Asif Syed
CONTENTS
Sustainable and High-Performance Facilities
Sustainable Assessment Initiatives for Buildings and Products
Energy Modeling and LCC and Assessment
INTRODUCTION
Sustainability, which is important to all sectors of the pharmaceutical industry, is defined as “meeting current needs without compromising the future.” In addition to protecting the environment, sustainability offers benefits ranging from operational cost savings to public approval. The cost reduction results from improving efficiency, thereby avoiding the cost of wasteful energy, and the public approval generated by environmental stewardship is a long-term asset. Employee satisfaction is also linked to companies “that do the right thing.” Sustainability is simply good business practice that generates innovation beneficial to the company.
Sustainability is applicable to both new development and renovation projects. The facilities and building operations groups are generally responsible for the sustainability goals established and often must demonstrate the sustainable path to top management; thus, facilities and building operations play a major role in the sustainability of the company.
This chapter explains how to structure current sustainable policies in the pharmaceutical industry, that is, how to adopt sustainable practices in product design, design and construction of new facilities, renovation of existing facilities, and ongoing operations. Additionally, key resources for sophisticated sustainable design and operations are identified.
Implementing a sustainable policy, reporting progress, and quantifying achievements are challenging and complex. There are several models used for measuring the sustainability of facilities, such as the rating system of the U.S. Green Building Council’s (USGBC) Leadership in Energy and Environmental Design (LEED) and the United Kingdom’s Building Research Establishment Environmental Assessment Method (BREEAM). While none of these models are specific to pharmaceutical manufacturing, almost all pharmaceutical companies have at least some commercial office buildings to which the standard model applies. Getting a LEED rating may not necessarily quantify achievements. However, measurable emissions and energy use can be easily quantified by calculating a carbon footprint in tons of carbon dioxide released into the atmosphere and kBTU/year (kW/year), which is a universally accepted measure of energy use by an organization. For existing buildings, after a baseline is established by building performance the first year, subsequent years can demonstrate reduction with energy-efficient measures. For new buildings, the baseline is generally the energy code–mandated energy efficiency measures, and additional sustainable measures can demonstrate a reduction from the baseline.
ISSUES IN SUSTAINABILITY
Generally, sustainable building design aims to reduce the negative impact on the environment and improve the health, comfort, and well-being of the building’s occupants. It is achieved by balancing the three P’s (i.e., people, planet, and profit). The guiding principles of sustainable buildings are site optimization, reduction of energy consumption, use of environmentally safe materials, reduction of water use, improvement of indoor air quality, and reduction of the ongoing impact to the environment.
AIR QUALITY AND EMISSIONS
The far-reaching benefits of the pharmaceutical industry in enhancing quality of life and preserving life are often overshadowed by environmental issues, such as air pollution. Understanding, documenting, and monitoring the air emissions are generally the first steps toward reducing or managing the emissions. Air emissions include organic and inorganic compounds, which are particulates from manufacturing or formulation. The Clean Air Act classifies the hazardous air pollutants (HAPs). These emissions vary from facility to facility based on the product and process. Air emissions must be identified and contained and require an integrated approach from start to finish. Input from drug designers, manufacturing process engineers, facility design architects and engineers, and local environmental engineers helps to address the issue of HAPs.
ENVIRONMENT
Release of Products
Release of pharmaceutical products into the environment can happen during production, which is under the control of the facilities and operations groups, or postproduction, which is not under the control of the manufacturing facility. Overall, the drug ingredients released postproduction into the environment can be reduced by avoiding overprescribing, patient compliance in drug usage, and proper drug disposal. Postproduction releases are beyond the scope of this book. For designers of pharmaceutical facilities, the most important issue is the release of the drug ingredients or other chemicals into the environment from the facility they design. Though environmental regulations govern specific chemicals, the gold standard of sustainability is not to release any ingredient into the environment, whether or not its effects are known. Processes generate waste and emissions, which depend on the process and materials used.
Water
Pharmaceutical manufacturing facilities often draw attention from the public and environmental groups because pharmaceutical ingredients have contaminated water in local streams, groundwater, or other bodies of water. The greatest concern is the ability of pharmaceutical agents to alter living organisms in these bodies of water. As with air pollution, an integrated approach between all stakeholders, from pharmaceutical developers to facilities designers, such as architects, engineers, and local environmental engineers, is the best for solving the water quality issue. Reduction of water use and water waste greatly contributes to sustainability.
