Fig. 28.1
Schematic construction of exhaust and air filtering equipment (= Fig. 28.1a–g). Source: Recepteerkunde 2009, ©KNMP
For the protection of the operator and co-workers the most basic engineering control measure to minimise inhalation exposure (see Sect. 26.4.1) is ventilation of the work area. A ventilation rate of 2 h−1 or 5 h−1 is common for offices but not sufficiently efficient for preparation areas. A better effect will be obtained by containment of the activities that releases hazardous substances. In order to prevent contaminated air to enter the room, the exhaust is guided to the outside of the building and discharged in the environment or the exhausted air is filtered before re-entering the room. Filtration of exhaust air will decrease any exposure of the environment outside the building and filtration is generally expected.
For the protection of the product, working in a laminar airflow directed from the critical places or working in a complete gastight box are options used in practice.
Complete protection of operator and product can be achieved by an isolator (see Sect. 28.3.7). Apart from complete product and operator protection other advantages are: controlled disinfection procedures, lower initial investments costs of the background area and exploitation costs. Disadvantages are higher costs compared to a LAF unit and its elaborate cleaning and maintenance. Therefore, in practice the choice of type of local exhaust equipment is determined by a risk assessment of the process (taking into account the contamination of the product and of health damage of the operator), the available investment and the local experience.
For a systematic approach to the choice of the right local exhaust ventilation, the allowed level of exposure is compared with the actual exposure level and the assumed effectiveness of the exhaust device. Reference is made to [2]. Local exhaust ventilation is generally expected to establish a ten-fold reduction of the exposure level. Containment with ‘small-scale breaches’ is considered to establish a 100-fold reduction. Total containment as is accomplished by using an isolator.
For a general approach of preparation situations in community and hospital pharmacies (working with maximal 100 g of substances of hazard classes 1–5) reference is made to Sect. 26.5.2. For higher exposure levels the Advanced REACH Tool (see Sect. 26.5.1) offers guidance. The small scale preparation in pharmacies may generally require:
A powder exhaust unit for most dust releasing operations: weighing, capsule filling, mixing of solids, rotor-stator mixing
A horizontal or vertical LAF unit for the common aseptic handling with closed containers (see Sect. 31.3.4)
A safety cabinet or isolator for processing class 4 and 5 substances
An isolator if capsules have to be prepared with class 5 substances
A fume cupboard for processing volatile, inflammable or corrosive substances
It cannot be stated that a ‘normal’ down flow cabinet, with open front and without sleeves to the work top (so not a safety cabinet), or a down flow unit is safe for the operator if working with half-open or open systems. It may very much depend on airflow patterns if any contamination with a substance will be actively blown in the direction of the operator. If so, the exposure would be higher, in which case no ventilation or exhaust is preferred.
Influence of Local Devices on the Performance of Room HVAC
Local safety cabinets of any type will influence the air pattern, temperature and HVAC system in the preparation area. (HVAC means heating, ventilation, air-conditioning; see Sect. 27.5.1). The influence will vary. Sometimes all doors of the room must be closed in order to insure a correct function of a fume cupboard. Air expelled by the local safety flow systems will also influence the ventilation and the pressure in the room. Local devices produce energy in the form of heat and, unless exhausted, will change the room temperature. This can be uncomfortable for the operator.
28.3.2 Fume Cupboard
Fume cupboards are meant to protect the operator from fumes, steam, volatiles and corrosive fluids.
Fume cupboards are not effective enough for the safe handling of aerosols and powders.
28.3.2.1 Description
In pharmacy practice mainly the ducted type of flowhood is used, which is not recirculating the air into the room. The air in the hood, eventually mixed with the volatiles is discharged into the open air outside the building, often by flexible special ducting. The extractor (fan) of a fume cupboard does not come in contact with these volatiles. This is the reason why explosive or highly combustible material can be exhausted safe.
The direction of the flow inside a fume cupboard is upwards at the end, see Fig. 28.1a. Heavy volatiles concentrate on the bottom of the fume cupboard; lighter volatiles can be found somewhat higher in the fume cupboard. In both areas of the fume cupboard sufficient force of the airflow is obligatory: 0.5 m/s for vapours and 1 m/s for dust [3]. However, the speed of the inflow in a fume cupboard is not high enough for the exhaust of small solid particles. The material of the fume cupboard and the exhaust fan and duct must be resistant to corrosion, in order to work with corrosive or caustic agents.
In front of the fume cupboard there is a transparent safety sash, sliding gently up or down with a counterbalance mechanism to reach precisely the defined and properly validated working or loading position. The loading position is not safe, but high enough to place equipment inside. Low airflow alarm control panels are common. The working position creates a safe area under the glass window to work in with (gloved) hands and arm covers for that part of the arm entering the fume cupboard working area.
28.3.2.2 Maintenance and Inspections
Fume hood maintenance involves periodical (daily, quarterly, annual) cleaning, maintenance, calibration, qualification and inspections. In daily inspection the fume hood area is visually inspected by the operator. Hood function indicating devices (LEDs) are a part of the modern fume cupboard. Periodic inspection covers capture or face velocity measured with a velometer or anemometer.
Annual maintenance: Yearly the fume cupboard must be maintained, calibrated and tested by a certified firm and competent person and the results of the official tests reported. Exhaust fan maintenance comprises lubrication, belt tension, fan blade deterioration and speed of the fan. Air velocity at different points, window performance, brightness of the light in the cupboard are tested in the working situation, with all doors of the room closed. Control of the frequency and method of cleaning the interior is also important.
Validation of the velocity of the incoming air in the area under the sash and validation of the volume of the exhausted air is not sufficient proof of the safety of the fume cupboard. The quality of design of a good fume cupboard is as important as it guarantees a stable vortex of the airstream. A good technical design of the ventilation system is essential too, as is the dimensioning of the interior of the fume cupboard itself. Last but not least: without good operating procedures and trained operators a good technical design is useless.
The main goal of the operation within a fume cupboard is that it will not be possible for contaminated air to enter the area or room outside the fume cupboard.
Never start activities in a brand new fume cupboard with certificate of the manufacturer only, because on site initial qualification and validation of the performance and proper training of the operators is essential.
For initial validation (and periodical revalidation) mostly a combination of tests is carried out:
Validation of the velocity of the exhausted air in the opening under the glass window and validation of the volume of the exhausted air (extract volume flow rate test).
