.
A monomer must have one or more reactive sites to form bonds with other monomers in order to prepare a polymer and may or may not be equivalent to the repeat unit. The small monomeric units are, indeed, connected to each other through the chemical reactions and the chemical process used for the synthesis of polymers is called the polymerization.
The simplest example of polymer is represented by PE which is obtained from its monomer ethylene (Fig. 1.1).
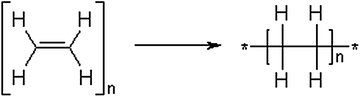
Fig. 1.1
Synthesis of polyethylene starting from ethylene monomer
The molecular structure of polyethylene chain contains connected tetrahedral sp3 hybridized C atoms and it can be viewed as an extension of the covalently bound molecule ethane. Thus, in this case, the chemical structure of the repeat unit is different from the structure of ethylene monomer from which the polymer is produced.
Several ways of classifying polymers can be adopted depending on different parameters, such as the type of monomer, the source, the structure, the polymerization mechanism, the molecular forces and tacticity (the way pendent groups are arranged on a polymeric backbone).
Type of Monomer
Homopolymers, polymers formed from only a single type of monomer;
Copolymers, polymers prepared from more than one type of monomers which can be further divided according to the arrangements of the different repeat units in the chain (Fig. 1.2):
alternating copolymers: the repeat units of two different monomers are arranged in alternating sequence within the chain;
block copolymers: in these polymers, two or more long linear sequences of different homopolymers (blocks) are linked together;
graft copolymers: they are branched block copolymers in which the backbone is one type of block and the other type of blocks are attached to the main chain as pendant groups;
random copolymers: they consist of two or more different repeat units attached in a random order.
Fig. 1.2
Schematic structures of: a alternating copolymers, b block copolymers, c graft copolymers and d random copolymers
The Source
Natural polymers: occur in plants and animals, in which play an essential role for life, and include starch, cellulose, silk, chitin, proteins, nucleic acids and natural rubber;
Synthetic polymers: are artificially synthesized in the laboratory and they can be defined as “man-made polymers”. In daily life, this kind of macromolecules finds several applications in a wide range of fields, such as cosmetics, pharmaceutics, medicine, packaging, food processing, textile. Examples include polyethylene, polystyrene, PVC, nylon and polyurethanes;
Semi–synthetic polymers: these are mostly derived from naturally occurring polymers by chemical modifications. An example is cellulose acetate, a derivative of cellulose which forms due to acetylation of cellulose and used for making threads, films and glasses.
The Chain Structure
Linear polymers: repeat units are joined together in the form of a single long straight chain (Fig. 1.3). The starting monomers have only two functional groups if the polymer is a step-growth polymer or a single double bond if it is a chain polymer. Examples are polythene, polyvinyl chloride, etc.;
Fig. 1.3
Macromolecule structures
Branched polymers: linear side chains get branches of different length along the main chain (Fig. 1.3). Branches are caused by the presence of small amounts of trifunctional monomers for step-growth or two unsaturations for chain polymers;
Crosslinked polymers: three-dimensional networks consisting of long linear chains connected to each other with multifunctional units (Fig. 1.3). The interconnections between chains can be formed during the polymerization process (by choice of a crosslinking agent) or after polymerization (by adding a specific reagent).
The Molecular Forces
Elastomers: they are amorphous polymers with high degree of elasticity and characterized by weak attraction forces between polymeric chains. An elastomer should be flexible and able to return to its original dimensions;
Fibres: they have strong intermolecular attraction forces between polymeric chains, high tensile strength, least elasticity, good pliability and are able to hold their shape;
Thermoplastics: they are characterized by intermediate intermolecular force of attraction between molecules. Linear and slightly branched chains become soft when the temperature is increased, but again gets rigidness after cooling, thus they can be safely processed by melting. These polymeric materials, indeed, can be reshaped with further application of heat and pressure because no changes in the chemical composition and no bond formation occur during heating and cooling processes. Some examples of thermoplastics include polythene, polyvinyl chloride, Teflon, polystyrene;
Thermoset polymers: unlike thermoplastics, they can not be melted and reshaped with the application of heat due to crosslinking reactions which take place during heating. Therefore, heating must be the last stage of processing due to irreversible changes in the chemical composition. Examples are Bakelite and urea-formaldehyde resin.
