!DOCTYPE html PUBLIC “-//W3C//DTD XHTML 1.1//EN” “http://www.w3.org/TR/xhtml11/DTD/xhtml11.dtd”>
Chapter 32: Maintenance and Metrology Systems
All instruments that control manufacturing facilities, utilities, and equipment must be maintained to ensure they are functioning as intended. Instrumentation should be uniquely numbered so it can be easily identified during calibration, maintenance, commissioning, and validation. Each instrument should have appropriate unique identification labeling permanently affixed; if the item is too small, the container that holds the device can be appropriately labeled. Associated documentation will link this unique identification to the instrument type, model, and serial number. Documentation includes when an instrument was put into service, its intended range of use, and when it was retired.
Based on the instrument category, installation qualification (IQ), operational qualification (OQ), and performance qualification (PQ) may be required when a new instrument, facility, utility, or equipment is introduced or replaced, or if instrumentation is moved from one location to another. A protocol should be written to define the purpose/objective, test procedures to be followed, parameters to be evaluated, and the criteria to demonstrate acceptability.
The IQ is conducted to ensure that the instrument and software, if applicable, were installed in the proper environment and manner as intended by the manufacturer. The OQ is conducted to ensure that the instrument and software, if applicable, operate as designed and generate accurate data. The PQ is conducted to ensure that the instrument and software, if applicable, meet the end user specific requirements and function as intended in the production environment. A report is generated to summarize the test results for the qualifications and any deviations. Upon completion of the qualification, the instrument can be put into service.
Facilities, utilities, or equipment used in the good manufacturing practices (GMP) environment will require routine maintenance and calibrations. The maintenance and calibration schedules can be established based on severity of environment, severity of use, frequency of use, durability of instrument, accuracy of measurement required, precision of measurement required, and history of maintenance and calibration. Each type of instrumentation should have a procedure that specifies its operation, maintenance, and calibration. The procedure must specify what activity should be conducted, what the acceptance criterion is, and the frequency. A logbook or software program may be used to track the usage, repair, and calibration. All maintenance and calibration information, which includes standards used, must be documented. When an instrument requires repair or calibration, it should be flagged as out of service (OOS) in some manner, such as with an “Out of Service” sticker. If an instrument fails the calibration, an impact assessment must be performed. During the impact assessment, all data generated since the last successful calibration must be evaluated. Upon completion of the repair or calibration, the OOS indicator is removed and the instrument is placed back into service. If the instrument was being calibrated, a new calibration sticker, which designates the next calibration due date, is applied.
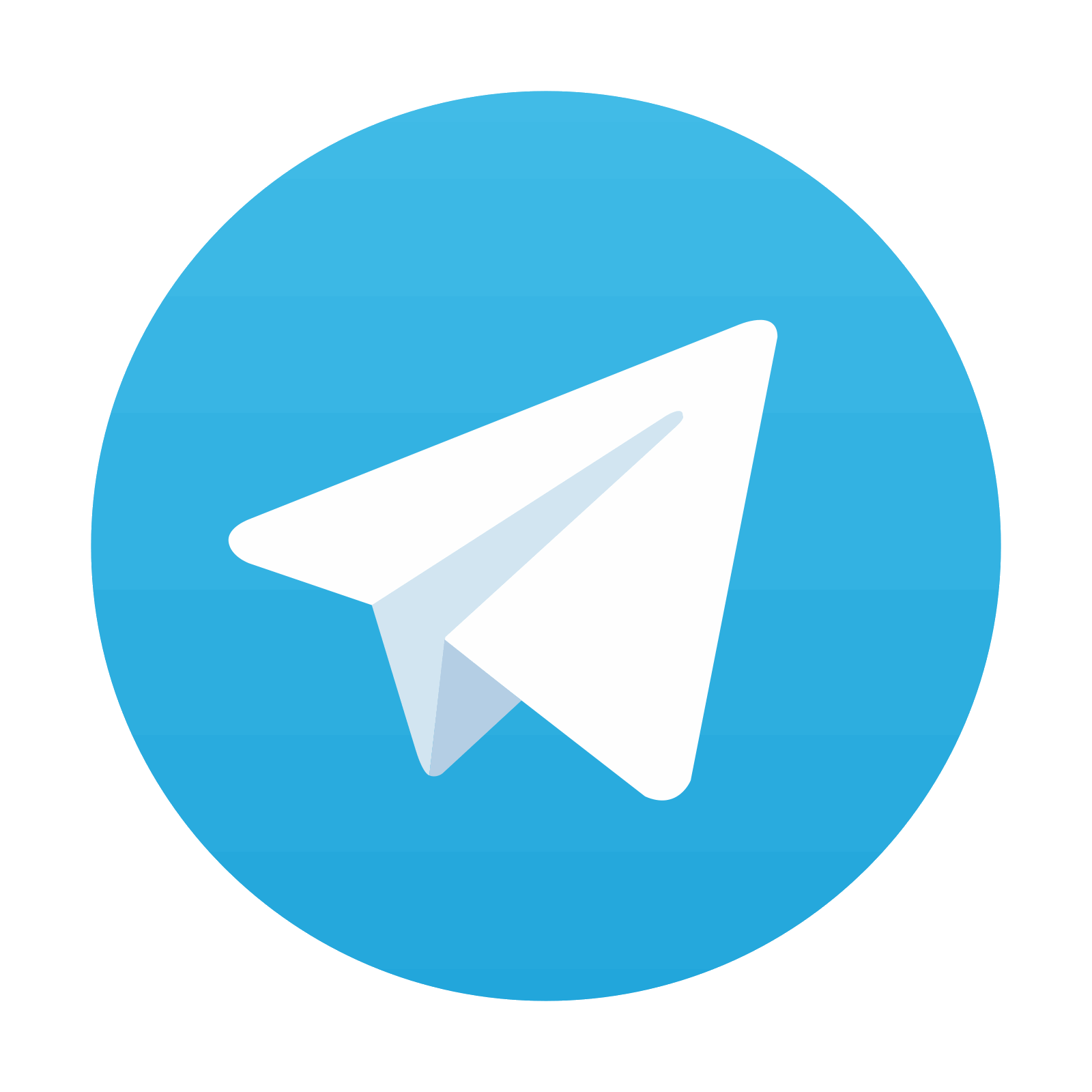
Stay updated, free articles. Join our Telegram channel
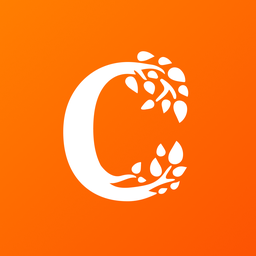
Full access? Get Clinical Tree
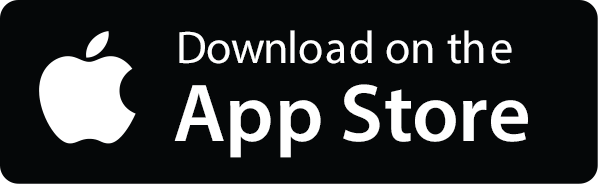