Containment testing – sometimes this test shows initially differences between test results in the test environment of the manufacturer (as built) and the results obtained in the pharmacy or in the laboratory of the end user (on site, as installed).
The test protocol of European Standard EN 14175-4 [4].
28.3.2.3 Operation
It is important not to disturb the performance and airflow pattern of the fume cupboard. Staff standing or walking in front of the fume cupboard will disturb the air exhaust. The operator must have sufficient space in front of the fume cupboard to work easily and comfortable. Room doors that open frequently during operation in a fume cupboard and (strong) inflowing air from the room ventilation system (in the direction of the fume cupboard) may have a negative impact on the performance of the fume cupboard. Airflow visualisation with smoke is illustrative and often necessary.
28.3.3 Moveable Exhaust Equipment
28.3.3.1 Applications
Moveable extraction equipment can be used for the local and small scale exhaust of fumes and vapours at the point where these fumes and vapours are produced in an environment with no classic fume cupboard available. For example the handling of organic solvents in a laboratory, near the analysis equipment.
An extraction duct may not be the best choice for the extraction of powders and dust. However, by placing the hood very close to the point where the dust is produced we can create a situation with high air velocity and an effective exhaust for dust. In that case the exhaust duct is a dust remover, but eventually without a dust collector bag for the dust. A problem is that collected dust in the duct or the hood can fall back on (other) products. This is a serious risk for cross contamination and needs a proper cleaning schedule in place.
A better solution for exhausting dust and powder is combining the exhaust unit with filters, see Fig. 28.1b. Contaminated air enters the pick-up hood and is drawn through the hose and into the dust containment unit. The flexible duct with pick-up hood is easily adjusted to any position by an externally mounted, self supported, adjustable arm. Larger, heavier particles are collected in a removable collection pan for easy maintenance. The first stage of filtration is a pleated pre-filter, designed to capture mid-sized particles before reaching the main filter therefore extending the life of the main filter. The main filter is a high efficiency 95 % filter designed to capture fine particulate before being exhausted. Other main filter options are available including a 99.97 % efficient HEPA Filter. Clean filtered air is returned to the environment.
Professional dust removers are used in tableting, capsule filling and closing machines and powder filling machines. They are used to clean the equipment during processing or to remove adsorbed dust and powder from the pharmaceutical product. Dust removers are not designed to extract fumes, because fumes pass the filter unit and are blown back in the room.
Mobile dust removers (vacuum cleaners) with integrated HEPA filter are used in clean rooms, most of the time to clean the floor and ceilings. Dust removers are not designed to extract fumes, because fumes pass the filter unit and are blown back in the room. The HEPA filter has to be replaced periodically.
28.3.3.2 Description
Extractors for industrial or laboratory environments are available in several duct diameters (Ø 75–200 mm), duct materials and sizes, with various constructions for ceiling, wall and bench installations. The standard model for fume extraction is used in most laboratory environments. The joints are made from polypropylene and ducts from anodised aluminium, for example. Polypropylene PP is used in environments containing high concentrations of corrosive pollutants; joints and tubes are made from polypropylene. ATEX material is used where hazardous explosive atmospheres may occur (see Sect. 26.11); joints and tubes are made from conductive polypropylene.
28.3.4 Powder Exhaust Units
28.3.4.1 Application
Powder exhaust units are often benches with horizontal backward flow and final vertical HEPA filters (see Fig. 28.1c), suitable to protect the operator largely from fine powder particles in the air or from water-based aerosols that otherwise would be released in the working area. These exhaust units might recirculate the exhausted air and pollutants can (also through basic filtration material) enter the room. In a Wibojekt® powder exhaust units the extracted air with particles is blown towards a special slit. That air is filtered and exhausted outside the room.
The filtration efficiency depends on the type of filter but is as said above generally expected to establish a ten-fold reduction of exposure.
These types of exhaust units usually don’t have a duct leading to the outside of the building and therefore are not suitable for the extraction of gasses, fumes and volatile products.
28.3.4.2 Description
Fine dust particles or small aerosol droplets generated in a powder exhaust unit must be extracted from the operators working space horizontally in the backward direction. The airflow is sometimes downwards into a special slit (Wibojekt®).
After passing a coarse pre-filter and a final ULPA filter the exhausted air can be exhausted into the preparation room. It that case the unit is recirculating the air. It is possible to discharge the air via a duct outside the building. As a result the room pressure will become lower.
The efficacy of an exhaust unit depends on the air velocity in the unit. For that reason the area of the filters is not too small. Settled dust cannot be exhausted once it has fallen down onto the horizontal work area in the unit.
The place in the room where the exhaust unit is installed and qualified has to be chosen carefully. A recirculating exhaust unit needs enough space to blow the exhausted air around the unit. An exhaust unit very close to a door will be influenced by the changing air pattern every time the door swings open or is closed.
The velocity of the incoming air stream in an exhaust unit must be between 0.25 and 0.50 m/s, with no major disturbing air pattern around or in front of the exhaust unit. A higher exhaust velocity causes unwanted turbulence before and in the unit.
Weighing in an exhaust unit is possible. Dependent on the results of the accuracy of the weighing tests it can be necessary to shut down the exhaust unit at the very moment that the weighing result is recorded.
28.3.4.3 Operating Instructions
Switch on the exhaust unit just before starting the activities. Clean the unit inside before and after activities.
Check the velocity meter. Check the status of the filtration area, no damage may be seen.
Check the unit once a year on air velocity; a leak test for HEPA or ULPA filters is easy to perform by an expert.
Change all pre-filters and the HEPA filter only after leakage or damage.
28.3.4.4 Replacement of the Pre-Filters
The pre-filters have to be changed when after a visual check the pre-filter is dirty or saturated, or after a chosen time interval (once per 1–3 months for example).
During a change of the pre-filter the operator has to wear a protective P2- or P3 mask (see Sect. 26.4.1) for dust and aerosols. The exhaust unit fan is switched on, so dust particles are trapped in the HEPA or ULPA filter cassette. Clean the filter frames and remove the old filters in a closed bag.
28.3.5 Laminar Airflow Units
A Laminar airflow unit, also called laminar flow -cabinet, -closet, -hood or -bench is a general and rather non-specific term for an enclosed workbench, with a HEPA filtered laminar airflow inside.