The Molecular Weight
Oligomers: molecules consisting of a few repeat units and characterized by a molecular weight ranged from 500 to 5,000 g mol−1. Dimers, trimers, and tetramers are oligomers composed of two, three and four monomers, respectively;
High polymers: have a molecular weight in the range of 104–106 g mol−1.
The Polymerization Mechanism
Step-growth polymers: polymers that differ from their monomer(s) and are formed when two di- or polyfunctional molecules react and condense producing macromolecules with the elimination of a small molecule, such as water or alcohols (polyamides and polyesters);
Chain polymers: produced by chain reactions of double-bonded monomers in which the chain carrier can be a radical or an ion.
Tacticity
Atactic polymers: pendant groups are arranged randomly;
Syndiotactic polymers: pendant groups are arranged alternately;
Isotactic polymers: pendant groups are arranged on the same side of the polymer backbone.
On the basis of the reaction mechanisms, polymerizations can be classified into step-growth and chain polymerization. In the first case, the polymerization mechanism involves a series of chemical condensation reactions between monomers with functional groups leading to the elimination of small molecules (water, alcohol, hydrogen). In chain polymerization, monomeric units incorporating double chemical bond are rapidly added to the reactive sites onto the growing polymeric chain. This reaction mechanism requires an initiator which forms the first active unit.
The present book chapter aims to explore the molecular mechanisms and kinetics of polymer formation reactions with a particular attention devoted to the main polymerization techniques which can be included into two main groups, such as homogeneous polymerization systems and heterogeneous polymerization systems.
Nowadays, several types of synthetic polymers or copolymers are produced in the laboratories and these macromolecules can find applications in every branch of medicine, thus, the most employed synthetic materials in biomedical field were also reviewed.
Mechanisms of Polymer Synthesis
The mechanisms of polymer synthesis reactions can be classified into two main categories: step-growth and chain polymerization.
Step-growth polymerization occurs when monomers bond together through an extension of normal organic condensation reactions in which side products, characterized by low molar weight such as water or alcohol, are eliminated as the link is formed. These reactions can be achieved through reacting molecules incorporating functional groups including carboxylic acid, carboxyl derivative, alcohol or amine. Therefore, step-growth polymers can be degraded to their starting monomers upon the addition of the eliminated small molecules.
On the other hand, chain polymerization involves the linking of unsaturated monomers by the opening of the π double bond. The monomeric units are added to the reactive sites onto the growing polymeric chain consisting of an all-carbon backbone of single σ bonds. This reaction mechanism requires an initiator able to generate the first active unit and start the chain growth. Chain polymerization is involved in the production of a large share of the most employed synthetic polymers including polyethene, polypropylene, polystyrene and PVC.
Step-growth Polymerization
Kinetics of Step-growth Polymerization
Polyesters are formed by typical condensation reactions involving the elimination of water and an example of polyester synthesis from a diol and a diacid is reported as follows:


The obtained dimer might form a trimer, by reaction with a diol monomer or with a diacid monomer, but it could also react with itself to form a tetramer. Then, the tetramer and trimer proceed to react with themselves, with each other, with the monomer and the dimer [1].
