17 QA/QC Laboratories and Related Support Spaces
Cassidy Hobbs, AIA
CONTENTS
Drug Enforcement Administration Storage
INTRODUCTION
In pharmaceutical manufacturing facilities, support laboratories play the crucial role of testing the product to verify its quality, safety, and stability at each stage of the manufacturing process, packaging, and product release. These labs are referred to as quality assurance (QA) and quality control (QC) laboratories and exist to support the manufacturing operations of the facility. The design of QA/QC laboratories requires an understanding of the facility; the processes and equipment used in the lab; the hazardous materials present; the heating, ventilation, and air conditioning (HVAC) systems used; and other requirements. Consideration must be given to the safety and protection of lab personnel and the product. Despite their small size relative to the facility at large, QA/QC laboratories are necessary to the operation of the facility, and a thorough understanding of good design practices is necessary to guarantee the efficiency and viability of the facility.
This chapter breaks down the process of programming and designing pharmaceutical support labs and related spaces, such as glass washrooms, sample storage, and stability storage, from initial information gathering through completion of the facility. It explores the key issues in this process for both new facilities and renovations of existing facilities and gives an overview of the components of a lab and the role of QA/QC labs in pharmaceutical manufacturing facilities.
EXECUTIVE SUMMARY
According to the Good Practice Guide Quality Laboratory Facilities, from the International Society of Pharmaceutical Engineering (ISPE), “the purpose of the quality laboratory is to support the execution of testing that assures the manufactured products meet the identity, strength, purity, efficacy, and safety as specified in the approved regulatory file” [1]. Testing verifies that no contamination or other problem has occurred in the manufacturing process.
The functions of QA/QC laboratories vary; they are general testing laboratories, sterility testing (microbiology) laboratories, biocontainment laboratories, potent compound laboratories, or other specialty laboratories, such as cold laboratories or laboratories that deal with radioactive substances. General testing laboratories are the most common type of QA/QC laboratory. Microbiology labs test for the presence of microorganisms in sterile products and may also test air and water quality for the facility, so maintaining a sterile, cleanable environment is particularly important. Biocontainment laboratories test biohazardous materials and are rated by the biohazard safety levels of the biological materials they contain, as defined by the National Institutes of Health (NIH) and the Centers for Disease Control and Prevention (CDC). Most QA/QC laboratories can be categorized as either general testing labs or microbiology labs, which may have biocontainment requirements.
The considerations necessary for the design of support labs vary slightly based on the laboratory type, but the key concepts and principles remain the same. In each lab, it is important to understand the necessary equipment and preparation space to help determine the required linear feet of bench space that is needed. Establishing a laboratory module can help to organize the plan. Lab flexibility, the location of offices or write-up space, compliance, and HVAC issues also influence the design of the lab. Recently, the concepts of lean labs, lab culture, and sustainability have grown in popularity, and the owners’ attitude toward these will impact the design process.
QA/QC LABS
LABORATORY PLANNING PROCESS
The process of laboratory design follows the path diagrammed in Figure 17.1, from programming through construction and then commissioning. This section will focus on the programming and schematic design phases, as that is when the major decisions relating to lab planning are made.
Laboratory planning can be organized into three stages: problem seeking, analysis, and problem solving (Figure 17.2). In the broadest sense, problem seeking is the task of gathering and organizing information, analysis is processing that information, and problem solving is the application of the analysis to get a result. When completed, this is compiled in the basis of design (BOD), a report completed at the end of the schematic design phase that includes all of the information collected, a program of the rooms required, diagrammatic plans laying out the spaces and their relationships, and a lab card for each space. This process applies to all labs, not just QA/QC labs, but in support labs, an understanding of the overall facility is especially important. The QA/QC laboratories may be separate from the main manufacturing areas or may be located near the stage of manufacturing where the tests take place. A single facility may have multiple QA/QC laboratories, depending on the tests that are required.
FIGURE 17.1 Design and construction process.
FIGURE 17.2 Problem seeking, analysis, and problem solving.
Problem Seeking
The problem-seeking phase has two parts: data gathering and space programming. Data gathering begins with interviews of lab personnel and the administration to develop goals and objectives for the project and gather information. This process often includes a preinterview survey for the users and a tour of existing facilities if the client has them. It is necessary for the designer to help the users complete the survey, as they may not know their exact needs. The designer may also have to act as referee between conflicting desires of the lab personnel (scientists and technicians) and the facility management or owners. It is also necessary to coordinate with the site’s security staff, information technology (IT), and other facility personnel so that facility-wide systems can be integrated.
Data Gathering
The following topics should be covered during the data gathering phase.
