15 Occupational Health and Safety
George Petroka CIH, CSP
CONTENTS
Occupational Health and Safety Management
Accident Prevention Signs and Tags
Review Available Data for the Solids and Powders Handled and Processed
Perform Dust Flammability and Explosibility Testing
Combustible Dust Evaluation and Risk Assessment
Control of Hazardous Energy (Lockout or Tagout)
Clearances and Space Separation
Emergency Equipment and Response
Proactive Ergonomics: Principles for Workplace Design
Identification and Evaluation of Fire Hazards and Risks
Identification and Elimination of Fire Hazards
Installation and Maintenance of Protective Systems
Control of Firewater and Hazardous Material Runoff
Flammable and Combustible Liquids
Maintenance and Support Services
Maintenance-Specific Hazards and Risks
Areas of Safe Refuge and Assembly Areas
INTRODUCTION
Occupational health and safety pertains to all personnel who perform work at pharmaceutical facilities: it covers both company and contract employees working during routine, nonroutine, and construction activities. It addresses the chemical, physical, and biological hazards that may be handled and processed at the facility. It does not address the safety of the products, which are addressed through current Good Manufacturing Practices (cGMPs).
To effectively manage the occupational health and safety components of a pharmaceutical manufacturing facility, all potential risks must be assessed and controlled. Risk assessments follow a standard process and are performed by teams and competent staff having knowledge, experience, and understanding of their work activities and the hazards associated with those activities. Risk assessments provide a process that identifies and prioritizes the hazards, evaluates the effectiveness of existing controls, and identifies additional control measures as necessary. During the assessment, hazards are identified and their severity categorized, the adequacy of current and planned controls is analyzed, the probability of occurrence is assessed, and methods to eliminate or control the hazard are identified.
Risk assessments are important, as they form an integral part of a good occupational health and safety management program. Risk assessments systematically evaluate risks to employees and facility, create awareness of hazards and risks, identify who may be at risk (i.e., employees, cleaners, visitors, contractors, and the public), and determine if existing control measures are adequate or if an action plan to address identified gaps in control measures is needed. They also minimize risk of injuries or illnesses when done at the design or planning stage, prioritize hazards and control measures, and prioritize resources for continuous improvement.
The operation of a pharmaceutical manufacturing facility can present significant hazards and the associated risks. Internationally, occupational safety and health regulations, codes, and best industry practices have been developed to address many of the potential hazards. Many of the regulations require an assessment of risk in order to implement the appropriate controls. The facility occupational health and safety program must therefore include an effective risk assessment process that incorporates the applicable regulations, codes, and best industry practices. In addition, these risk management concepts and compliance requirements must be addressed during the design of the facility and through ongoing management of change.
OCCUPATIONAL HEALTH AND SAFETY MANAGEMENT
Health and safety management has the goal of providing guidance and direction in all phases of the safety program, including occupational safety and health, environmental control, fire safety, safety-oriented training programs, and building and equipment design criteria affecting safety codes and standards. Pharmaceutical companies must consider the health and safety of their employees to be of primary importance in the design, installation, and maintenance of all equipment, processes, and facilities, as well as during the performance of all operations.
From an occupational health and safety standpoint, the pharmaceutical company should comply with all country-specific, state, province, and local health and safety regulations in the design and operation of the facility. In addition, various organizations, including the International Society for Pharmaceutical Engineering (ISPE), publish consensus health and safety standards and guidelines having applicability to the pharmaceutical industry. Finally, the pharmaceutical company in many instances will adopt, as applicable, occupational health and safety regulations and guidelines as minimum requirements supplemented with pharmaceutical best industry practices. The most common example is the application of performance-based exposure control limits (PBECLs) for active pharmaceutical ingredients (APIs).
ACCIDENT PREVENTION SIGNS AND TAGS
Accident prevention signs and tags provide a method of warning of the presence of a hazardous material, hazardous condition, defective equipment, and so forth. Accident prevention signs are utilized in pharmaceutical facilities for normal operation, new construction activities, renovations, and emergency conditions. Minimum requirements for the wording, colors, and design for accident prevention signs and tags are specified by country-specific regulations and codes and include the following:
ANSI Z53.1, “Safety Color Code for Marking Physical Hazards,” and the identification of certain equipment, specifies standard colors and signs to be used in a safety and health program.