The rate of a step-growth polymerization is the sum of the rates of reactions which take place between molecules of different size, therefore, in this case the kinetics is difficult to analyze. However, the kinetics of step-growth polymerization can be considered identical to those of analogous small molecule reaction and can be expressed as follows:
![$$\begin{aligned} & {-}{\text{A }} + {\text{ B}}{-} \, + {\text{ catalyst}} \to {-}{\text{AB}}{-} \, + {\text{ catalyst}} \\ & R = K\left[ A \right]\left[ B \right]\left[ {catalyst} \right] \\ \end{aligned}$$](/wp-content/uploads/2017/03/A320747_1_En_1_Chapter_Equ1.gif)
![$$\begin{aligned} & {-}{\text{A }} + {\text{ B}}{-} \, + {\text{ catalyst}} \to {-}{\text{AB}}{-} \, + {\text{ catalyst}} \\ & R = K\left[ A \right]\left[ B \right]\left[ {catalyst} \right] \\ \end{aligned}$$](/wp-content/uploads/2017/03/A320747_1_En_1_Chapter_Equ1.gif)
(1.1)
If the reaction is acid-catalyzed (catalyst = H+) and if stoichiometry of the groups A and B is assumed, the previous Eq. (1.1) becomes:
![$$R = - \frac{d\left[ A \right]}{dt} = K\left[ {H^{ + } } \right]\left[ A \right]^{2}$$](/wp-content/uploads/2017/03/A320747_1_En_1_Chapter_Equ2.gif)
![$$R = - \frac{d\left[ A \right]}{dt} = K\left[ {H^{ + } } \right]\left[ A \right]^{2}$$](/wp-content/uploads/2017/03/A320747_1_En_1_Chapter_Equ2.gif)
(1.2)
Mechanisms of Step-growth Polymerization
In a step-growth polymerization, the monomers polymerize following different reaction mechanisms, such as carbonyl addition-elimination, carbonyl addition-substitution, nucleophilic substitution, double bond addition or free radical coupling [2].
Carbonyl addition–elimination represents the most important reaction employed for the synthesis of polymeric molecules including polyamides, polyacetals, phenol–, urea–, and melamine–formaldehyde polymers. Carbonyl addition-elimination includes:
the direct reaction of a dibasic acid and a glycol (to form a polyester) or a dibasic acid and a diamine (to form a polyamide);
interchange (the reaction between a glycol and an ester);
the reaction of acid chloride or anhydride with a glycol or an amine;
interfacial condensation (the reaction of an acid halide with a glycol or a diamine proceeds rapidly to high molecular weight polymer if carried out at the interface between two immiscible liquid phases each containing one of the reactants);
ring versus chain formation (bifunctional monomers react intramolecularly to produce a cyclic product).
The other step-growth mechanisms include [3]:
Carbonyl addition–substitution reactions: the reaction of aldehydes with alcohols involving addition followed by substitution at the carbonyl group leading to the formation of polyacetals;
Nucleophilic substitution reactions: the reaction of an electron pair donor (the nucleophile) with an electron pair acceptor (the electrophile);
Free radical coupling: for the synthesis of polymers containing acetylene units and arylenealkylidene polymers.
Chain Polymerization
In chain polymerization, monomeric units incorporating double bond are rapidly added to the reactive sites onto the growing polymeric chain.
Three main categories of chain polymerization mechanisms can be considered:
free radical polymerization;
ionic polymerization, which can be further divided into cationic and anionic;
coordination polymerization.
In general, all these types of polymerization reactions are characterized by three main steps including:
an initiation stage, in which a reactive species is generated and attacks the first monomer molecule;
a propagation stage, in which a large number of monomers are added to the growing polymer chain retaining the active end-group;
a termination stage, in which the reactive end-site is deactivated.
Free Radical Polymerization
In free radical polymerization the monomer double bond opens homolytically, the initiator is a radical and the propagating reactive site is a carbon radical.
Free radicals are species containing unpaired electrons that are highly reactive and undergo reactions to extract an electron from another substrate. In this kind of polymerization, each polymer chain grows by addition of monomer to the free radical of the growing chain and, upon addition of the monomer, the radical is transferred to the new chain end.
Free radical polymerization consists of three stages, such as initiation, propagation and termination.
In the initiation stage, free radicals are produced from an initiator molecule and, then, react with the monomer. Initiators can decompose due to the application of heat or electromagnetic radiations (e.g., UV) and can be divided into two main classes, including peroxides and hydroperoxides and azo compounds, in which radicals are generated by the scission of a single bond or by an electron transfer to or from an ion or molecule during a redox reaction. Peroxides and hydroperoxides are frequently used as initiators because of the instability of the O–O bond. An example of organic peroxide is represented by benzoyl peroxide which decomposes on heating; at 100 °C, indeed, it has a half-life of 30 min. On the contrary, potassium persulphate K2S2O8 is an inorganic peroxide and, thus, water-soluble. In the case of azo compounds, the process is driven by the release of N2. The most common employed azo compound is AIBN (Fig. 1.4) which decomposes at relatively low temperatures (60 °C) and also at room temperature by irradiating with ultraviolet light (360 nm).
