OUTLINE
The Role of Viscosity in Formulation
Suspending and/or Viscosity-Inducing Agents Listed in USP 30/NF 25
I. DEFINITIONS
A. Viscosity is a measure of the resistance to flow of a system under an applied stress. The more viscous a liquid, the greater the applied force required to make it flow at a particular rate. This is expressed mathematically by Newton’s Law of Flow (1):
where F/A is shearing stress, the force per unit area required to bring about flow; dv/dr is the rate of shear; and η is the coefficient of viscosity, usually referred to as just viscosity.
B. The traditional unit of viscosity is the poise, which is defined as the shearing force in dynes required to produce a velocity of 1 cm/s between two parallel planes of a liquid each 1 cm2 in area and separated by a distance of 1 cm.
C. The unit of viscosity commonly used in pharmacy is the centipoise (cp; plural, cps), which is equal to 0.01 poise.
D. In the more recently adopted International System of Units (SI), the basic unit of viscosity is Pascal sec (Pa s) or Newton/m2–sec−1, which equals 10 poise. The SI unit of viscosity commonly used to report viscosities of pharmaceutical liquids is the milliPascal sec (mPa s), which conveniently is numerically equal to the viscosity value in centipoise. The various units of viscosity can be illustrated with the viscosity of water, which is approximately 1 cps at 20°C.
The SI System’s mPa s viscosity units are now used for reporting viscosity values in books such as the Handbook of Pharmaceutical Excipients (2).
E. While “thick” liquids are generally more viscous than “thin” liquids, there is not a direct relationship between perceived thickness and viscosity. The viscosity values for some common substances are given in Table 19.1; these give some feeling for relative centipoise (or mPa s) values.
F. Viscosity-inducing agents are molecules that interact with water molecules to form a structured system that interrupts the flow of the molecules past one another. They are hydrophilic colloids that are classified either as soluble macromolecules or particulate association colloids (3).
1. The soluble macromolecules are linear or branched-chain polymers that dissolve molecularly in water. The resulting preparations are classified as colloidal dispersions because the individual molecules are in the colloidal particle size range, exceeding 50 to 100 Å. The macromolecules are further classified into one of three groups: natural polymers, semisynthetic cellulose derivatives, and synthetic polymers.
2. The particulate association colloids are water-insoluble particles that hydrate strongly. They include inorganic silicates, colloidal silicon dioxide, and microcrystalline cellulose.
3. When in liquid form colloidal dispersions are sometimes referred to as sols, when these systems are semisolids or solids they are called gels.
G. Newtonian and non-Newtonian flow (1)
1. Pure liquids and dilute solutions (such as those in Table 19.1) exhibit Newtonian flow, which means that their viscosity, η, is characterized by a single value. The relationship between shearing stress (F’/A) and rate of shear (dv/dr) is linear: a plot of shearing stress versus rate of shear gives a straight line; the slope of the line, η, is constant and the line passes through the origin (Fig. 19.1A).
2. Many pharmaceutical systems exhibit non-Newtonian flow patterns. The viscosity of these systems is not constant; rather, it depends on the shearing stress or force applied. Liquid and solid heterogeneous dispersions, such as suspensions, emulsions, colloidal dispersions, and ointments and creams, are non-Newtonian systems. These are further classified into three different groups, based on their flow characteristics: plastic, pseudoplastic, and dilatant. It is helpful for pharmacists who compound drug preparations to have some understanding of these systems. A brief description follows; for a more detailed treatment, refer to a book on physical pharmacy (1) or the chapter on rheology in Remington’s The Science and Practice of Pharmacy (4).
a. Pseudoplastic systems are sometimes called shear thinning systems because their viscosity decreases with increasing shear stress. In this case, a plot of shearing stress versus rate of shear initially starts at the origin and appears Newtonian, but the slope begins to decrease, giving a curved line (Fig. 19.1B). Pharmaceutical systems that exhibit pseudoplastic behavior are the colloidal dispersions of the natural gums, such as acacia and tragacanth, and the synthetic and semisynthetic hydrophilic polymers, such as methylcellulose and carboxymethylcellulose.
