, so if there is a choice of oils, select one of the fixed oils.
b. The ratio for volatile and essential oils is 3:2:1 or 2:2:1.
c. The absolute ingredient amounts calculated from the appropriate ratio are predicated on the total amount of oil in the formulation. Because acacia forms o/w emulsions, the oil is the internal phase. Therefore, all of the oil in the formulation must be emulsified when making the primary emulsion. After the primary emulsion is formed, the emulsion may be diluted with any extra water or water-miscible phase, as required.
3. Methods of forming the primary emulsion
a. Dry gum method. The dry gum method usually is the preferred method. Its steps are given next and are illustrated with a set of four photographs in Color Plate 7.
(1) The calculated amount of acacia and all the oil contained in the formulation are put in a Wedgwood mortar and triturated until a smooth slurry results and all the acacia is properly wet by the oil.
(2) The amount of the aqueous phase, which is calculated from the ratio given earlier, is measured in a clean, dry graduated cylinder and is added, all at once, with hard and fast trituration.
(3) Trituration is continued until the primary emulsion is formed. You know this has occurred when the system changes from a translucent, oily-appearing liquid into a thick, white liquid. The sound of trituration also changes to give a crackling sound.
(4) Once the primary emulsion is formed, other ingredients may be added.
b. Wet gum method. With the wet gum method, the order of mixing is as follows:
(1) The appropriate amount of acacia is put in a Wedgwood mortar, and a small amount of water-miscible wetting agent, such as glycerin, is added to wet the acacia. This is necessary because powdered acacia gets lumpy when water is added directly to it.
(2) The calculated amount of water is then gradually added in portions with trituration.
(3) The oil is then gradually added with trituration until all the oil has been added and the primary is formed.
(4) As with the dry gum method, once the primary emulsion is formed, water or other ingredients may be added.
4. Order of mixing for acacia emulsions
a. Make the primary emulsion first using all the oil(s), the acacia, and Purified Water, in the appropriate ratio.
b. Additional water, water-miscible liquids, including flavored syrups, and water-soluble drugs or chemicals may then be added directly to the primary emulsion. Soluble ingredients that are in solid form may be dissolved first in water or another appropriate solvent before being added to the emulsion.
c. Insoluble ingredients, such as zinc oxide and calamine, should be put in a separate mortar, and the primary emulsion should be added to the powders in portions with trituration. This is done to wet the powders and reduce their particle size so that a smooth preparation results. This process is illustrated in Sample Prescription 29.1.
d. In some cases, oil-soluble ingredients may be dissolved in the oil phase before the formation of the primary emulsion. This is illustrated with the active ingredients avobenzone and oxybenzone in Sample Prescription 29.1. If the primary emulsion fails to form with the extra ingredient or ingredients in the oil phase, the ingredients should be handled as described in c. preceding.
5. Preservation and storage
a. USP Chapter 〈1151〉 states that preservatives are required for all emulsions (1). This is especially important with acacia emulsions because they are very susceptible to microbial (especially mold) growth.
b. Acacia emulsions have a pH in the range of 4.5 to 5.0, unless the formulation contains an ingredient that alters the pH. Therefore, preservatives that require a slightly acid pH, such as benzoic acid or sorbic acid, are effective preservatives for acacia emulsions. For the official acacia emulsion, Mineral Oil Emulsion USP, the use of either benzoic acid 0.2% or alcohol 4% to 6% is recommended. The benzoic acid may be added as its sodium salt. Methylparaben 0.2% with propylparaben 0.02% is also an acceptable preservative system. The quaternary ammonium preservatives, such as benzalkonium chloride, benzethonium chloride, and cetylpyridinium chloride, are not recommended because they are inactivated through binding with acacia.
c. For reasons of improved stability and taste, internal preparations should be stored in a refrigerator. External preparations are generally stored at controlled room temperature.
6. A complete description of acacia, including its incompatibilities and limitations, is given in Chapter 19, Viscosity-Inducing Agents.
B. Nascent soap emulsions: The term nascent means beginning to exist or to develop. As the name implies, the emulsifier is formed as these emulsions are made. These emulsifiers are the hard and soft soaps, which are discussed in Chapter 20, Surfactants and Emulsifying Agents. The current section concentrates on a prototype of this emulsion type, so-called lime water emulsions, in which the emulsifier, calcium oleate, is formed when saturated solution of calcium hydroxide (lime water) is added to a vegetable oil containing oleic acid.
1. Oil phase
a. Olive oil was the original oil used in these emulsions because, of all the vegetable oils, it has the largest amount of free fatty acid necessary for forming the soap-emulsifying agent.
b. Olive oil may be replaced by other vegetable oils; however, in this case, extra free fatty acid in the form of oleic acid must be added.
c. Depending on its source, olive oil may also need fortification with extra oleic acid. It may be advisable to add 3 to 5 drops of oleic acid per 30 mL of olive oil or 1 to 1.5 mL oleic acid per 30 mL of any other vegetable oil before the emulsification process is begun. Extra oleic acid may be added drop-wise during emulsification if necessary. This is illustrated in Sample Prescription 29.2.
2. Lime water should be freshly prepared. The formula can be found in the USP under Calcium Hydroxide Topical Solution. It is reproduced here (4):
Calcium hydroxide | 3 g |
Purified Water | 1,000 mL |
Add the calcium hydroxide to 1,000 mL of cool Purified Water, and agitate the mixture vigorously and repeatedly during 1 hour. Allow the excess calcium hydroxide to settle. Dispense only the clear, supernatant.