The laminar airflow is unidirectional, so not turbulent. This is achieved by choosing the right design, technology, air velocity and filter sets. This unidirectional airflow must not be disturbed too much by the environment or movements of the operator. So a specific working technique and behaviour for the operator(s) is necessary. The direction of the filtered and clean laminar airflow can be horizontal (from the left to the right or from the back of the cabinet towards the operator), or downwards: from the HEPA filter in the top of the cabinet to the bottom (which often is a flat stainless steel work area). See Fig. 28.1d and e. In pharmaceutical terminology: HEPA filtered horizontal or vertical laminar airflow (cross- or downflow) in a laminar flow bench creates an ISO 14644-1 (Class 5) / GMP Annex 1 (Class A) work area and prevents contaminated ambient air entering the work area. With the right working techniques, a trained operator and the right classified background this can result in good product protection.
28.3.5.1 Application
In pharmacies a laminar flow unit is used to protect the product against microbiological contamination from the operator. With a cross flow LAF cabinet the HEPA filtered air is directed over the working area to the operator. This type of LAF bench thus cannot be used for operations with hazardous substances (hazardous being defined as any substance with a H statement, so with a hazard class higher than one, see Sect. 26.3.1). It can be used for aseptic preparation processes with closed systems, such as aseptic handling, see Chap. 31.
For larger equipment a down flow LAF unit is common, e.g. a HEPA plenum in a preparation area for sterile products. A HEPA plenum with plastic curtains mounted in and hanging from the ceiling creates a dedicated area for aseptic processes. A plenum can be used for example to protect washed and opened glass infusion containers, moving in a filling line in the downflow of the plenum to the point of aseptic filling. As said, it depends on airflow patterns if any substance is actively blown in the direction of the operator. If so, the exposure may be higher than when no ventilation or exhaust takes place. This means that a down flow LAF unit cannot be used for open processing substances with a hazard class higher than one.
28.3.5.2 Description
In general, the air from the production area enters the front of the LAF cabinet in a controlled way, passes at first a set of pre-filters in the cabinet that separates coarse dust. Sometimes more HEPA filters placed in series after the pre-filters act as supplementary pre-filters (in certain types of safety cabinets). After pre-filtration the air is forced via a ventilator box through a set of framed HEPA filters and finally enters the aseptic process area as sterile filtered air in a unidirectional flow. The speed of the unidirectional flow is kept between limits. Finally the exhaust air re-enters the room (crossflow LAF units), or can be exhausted to the outside with or without extra HEPA filtration (safety cabinets).
With these principles in mind horizontal crossflow LAF cabinets, downflow LAF cabinets, downflow safety cabinets or downflow LAF units with a large area (HEPA filter plenums) are constructed.
The exact positioning of pre-filters in a LAF cabinet depends on the brand and type of the LAF cabinet and is an important part of the functional and detail specifications of it.
Testing of HEPA Filter Units
Filter efficiency, dust holding capacity and differential pressure changes are tested frequently.
HEPA filters can be tested with different methods. A wide range of test equipment for on-site measurements include particle counters, pressure gauges, airflow meters, energy data loggers, corrosion monitors and gas analysis equipment. One of the tests is the measurement of penetration of dispersed oil particles (DOP) through the HEPA filters. DOP used to be the abbreviation of DiOctylPhtalate, which however has been replaced by safer products.
By dispersing the oil aerosol towards the HEPA filters in the air channel the testing operator can measure how many particles penetrate the HEPA filter and can be counted at the clean part of the HEPA filter. According to ISO 14644-3 the filter area is scanned in small well-defined sequential parts. This percentage penetrated particles can be dependent on the exact position on the filter where the particle counter measures. Inferior and good parts of the filter area are detected and the position is documented. The condition of the filter is expressed as percentage penetration giving filter efficiency. The penetration is the percentage of the particles that passed; the filter efficiency is the part that was blocked by the filter material. The efficiency for the most penetrating particle in a H14 HEPA filter can be 99,995 % and for the particles with a size larger than 0.3 μm the efficiency can be 99,999 % or more. Small defects in the filter can be repaired by a professional operator.
Other important functional details of LAF cabinets are:
The light intensity in the cabinet, measured on the work spot must be sufficient to reach a minimum level of 1,000 lux. The lighting unit must be built inside the cabinet and the frame of it must be easily cleaned and disinfected.
The speed of the ventilator must be adjustable, and automatically controlled in order to reach the required quality of laminar flow and speed.
Detection of full speed, half speed, on and off or night function.
The speed of the unidirectional flow must be monitored and shown on a display to detect disturbances in the flow by a clogged filter or a defective ventilator.
To keep the flow as unidirectional as possible a minimal number of extra utilities inside the working area of LAF cabinet are allowed. Extra utilities might be:
Nitrogen and compressed air valves, for membrane filtration devices.
Vacuum valve, used only in dedicated LAF units for microbiological quality control: the filtration of fluids for sterility testing or bioburden control.
Electricity sockets.
Electronic balances. They can be used inside the LAF cabinet but give disturbance of the laminar airflow and in return the LAF cabinet might disturb the weighing result. Use only following a risk analysis.
Clamps outside on the front of the LAF unit, to attach temporary documentation.
A stainless steel rail with hooks in the LAF area to attach infusion bottles and bags for the aseptic processing.
Computer monitor for instructions.
(Continuous) monitoring equipment.
It is advised to require silent, modern ventilators. The expected daily noise of a LAF unit in operation must be reasonable low and specified in dB. The best solution is to choose a cabinet ventilator with enough spare capacity. In that case the ventilator will not work at the maximum capacity and the noise level in dB will be reasonable or low.
A laminar flow cabinet will continuously produce heat from the ventilators. If the exhaust airflow from the LAF unit is returned into the room (recirculation), the temperature in the room will rise and more room ventilation and cooling is necessary. Air exhaust to outside the room will give less heating of the room.
28.3.5.3 Operating instructions
Commonly two operators are at work in a LAF cabinet. One is the operator, working with the arms and hands inside the cabinet. The second person is standing aside, supporting and controlling the operator, or supporting two operators working simultaneously in two different cabinets.
These persons must move gently in the room. Opening a door will have some effect on the balance of the airflow in the cabinet. So try to avoid opening clean room doors during aseptic processing.
Spillage of material must be removed as soon as possible for example with a cloth wetted with disinfectant.
The interior of the LAF cabinet (horizontal bench, two sides left and right and the back inside of the bench) is disinfected with alcohol 70–80 % at the end of each working session (shift of about two hours) and at the end of the working day. For LAF benches that keep running 24 h a daily disinfection of the horizontal working bench only between sessions and before start of the activities the next morning might be allowed. This decision is based on a risk analysis, and might be allowed because the rest of the interior was disinfected at the end of the past working day. In addition on disinfection the interior must be cleaned frequently with lukewarm water and a detergent, followed by a disinfection.