U.S. Occupational Health and Safety Administration (OSHA) 29 CFR 1910.145 outlines specifications for accident prevention signs and tags.
In Europe, the “Health and Safety (Safety Signs and Signals) Regulations 1995” implemented a European Council directive on minimum requirements for the provision of safety signs at work.
ACCIDENT PREVENTION SIGNS
Accident prevention signs provide a permanent method of warning of the presence of a hazardous material, hazardous condition, defective equipment, and so forth. The determination and use of accident prevention signs for a pharmaceutical facility should be identified during the design phase of a new facility or renovation. Accident prevention signs should be inspected and maintained as part of the facility’s preventative maintenance (PM) program to ensure the accident prevention signs are accurate for the hazard and work area and are legible and in good condition (Figure 15.1).
In general, accident prevention signs can be classified according to use as listed below:
Caution signs: Caution signs are used only to warn against potential hazards or caution against unsafe practices. Typically, the standard color of the background is yellow, and the panel is black with yellow letters.
Danger signs: Danger signs are used only where an immediate hazard exists. Typically, danger signs consist of the colors red, black, and white.
FIGURE 15.1 Accident prevention sign.
Directional signs, other than automotive traffic signs: These signs are typically white with a black panel and white directional symbol.
General safety signs: General safety signs are used where there is a need for general instructions and suggestions relative to safety measures. Typically, the standard color of the background is white, and the panel is green with white letters.
Slow-moving vehicle sign: This sign typically consists of a fluorescent yellow-orange triangle with a dark red reflective border. The yellow-orange fluorescent triangle is a highly visible color for daylight exposure. The reflective border defines the shape of the fluorescent color in daylight and creates a hollow red triangle in the path of motor vehicle headlights at night. The emblem is intended as a unique identification for vehicles that, by design, move slowly (25 mph [40 kph] or less) on the public roads.
Specific hazard signs: These signs utilize specific warning symbols (chemical, biological, and physical hazards; noise; laser; ultraviolet radiation; microwave radiation; etc.) to signify the actual or potential presence of a biohazard and to identify equipment, containers, rooms, materials, or combinations thereof that contain or are contaminated with viable hazardous agents.
Warning signs: Warning signs are used to indicate a potentially hazardous situation that, if not avoided, could result in death or serious injury. Typically, they have the signal word WARNING in black letters within a safety orange truncated diamond on a black rectangular background.
ACCIDENT PREVENTION TAGS
Accident prevention tags provide a temporary method of warning of the presence of a hazardous material, hazardous condition, defective equipment, and so forth. Accident prevention tags should not be used as a substitute for accident prevention signs. The designs of accident prevention tags should be the same as those of accident prevention signs. The messages on these tags will be removed or covered when the hazard no longer exists. Accident prevention tags should contain a signal word or emblem (such as Danger, Caution, or Biohazard) and a major message. The signal word should be readable from a distance of at least 5 ft and be understandable to all employees. The major message will indicate the particular hazard involved or instructions to the exposed person. Accident prevention tags will be located and secured as close as possible to the hazard (Figure 15.2).
FIGURE 15.2 Accident prevention tag. (From Seton. Available at http://www.seton.net.au/lockout-tagout/lockout-tags/accident-prevention-tags/accident-prevention-tags-out-of-service-m3368.html)
COMBUSTIBLE DUST
When a combustible dust is processed or handled, a potential for deflagration exists. The degree of deflagration hazard varies depending on the type of combustible dust and the processing methods used. For a dust explosion to occur, the following criteria must be met:
The dust must be combustible.
The oxygen content of the atmosphere in which the dust is dispersed must be sufficient to sustain combustion.
The dust concentration must be capable of supporting combustion.
The particle size distribution must be capable of supporting combustion.
There must be an ignition source for sufficient energy to initiate the explosion.
A dust cloud explosion can be prevented if any of the above five conditions is not met (Figure 15.3).
In order to assess the risk potential for the likelihood of a dust explosion occurring, one needs to characterize the fire and explosion properties of the dust, determine the likelihood that a dust cloud with the properties and conditions to propagate a flame may form, determine whether adequate sources of ignition exist, identify the types and tasks of operations involved, and review the frequency and duration of the tasks.