b. Plastic systems exhibit Newtonian flow patterns, but only after a certain shearing stress, called the yield value, is reached. In this case, the plot of shearing stress versus rate of shear does not go through the origin. In other words, a plastic system exhibits infinite viscosity (the slope, η = ∞) and does not flow at all until the yield value is reached; once flow is established, the system behaves like a Newtonian system (Fig. 19.1C). Plastic flow is a desirable property in disperse systems in which the force of gravity on small particles is not enough to overcome the yield value; that is, suspension particles do not settle and emulsion droplets do not cream but, under the larger stresses of shaking, pouring, rubbing, or syringing, the system flows. Plastic flow is produced by structured systems of flocculated particles in concentrated suspensions or emulsions.
c. Thixotropy is a property of many plastic and pseudoplastic systems in which the consistency lost when shear is applied (e.g., shaking) takes some finite amount of time for recovery (Fig. 19.1D). This is a desirable property of liquid pharmaceutical dispersions: The dispersion becomes fluid when the product is shaken; the product remains fluid long enough for a dose to be poured or a topical product to be applied; the system then regains its consistency rapidly enough on standing so that the suspended particles do not settle. Catsup is a nonpharmaceutical example of a thixotropic system. Bentonite Magma, consisting of flocculated colloidal clay particles, and several of the structured liquids marketed as suspending vehicles for compounding, are examples of pharmaceutical thixotropic systems.
FIGURE 19.1. A: FLOW CURVE FOR A NEWTONIAN SYSTEM. B: FLOW CURVE FOR A PSEUDOPLASTIC SYSTEM. C: FLOW CURVE FOR A PLASTIC SYSTEM. D: FLOW CURVE OF A SYSTEM EXHIBITING THIXOTROPY. E: FLOW CURVE FOR A DILATANT SYSTEM.
d. Dilatant systems act in a manner opposite that of pseudoplastic systems. They are called shear-thickening systems because their viscosity increases with increasing shear stress (Fig. 19.1E). Suspensions that have high concentrations of deflocculated particles may exhibit dilatant behavior. One common example of a dilatant system is a starch-in-water slurry. This system flows when left at rest but firms up when pressure is applied. Dilatant systems may cause problems with high-speed mixing equipment used in formulation; these materials may solidify under conditions of high shear and damage the equipment. Dilatancy must also be avoided in injectable suspensions because the high shear stress that results when pushing a liquid through a small needle bore may cause the syringe to lock—not a pleasant experience for the patient.
II. THE ROLE OF VISCOSITY IN FORMULATION
A. Increased viscosity can offer both advantages and disadvantages with respect to formulating liquid and semisolid preparations. Understanding the meaning of viscosity and the various types of flow behavior is useful to the pharmacist in selecting appropriate formulation ingredients.
B. For topical preparations, appropriate viscosity is essential in achieving desirable smoothness and consistency so that the preparation will be easy to apply, will remain in contact with the affected area, and will feel good to the patient.
C. Palatability of oral liquid preparations is often enhanced by formulating the preparation with appropriate viscosity. This provides what is sometimes referred to as desirable mouth feel. Viscous vehicles also may improve the perceived flavor of oral liquids by reducing the contact of bad-tasting drugs with the taste buds on the tongue.
D. High viscosity is a disadvantage when dissolving drugs to make solutions because diffusion, and therefore rate of dissolution, decreases as viscosity increases. This is why compounders do not dissolve drugs directly in viscous vehicles but rather first dissolve them in a minimum quantity of water or other low-viscosity solvent and then combine the resulting solution with the desired viscous vehicle.
E. If increased viscosity is the only formulation goal, a high-viscosity liquid, such as glycerin, or a concentrated aqueous solution of a soluble micromolecule, such as sucrose or sorbitol, may be used.