LAF cabinets that do not run 24 h a day must be switched on first; after 15 min operating at full speed the cabinet must be disinfected and can be used.
Disinfection efficacy must be proved with contact plates (RODAC plates, see Sect. 31.6); specifications of the results can be found in Annex 1 of the European GMP.
Validation of the aseptic process can be found in Sect. 31.6.2.
28.3.5.4 Qualification of a LAF Unit
Once or twice a year (depending on the criticality of the processes) the LAF cabinet is inspected, calibrated and qualified. Commonly a contract is signed with a specialised external firm for this.
The following aspects are important in qualification:
Inspection and installation of new pre-filters. Sometimes the filters are grey or coloured, as proof of the need of change.
Efficacy of the HEPA filters. It is not necessary to change the HEPA filters too often. Change of a HEPA filter is expensive and must be a result of documented defects that cannot be repaired.
Air velocity.
Intensity of the light.
28.3.6 Safety Cabinets
28.3.6.1 Application
A safety cabinet is a laminar down flow cabinet, which is constructed specifically for protection of both the sterile product and the operator. It is frequently used in (hospital) pharmacies for aseptic preparation (when products are not fully closed) and for aseptic handling of class 4 or 5 substances (see Sects. 26.5.2 and 26.8). Laminar down flow has the advantage compared to cross flow that the operator does not feel the continuous flow in his direction. Other names for a safety cabinet are: biosafety cabinet, biosafety bench, biohazard bench, biohazard cabinet, biological safety cabinet etc.
In safety cabinets with a “slope” glass window the operator works with both arms under the window into the half-open sterile working area.
28.3.6.2 Description
The air within a safety cabinet comes from the HEPA filter in the top of the cabinet (see Fig. 28.1f). The flow is led into exit grills at the back and the front of the work bench. A second airflow is drawn from the working room into the front grill where the elbows of the operator are. This flow prevents air or aerosols from the working area escaping the cabinet and protects the operator from inhaling aerosols. After being collected through the slits the air is prefiltered through coarse disposable filter material situated under the work bench in a tray.
In safety cabinets of the type partial or total exhaust, the air eventually is collected in a box on top of the bench, connected via a HEPA-filter with the air in the room (see Fig. 28.1f). The box has underpressure due to the exhaust air velocity. In case the safety cabinet has a breakdown, the box construction prevents the ventilator of the exhaust channel to continue while the down flow ventilator in the cabinet stops. Otherwise contaminated air from the room would be sucked under the sash, contaminating the clean side of the HEPA filter in the work area of the safety cabinet.
28.3.6.3 Specifications and Classification
The specifications of the airflow pattern in a safety cabinet might be confusing. Following EN 12469 (Biotechnology – Performance criteria for microbiological safety cabinets) [5] the velocity of the incoming room air under the glass panel must be between 0.4 and 0.7 m/s; the mean downflow velocity must be between 0.25 and 0.50 m/s, with no individual measurement outside +/− 20 % of the mean. However, in pharmacy the GMP [6] takes precedence. In Annex 1 the down flow air velocity differs somewhat from the EN 12469. The mean velocity for the down flow in Annex 1 (Class A) must be 0.45 m/s +/− 20 %. It is important to stress GMP compliance during installation and initial qualification of a new safety cabinet in a pharmaceutical environment.
The air in a safety cabinet is filtered through pre-filters and HEPA filters so the resulting workspace inside the bench complies to GMP Class A. All safety cabinets of type II are built with a HEPA filter at the point where the used air is finally expelled through the exhaust channel. This is an extra HEPA barrier, preventing aerosols contaminating the HVAC system.
Classification of Safety Cabinets
Safety cabinets must comply to Class II of the European Standard EN-12469. Some types comply moreover to the German DIN 12980. Document your specifications well before purchase and be aware that in pharmacy practice a down flow velocity of the air in a safety cabinet must comply with current GMP. Communication about GMP is very important, because these safety cabinets are used in non-GMP laboratories too.
The Classification IIA and IIB is not found in the EN-12469 but in US-CDC guidelines (see further down). In a Class IIA cabinet the (potentially contaminated) air from the work bench is led without filtration to the last exhaust HEPA filter; in this way the ventilator compartment can be contaminated after sustained use of this type of safety cabinet. In Class IIB cabinets an extra HEPA filtration cassette is placed below the work bench; as a result HEPA filtrated (potentially contaminated) air from the work bench enters the ventilator part before it passes the last HEPA exhaust filter. The ventilator compartment remains cleaner by this extra HEPA filtration step. The environment is better protected, as well as service personnel working inside the safety cabinet.
Safety cabinets placed in a room with underpressure (for the preparation of radiopharmaceuticals for example) must have an extra exhaust ventilator, discharging the exhaust air outside the building. This exhaust ventilator must be tested also in daily practice and at periodical electricity break tests. Safety cabinets have visual and acoustic alarms that warn for deviations in airflow (down flow and in flow alarms).
The classification by the U.S. Centers for Disease Control and Prevention (CDC) is to be found in Appendix C: Types of Biological Safety Cabinets (BSC) of the draft USP monograph Hazardous drugs – handling in healthcare settings [7]. Terminology (biological safety) may be confusing but is historically determined: the first safety cabinets were developed for working with dangerous microbiological materials. The classification of the cabinets is based on their technical construction which is described in this Appendix. The fields of application are suggested for each class.
Class I: A BSC that protects personnel and the environment but does not protect the product/preparation. Personnel protection is provided when a minimum velocity of 75 linear feet/min of unfiltered room air is drawn through the front opening and across the work surface. The air is then passed through a HEPA/ULPA filter either into the room or to the outside in the exhaust plenum, providing environmental protection.
Class II: Class II (Types A1, A2, B1, and B2) BSCs are partial barrier systems that rely on the movement of air to provide personnel, environmental, and product/preparation protection. Personnel and product/preparation protection is provided by the combination of inward and downward airflow captured by the front grid of the cabinet. Side-to-side cross-contamination of products/preparations is minimised by the internal downward flow of HEPA/ULPA filtered air moving toward the work surface and then drawn into the front and rear exhaust grids. Environmental protection is provided when the cabinet exhaust air is passed through a HEPA/ULPA filter.