Pharmaceutical facilities that handle raw materials, intermediates, and APIs in powder form need to assess the combustible dust risks associated with handling these materials. This should include the assessments and tests discussed in the following sections.
REVIEW AVAILABLE DATA FOR THE SOLIDS AND POWDERS HANDLED AND PROCESSED
A list of the raw materials, intermediates, and final products handled and processed at the facility should be assembled with the available dust combustibility and explosibility data on the solids and powders.
PERFORM DUST FLAMMABILITY AND EXPLOSIBILITY TESTING
Initial screening tests should include the following:
Explosibility screening test—A/B classification: The explosibility screening test determines whether a powder or dust will explode when exposed to an ignition source when in the form of a dust cloud. The test results in a material are classified as either Type A (explosible) or Type B (nonexplosible). Thus, the test is also known as the A/B classification test. If the material is determined to be explosible, it will be further subjected to the minimum ignition energy and minimum explosible concentration tests described below.
FIGURE 15.3 Fire and explosion pentagon. (From Airsystemsales, Inc. Available at http://www.airsystemsales.com/combustibledust/)
Minimum ignition energy (MIE) test—dust cloud: The MIE test determines the lowest spark energy capable of igniting a sample when dispersed in the form of a dust cloud. This test is used primarily to assess the potential vulnerability of powders and dusts to electrostatic discharges, but is also relevant to frictional sparks.
Based on the data from these tests, additional testing may include:
Minimum explosible concentration (MEC) test: The MEC test determines the smallest concentration of material in air that can give rise to flame propagation upon ignition when in the form of a dust cloud. This test involves dispersing powder or dust samples in a vessel and attempting to ignite the resulting dust cloud with an energetic ignition source. Trials are repeated for decreasing sample sizes until the MEC is determined.
KSt (DPmax) Test: These tests are measures of explosion severity that are used in relief vent sizing and the design of explosion suppression and containment systems.
COMBUSTIBLE DUST EVALUATION AND RISK ASSESSMENT
A comprehensive combustible dust evaluation and risk assessment should be performed by first reviewing relevant solids and powder data (including material specifications); process equipment specifications; process, material flow, and equipment arrangement drawings; and safety procedures pertaining to handling combustible powders and dusts.
Following this review, a detailed site inspection of the facility, equipment, and operations should be performed. As part of the site assessment, key elements relating to powder handling, ignition sources, and electrical hazards and static electricity relating to the safe handling of combustible powders and dust explosion control and minimization will be evaluated utilizing best process engineering and chemical industry practices. These include
Powder dust explosivity characteristics, including MIE, MIT, and KSt values
Process batch size
Charging and discharging of the equipment
Grounding, bonding, and static dissipation of equipment and personnel
Facility design issues, including conductive flooring and grounding bars
Heating, ventilation, and air conditioning (HVAC) system, dust control and collection, and support utilities
Personal protective equipment (PPE)
Operability impacts to the process
Equipment cleaning and maintenance activities
Employee work practices
CONFINED SPACES
Confined spaces are defined as locations that meet the following criteria: they are large enough and so configured that they can be bodily entered, there is a limited means of access and egress, and they are not intended for continuous occupancy. Common examples of confined spaces in a pharmaceutical manufacturing facility include storage tanks, process vessels, tumble blenders, covered mixers, air handlers, and ductwork. Other less obvious confined spaces include manholes, vaults, pits, underground storage tanks, and trenches.
The hazards associated with confined spaces are potentially severe. Confined spaces may contain unknown or very high concentrations of airborne contaminants, including gases, vapors, and dusts at levels that are immediately dangerous to life or health; oxygen-deficient or oxygen-enriched atmospheres; potentially flammable or explosive atmospheres; contents such as liquids or powdered materials that could engulf a person; and a variety of other hazards, such as electrical, mechanical, thermal, or fall hazards. They may also have inwardly converging sides or a configuration such that a person could become trapped.
Pharmaceutical facilities that include confined spaces as part of the production or utilities should develop and implement the means, procedures, and practices necessary to ensure safe operations when employees must bodily enter confined spaces to perform cleaning, maintenance, and servicing activities.
The risks associated with potential confined space conditions should be assessed during the initial design phase for a new pharmaceutical facility or pharmaceutical process.