3. Methods of preparation
a. Bottle method: With this method, equal amounts of oil (containing adequate oleic acid) and lime water are placed in a bottle. The bottle is shaken vigorously to form the emulsion. The emulsion can then be used as a wetting agent for any solid insoluble ingredients. This method is illustrated on Color Plate 8, and the procedure is demonstrated on the CD that accompanies this book.
b. Mortar method:The mortar method is often preferred when the formulation contains solid insoluble ingredients, such as zinc oxide or calamine. These solids concentrate at the oil–water interface as the emulsion is being formed and enhance the interfacial barrier, which improves the stability of the system. With this method, the solids are placed in a mortar. The oil (containing oleic acid) is added in portions with trituration until all the oil has been added and a smooth slurry of oil-powders is obtained. The lime water is then added in portions with trituration to form the emulsion.
4. Order of mixing: This depends somewhat on the method of emulsification as described earlier.
a. With either method, water-miscible liquids and water-soluble drugs or chemicals should be added to the lime water before it is added to the bottle or mortar for emulsification. This is because water is the internal phase.
b. Because oil is the external phase, oil-soluble and oil-miscible ingredients can be added to the oil before emulsification or to the emulsion after the water phase is emulsified.
c.
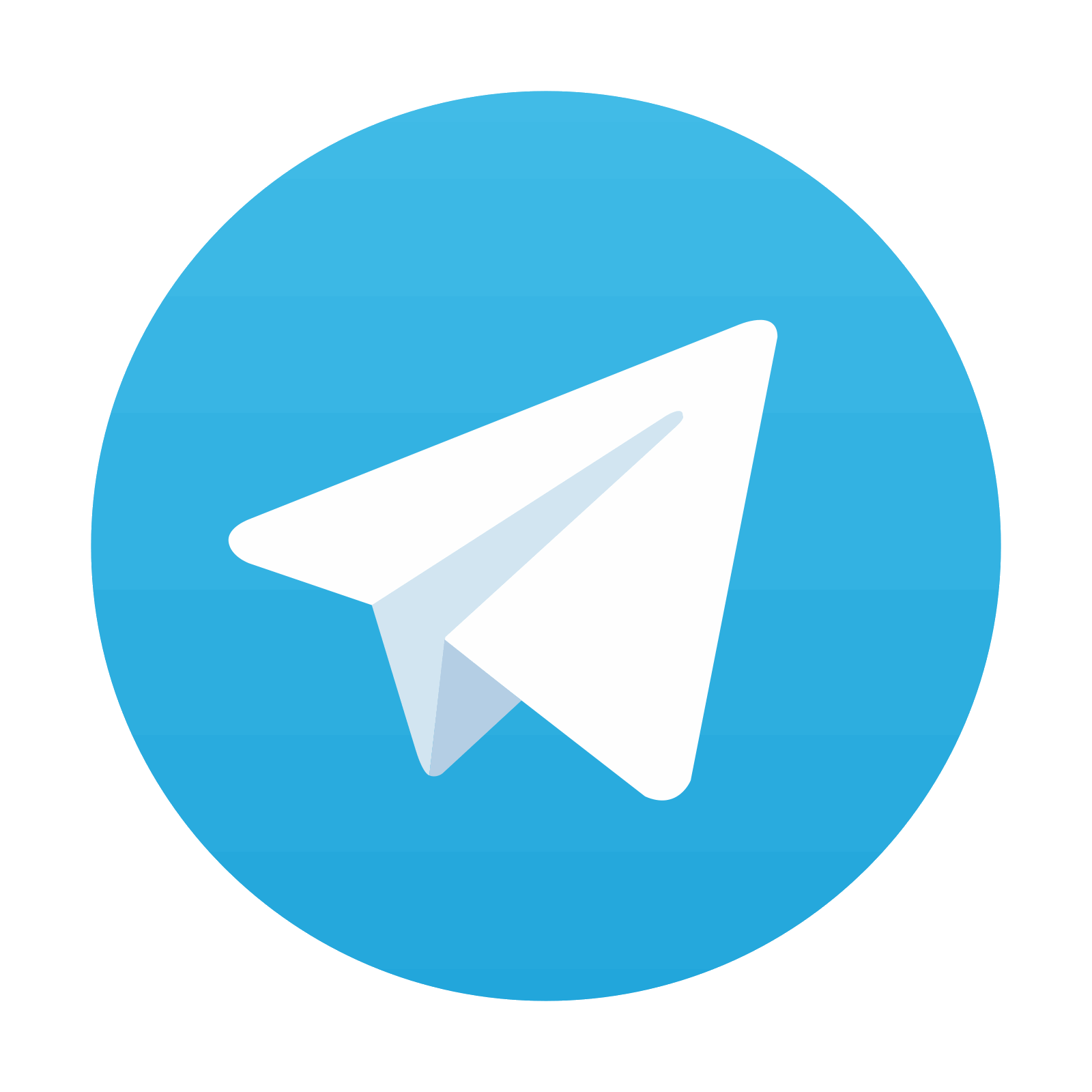
Stay updated, free articles. Join our Telegram channel
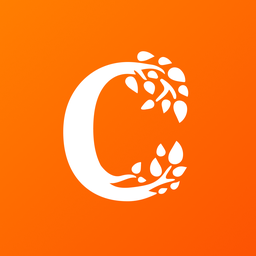
Full access? Get Clinical Tree
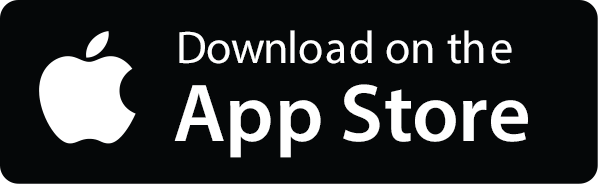