Type A1 (formerly, Type A): These Class II BSCs maintain a minimum inflow velocity of 75 ft/min, have HEPA-filtered, down-flow air that is a portion of the mixed down-flow and inflow air from a common plenum, may exhaust HEPA-filtered air back into the laboratory or to the environment through an exhaust canopy, and may have positive-pressure contaminated ducts and plenums that are not surrounded by negative-pressure plenums. They are not suitable for use with volatile toxic chemicals and volatile radionucleotides.
Type A2 (formerly, Type B3): These Class II BSCs maintain a minimum inflow velocity of 100 ft/min, have HEPA-filtered, down-flow air that is a portion of the mixed down-flow and inflow air from a common exhaust plenum, may exhaust HEPA filtered air back into the laboratory or to the environment through an exhaust canopy, and have all contaminated ducts and plenums under negative pressure or surrounded by negative-pressure ducts and plenums. If these cabinets are used for minute quantities of volatile toxic chemicals and trace amounts of radionucleotides, they must be exhausted through properly functioning exhaust canopies.
Type B1: These Class II BSCs maintain a minimum inflow velocity of 100 ft/min, have HEPA-filtered down-flow air composed largely of uncontaminated, recirculated inflow air, exhaust most of the contaminated down-flow air through a dedicated duct exhausted to the atmosphere after passing it through a HEPA filter, and have all contaminated ducts and plenums under negative pressure or surrounded by negative-pressure ducts and plenums. If these cabinets are used for work involving minute quantities of volatile toxic chemicals and trace amounts of radionucleotides, the work must be done in the directly exhausted portion of the cabinet.
Type B2 (total exhaust): These Class II BSCs maintain a minimum inflow velocity of 100 ft/min, have HEPA-filtered down-flow air drawn from the laboratory or the outside, exhaust all inflow and down-flow air to the atmosphere after filtration through a HEPA filter without recirculation inside the cabinet or return to the laboratory, and have all contaminated ducts and plenums under negative pressure or surrounded by directly exhausted negative-pressure ducts and plenums. These cabinets may be used with volatile toxic chemicals and radionucleotides.
Class III: The Class III BSC is designed for work with highly infectious microbiological agents and other hazardous operations. It provides maximum protection for the environment and the worker. It is a gas-tight enclosure with a viewing window that is secured with locks and/or requires the use of tools to open. Both supply and exhaust air are HEPA/ULPA filtered. Exhaust air must pass through two HEPA/ULPA filters in series before discharge to the outdoors.
28.3.6.4 Operation Instructions
The operational aspects of maintenance and calibration for safety cabinets are almost the same as for cross flow laminar airflow units (see Sect. 28.3.5). Additionally the inflow as protective barrier has to be measured.
Daily cleaning and disinfection of the interior of a safety cabinet is important. The tray under the work bench as well as the pre-filter contains spilled fluids. This area has to be cleaned and disinfected at least once a week wearing a P3 mask (see Sect. 26.4.1) and protective impermeable clothing. The pre-filters must be changed every 3–6 months; the HEPA filters must be changed only after significant failure at qualification tests, repair being not possible any more.
28.3.6.5 Qualification
The protection performance of a safety cabinet is given by the so called Protection Factor, which is determined by the Potassium Iodide test. Potassium Iodide solution is dropped on a spinning drive. An aerosol inside the work area of the cabinet is formed; some droplets are forced in the direction of the protecting air curtain. The number of aerosol particles inside the bench is counted (A). Outside the cabinet (where the operator normally is sitting) the number of aerosol particles that escaped the air curtain in front of the bench is counted again (B). A/B is the protection factor. The protection factor has to be at least 1.5 × 105.
A second test is a test with spores of bacteria. This is a factory test for obvious reasons, see EN-12469.
The potassium Iodide test is time-consuming. This test is performed in OQ/PQ qualification or when possible harm could have occurred, for instance when the cabinet is moved to another place.
28.3.7 Isolators
An isolator, as is in its name, offers physical isolation of the operator from the product. It offers complete containment (see Sect. 26.7.1). Its presence in pharmacies differs considerably between countries.
In industry an isolator technique is often used for critical aseptic processes. Other techniques with robots and barrier system isolator technology are in use also. Isolators for aseptic manufacturing can be placed in class C or D clean rooms, whereas LAF cabinets should be placed in GMP class B.
28.3.7.1 Description
An isolator is according to the description of EN-12469 a Class III safety cabinet, as said a complete physical barrier, see Fig. 28.1g. The air inside the isolator is HEPA filtered, so inside the isolator a GMP Class A air quality is maintained. The gloves or full or half suits are the physical barrier between the sterile product inside the isolator and the operator standing outside and the integrity of this barrier requires very much attention.
The main compartment of an isolator is often made of stainless steel and has two rubber gloves in the front of a clear viewing panel. The HEPA filtered airflow can be laminar or turbulent.
The pressure inside the main compartment is higher or lower than the background area of the isolator. Containment isolators often employ negative internal air pressure and most isolators use positive pressure for aseptic processing. A sporicidal process, usually delivered by gassing can be used to aid microbiological control. A gas generator delivers the gas (e.g. peracetic acid or hydrogen peroxide) via defined ducts [8].
If the isolator is only used for non-hazardous products the exhaust air can be discharged into the background area. However, commonly the air is discharged outside the building.
Some isolators have a modular construction for many different kind of applications. Sometimes an extra HEPA filter is built in, underneath the working surface. An isolator may have no, one or two hatches, constructed as a lock. The hatches may have their own HEPA filters and have a door to the main compartment and another door to the background area. The isolator has an interlock system for the hatches to prevent loss of air pressure. As an alternative for the hatches special isolator transport and loading boxes can be used with a tight (screw) fitting to the main compartment (‘mousehole’). In practice the terms ‘open’ and ‘closed’ isolators are used. In ‘closed’ isolators all materials are inside the isolator during the gaseous disinfection and the aseptic handling is done without opening hatches or mouseholes.
The operator wears disposable gloves and puts the hands and arms in the long rubber isolator gloves, which have inflatable gaskets for tight fitting to the isolator. Half or full suits are also a possibility.
The isolator gives an acoustic alarm when the pressure drops or with other deviations.
Maintenance or repair of an isolator has to be done with gloves, a protective mask and protective clothing. Change of HEPA filters has to be done very carefully and with qualification after replacement. Further descriptions can be found in [8].