Because of the potential hazards associated with confined spaces, it is desirable to design the facility and select equipment such that the need to enter a confined space is eliminated. The need to enter a confined space can be eliminated for process vessels and tanks by designing and installing clean-in-place (CIP) capabilities to limit the need for entry to perform cleaning, and by identifying equipment with externally mounted features, such as magnetic stirrers, that do not require entry for servicing and maintenance activities. For manholes, pits, and so forth, the need can be eliminated by installing sensors and equipment that can be monitored and controlled remotely from outside of the confined space. For air handlers and ducts, select equipment that will facilitate maintenance and filter changes to be performed externally, and provide clean-out openings for ducts (Figure 15.4).
FIGURE 15.4 Confined space. (From Canadian Centre for Occupational Health and Safety. Available at http://www.ccohs.ca/oshanswers/hsprograms/confinedspace_program.html)
CONTROL OF HAZARDOUS ENERGY (LOCKOUT OR TAGOUT)
Pharmaceutical personnel servicing or maintaining machines or equipment may be seriously injured or killed if hazardous energy is not properly controlled. Injuries resulting from the failure to control hazardous energy during maintenance activities can be serious or fatal and may include electrocution, burns, crushing, cutting, lacerating, amputating, and fracturing body parts (Figure 15.5).
These hazardous energy sources include
Electrical energy, including stored electric charges
Hydraulic pressure
Pneumatic pressure
Pressurized gases and steam in process lines and piping systems
Chemical energy
Potential energy from suspended parts or springs under pressure
Kinetic energy from moving parts
Thermal energy
The risks associated with these hazardous energy sources must be assessed and controlled. In order to do so, it is imperative that all facility, maintenance, and production personnel have the ability to completely isolate equipment from all hazardous energy sources and achieve a zero energy state before commencing any servicing, maintenance, or cleaning activities. By rendering the equipment completely inoperative, affected personnel will be protected from injuries that could result from the unexpected reenergization or start-up of the equipment. To achieve a zero energy state, it is necessary to interrupt the transmission of all hazardous energy and physically prevent the restoration of that energy until the required work has been completed. Energy isolation devices, such as circuit breakers, electrical disconnects, and isolation valves, are the primary means for interrupting the transmission of hazardous energy. Locks should then be applied to the energy isolation devices to provide a physical barrier against the accidental restoration of energy (this is commonly referred to as lockout).
FIGURE 15.5 Danger: Use lockout before working on equipment. (From Ottawa Kent. Available at http://ottawakent.com/tag/lockouttagout/)
Hazardous energy control capabilities are an important factor in the design, selection, and operation of a pharmaceutical facility and its associated manufacturing equipment and utilities. In addition, prior to the designing of electrical and piping systems, the designers must anticipate the uses of the equipment and the maintenance, cleaning, and servicing needs to ensure that effective hazardous energy control can be designed into the system. Each process or piece of equipment must be equipped with energy isolation devices that are capable of being locked out. Energy isolation capabilities should be provided as close as possible to the individual process or piece of equipment on which work will be performed. In pharmaceutical facilities where APIs are being handled and equipment surfaces may be contaminated, it is desirable to provide localized lockout capabilities in each process room to eliminate the need for personnel to have to leave the room to implement the hazardous energy control procedures prior to servicing, maintenance, or cleaning.
All energy isolation devices must be readily accessible (e.g., located at ground level near equipment controls) with adequate clearance to accept the application of lockout devices. The design of the facility electrical and piping systems should be such that the application of any one energy isolation device will result in the minimal interruption of service to other equipment or processes. It is particularly important to provide an adequate number of isolation valves in pressurized liquid, gas, and chemical lines to help eliminate the need for hot tapping during maintenance activities. It is also important to plan for the ongoing maintenance of equipment and systems, including the changing of in-line filters and the removal and maintenance of inline pumps. In these cases, the types of appropriate isolation devices, such as isolation valves or flanges, must be installed to limit the potential hazards associated with line breaking. Electrical equipment that is equipped with capacitors or otherwise has the ability to store or build up an electrical charge must have the capability to be easily grounded and the charge dissipated. Equipment with suspended parts, moving mechanical parts, and springs must have the capability to be physically restrained.