Solid Waste
At pharmaceutical facilities, solid waste is generated from several sources: manufacturing processes, filtration of air and water (i.e., abatement), construction and demolition operations, incineration waste, and excess product. Generally, pharmaceutical solid wastes are generated during formulation, mixing, compounding, and discarding excess. The solid wastes include excess raw materials, spent solvents, reaction residues, air and liquid filter media, and chemical reagents. Most solid wastes are incinerated or disposed off-site.
Compliance with federal, state, and local regulations is required in all solid waste disposal. The regulations are beyond the scope of this chapter. However, solid waste reduction can be integrated into the product design by factoring in the input from the solid waste handling and disposal team. The facility design team must integrate the process of waste reduction and recycling into their overall design.
ENERGY
All pharmaceutical facilities use energy in several different forms, such as electricity for power and light and natural gas to produce heat, steam, and hot water for processing. Liquid fuels, such as diesel, are commonly used as backup fuel sources for generators. While most energy used in the world is directly related to the burning of fossil fuels, there are non–fossil fuel energy sources, such as nuclear, solar, wind, and geothermal. There are several opportunities to reduce energy use in the design, renovation, and operation of pharmaceutical facilities. Reduction of energy leads to lower utility bills for electricity and natural gas, which directly improves the bottom line. The indirect benefit comes from the reduction of the carbon footprint as a result of lower energy use either on-site or at the power plant where the energy is generated.
Generally, pharmaceutical facilities use more energy than other manufacturing practices. The high energy use results from process loads that use steam. While a batch process may operate for a few hours or days of a week, the boiler plant is constantly using energy by staying warm around the clock. In addition, the need for cleanliness, which necessitates a high air-change rate and filtration, is a constant energy drain. The air-change rate, which complies with current Good Manufacturing Practices (cGMPs), varies based on the drug or formulation. The generally accepted industry practices for air-change rates are listed in Table 16.1 [1]. These high air-change rates require fan power to circulate the air, in addition to increasing cooling and heating costs. Careful attention to energy use and costs can lead to reduction in energy preservation of resources, reduction in capital costs, and above all, a reduction in ongoing operational costs, the benefits of which can be reaped year after year.
SUSTAINABLE AND HIGH-PERFORMANCE FACILITIES
High-performance design is generally understood, as defined by the U.S. Energy Independence and Security Act of 2007, as “a building that integrates and optimizes on a life cycle basis, all major high-performance attributes, including energy and water conservation, environment, safety, security, durability, accessibility, cost-benefit, productivity, sustainability, functionality, and operational considerations.”
TABLE 16.1
Generally Accepted Air-Change Rates for Clean Rooms
The quantitatively measurable aspects of high-performance design are energy and water conservation. The baseline is defined by the governing codes and regulations. The most commonly adopted energy code is ASHRAE 90.1. This standard has a prescriptive methodology of minimum energy efficiency standards, which leads to an annual energy consumption per year in BTU/sf/year (watts/sm/year). Exceeding this value by a percentage, such as 10%, 20%, or 30%, is a good measure of a building’s performance in energy efficiency. Similarly, a baseline for water consumption is mandated by the Energy Policy Act of 1992 and 2005.
INTEGRATED PRODUCT DESIGN
Product design plays an important part in sustainability in the pharmaceutical industry. Although the product is paramount, a sustainable design approach and an integrated design process are recommended. An integrated design starts with a design charrette, where everyone involved with the product is invited. The charrette provides an opportunity for all stakeholders to highlight the issues that are important to their role in the life of the product. This process illustrates the different aspects of the product to all parties involved; it eliminates the silos in which groups can sometimes operate. This integrated process improves the production of the product by reducing waste, energy, and especially costs.
SUSTAINABLE ASSESSMENT INITIATIVES FOR BUILDINGS AND PRODUCTS
There are several nonprofit organizations worldwide that promote sustainability in the design, construction, and operation of buildings. These organizations have developed tools that assist designers in tracking and monitoring building sustainability goals that are specific to a building and a site. The USGBC is best known for the development of the LEED rating system. The Green Building Initiative (GBI) is another nonprofit organization that has developed a web-based rating tool called Green Globes. The Energy Star program was developed by the U.S. Environmental Protection Agency (EPA); it rates commercial buildings for energy efficiency and provides a percentile ranking system compared to similar buildings in the United States. The Living Building Challenge offers performance-based standards and a certification program for renovations and new construction.