28.3.7.2 Using an Isolator
After delivery of a new isolator a qualification protocol is followed (see Sect. 34.15). The interior of the isolator must comply to GMP Class A (particles and microbiological tests). A program to minimize the risk of loss of integrity of gloves, sleeves and suits should be present including operator practice, vigilance and the absence of sharp edges. The glove ports and, if applicable, the suits present particular risk because they are more prone to damage and if not noticed will contaminate the product. Transfer of material in and out should not compromise the critical zone. The transfer is especially critical if no gassing is used. In that case a proper disinfection procedure such as used in normal LAF has to be used.
As the absence of micro-organisms is expected, the question of laminar versus turbulent flow and the strict application of aseptic procedures during operations might be irrelevant.
The isolator and gloves are tested daily for leakage. Airflow velocity if applicable is measured in-line with a calibrated instrument. The pressure inside the isolator is checked continuously. Furthermore, gas detection in case gaseous disinfection is used.
Before working the inside of the isolator has to be cleaned and disinfected. Disinfection can be done with peracetic acid or hydrogen peroxide, using special disinfection devices and procedures. For small scale or incidental use ethanol 70–80 % may be used as an alternative.
28.4 Apparatus for the Production of Pharmaceutical Water
Water is the most important pharmaceutical substance. The requirements to be met are being discussed in Sect. 23.3.1. The equipment for storage and distribution (loop system, pump and storage vessel) is considered as a built-in installation and therefore is discussed in Sect. 27.5.2. The development of biofilms is discussed in Sect. 19.3.5.
Pharmaceutical water (Ph. Eur.) is produced by a multi-staged process using different techniques with different apparatus in series [9, 10]. In this section those different apparatus producing water with a pharmaceutical quality are discussed, e.g.:
Water softeners
Demineralisation apparatus based on ion exchange
Apparatus for reverse osmosis
Apparatus for electro-deionisation
Distillation apparatus
28.4.1 Water Softeners
28.4.1.1 Application
The water softening process removes most calcium and magnesium ions from tap water. By doing so a downstream placed apparatus, such as reverse osmosis, electro-deionisation or distillation apparatus, is protected against the deposit of calcium and magnesium salts (‘limescale’).
28.4.1.2 Description
The principle of a water softener is based on ion exchange using synthetic resins. The synthetic resin has negatively charged functional groups with sodium as a counter ion. Calcium and magnesium ions from the water are exchanged for the sodium ions of the resin. Therefore, this type of water softeners is called cation exchangers. See Sect. 23.3.1 for the hardness degrees. The resins pearls do not retain any other contamination such as solid particles.
28.4.1.3 Operating Procedure
Water softeners must be regenerated periodically. This regeneration involves the immersion of the resin, being saturated with calcium and magnesium ions, in a concentrated sodium chloride solution (brine). This brine is prepared and kept in a separate vessel. The calcium and magnesium ions bound to the resin will exchange with the sodium ions in the brine. After regeneration the brine containing calcium and magnesium must be flushed thoroughly. Often the softening apparatus is provided with fully automatic regeneration equipment. In that case regeneration will occur periodically or be triggered by an in-line hardness tester.
Larger installations for continuous water purification usually have two automated softening apparatus mounted in a parallel arrangement. As soon as one of them has to be regenerated an automated control system will switch that water softener off. The other one will continue delivering soft water in the meantime.
Water softeners are a good substrate for bacteria. Therefore, apart from being regenerated, the system must be disinfected periodically as well. Some (automated) softeners can generate chlorine gas from the brine solution during regeneration. This chlorine gas dissolves in the water as hypochlorite and acts as a disinfectant. All chlorine must be flushed away thoroughly after the combined regeneration and disinfection process.
The quality of the water will be controlled by means of pressure and flow meters and by a hardness tester. The hardness tester consists of an automated titration apparatus. The reservoir, with combined titre and indicator solution, should be refilled regularly.
28.4.2 Demineralisation Apparatus Based on Ion Exchange
28.4.2.1 Application
Purified water (Ph. Eur.) can be produced from tap water or from pre-softened tap water by demineralisation. As this production method easily leads to microbiological growth the product will not always meet the microbiological requirements. Passing through a bacteria retentive filter may render the demi-water compliant. However this treatment should be monitored because of micro-organisms growing through the filter. Endotoxins will not be removed by filtration.
28.4.2.2 Description
Ion exchangers can be applied both as a water softener (see Sect. 28.4.1) and as a demineralisation apparatus. After softening of tap water, calcium and magnesium ions have been removed; however any other mono and bivalent ions (cations such as potassium and sodium and anions such as nitrate, chloride, sulphate, bicarbonate and carbonate) have still to be removed in order to obtain Purified Water Ph. Eur. This process is called deionisation or demineralisation. It proceeds at room temperature. Demineralisation apparatus based on ion exchange consist of columns filled with several varieties of synthetic resin pearls that remove unwanted ions from the water by exchanging them for hydrogen and hydroxyl ions. The general principle is that all cations are being exchanged for hydrogen ions and all anions for hydroxyl ions. Finally the recombination of hydrogen and hydroxyl ions results in pure water.
An ion exchange resin is a synthetic resin with positively and negatively charged functional groups. The demineralisation process (which might proceed over one combined or over separate columns) exchanges cations from the water for hydrogen ions from the cation exchange resin and anions from the water for hydroxyl ions from the anion exchange resin. Exemplified (s = solid):
Any bivalent anion, e.g. sulfate, exchanges for 2 hydroxyl ions in a anion exchange resin.

Two different types of anion resin are used for demineralisation: weak basic and strong basic exchange resins. Both types exchange anions such as chloride, sulfate, bicarbonate and carbonate for hydroxyl ions. However strong basic exchange resins can additionally exchange silicic acid and silicates for hydroxyl ions.
The quality of demineralised water depends on several factors, such as the quality of the feeding water, the type of exchange resin, the quantity of resin and the number of resin containing tanks.
In a mixed-bed demi-tank or column, cationic resins and anionic resins are thoroughly mixed in just one container. The alternating cationic – anionic resin pearls in one column can provide water of excellent quality. A mixed bed column can achieve a water quality with a conductivity of less than 1 microSiemens/cm.
Dual-bed demineralisation columns consist of two serially arranged containers, one with cationic resin and one with anionic resin pearls. A dual-bed weak basic demi-column delivers water with a conductivity of approximately 20 microSiemens/cm. A dual-bed strong basic demi-column delivers water of approximately 5 microSiemens/cm.