There are many possibilities when it comes to hazardous energy control capabilities, and “one size” certainly does not fit all. In all cases, engineers and designers should work closely with the building owners and end users to ensure that hazardous energy control capabilities are incorporated into the facility design in order to ensure safe and efficient operations during maintenance, cleaning, and servicing activities.
ELECTRICAL SAFETY
Electrical systems should be looked at from two perspectives during the design, construction, and operation of pharmaceutical manufacturing facilities: personnel safety and operational safety. Building and electrical codes essentially mandate safe installation criteria and practice; however, it is crucial that the proper operational intent be fully evaluated prior to detailed electrical system design. Designers, engineers, and environmental health and safety (EHS) personnel should try to anticipate future operations and electrical needs to reduce the need for costly infrastructure upgrades. The rapidly changing pharmaceutical manufacturing environment could lead to early obsolesce of an electrical system, particularly in multipurpose manufacturing suites and buildings. For example, consider a suite that is constructed for the manufacture of aqueous-based products. Typically, ordinary rated electrical equipment would be installed. However, if a flammable solvent is needed for equipment cleaning and decontamination purposes, there may be the need for the installation of hazardous-rated electrical devices in certain areas of the suite. Identifying this during the design is critical.
In the United States, all electrical installations must conform to the National Electrical Code (NEC). This standard specifies all installation requirements for equipment and wiring of all voltages. Other countries have similar regulatory requirements and electrical standards. Design and installation should only be done by qualified electrical engineers and licensed electricians. A valuable international reference is the International Electrotechnical Commission (IEC). The IEC provides information on identifying and comparing electrical standards and equipment from varying countries (Figure 15.6).
FIGURE 15.6 Danger: Electrical hazard. (From Ibex Tech Corp. Available at http://ibextechcorp.com/how-to-prevent-electrical-hazards/)
Items that should be considered during the design of electrical systems and the installation of electrical apparatus are discussed in the next sections.
AREA CLASSIFICATION
Electrical equipment should be selected based on the hazards of the occupancy. Regulatory standards dictate the requirements for electrical equipment and wiring for all voltages where fire or explosion hazards exist due to the use or storage of flammable and combustible liquids, gases, dusts, or fibers.
The key is to ensure that electrical systems and apparatus are not potential ignition sources for hazardous materials. Process areas with hazardous-rated electrical equipment should be easily identified with warning signs to ensure that the basis of safety is not compromised.
STATIC ELECTRICITY
Static electricity can occur in all pharmaceutical manufacturing environments. Its presence not only creates safety risks, but also can affect product quality and process yield. Static electricity cannot be prevented; therefore, it must be controlled to reduce the risk of fire, explosion, personnel shock, and the effects on material handling. Static is generated any time dissimilar materials move together and are then separated. Typically, with more rapid movement of materials there exists greater potential for higher static charges. Static charges powerful enough to ignite flammable liquids, gases, and combustible solids can commonly occur in pharmaceutical operations such as liquid and powder transfer, on conveyor equipment, within ventilation systems, and by operators wearing synthetic garments and nonconductive footwear.
NFPA 77, “Recommended Practice on Static Electricity,” is an excellent reference on the fundamentals of static generation and control methodologies. FM Global’s Data Sheet 5-8, “Static Electricity,” also provides sound recommendations and practical guidance for static control. The more common control techniques are
Electrically bonding and grounding (earthing) all equipment, walking and working surfaces, hoods, ductwork, and conductive objects to the same electrical potential with a resistance to ground not greater than 106 Ω
Maintaining relativity humidity between 60% and 70%
Installing conductive flooring, wearing conductive footwear, and using clothing that does not create static
Installing static eliminators and dissipating devices
Avoiding the use of insulating materials such as plastic ducts and piping, plastic drums, and plastic drum liners unless they are specifically designed for static control
The generation of static can also affect the quality of products and manufacturing process effectiveness. Static accumulations can prevent effective transfer of very fine powders, causing the material to cling to containers, weigh scales, and operator’s hands and clothing. This can create risks of fire, explosion, and operator exposure, as well as loss of product into a process waste stream. With high-potency materials and high unit costs for active ingredients, these wastes can be very costly to the operation.