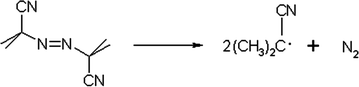
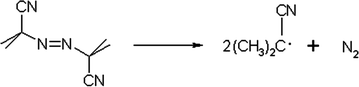
Fig. 1.4
Chemical structure of AIBN and its decomposition
The initiation step involves the dissociation of an initiator (I) with the formation of two radicals (R·) with a dissociation rate constant k d :


(1.3)
This radical then reacts with the monomer molecule to generate the first activated monomer (RM·):
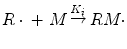
where k i is the rate constant of initiation.
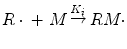
(1.4)
During the propagation step, the formed activated monomer (RM·) immediately reacts with more monomer molecules leading to growing macroradicals. In the polymerization mechanism, it is assumed that all growing chains have the same propagation constant (k p ) and for most monomers it is in the range of 102–104 L mol−1 s−1:
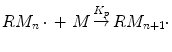
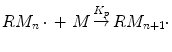
(1.5)
Termination stage consists of the deactivation of the growth process occurs by combination or disproportionation reactions. Combination is coupling of two radical species to produce a single “dead” polymer molecule:
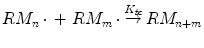
where k tc is the rate constant for termination by combination.
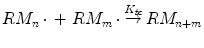
(1.6)
In disproportionation reaction, a hydrogen atom is abstracted and exchanged between the growing chains leaving behind two terminated chains and producing one deactivated polymer molecule with a saturated end-group and another one with a double bond as end-group:
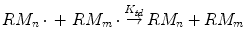
where k td is the rate constant for termination by disproportionation.
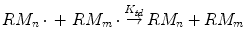
(1.7)
Kinetics of Free Radical Polymerization
In radical polymerization reactions, the initiator decomposition proceeds more slowly than the reaction of the free radical with the monomer molecule. Therefore, this is the rate-determining step.
The rate of initiation (R i ) is expressed by the following Eq. ( 1.8 ):
![$$R_{i} = - \left( {\frac{d\left[ I \right]}{dt}} \right) = \left( {\frac{{d\left[ {R \cdot } \right]}}{dt}} \right) = 2fK_{i} \left[ I \right]$$](/wp-content/uploads/2017/03/A320747_1_En_1_Chapter_Equ8.gif)
where f represents the initiator efficiency that indicates the fraction of the radicals successful in initiating chains (0 < f < 1), k d is the rate constant for initiator dissociation, [I] is the concentration of the initiator and the constant 2 defines that two radicals are formed from one initiator molecule. The initiator efficiency decreases when side reactions terminates the radicals [4].
![$$R_{i} = - \left( {\frac{d\left[ I \right]}{dt}} \right) = \left( {\frac{{d\left[ {R \cdot } \right]}}{dt}} \right) = 2fK_{i} \left[ I \right]$$](/wp-content/uploads/2017/03/A320747_1_En_1_Chapter_Equ8.gif)
(1.8)
In the propagation step, the rate of monomer loss can be equated to the rate of propagation (R p ) which is represented by the Eq. ( 1.9 ):
![$$R_{p} = - \left( {\frac{d\left[ M \right]}{dt}} \right) = K_{p} \left[ {R \cdot } \right]\left[ M \right]$$](/wp-content/uploads/2017/03/A320747_1_En_1_Chapter_Equ9.gif)
![$$R_{p} = - \left( {\frac{d\left[ M \right]}{dt}} \right) = K_{p} \left[ {R \cdot } \right]\left[ M \right]$$](/wp-content/uploads/2017/03/A320747_1_En_1_Chapter_Equ9.gif)
(1.9)
Finally, the rate of termination (R t ) is represented as:
![$$R_{t} = - \left( {\frac{dRM \cdot }{dt}} \right) = 2K_{t} \left[ {RM \cdot } \right]^{2}$$](/wp-content/uploads/2017/03/A320747_1_En_1_Chapter_Equ10.gif)
where k t is the overall rate constant for termination and the factor 2 comes from the fact that the two growing chains are terminated by each termination reaction.