F. If a structured system is needed to retard the settling or creaming rate of the particles or oil droplets in dispersed systems, the selection and addition of a viscosity-inducing agent that gives pseudoplastic, plastic, or thixotropic flow is required.
III. SUSPENDING AND/OR VISCOSITY-INDUCING AGENTS LISTED IN USP 30/NF 25
A. Table 19.2 gives the articles listed as suspending and/or viscosity-increasing agents in the USP 30/NF 25 (5). This is not a complete list of all agents used in this way; some compounds, although not on this list, are used for these purposes in manufactured products and compounded preparations.
B. The agents used most commonly as suspending or viscosity-increasing agents in extemporaneous compounding are described in the following section. This text employs the usual convention of using upper-case first letters for words designating official USP/NF articles (e.g., Alcohol, Purified Water) and lower-case first letters for words designating the chemical substances (e.g., ethanol, water). For each agent, the text gives the information needed for selection and use of a suitable compound: a description of each compound, including the pH of its dispersions, its solubility, incompatibilities, suggestions for preparing and preserving its dispersions, possible uses for the compound, and some advantages and disadvantages of its use.
IV. VISCOSITY-INDUCING AGENTS
The descriptions and solubilities presented here give a composite of information from Remington’s The Science and Practice of Pharmacy (6), the Handbook of Pharmaceutical Excipients (2), The Merck Index (7), official monographs in the USP 30/NF 25 (8,9), the Chemistry and Compendial Requirements section of the USP DI Vol. III (10), and other references as cited. Additional information on each agent, including references to original research journal articles, can be found in the Handbook of Pharmaceutical Excipients (2).
A. Semisynthetic cellulose derivatives
Cellulose is a polymer of β-D-Glucose, with –CH2OH groups alternating above and below the plane of the cellulose molecule, thus producing long, unbranched chains. The absence of side chains allows cellulose molecules to lie close together and form rigid structures. Cellulose is the major structural material of plants. Cellulose may be modified to produce many semisynthetic cellulose derivatives.
1. Methylcellulose USP
a. Description
(1) Methylcellulose is a polymer formed by the methylation of cellulose to form methyl ether linkages. In other words, some of the hydrogens on the –OH groups are replaced with methyl (–CH3) groups. The degree of methylation is regulated to yield polymers with a controlled number of sites for hydrogen bonding. This, together with polymer chain length, determines the degree to which the polymer increases the viscosity of its water solutions or gels. These solutions or gels exhibit pseudoplastic flow characteristics.
(2) Methylcellulose is a white, fibrous powder or granules. The pH of a 1% dispersion is 5.5 to 8.0.
(3) Methylcellulose is available in various viscosity grades: 15, 25, 100, 400, 1,500, and 4,000 cps are the most commonly available grades. The grade number refers to the viscosity of a 2% aqueous solution at 20°C.
b. Solubility: Methylcellulose is insoluble or practically insoluble in acetone, alcohols, glycols, hot water, and saturated salt solutions, but it is soluble in glacial acetic acid. It swells in water and produces a clear to opalescent, viscous colloidal solution that is neutral to litmus.
c. Incompatibilities
(1) Methylcellulose is stable to alkalies and dilute acids but coagulates from solution with high concentrations of salts of mineral acids, with moderate to high concentrations of salts of polybasic acids, and with phenols and tannins. This is reported to be prevented by the addition of alcohol or glycol diacetate (6).