In addition to these, international organizations include BREEAM in the United Kingdom, European Union, and parts of the Middle East; Building Environmental Assessment Method (BEAM) in Hong Kong; Comprehensive Assessment System for Built Environment Efficiency (CASBEE) in Japan; Green Mark Scheme in Singapore; Green Star in South Africa; and Pearl Rating System in the United Arab Emirates.
SUSTAINABLE BUILDING SYSTEMS
Building systems play a key role in the sustainability of pharmaceutical companies, including manufacturing plants, cGMP facilities, research labs, and administrative office buildings. After a building is built, the systems that keep the building operational are the major users of energy and resources. Well-designed and energy-efficient systems use less energy and generate less waste. Conventional heating, ventilation, and air conditioning (HVAC) systems were designed when the cost of electricity was insignificant compared to the overall cost of doing business. Resources, such as water, were not in short supply. In the last two decades, however, things have changed. The cost of energy has increased dramatically, and developing countries are increasing their demands for limited resources, creating noticeable shortages. Additionally, global warming has been shown to be linked to greenhouse gases.
The HVAC and manufacturing industries have responded to the above changes with new technologies, advanced systems, new design approaches, and operational practices that reduce energy and resource consumption, eliminate waste, and optimize comfort. This change has happened so quickly that many professionals in the industry are just catching up. The old practices and customs are hard to change. The following section introduces several new technologies and advanced systems that are sustainable. This is an introduction to the fundamental concepts that allow designers to identify technologies that are adaptable to pharmaceutical facilities.
RENEWABLE ENERGY PRODUCTION
Solar
Solar energy is the most abundant and clean form of energy available on the planet. Its abundance is such that it could provide 44 quadrillion (4.4 × 1016) W of power; it would take 44 million large electric power plants, each producing about 1 billion (1 × 109) W of power to equal the energy coming from the sun [2]. The solar energy coming from the sun far exceeds the energy used by humans on the earth. Solar power has zero pollution, no carbon footprint, and no emissions produced by its operation. Solar energy can be captured by thermal or photovoltaic (PV) methods. Thermal energy is captured in the form of heat (hot water) and PV energy in the form of electricity (PV panels). Energy payback estimates for rooftop PV systems are 1–4 years (Figure 16.1); this is the energy that goes into manufacturing PV panels. This should not be confused with the cost payback, which is the cost to install the PV panels at the site, paid back by the reduction in electricity bills. This payback can vary based on the location of the PV installation and the cost of electricity produced from conventional sources, such as coal and natural gas. The cost of electricity varies in different parts of the country. The U.S. Energy Information Administration publishes the electric rates for the different states and regions in the United States, which can vary from 10 to 30 cents per kilowatt-hour (kWh). In addition to this consumption charge, there is also a demand charge, which can vary in different parts of the country. While calculating the cost of electricity, both demand and consumption charges are necessary to compute the total cost.
Approximately 100 W/ft2 of useful energy reaches the ground surface of the earth, of which about 15–20 W/ft2 can be converted into electricity with PV panels. With solar thermal, about 60–70 W/ft2 can be captured in heat. Thus, the efficiency of the thermal system is far higher than that of the PV system. When there is a steady need for hot water in a facility, thermal energy capture is more desirable than PV capture for the same real estate of the roof or ground area.
A PV watts calculator is a web-based tool developed by the National Renewable Energy Laboratory (NREL) and is popular for preliminary studies. It estimates the electricity production potential of a given site. The inputs to the calculator are site location (zip code) and the design of the PV system, such as the PV tilt and direction. The system database includes the cost of grid power for the site location selected. Using these values, a report with estimated monthly and annual electricity production and cost savings is produced. It is recommended that once the decision is made to proceed, a professional who is familiar with the system needs to be retained for design and financial analysis, including capital costs, running costs and savings, utility rebates, and grid connections.
