!DOCTYPE html PUBLIC “-//W3C//DTD XHTML 1.1//EN” “http://www.w3.org/TR/xhtml11/DTD/xhtml11.dtd”>
Chapter 38: Material Storage, Identification, and Rotation
Material Storage
Storage locations should meet the general principles outlined for pharmaceutical manufacturing facilities in each of the good manufacturing practices (GMP), that is, United States 21 CFR Subpart C, European Union (EU) GMP Chapter 3, and World Health Organization (WHO) GMP Section 12. Additional requirements for storage areas are included in 21 CFR 211 Subpart H, WHO GMP Annex 9, WHO Technical Report Series 908 and Annex 5, and WHO Technical Report Series 937.
Storage areas should be of sufficient capacity to permit the orderly storage of materials and to facilitate cleaning and inspection, and materials should be stored off the floor. Storage areas should be designed to maintain any required label storage conditions, such as controlled temperature and humidity. Records should be maintained of temperature monitoring, and the monitoring equipment should be checked periodically and calibrated. WHO specifies that temperature mapping should show temperature uniformity. Areas should be clean and free from pests. Receiving and dispatch bays should protect materials from the weather and should enable cleaning of the materials before storage.
If quarantine status is maintained by storage in separate areas, these areas should be clearly marked, with access restricted to authorized personnel. Any system replacing physical quarantine should provide equivalent security, particularly for rejected, expired, recalled, or returned materials or products. The status of all materials should be identified.
Highly active materials, narcotics, and hazardous materials should be stored in dedicated areas and subject to additional safety and security measures. Materials should be handled and stored to prevent mix-ups and cross-contamination. They should be stored under conditions that assure their quality is maintained, and stock should be appropriately rotated.
Printed packaging materials should be stored in secure conditions with limited access. Cut labels and other loose printed materials should be stored and transported in separate closed containers to avoid mix-ups. Packaging materials should be issued for use by designated personnel in accordance with defined procedures.
Rejected materials and products should be identified and controlled to prevent their use before a final disposition by the quality unit (QU). Broken or damaged items should be segregated and withdrawn from usable stock.
Material Identification
Each container should be identified, and the status of the material should be controlled either by physical labeling and segregation or by electronic systems that provide equivalent security.
Stock Rotation and Control
WHO GMP contain more detailed guidance on stock rotation and control than either EU or United States Food and Drug Administration (FDA). Periodic stock reconciliation should be performed by comparing actual and recorded stocks, and any significant discrepancies should be investigated. Partly used containers should be securely closed and resealed to prevent contamination. Materials from opened containers should be used before those in unopened containers. Damaged containers should not be used unless the quality of the material has been shown to be unaffected. The QU should be notified of damage, and any actions taken should be documented.
Control of Obsolete and Outdated Materials and Products
Stocks should be checked periodically for obsolete and outdated materials. Procedures should be in place to prevent the issuance and use of outdated materials. Approved procedures should be in place for control of returned goods. All returns should be placed in quarantine pending disposition by the QU. Products returned from the market and that have left the control of the manufacturer should be destroyed; they may be considered for resale, relabeling, or recovery in a subsequent batch only after they have been critically assessed by the QU in accordance with a written procedure.