(2) It is also incompatible with aminacrine hydrochloride, chlorocresol, mercuric chloride, silver nitrate, cetylpyridium chloride (but not benzalkonium chloride), p-hydroxybenzoic acid, p-aminobenzoic acid, and the parabens (2). Benzyl alcohol is also stated to be incompatible with methylcellulose.
d. Preparation of dispersions
While the hydrogen bonding sites make possible the formation of clear viscous gels of methylcellulose, they are also responsible for the difficulty with which its solutions are made. If you were to add water at room temperature to methylcellulose powder, a clumpy mess would result. This is because water forms hydrogen bonds rapidly with the methylcellulose on the outside of the powder bed, forming a very viscous layer and preventing water penetration to the rest of the powder. Hydration of the powder and clear gel formation would eventually occur, but this takes a long time. Listed below are three methods for successful dispersion of methylcellulose in water:
(1) Heat to boiling a portion (approximately one third) of the total water needed for the dispersion. Add the methylcellulose powder and stir to completely wet the powder. Add the remaining water as cold water or ice chips and stir. This method is useful when you need to make a relatively clear solution quickly.
(2) Heat to boiling the total amount of water needed for the solution. Disperse the methylcellulose in the water. Put the cloudy dispersion in a refrigerator and gently stir or agitate frequently until a clear viscous solution results. This method is not useful when you need the solution immediately because it takes a minimum of 4 hours to convert the nonviscous, cloudy dispersion to a clear, viscous gel.
(3) Place the methylcellulose powder in a glass mortar and wet the powder completely with a minimum amount of alcohol or glycerin; then, with trituration, gradually add cold water to the final desired volume. This method is useful when boiling water is not readily available; however, the gels that result may not be crystal clear. Furthermore, there may be cases when you want to avoid alcohol or glycerin in a formulation. This method is particularly handy when the formulation contains an alcohol or glycol as an ingredient and the end product is a suspension or emulsion in which clarity is not essential.
e. Preservation of aqueous dispersions
(1) Although pure solutions or gels of methylcellulose do not support bacterial or mold growth as readily as comparable preparations of the natural polymers (e.g., acacia and tragacanth), preservatives are recommended for methylcellulose solutions because they are liable to microbial spoilage.
(2) Because the pH of methylcellulose solutions is between 5.5 and 8.0, the organic acid preservatives benzoic acid/sodium benzoate and sorbic acid/potassium sorbate would not be effective unless the pH of the solution is adjusted to a level of 5.0 or lower.
(3) As stated earlier, methylcellulose is incompatible with the parabens, benzyl alcohol, and cetylpyridium chloride. For methylcellulose solutions with pH exceeding 5.0, this leaves the following possibilities for preservatives: alcohol, propylene glycol, and benzalkonium or benzethonium chloride.
f. Uses
(1) Methylcellulose is used extensively by the pharmaceutical industry in both oral and topical products. It is used both in solid dosage forms and in emulsions, suspensions, and solutions.
(2) These polymers are also used therapeutically as bulk laxatives, as diet aids, and in artificial tears products. These manufactured products are sometimes used as vehicles or excipients for compounding. For example, artificial tears are useful vehicles for compounding sterile ophthalmic solutions (11). The use of the methylcellulose bulk laxative powder Citrucel is illustrated with Sample Prescription 28.5 in Chapter 28, Suspensions.
(3) In compounding, methylcellulose is useful for making sugar-free vehicles to use in formulating oral solutions and suspensions. It can also be used as a viscosity-inducing agent for topical liquid and gel preparations when a film is acceptable.
(4) A 1% gel of methylcellulose 1,500 cps dispersed in Purified Water or Water for Irrigation gives a liquid vehicle that is useful for many purposes. Although there are published formulas like this that are preserved with 0.2% sodium benzoate, the pH of methylcellulose solutions is not favorable to preservation with this agent.
(5) A 5% gel of methylcellulose 1,500 cps dispersed in Purified Water or Water for Irrigation gives a soft semisolid gel that can be used for topical or vaginal preparations.
g. Advantages of methylcellulose
(1) It produces aesthetically pleasing, clear, colorless, odorless gels.
(2) Its gels have a neutral pH and are stable over a wide pH range, approximately 3 to 12.
(3) It is a nonelectrolyte with no ionizable groups, so it is compatible with many other ingredients and drugs; it is not reactive with quaternary nitrogen compounds (such as benzalkonium chloride), weak acids, or the salts of weak bases.