An ion exchange demineraliser has to be regenerated periodically by flushing the resin pearls with a highly concentrated regeneration fluid. The type of regeneration fluid depends on the specific type of ion exchange resin. Commonly a solution of sodium hydroxide or hydrochloric acid is used. Afterwards, the regeneration medium has to be flushed thoroughly and the ion exchanger can be reused again. Regeneration sometimes takes place at the site of the user, sometimes used columns are exchanged for regenerated ones by the supplier.
28.4.2.3 Operating Procedure
The quality of the water is controlled with conductivity meters, pressure meters and flow meters.
If the feed water contains a relatively high concentration of dissolved substances a dual-bed system is usually preferred. If the feed water contains low concentrations a mixed bed ion exchange demineralisation will be preferred. As said above for water softeners, the resins pearls in a demineralisation column do not retain any other contamination such as solid particles. They constitute a rather good substrate for the growth of bacteria; mixed bed systems are even more vulnerable. The investment costs are comparatively low in contrast to the relatively high operational costs including regeneration. If the installation must produce Purified Water Ph. Eur. the microbiological quality has to be monitored or the bacteria filter has to be changed frequently.
28.4.3 Apparatus for Reverse Osmosis
28.4.3.1 Application
An apparatus for reverse osmosis removes more than 95 % of all ions and more than 99 % of all particles, colloids and dissolved organic material including endotoxins. Nevertheless the permeate still contains too much small, univalent ions to comply with the requirements for purified water after one filtration step. Therefore, reverse osmosis is often used as a preliminary treatment, preceding distillation or demineralisation. The available reverse osmosis systems will only be economically feasible if a rather large amount of purified water is required. As an example reverse osmosis installations are being used, in combination with other purification methods, as a preliminary treatment in the production of Water for Injections and in the production of purified water for haemodialysis. Sometimes purified water is prepared using just a series of semi-permeable membranes. Reverse osmosis has the advantage compared to demineralisation that few chemicals are being consumed. However, as the process does not involve any heating, a substantial risk exists of microbiological contamination and biofouling.
28.4.3.2 Description
Reverse osmosis utilises semi-permeable membranes. The name “reverse osmosis” (abbreviated as “RO”) uses the fact that the osmotic pressure building up over a semi-permeable membrane has to be overcompensated. In a reverse osmosis process the water is forced by high pressure to flow through a semi-permeable membrane thereby eliminating any particle or larger ion, see Fig. 28.2
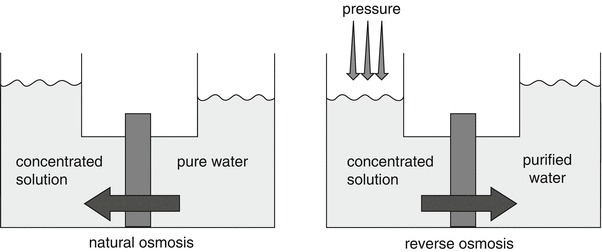
.
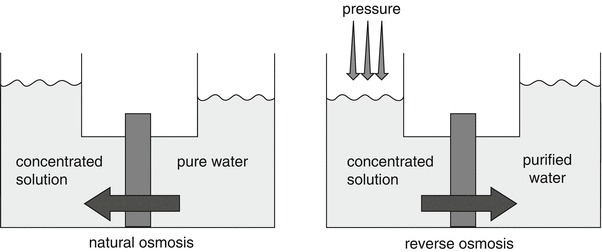
Fig. 28.2
Principle of reverse osmosis. Source: Recepteerkunde 2009, ©KNMP
RO membranes are designed to pass water through the intersegmental space between the polymer molecules. This space is wide enough to allow individual water molecules to pass, but too small for any hydrated ions. Because the system has many additional surfaces beyond the membrane, on which undisturbed biofilms could built up, the prevention of microbiological contamination in a reverse osmosis system is a challenge. Biofouling is effectively limited by a smart choice of materials and by avoiding blind angles, however still intensive control is mandatory.
28.4.3.3 Operating Procedure
Apparatus for reverse osmosis can function for a long time without much maintenance. The semi-permeable membrane should be replaced periodically because of ageing. The average lifetime of a membrane is 2–3 years.
During the first start-up a balance has to be found between the amount of water being produced as permeate and the amount that is flushed away as concentrate. Usually an optimal result in water quality and quantity will be achieved when approximately 10 % of the feed water is drained away as concentrate. By choosing a higher percentage the quality of the permeate might increase. However, this will have a negative impact on the yield of the installation. A lower concentrate percentage will decrease the quality of the permeate.
Most attention should be paid to the microbiological quality of the water. Again a well-monitored bacteria retentive filter can be significant.
28.4.4 Apparatus for Electro-Deionisation
28.4.4.1 Application
Electro-deionisation (EDI) is used in combination with other purification methods. Electro-deionisation is applied to the production of Purified Water Ph. Eur. or Highly Purified Water Ph. Eur. Highly purified water may be used in the haemodialysis department for in-line production of dialysis fluids for continuous dialysis. EDI in combination with other techniques can be used for in-line dialysis, it requires thorough in process controls. A distillation apparatus, suitable for water for injection, would not comply the large peak demand at dialysis unless equipped with a very large storage vessel and an extremely powerful (energetically unrealistic) cooling system.
Sometimes hospital pharmacies use an EDI installation for the preparation of water for pharmaceutical non-sterile stock preparations.
28.4.4.2 Description
Electro-deionisation (EDI), also called continuous electro-deionisation (CEDI), is a special type of demineralisation.
The apparatus using this technique is equipped with mixed resin pearls and selectively permeable membranes. It functions by applying an electrical current fed through resin and membranes. The feeding water will be normally deionised by flushing through the resin. However, the “captured” ions subsequently do not stick to the resin, but are being removed under the influence of the applied potential difference and drained through the selectively permeable membranes. The potential difference also splits a part of the pure water into H+ and OH− ions that regenerate the resin at their turn, see Fig. 28.3.