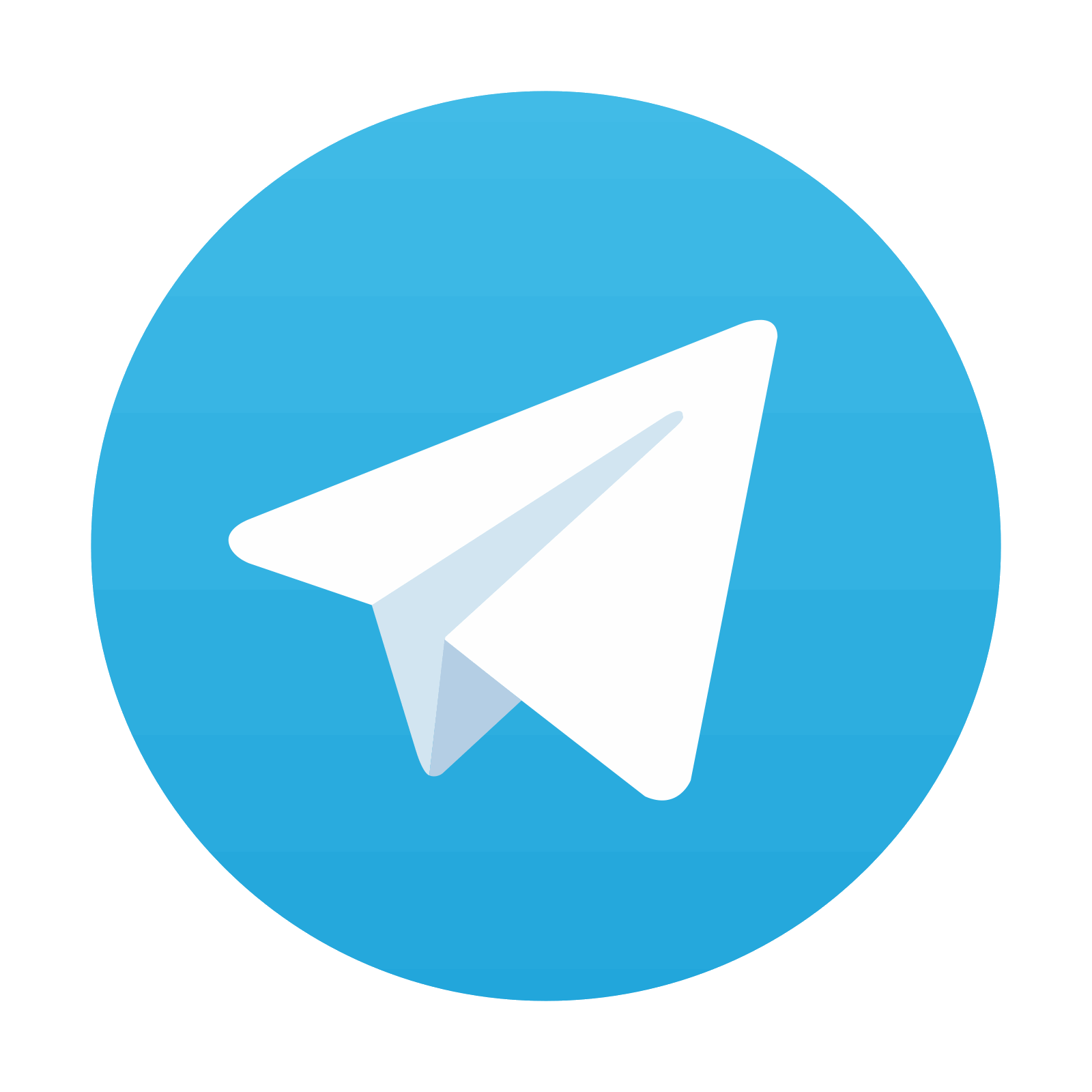
Stay updated, free articles. Join our Telegram channel
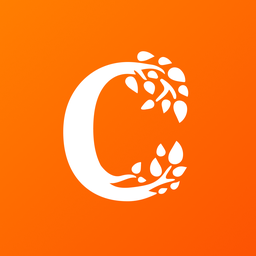
Full access? Get Clinical Tree
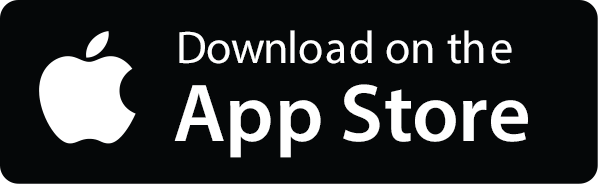