PROTECTING EMPLOYEES
Electrical installations that are completed in accordance with a recognized standard typically result in the proper level of electrical protection for personnel. Additionally, the application of safety standards that focus on safe electrical work practices ensures that personnel working with electrical systems are doing so safely. Safety devices such as circuit breakers, ground fault circuit interrupters (GFCIs), and emergency disconnects must be properly sized, installed, tested, and maintained to ensure personnel safety. GFCIs are required for all electrical services in wet or damp locations. This is particularly critical in pharmaceutical manufacturing operations where process areas are washed with water during routine cleaning or decontamination.
CLEARANCES AND SPACE SEPARATION
All electrical systems generate heat. To prevent premature failure of systems and equipment due to overheating, clear spaces must be maintained around the equipment to permit air circulation. Similarly, adequate clearances must be provided to prevent accidental ignition of ordinary combustible materials. Manufacturers and electrical standards provide specific guidance for these distances. These distances are also necessary to allow safe access for routine and emergency service.
EMERGENCY EQUIPMENT AND RESPONSE
The most important consideration in emergency planning and response equipment selection is the assessment of the risks related to an emergency occurrence. Consideration should be given to the types and quantities of hazardous materials handled and stored, and the equipment used in the facility. Response equipment should then be chosen based on the risk assessment.
EMERGENCY RESPONSE EQUIPMENT
A site must have and maintain an alarm system for personnel. There are different types of alarm systems, based on sound or light. Each area should be evaluated to determine the best alarm for the area and ensure adequate coverage of all areas in the facility. (Alarm systems should comply with the national or local requirements for employee alarm systems.) Areas where hazardous materials are used should be equipped with an eyewash and safety shower, spill kits, a first aid kit, a fire alarm, fire extinguishers rated for the hazard, and a fire suppression system. Typically, a high-efficiency particulate air (HEPA) filter vacuum is provided in pharmaceutical facilities where APIs are handled or processed to respond to spills of potent powders (Figure 15.7).
FIGURE 15.7 Emergency spill response kit sign. (From Stonehouse Signs. Available at http://stonehousesigns.com/product/hazardous-chemicals-and-materials-sign-emergency-spill-response-kit)
All emergency equipment should be in easily accessible locations that do not block emergency exit routes. In the case of eyewashes and safety showers, quick drenching or flushing of the eyes and body must be provided within the work area at a distance that requires no more than 10 s for personnel to reach. In addition, it must be located on the same level of the hazard, and the path of travel must be free of obstructions that may prevent immediate use of the equipment. Specific details about the placement and design of safety showers and eyewashes are presented in national regulations and consensus standards such as ANSI 358.1.
ERGONOMICS
Ergonomics can be defined in simple terms as fitting the job to the worker. Ergonomics is the study of preventing musculoskeletal disorders (MSDs) in the workplace. This includes the study of human behavior, abilities, and limitations in conjunction with the design of tools, machines, tasks, and the work environment with the goal of a productive, safe, comfortable, and effective interface between the work environment and employee (Figure 15.8).
In the pharmaceutical industry, common ergonomic issues involve strains and sprains from lifting heavy materials, and repetitive motion injuries from improper workstation design or tool design. A focus on ergonomics during the process design and equipment selection can reduce muscle fatigue, increase productivity, and reduce the number and severity of work-related MSDs. MSDs often involve the back, wrist, elbow, and shoulder.
A risk-based approach to prevention of work-related MSDs has been demonstrated to reduce the risk of developing MSDs by evaluating the proposed process and involving employees in review of mock workstation design and equipment plans. Reducing exposures involves evaluation of risk factors associated with workstations, tasks, and hand tools.
FIGURE 15.8 Ergonomic adjustments. (From JP Office workstations. Available at http://blog.jpofficeworkstations.com.au/2013/03/role-of-ergonomics-preventing-wmsd.html#.VfONGxFVhBc)
RISK FACTORS
Within the pharmaceutical industry, the primary ergonomic risk factors include awkward posture, forceful exertion, and repetitive motion, which affect the back (low back and neck) and upper extremities (arms, hands, wrists, and elbows). The risk factors, if not addressed, may lead to over-exertion and repetitive motion injuries and illnesses.
Awkward postures include reaching overhead or behind the head; twisting at the waist; bending the torso forward, backward, or to the side; squatting; kneeling; and bending the wrist.
