Cleaning validation may be conducted during the PQ phase or the tradi-tional process validation phase in parallel with the manufacturing of the validation batches. The details of the philosophy and approach for process and validation activities must be detailed in the site’s VMP. Validated laboratory test methods are required for the execution of process and cleaning validation studies.
After successful completion of the process validation batch campaign, the next stage in the validation life cycle approach is operational phase or continuous monitoring/sustaining of operations, also termed continued process verification. During routine manufacturing, continuous monitoring of the critical quality attributes provides a continuous loop of information. The continuous monitoring aspect of the validation life cycle creates a feedback mechanism that is used to improve the process. Any proposed changes to improve the process must be formally documented in the change control system. Information gained during the continuous monitoring program is feedback into various systems, including updating and improving calibration and preventive maintenance systems.
Validation Life Cycle
Validation is a prospective and confirmatory exercise. The difference between qualification and validation is that equipment is individually qualified, and the system or process is validated. The intent of validation activities, including PQ and process validations, is to confirm the knowledge gained during design, development, installation, and challenge exercises, and as a confirmatory exercise of a process that is already known and in control. A few types of validation are discussed in some regulatory guidance documents, which include prospective, retrospective, and concurrent. The chapter has discussed and outlined prospective validation. Prospective validation is the most preferable and defendable nature of validation. This type of validation aligns with the validation life cycle approach and provides the most confidence in the documentation generated that the drug is produced as required by GMP.
Retrospective validation is a look-back approach to validation and an attempt to justify legacy systems based on a retrospective gathering of documentation. Retrospective validation is not normally considered acceptable. There is an expectation of understanding and documenting processes, including the site’s legacy processes and equipment. Retrospective validation is difficult to document as the data gathered must be statistically based and analyzed.
Concurrent validation occurs when manufactured batches are released one lot at a time before the completion of the three or designated number of batches for the process validation campaign, and should only be used when drugs are medically necessary and an approved plan that outlines the nature of concurrent release is approved by required regulatory agencies.
Qualification and validation are regulatory guided programs for GMP pharmaceutical companies. Although these programs are mandated by various regulatory bodies, the intent of a robust qualification and validation program is to ensure that facilities, utilities, equipment, systems, and processes are designed with the end in mind. Requirements are tested and verified to predetermined specifications, and there is verification that the facilities, utilities, or equipment are installed and operate properly. These programs provide documented evidence that what was purchased meets expectations and produces a drug product that meets the requirements of 21 CFR 210.1.
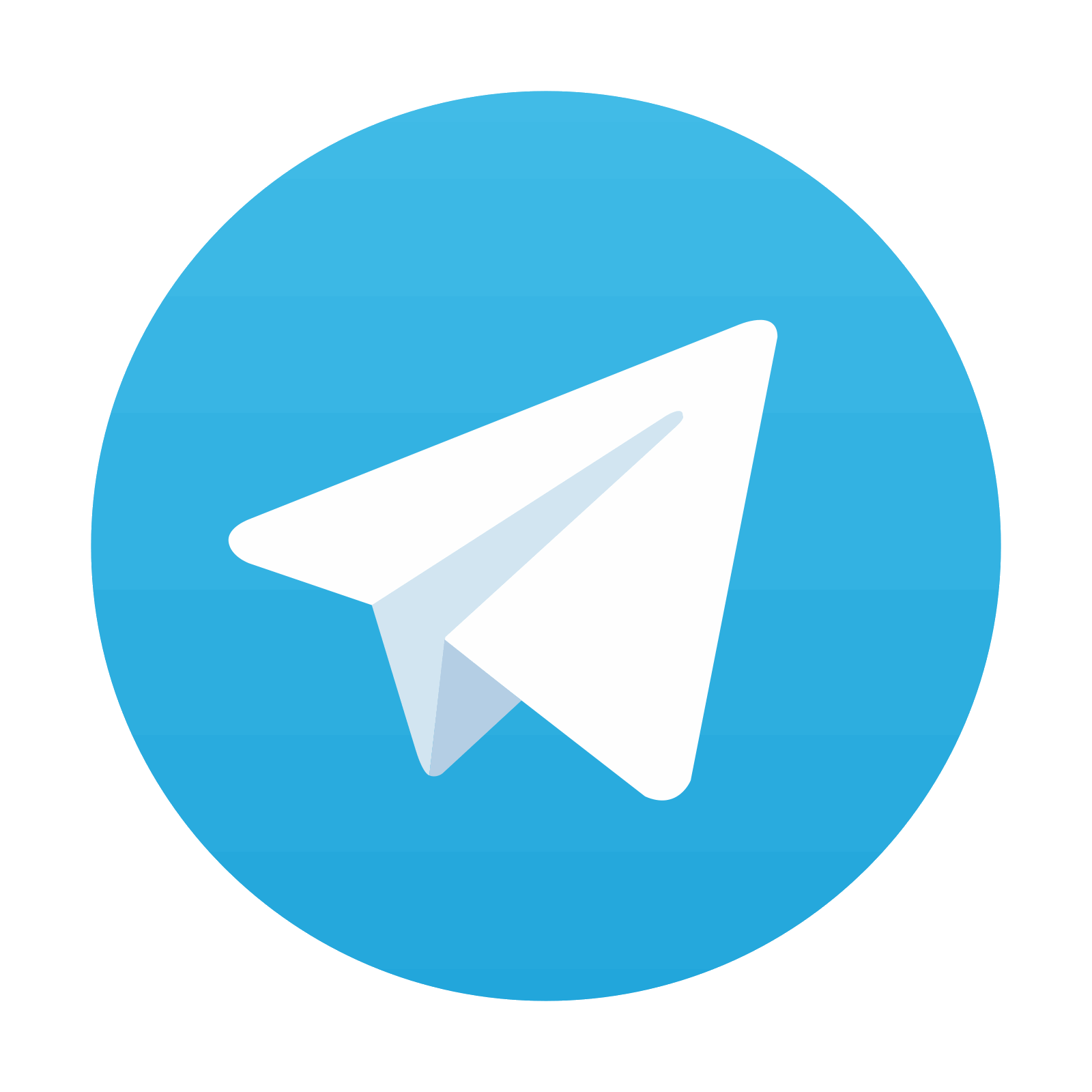
Stay updated, free articles. Join our Telegram channel
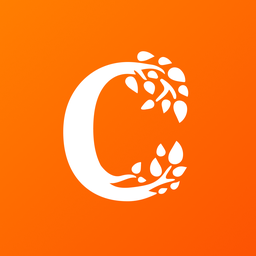
Full access? Get Clinical Tree
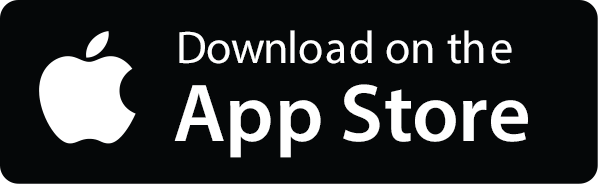