![$$R_{t} = - \left( {\frac{dRM \cdot }{dt}} \right) = 2K_{t} \left[ {RM \cdot } \right]^{2}$$](/wp-content/uploads/2017/03/A320747_1_En_1_Chapter_Equ10.gif)
(1.10)
At the start of the polymerization, the rate of formation of radicals exceeds the rate of loss of radicals by termination. As the reaction proceeds, the rate of initiation becomes equal to the rate of termination (Ri = Rt) leading to the “Steady State”:
![$$\left[ {M \cdot } \right] = \left( {\frac{{fK_{i} \left[ I \right]}}{{K_{t} }}} \right)^{1/2}$$](/wp-content/uploads/2017/03/A320747_1_En_1_Chapter_Equ11.gif)
![$$\left[ {M \cdot } \right] = \left( {\frac{{fK_{i} \left[ I \right]}}{{K_{t} }}} \right)^{1/2}$$](/wp-content/uploads/2017/03/A320747_1_En_1_Chapter_Equ11.gif)
(1.11)
Degree of Polymerization
The degree of polymerization
is defined as the average number of monomer molecules added to the polymer molecule.

Kinetic chain length
is defined as the number of monomer molecules used per active center and it is represented as Rp/Ri = Rp/Rt [3]:
![$${\upnu } = \frac{{K_{p} \left[ M \right]}}{{2K_{t} \left[ {M \cdot } \right]}}$$](/wp-content/uploads/2017/03/A320747_1_En_1_Chapter_Equ12.gif)

![$${\upnu } = \frac{{K_{p} \left[ M \right]}}{{2K_{t} \left[ {M \cdot } \right]}}$$](/wp-content/uploads/2017/03/A320747_1_En_1_Chapter_Equ12.gif)
(1.12)
If the propagating radicals terminate by combination
, while if termination involves a disproportionation
.


Ionic Polymerization
Chain polymerization of monomers containing double bond can also be achieved with growing centers which can be negatively (anionic) or positively (cationic) charged.
Due to the ionic charge of the active center, these ionic polymerizations are more selective than free radical polymerization in which termination occurs by combination or disproportionation. Initiation stage, indeed, depends on the presence of appropriate substituent groups on the monomer molecule able to stabilize the active center, and on their inductive or resonance characteristics. For cationic active centers, electron-donating substituents (D), including alkoxy, alkyl or phenyl, are needed because they increase the electron density on double bond facilitating the linking to cationic species. On the other hand, electron-withdrawing substituents (W), such as cyano and carbonyl, stabilize the negative charge in anionic polymerization.
Radical species are neutral while in ionic polymerization charged species are involved; therefore, the type of solvent is of significant importance. High dielectric solvents, indeed, allow to completely separate the ions which are less sterically hindered and, thus, able to react and propagate faster than ion pairs.
Since the required activation energy for ionic polymerization is small, these reactions may occur at very low temperatures.
Another difference between radical and ionic polymerizations is that in the last one the termination step does not occur by a reaction between two ionic active centers because they are of similar charge [5].
Cationic Polymerization
In cationic polymerization typical catalysts are represented by strong electron acceptors including Lewis acids, Friedel-Crafts halides, Brönsted acids and stable carbenium-ion salts. However, many of them are not sufficient to initiate the polymerization and, therefore, require small amounts of a co-catalyst, usually a proton donor such as alcohols.
In Fig. 1.5 the mechanism of cationic polymerization is shown.


Fig. 1.5
Mechanism of cationic polymerization
The propagation stage is usually very fast and, therefore, polymerizations are in solution at low temperature ranged from −80 to −100 °C. The employed solvent is important because it affects the activity of the ion at the end of the growing polymeric chain.