FIGURE 16.1 Energy payback for rooftop PV panels. (From National Renewable Energy Laboratory, PV FAQs, DOE/GO-102004-1847, U.S. Department of Energy, Office of Energy Efficiency and Renewable Energy, Washington, DC, January 2004. http://www.nrel.gov/docs/fy04osti/35489.pdf)
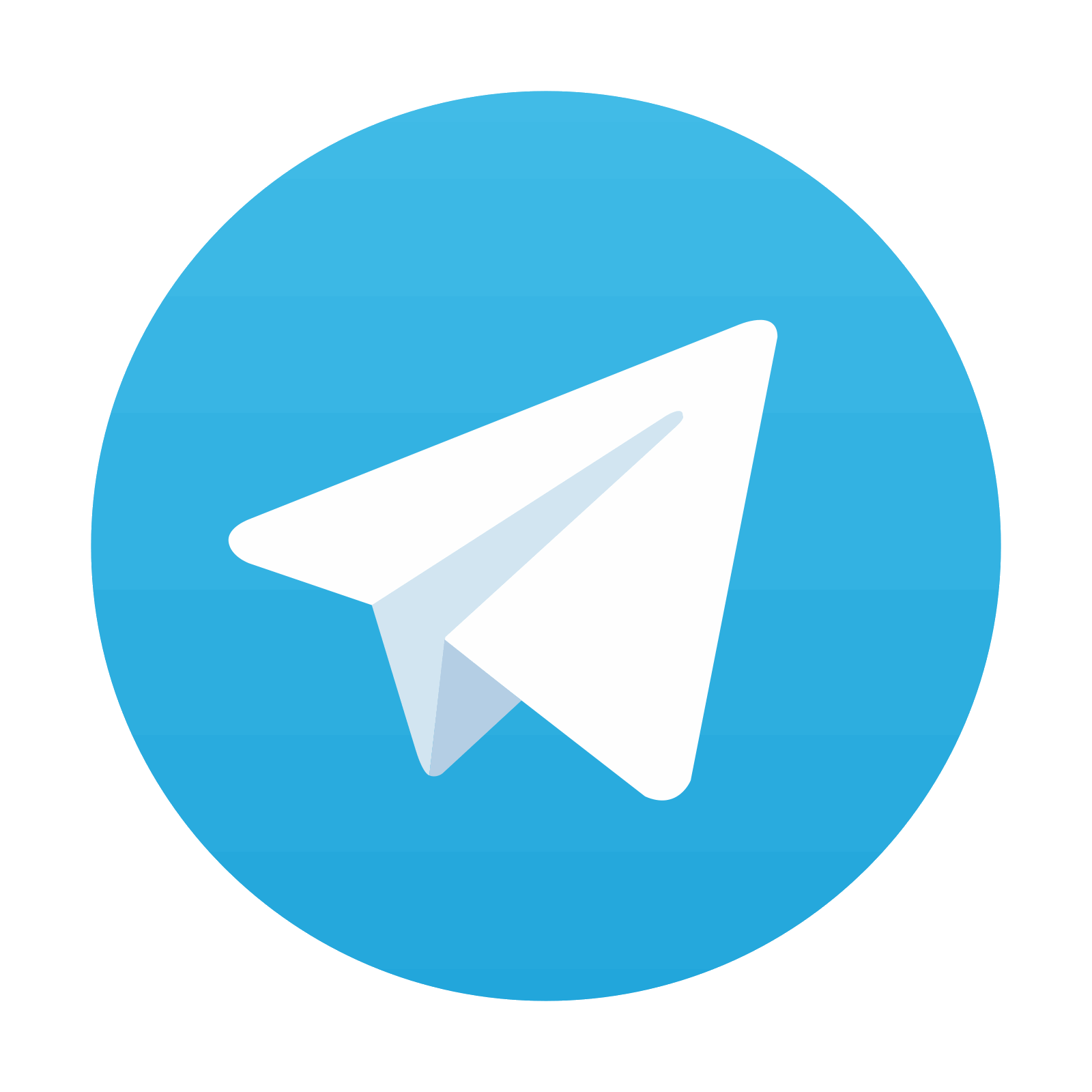
Stay updated, free articles. Join our Telegram channel
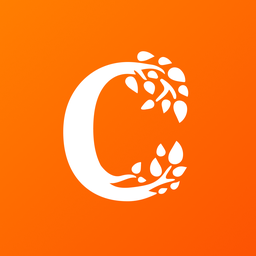
Full access? Get Clinical Tree
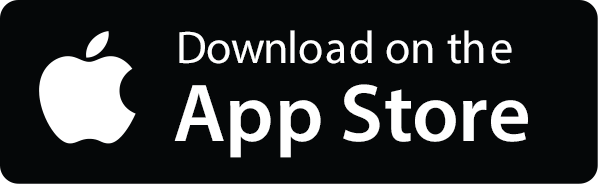