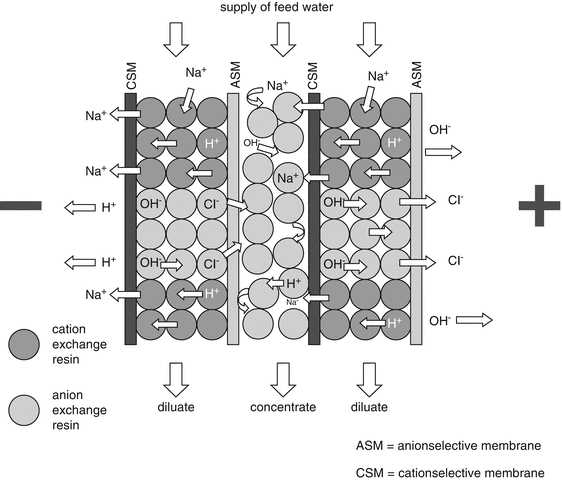
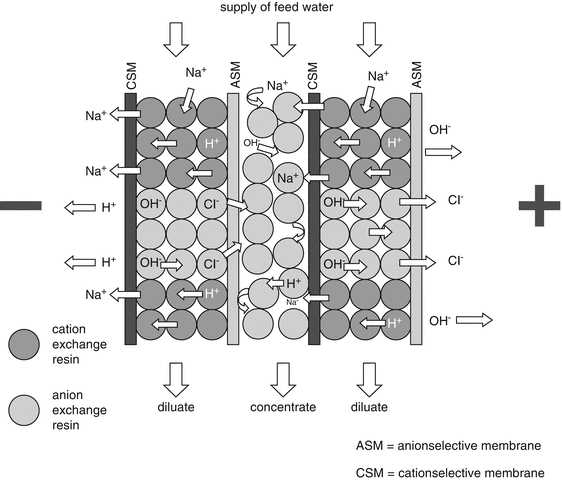
Fig. 28.3
Principles of electro-deionisation. Source: Recepteerkunde 2009, ©KNMP
The potential difference and the pH-gradient impede the growth of micro-organisms additionally, but the risk of growth of micro-organisms still exists.
28.4.4.3 Operating Procedure
A (C)EDI-installation requires relatively limited maintenance efforts. To maintain the potential gradient a pure sodium chloride solution has to be fed behind the selective permeable membrane. This sodium chloride solution is drained away with a part of the feed water. The stock sodium chloride must be refilled regularly. The product water should be checked for its conductivity.
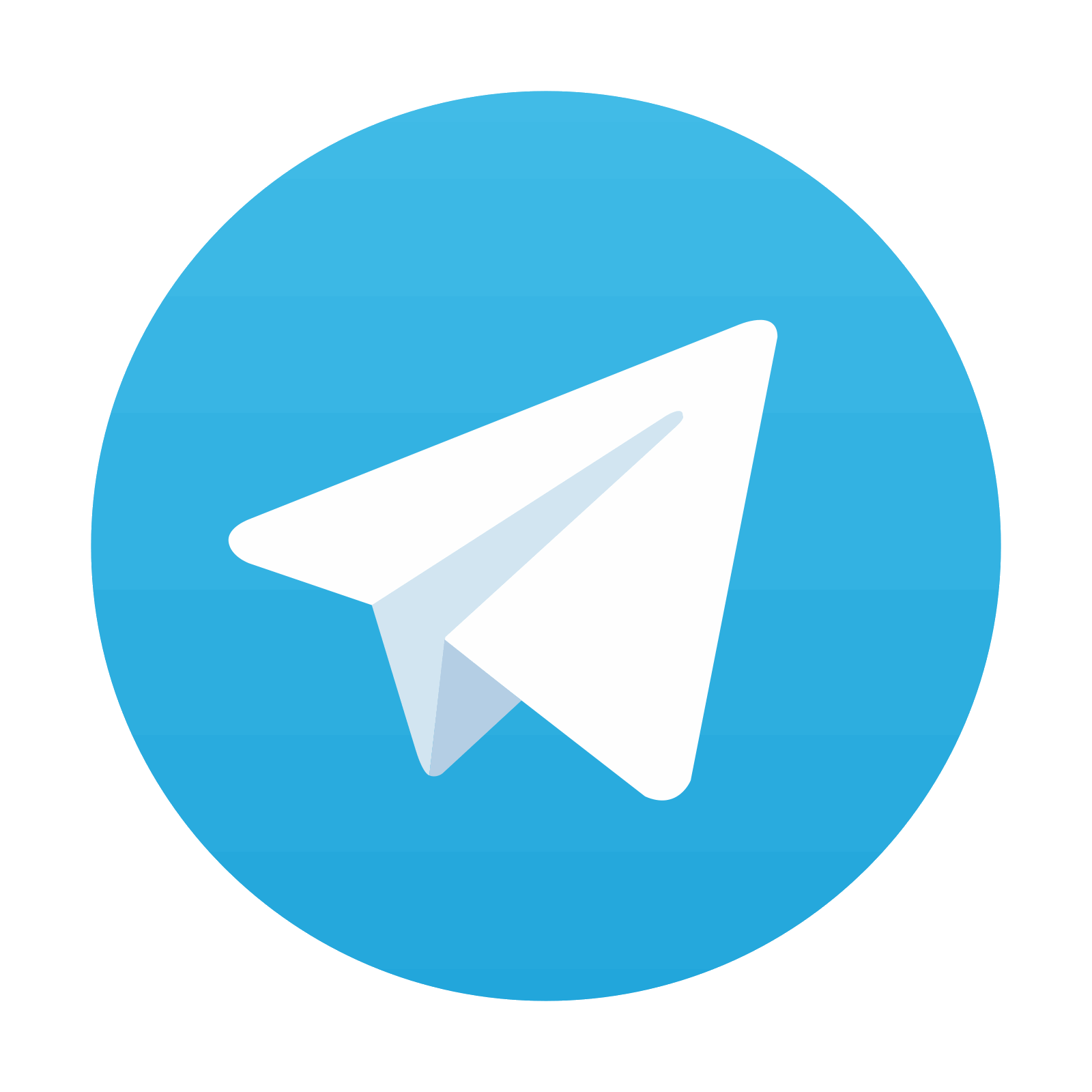
Stay updated, free articles. Join our Telegram channel
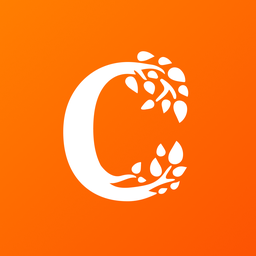
Full access? Get Clinical Tree
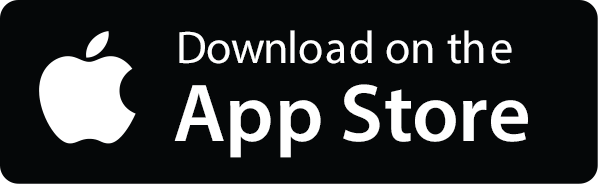