Regarding the termination step, chain transfer to a monomer, polymer, solvent or counterion can terminate the growth of chains. If X+ is not loss and rejoins the anion to reform the acid catalyst, the termination is called “transfer to counterion”; if X+ initiates another monomer molecule to start a new chain, termination is defined as “transfer to monomer” [6]. When a distinct termination reaction does not occur, “living” cationic polymers are obtained.
Kinetics of Cationic Polymerization
The generation of active species can be described as follows:
while, the attack of the first monomer molecule is reported as follows:
where AX is the Lewis acid, BH is the Lewis base and M is the monomer.
![$$AX + BH \to \left[ {H^{ + } } \right] + \left[ {BAX} \right]^{ - }$$](/wp-content/uploads/2017/03/A320747_1_En_1_Chapter_Equb.gif)
![$$\left[ {H^{ + } } \right] + M \to \left[ {MH^{ + } } \right]$$](/wp-content/uploads/2017/03/A320747_1_En_1_Chapter_Equc.gif)
The propagation step consists of the sequential addition of monomers to the active complex [MH+]:
![$$\left[ {MH} \right]^{ + } + M \to \left[ {M_{2} H} \right]^{ + } \quad{\text{or}}\quad \left[ {M_{n} } \right]^{ + } + M \to \left[ {M_{n + 1} } \right]$$](/wp-content/uploads/2017/03/A320747_1_En_1_Chapter_Equd.gif)
![$$\left[ {MH} \right]^{ + } + M \to \left[ {M_{2} H} \right]^{ + } \quad{\text{or}}\quad \left[ {M_{n} } \right]^{ + } + M \to \left[ {M_{n + 1} } \right]$$](/wp-content/uploads/2017/03/A320747_1_En_1_Chapter_Equd.gif)
The kinetics of the propagation stage depends on the strength of the acid and the dielectric constant of the solvent. Indeed, the rate of the process is faster as stronger is the acid and higher is the dielectric constant that means more ions and a larger separation of the ions, respectively.
Kinetics of isobutene initiated by BF3/H2O system can be expressed as follows:
![$$Initiation{:}\quad R_{i} = K_{i} \left[ M \right]\left[ C \right]$$](/wp-content/uploads/2017/03/A320747_1_En_1_Chapter_Equ13.gif)
where C represents the catalyst/co-catalyst system.
![$$Propagation{:}\quad R_{p} = \left[ {MH^{ + } } \right]\left[ M \right]$$](/wp-content/uploads/2017/03/A320747_1_En_1_Chapter_Equ14.gif)
![$$Termination\,\,by\,\,rearrangement{:}\quad R_{t} = K_{t} \left[ {MH^{ + } } \right]$$](/wp-content/uploads/2017/03/A320747_1_En_1_Chapter_Equ15.gif)
![$$Termination\,\,by\,\,transfer\,\,monomer{:}\quad R_{tr} = K_{tr} \left[ {MH^{ + } } \right]\left[ M \right]$$](/wp-content/uploads/2017/03/A320747_1_En_1_Chapter_Equ16.gif)
![$$Initiation{:}\quad R_{i} = K_{i} \left[ M \right]\left[ C \right]$$](/wp-content/uploads/2017/03/A320747_1_En_1_Chapter_Equ13.gif)
(1.13)
![$$Propagation{:}\quad R_{p} = \left[ {MH^{ + } } \right]\left[ M \right]$$](/wp-content/uploads/2017/03/A320747_1_En_1_Chapter_Equ14.gif)
(1.14)
![$$Termination\,\,by\,\,rearrangement{:}\quad R_{t} = K_{t} \left[ {MH^{ + } } \right]$$](/wp-content/uploads/2017/03/A320747_1_En_1_Chapter_Equ15.gif)
(1.15)
![$$Termination\,\,by\,\,transfer\,\,monomer{:}\quad R_{tr} = K_{tr} \left[ {MH^{ + } } \right]\left[ M \right]$$](/wp-content/uploads/2017/03/A320747_1_En_1_Chapter_Equ16.gif)
(1.16)
Therefore, for both the termination processes, the dependence of rate and molar mass on the initial concentration of initiator and starting monomer are less complex than those of radical polymerization.