Repetitive motion involves repeated motion of the same body part (typically upper extremity and back). The severity of the risks depends on the frequency, speed of the movement, muscle groups involved, and required force.
In evaluation of tasks, equipment, and tools, risk factors such as posture, repetition, and force should be assessed.
PROACTIVE ERGONOMICS: PRINCIPLES FOR WORKPLACE DESIGN
Prevention of work-related MSDs can be accomplished by recognizing, anticipating, and reducing risk factors during the planning stages. Design strategies should include incorporation of principles that reduce risk. These include keeping work close to the body; maintaining arms, shoulders, and wrists in a neutral position (avoid overextension of joints); avoiding bending forward and twisting the trunk and back; avoiding static muscle load (maintaining the same posture for extended periods of time); avoiding tasks above shoulder height (hands and elbows should remain below shoulder level when conducting a task); limiting the weight of a load to be lifted and utilizing mechanical lifting aids; avoiding carrying with one arm; and using transport accessories such as roller conveyors and mobile platforms.
Hand tool selection and evaluation of handling of small parts and containers should include evaluation of hand grip. A power grip is a grip in which the hand wraps completely around a handle or object and is of lower risk than a pinch grip or pistol grip.
ERGONOMIC PROGRAM ELEMENTS
Prevention includes implementation of an ergonomic process with emphasis on management support, worker involvement, training, risk identification, early reporting of symptoms, solution implementation, and program evaluation.
Tools for evaluation of risk are available through the Federation of European Ergonomics Society (FEES), National Institute of Occupational Safety and Health (NIOSH), Human Factors and Ergonomics Society (HFES), Southeast Asian Network of Ergonomics Societies (SEANES), Union of Latin American Ergonomics Societies (ULAERGO), Center for Registration of European Ergonomists (CREE), and Centers for Disease Control and Prevention (CDC).
FIRE PROTECTION
Within the pharmaceutical industry, compliance with cGMP standards and guidelines supports the overall objectives of a fire protection program. Cleanliness requirements, standardized operating procedures, and access control all contribute to the overall safe operation of a pharmaceutical facility.
The following overview of each of the key elements provides insight into the engineering and management of fire prevention and protection for pharmaceutical manufacturing plants. Engineering criteria are presented in general terms. Detailed design information can only be developed when the specific fire hazards and risks are available. There are many technical resources available to support fire protection engineering efforts. Agencies such as the National Fire Protection Association (NFPA) in the United States, the Health Safety Executive (HSE) in the United Kingdom, and FM Global produce fire protection reference standards and guidelines for use in the pharmaceutical industry. Many engineering firms also employ fire protection engineers who are well versed in the risks and protection needs of the industry.
IDENTIFICATION AND EVALUATION OF FIRE HAZARDS AND RISKS
The overall goal of any fire protection program should be to prevent fires from starting and to minimize the loss impacts of any fire that does occur. Fire prevention requires constant vigilance supported by protective systems, inspections, and fire response plans. The early detection of fire, the safe evacuation of personnel, and prompt actions to control and extinguish the fire are critical to safeguard employees, emergency responders, and the business.
Fire risk assessments must be completed for all sites and operations. The fire hazards must be identified, evaluated, and controlled using a combination of risk elimination, engineering controls, and preventative operating procedures (Figure 15.9).
IDENTIFICATION AND ELIMINATION OF FIRE HAZARDS
Whenever possible, fire hazards should be eliminated. This approach needs to start during the product and process development stage within research and development (R&D). The use of safe and environmentally friendly solvents can play a major role in reducing the combustible loading within a manufacturing plant. Similarly, changing to nonflammable cleaning and decontamination materials eliminates a fire hazard as well.