Existing Operating Procedures and Facilities
In renovation projects or projects for clients with other facilities, an analysis of the existing facility can provide a wealth of information on the client’s needs and existing operating procedures. The analysis can help determine the required amounts of storage and bench space and can help the designer replicate what works well and avoid recreating any existing issues. It is especially important in renovation projects, as there are often missed opportunities of which the client is unaware. Space and resources are often underutilized (e.g., bench space used to store obsolete equipment), and identifying these inefficiencies will allow them to be corrected in a renovation. It is very important for the designer to note how existing hoods are used, and whether storage space is utilized.
The goals of the QA/QC lab can be accomplished through a combination of standard operating procedures (SOPs) and physical design. The methods used by lab personnel when performing tests are defined by SOPs, which can be used to prevent opportunities for contamination of samples; however, it is preferable to prevent problems through the physical design of the lab, rather than SOPs, whenever possible. For example, while waste could be moved through another part of the lab during off-hours in sealed containers, a better solution would be to provide an alternate route directly out of the lab. Various options must be explored, and the SOPs and lab design must work hand in hand. SOPs are laid out in an operations manual for each laboratory, and it is important that laboratory personnel are familiar with the hazards they may encounter in the lab and the SOPs that are in place to protect them and the samples.
Equipment
During the data gathering phase, the design team will begin to identify the types of equipment to be used and the general equipment requirements for space, power, and services. Ultimately, an equipment list will be developed that lists all equipment, along with sizes, services required, electrical requirements, backup power requirements, and in the case of renovations, existing locations and site identification numbers if available. In a renovation, the equipment may be existing or new and may have limits on its relocation. For example, relocating an autoclave or glass washer might necessitate relocating drains in the existing slab, which would unnecessarily add cost to the project. For a new facility, the equipment list is developed by the users and may be modified as the design progresses. Some clients will be able to provide this list, while others will need time and assistance with its development. In a renovation project, this stage may include a survey of the existing equipment. It is important to create the equipment list early in the project, as it will have a large impact on the overall design and schedule. Many pieces of equipment have plumbing or exhaust requirements that must be coordinated with the plumbing engineers (e.g., water sources or drains) and HVAC designers (e.g., exhaust systems). Additionally, many pieces have long lead times, and it is important to make sure they are ordered early enough to arrive in time for installation.
Although they vary by product, general testing laboratories typically contain high-performance liquid chromatography (HPLC) equipment, preparation space (in a fume hood) for mobile phase mixtures for the HPLCs, gas chromatography (GC) equipment, hoods for handling solvents and reagents, and incubators, freezers, and refrigerators for storage. A typical microbiology laboratory might consist of a media prep space with refrigerators, hoods for sampling, and incubators. Table 17.1 shows an example preliminary equipment list. As the project progresses, additional information, such as power requirements and services, is added, and equipment selections are finalized.
Hoods: There are many types of hoods used in QA/QC laboratories, and often, it is up to the designer to work with laboratory personnel to determine the appropriate type. Often, biosafety cabinets (BSCs), fume hoods, and laminar flow hoods are all referred to as hoods by laboratory personnel, but their uses are very different. It is important to determine hood requirements early in the design process so they are included in the HVAC design.
Fume hoods: Fume hoods are used for containment of chemical or biological hazards through negative airflow, which may be exhausted to the outside, connected to the HVAC system, or filtered and returned to the lab.
Laminar flow hoods: Laminar flow hoods are used to prevent contamination of samples. High-efficiency particulate air (HEPA) filters remove particulates from the air that is blown over a surface and out into the lab to keep the surface in the hood sterile. Laminar flow hoods come in both vertical and horizontal varieties.
Biosafety cabinets: Biosafety cabinets are used to both contain and protect biological materials. They are rated by classification, as shown in Table 17.2.
Incubators: Incubators are used to store materials at a constant temperature. They are often required to be on emergency power, along with the lab’s refrigerators and freezers.
TABLE 17.1
Example Equipment List
TABLE 17.2
Classification of Biosafety Cabinets
Classification
Biosafety Level
Application
Class I
1, 2, 3
Low to moderate risk
Class II
1, 2, 3
Low to moderate risk
Class III
4
High-risk biological agent
Note: Biosafety levels are discussed later in the chapter.
Stay updated, free articles. Join our Telegram channel
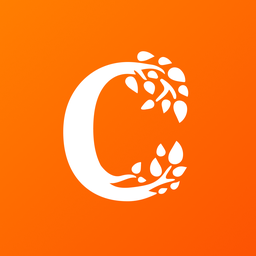
Full access? Get Clinical Tree
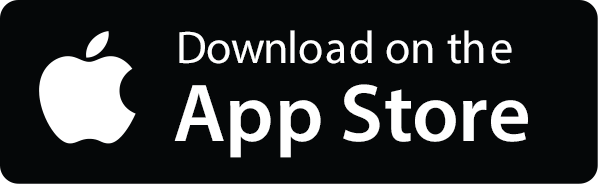