Anionic Polymerization
Monomers susceptible to this type of polymerization should be characterized by the presence of an electron-withdrawing group (W) able to stabilize the carbanion (Fig. 1.6).


Fig. 1.6
Mechanism of anionic polymerization
The reaction is initiated by strong nucleophiles and the most employed anionic initiators include Grignard reagents and other organometallic compounds, such as organolithium compounds which are air-sensitive, soluble in hydrocarbon solvent and very reactive towards molecules with labile protons.
In particular reaction conditions, characterized by a rigorous exclusion of starting reagents impurities, oxygen and water, the polymeric backbone chain can grow until all the monomer is disappeared, therefore, no termination or chain transfer occur. For this reason, anionic polymerization is sometimes called “living” polymerization and termination takes place only by the deliberate introduction of oxygen, carbon dioxide, methanol or water. The absence of a termination step during a living polymerization leads to a very narrow molecular weight distribution [7].
Kinetics of Anionic Polymerization
The reaction between styrene and potassium amide (KNH2) represents the first anionic polymerization studied. The kinetics of the three steps, initiation, propagation and termination, can be expressed by the following equations, respectively:
![$$Initiation{:}\quad R_{i} = K_{i} \left[ {NH_{2}^{ - } } \right]\left[ M \right]$$](/wp-content/uploads/2017/03/A320747_1_En_1_Chapter_Equ17.gif)
![$$Propagation{:}\quad R_{p} = K_{p} \left[ M \right]\left[ {M^{ - } } \right]$$](/wp-content/uploads/2017/03/A320747_1_En_1_Chapter_Equ18.gif)
![$$Termination{:}\quad R_{tr} = K_{tr} \left[ {M^{ - } } \right]\left[ {NH_{3} } \right]$$](/wp-content/uploads/2017/03/A320747_1_En_1_Chapter_Equ19.gif)
![$$Initiation{:}\quad R_{i} = K_{i} \left[ {NH_{2}^{ - } } \right]\left[ M \right]$$](/wp-content/uploads/2017/03/A320747_1_En_1_Chapter_Equ17.gif)
(1.17)
![$$Propagation{:}\quad R_{p} = K_{p} \left[ M \right]\left[ {M^{ - } } \right]$$](/wp-content/uploads/2017/03/A320747_1_En_1_Chapter_Equ18.gif)
(1.18)
![$$Termination{:}\quad R_{tr} = K_{tr} \left[ {M^{ - } } \right]\left[ {NH_{3} } \right]$$](/wp-content/uploads/2017/03/A320747_1_En_1_Chapter_Equ19.gif)
(1.19)
The initiation step is followed by propagation and termination takes place by a transfer process involving the extraction of a proton from the solvent ammonia by the growing anion.
Coordination Polymerization
The use of special catalysts may lead to the formation of very orderly structured polymers characterized by high stereospecificity.
The polymerization processes used in the synthesis of both isotactic polypropylene (i-PP) and high density polyethylene (HDPE) involve the use of transition-metal catalysts called Ziegler-Natta catalysts, which utilize a coordination type mechanism reaction.
Ziegler-Natta catalysts are organometallic complexes prepared by reaction of an alkil of a metal from Groups I to III in the Periodic Table (e.g. Al(C2H5)3) with a halide of transition metal from Groups IV to VIII (e.g., TiCl4) which are dissolved in a hydrocarbon solvent, such as toluene or n-heptane, at room temperature. The possible reactions, which take place during the preparation of a coordination complex catalyst from Al(C2H5)3 and TiCl4, are reported in Fig. 1.7.
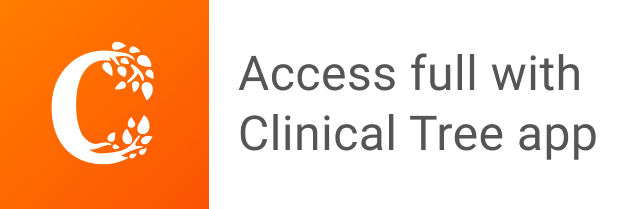