FIGURE 15.9 Oxygen, heat, and fuel. (From Elite Fire. Available at http://www.elitefire.co.uk/news/basics-fire-triangle/)
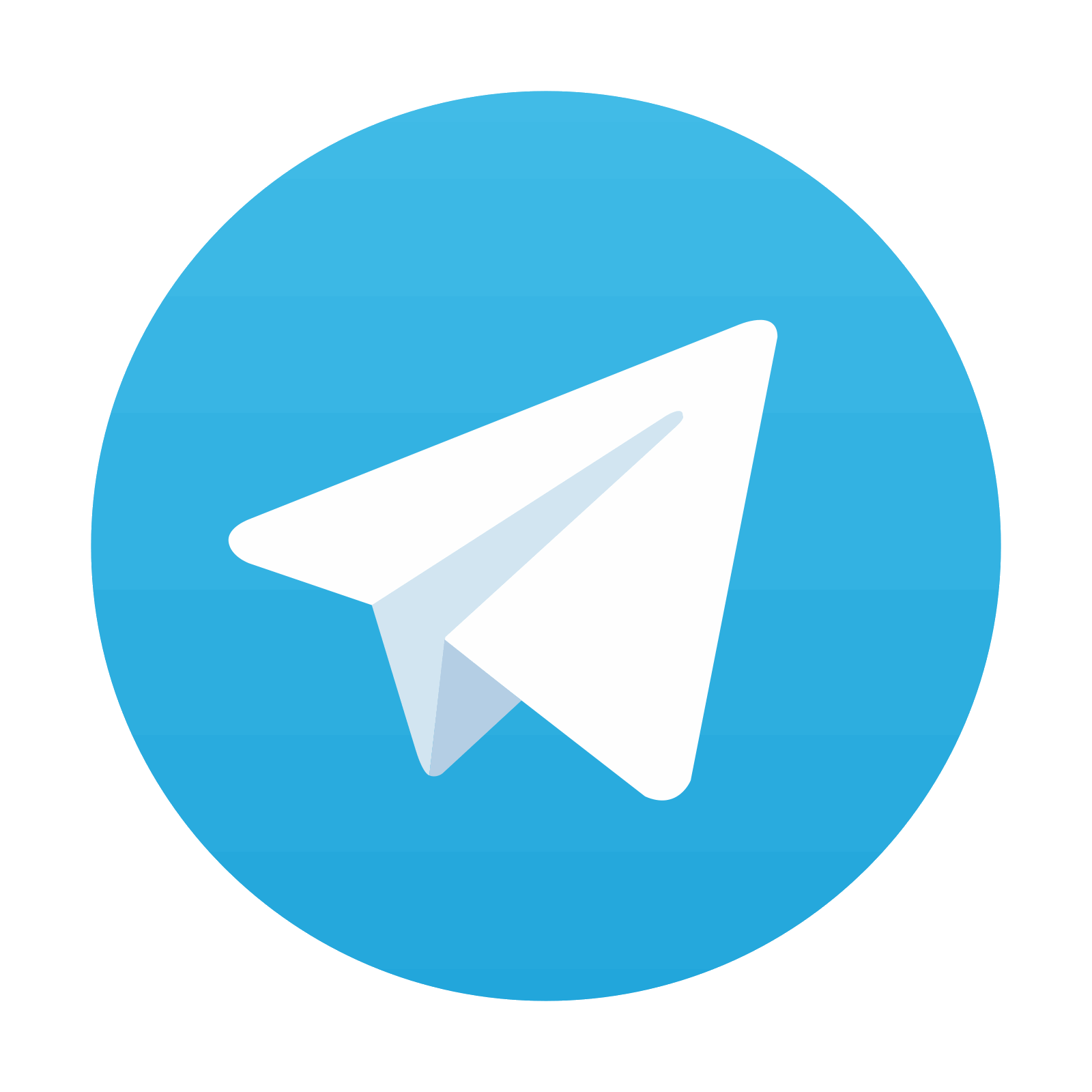
Stay updated, free articles. Join our Telegram channel
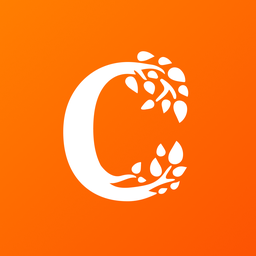
Full access? Get Clinical Tree
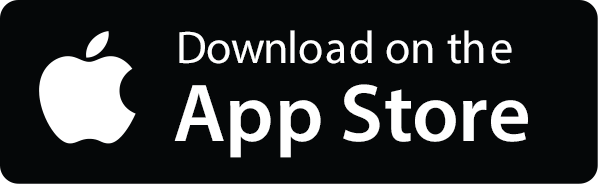