(4) It is relatively unaffected by moderate concentrations of univalent ions.
(5) Although not soluble in alcohol or most other organic solvents, its solutions tolerate relatively high alcohol concentrations.
(6) It is not a sugar, so it is useful when a sugar-free vehicle is needed.
(7) It is effective as a viscosity-inducing agent at low concentrations, so vehicles made with methylcellulose are not hypertonic. If necessary, its solutions can be made isotonic by adding compatible solutes.
(8) Methylcellulose solutions and gels are less susceptible to bacterial and mold growth than are the natural polymer dispersions.
h. Disadvantages
(1) Flavoring and sweetening are required for palatability when the solutions are used as vehicles for oral drug preparations.
(2) Because methylcellulose depends on hydrogen bonding for its solubility in water, drugs or chemicals that strongly associate with water can dehydrate methylcellulose molecules and cause their separation from solution. Compatibility problems occur with high concentrations of univalent ions and moderate concentrations of polyvalent ions. (See Sample Prescription 27.2 in Chapter 27, Solutions.) Methylcellulose is also dehydrated by phenolic substances, including phenol and resorcinol. (See Sample Prescription 28.3 in Chapter 28, Suspensions.)
(3) Methylcellulose is not soluble in alcohol or most other organic solvents, although its aqueous solutions do tolerate fairly high concentrations of alcohol.
(4) The solutions support bacterial or mold growth, especially when nutrients such as organic drugs, sweeteners, or flavors are added.
(5) The solutions are somewhat difficult to prepare.
2. Carboxymethylcellulose Sodium USP (Sodium CMC)
a. Description
(1) Sodium CMC is structurally similar to methylcellulose except that the methyl groups are replaced with—CH2COO−Na+ moieties. Although sodium CMC has properties similar to methylcellulose, there are some differences, due mainly to the ionic centers in sodium CMC molecules.
(2) It is a white to cream-colored powder or granules. The powder is hygroscopic and, in conditions of high humidity, it can absorb large amounts of water. It has a pKa of 4.3, and a 1% w/v aqueous solution has a pH of approximately 7.5.
(3) Sodium CMC comes in three basic viscosity grades: low, medium, and high. These are sometimes designated LF (1% aqueous solution = 25 to 50 cps), MF (1% aqueous solution = 400 to 800 cps), and HF (1% aqueous solution = 1,500 to 3,000 cps).
(4) Table 19.3 gives the percent concentrations in water of various viscosity-inducing agents needed to give a viscosity of 800 cps. Notice that a 1.7% methylcellulose 1,500 cps solution gives approximately the same viscosity as a 1.9% solution of medium-viscosity sodium CMC. Based on this observation, you can conclude that methylcellulose 1,500 cps is approximately equal to medium-viscosity sodium CMC in its ability to induce viscosity. Table 19.3 gives useful information when it is necessary to substitute one viscosity-increasing agent for another in a formulation.
b. Solubility: Sodium CMC is insoluble or practically insoluble in acetone, alcohol, glycols, and most other organic solvents. Its solubility in water varies with the degree of substitution on the polymer. It disperses in both hot and cold water to form clear, colloidal solutions.
c. Incompatibilities
(1) Because sodium CMC molecules interact with water using both hydrogen bonding and ion-dipole interactions, they are less susceptible to dehydration than methylcellulose but are subject to the normal incompatibilities of its weak electrolyte group.
(2) Because it is the salt of a weak carboxylic acid, it is more sensitive to pH than methylcellulose. Although they will tolerate a fairly wide pH range (2 to 10), its solutions are most stable in the range of pH 5 to 10 and exhibit maximum viscosity at pH 7 to 9 (2).
(3) Its solutions tolerate a fairly high concentration of alcohol or glycols.
(4) Sodium CMC, as a large anionic molecule, has potential incompatibilities with quaternary nitrogen compounds such as benzethonium and benzalkonium chloride and with acids and the salts of some weak bases.
