Sanitization and Hygiene
Clean areas should be cleaned thoroughly according to documented procedures. Detailed hygiene programs should be established. They should include procedures relating to the health, hygiene practices, and clothing of personnel. Hygiene procedures should be understood and followed in a very strict way by every person whose duties take him/her into the production and control areas. The hygiene program should be promoted by management and discussed during training sessions. Every person entering the manufacturing areas should wear protective garments appropriate to the operations to be carried out. Where a potential for the contamination of a raw material, in-process material, or drug exists, individuals wear clean clothing and protective covering. Unsanitary practices such as eating, drinking, chewing gum, or smoking, or the storage of food, drink, smoking materials, or personal medication in the production and storage areas should be prohibited. Requirements concerning personal hygiene, with an emphasis on hand hygiene, are outlined and are followed by employees. Personnel should be instructed to use the hand-washing facilities. Direct skin contact between the operator’s hands and raw materials, primary packaging materials, intermediate or bulk drug, or exposed product, as well as with any part of the equipment that comes into contact with the products, should be avoided. Houseplants are not permitted in fabrication, packaging/labeling, and storage areas or in any other areas where they might adversely influence product quality. Requirements concerning cosmetics and jewelry worn by employees are outlined and are observed by employees. Soiled protective garments, if reusable, are stored in separate containers until properly laundered and, if necessary, disinfected or sterilized. Steps should be taken to ensure as far as is practicable that no person affected by an infectious disease or having open lesions on the exposed surface of the body is engaged in the manufacture of medicinal products. Personal hygiene procedures, including the use of protective clothing, apply to all persons entering production areas. The hygiene program clearly defines clothing requirements and hygiene procedures for personnel and visitors. It must be the manufacturer’s responsibility to provide instructions ensuring that health conditions that can be of relevance to the quality of products are brought to the manufacturer’s attention. In general, any unhygienic practice within the manufacturing areas or in any other area where the product might be adversely affected should be forbidden.
In addition, some jurisdictions require medical examinations, particularly at time of recruitment. After the first medical examination, examinations should be carried out when necessary for the work and personal health.
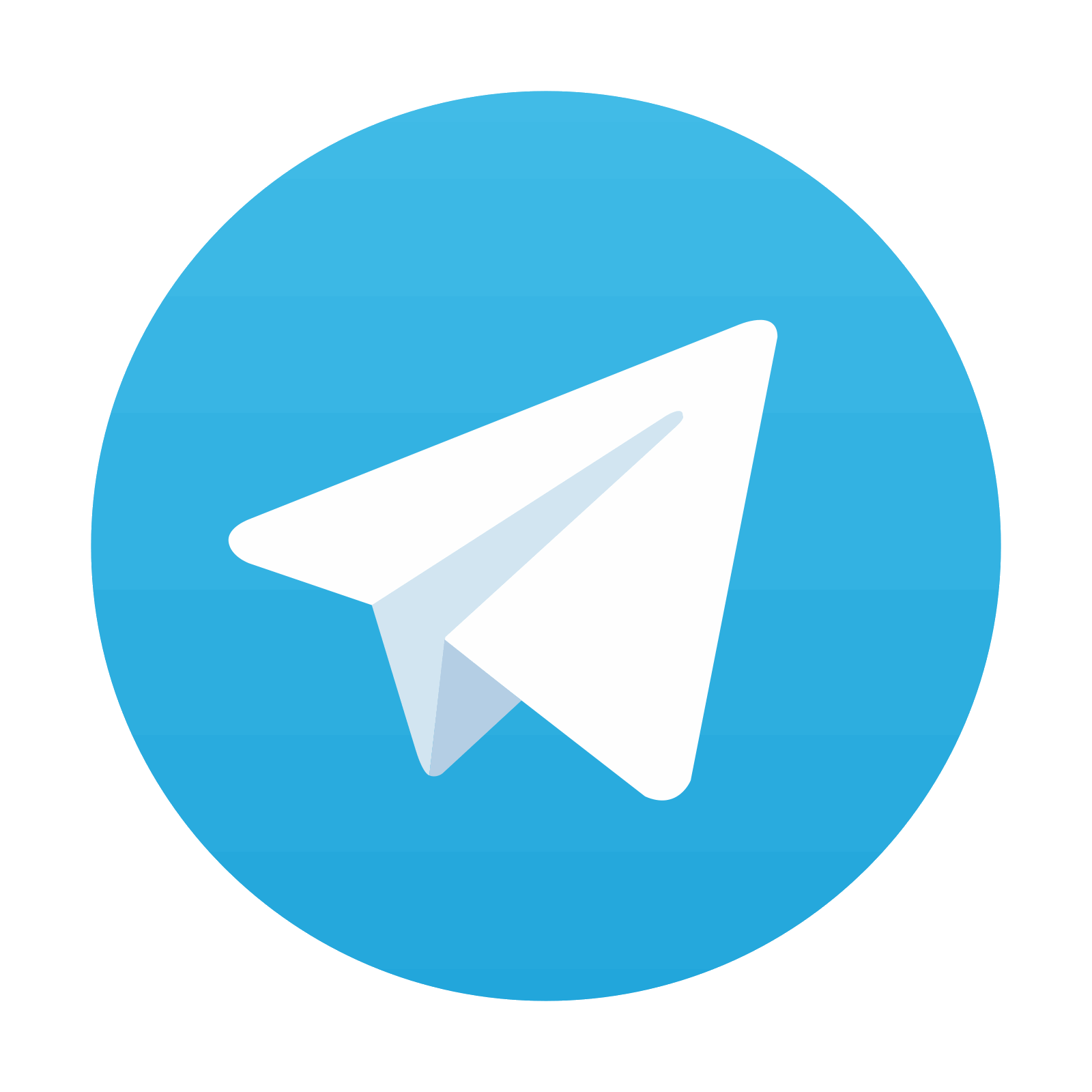
Stay updated, free articles. Join our Telegram channel
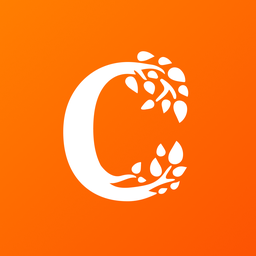
Full access? Get Clinical Tree
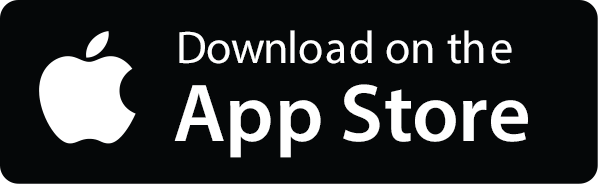