(5) It is also incompatible with soluble iron salts and some other metals such as aluminum, mercury, and zinc (2).
d. Preparation of dispersions
(1) Remington ’s statement that it is easily dispersed in water to form colloidal solutions is somewhat of an overstatement:When water is added to the powder or granules, clumps of partially hydrated powder result; fortunately, the powder hydrates fully and disperses to form a clear solution in 1 to 2 hours.
(2) Although sodium CMC gels are made more easily than are methylcellulose solutions, CMC powder clumps initially when either hot or cold water is added. As stated previously, these solutions clear in 1 to 2 hours, irrespective of the temperature of the water added.
(3) Carboxymethylcellulose Sodium Paste USP is a thick semisolid with a concentration of 16.5% sodium CMC in water (8).
(4) Gels of sodium CMC can be made from sols by the addition of controlled amounts of polyvalent cations, such as aluminum. If too much electrolyte is added or if it is added too rapidly, precipitation of the polymer results (12).
e. Preservation of aqueous dispersions
(1) It is recommended that aqueous solutions of sodium CMC be preserved if stored for an extended period (2).
(2) Selection of a preservative for sodium CMC sols poses a dilemma. The pH of its solutions is too high for effective use of the organic acids, and sodium CMC is incompatible with the quaternary ammonium preservatives. Methylparaben by itself does not preserve these solutions adequately, but the combination with propylparaben in propylene glycol, which is described in Chapter 16, can be used. Alcohol and/or propylene glycol are possibilities, depending on the circumstances.
f. Uses: Its uses are similar to those of methylcellulose.
g. Advantages of sodium carboxymethylcellulose
(1) Because of its ionic centers, sodium CMC interacts with water through ion-dipole interactions and is therefore less easily dehydrated than is methylcellulose, which depends solely on hydrogen bonding with water. As a result, sodium CMC gels are less affected by high concentrations of electrolytes. Sample Prescription 27.2 in Chapter 27, Solutions, illustrates this effect. As stated previously, controlled amounts of polyvalent cations cause gelation of CMC solutions.
(2) Although it is not soluble in alcohol or most other organic solvents, its solutions tolerate high alcohol concentrations.
(3) It is more stable than methylcellulose to phenolic-type compounds. This is illustrated in Sample Prescription 28.3 in Chapter 28, Suspensions.
h. Disadvantages
(1) Because of its ionic centers, which are salt forms of weak carboxylic acids, it has the potential for interactions and incompatibilities characteristic of these groups.
(2) Its gels have a pH of approximately 7.5; therefore, preservatives such as benzoic acid/Na benzoate and sorbic acid/K sorbate, which require a pH of 5 or less for activity, are not effective in solutions of sodium CMC.
3. Hypromellose (formerly Hydroxypropyl Methylcellulose) USP
a. Description
(1) Hypromellose is a propylene glycol ether of methylcellulose. It is official in the USP (8) with varying degrees of substitution, which confer several levels of viscosity induction.
(2) It is a white or slightly off-white, fibrous or granular powder. It is odorless and tasteless.
(3) Its solutions have a pH similar to that of methylcellulose, with a 1% solution having a pH range of 5.5 to 8.0.
b.
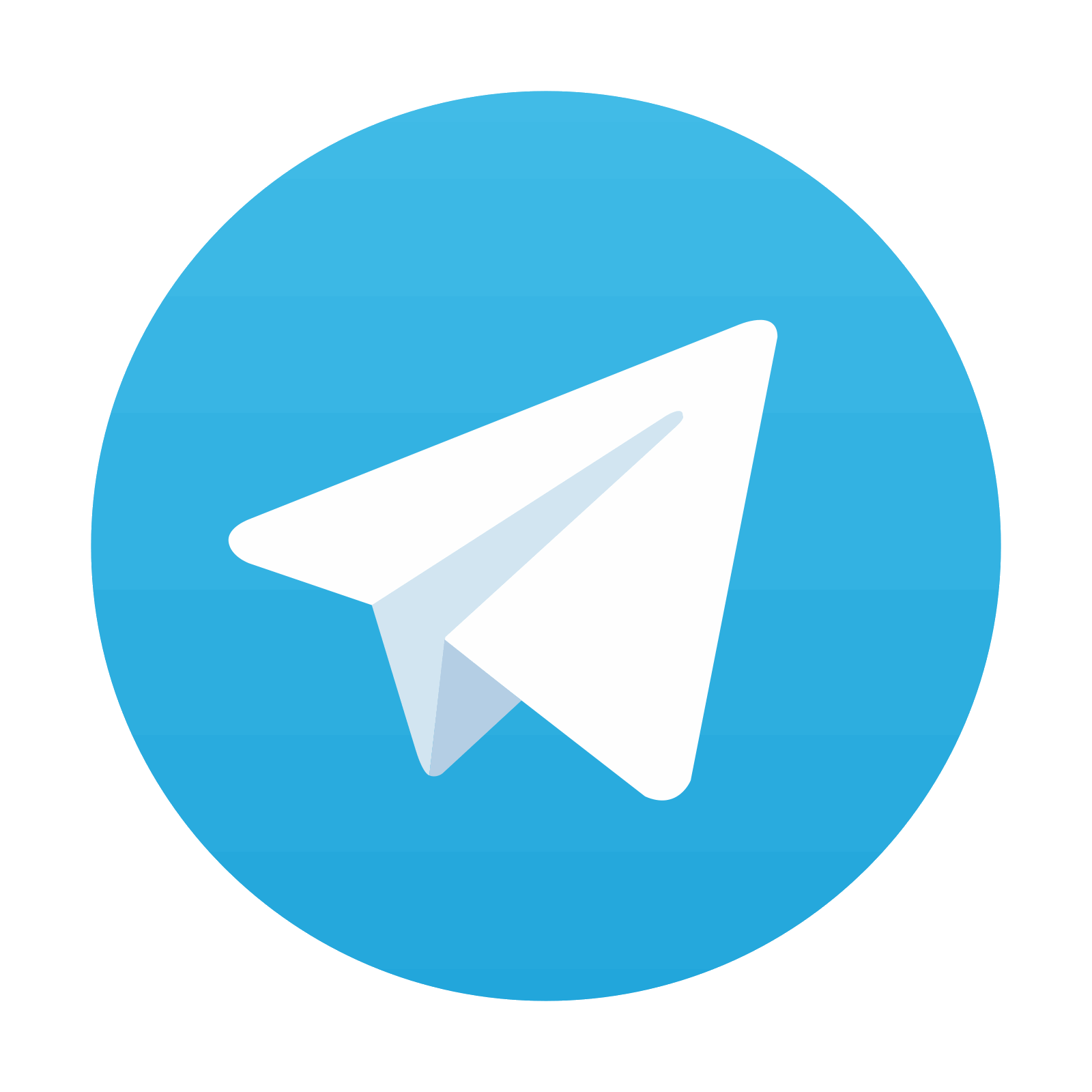
Stay updated, free articles. Join our Telegram channel
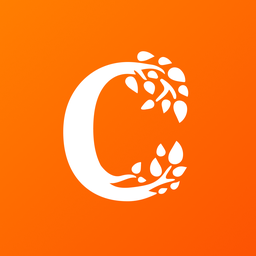
Full access? Get Clinical Tree
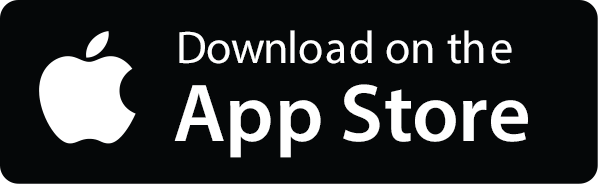
