3 Legacy Facility Master Planning
Eric Bohn
CONTENTS
Definition of a Legacy Facility
The Business Case for Legacy Facilities
Select an Alternative (The Master Plan)
Trends and Future Developments
INTRODUCTION
The development of the modern pharmaceutical manufacturing facility is deeply entwined with the history of the twentieth century. After the Second World War, there was an explosion in drug development. In order to make these innovative lifesaving products available to patients, a corresponding eruption occurred in the construction of manufacturing plants. With each new drug, and new class of drug, additional manufacturing capacity was required and then built. As a consequence, today there are many of these older facilities still in use.
Due to their longevity and the need to continue to support the needs of patients, such established plants often have undergone numerous additions and renovations. Given their age, coming to terms with these existing legacy facilities is a challenge. A steel-framed structure can last upwards of 100 years. To avoid waste and the loss of capital that has been invested, in both building and human infrastructure, it is necessary to learn to revitalize these important assets.
Legacy facilities were built for Good Manufacturing Practices (GMPs) that existed at the time of their construction. Over time, these standards have evolved and changed. In the other chapters of this book, GMP issues are individually explored in depth. This chapter does not study the individual issues, but instead explores the legacy pharmaceutical facility as a complete entity. As such, this chapter touches on all aspects of facility design and all aspects of facility GMPs. To successfully design a new manufacturing facility, it is necessary to understand GMPs. The special conditions of a legacy facility also require knowledge of GMPs. However, in this chapter, we focus on describing a process that leads to making established, older facilities a sustainable link within the larger framework of the corporate supply chain.
This chapter’s objective is to develop an understanding of the unique character of existing legacy facilities, their limitations, and the need to actively work to stay ahead of the curve in terms of industry changes in technology, quality assurance, and GMPs. In this chapter, we define legacy facilities, identify common issues and problems found in these facilities, and identify methodologies that can help manage legacy facilities for the long term. The intent is to enable management teams to maintain their facility as vital and sustainable now and into the future.
EXECUTIVE SUMMARY
KEY CONCEPTS
The following are key concepts that will be discussed in this chapter:
Legacy facility: An existing, older facility that has been successfully repurposed many times, over many years. Due to incremental changes and the pressures to act expeditiously, these facilities often face challenges staying current and sustainable.
Master plan: A comprehensive plan of action focused on a facility’s process capability and physical plant. A master plan is a long-term planning document that establishes a framework for future changes that brings together a site’s goals and aspirations and gives form and organization to define a realistic plan for action.
DEFINITION OF A LEGACY FACILITY
Merriam-Webster defines legacy as “something transmitted by or received from an ancestor or predecessor or from the past.” Legacy facilities are manufacturing plants that have been in use long enough that they have lived through several cycles of change. They develop over a period of time and, in the process, accrue incremental alterations that impact the integrity of the facility’s original configuration and operational strategies. When new products, equipment, and processes are introduced, necessary steps must be taken to accommodate them.
Because of their success, profitability, and investment in infrastructure, the expansion of such facilities will logically follow. To provide for more capacity and new product lines, new processes and spaces are added and old spaces reconfigured. These modifications to the original plant arrangement create correspondingly new patterns of material and personnel movement. When such changes happen, they are often relatively small in scale and accommodated through solutions that emphasize cost-effectiveness. Over time, these individual changes accumulate, and eventually the original building configuration and operational strategies can be impacted.
Beyond the immediate boundaries of these facilities, there are additional pressures that mount. Unlike the physical structure of an existing facility, regulatory and business environments are not frozen in time. For instance, advances in technology cannot be stopped. Neither are Good Manufacturing Practices static. Over time, they evolve, which is why GMPs have acquired the moniker of “current” Good Manufacturing Practices (cGMPs). These differences develop gradually, and over many years they become significant. Contrasting the understanding of GMPs from 20 or 30 years ago to the science and risk-based approach of the present reveals how divergent they can become.
In terms of business trends, the environment in which the pharmaceutical industry operates is also continually under change. Generics, outsourcing, and new therapies, such as gene and protein therapies, have all exerted their influence. In the end, as a facility ages, its ability to reflect the most up-to-date and best industry practices degrades. As these changes accrue, such facilities become characterized by compromises. Eventually, legacy facilities become burdened with outmoded infrastructure, equipment, and production facilities due to their inability to keep pace with the current standards.
The pharmaceutical industry developed quickly at the beginning of the twentieth century. Initially, drugs were predominantly produced by small manufacturers with little control over their claims or the reality of efficacy and safety. Our modern, large-scale pharmaceutical industry emerged as part of the war effort to develop and commercialize penicillin during the Second World War. Throughout the 1950s, an explosion in the discovery of new classes of antibiotics and vaccines occurred. At this time, funding for medical and scientific research expanded from $161 million in 1950 to more than $2.5 billion in 1968 [1]. In 1962, drug development was modernized by the Kefauver–Harris Amendments, which for the first time required that drug manufacturers scientifically prove that a medication was both safe and effective. This act also provided that the U.S. Food and Drug Administration (FDA) set GMPs for industry and further mandated regular inspections of production facilities. Since then, drug discovery and development have continued unabated, with new drugs being developed every year.
The large-scale production of pharmaceuticals requires large buildings to support this activity. With the success of new drugs comes the need for additional capacity, and in turn, existing facilities are typically expanded to meet that demand. Historically, these buildings have followed a common pattern of successive cycles of expansion and retrofit as new products and technologies are incorporated. Today, such legacy facilities are found throughout the industry. After many decades of pharmaceutical development, it is not hard to find facilities that were first constructed 30–40 years ago, and in some cases, even longer.
Over this same period of time, changes in technology and regulations have been monumental. At the beginning of the twentieth century, Bayer AG’s worldwide sales of aspirin attested to the industry’s long-standing international character. However, this was the exception. Today globalization is a fundamental condition of the pharmaceutical industry, and a global supply chain is the norm.
GMPs have evolved and are instituted worldwide by numerous regional agencies. So too equipment and process advances have been enormous, and aided by the computer revolution of the same era, highly sophisticated controls have contributed to higher product quality and cost-effectiveness. As these and other forces of change continue, making sure that legacy facilities are up to current industry standards is a continual challenge.
LEGACY FACILITY ISSUES
As legacy facilities grow older, the development of certain traits is predictable. These identifiable characteristics are a hallmark of such facilities. Examples include
Circuitous circulation
Crossing of material, equipment, and personnel flows
Excessive handling of materials
Inconsistent gowning practices
Inadequate segregation of unit operations, products, and batches
Inefficient organization of environmental or hygienic zones
Incremental change in an existing facility is usually accompanied by the need to disturb as little of the current operations as possible. Building within the limits of a legacy structure restricts the options available and, if not carefully planned, will eventually end up with inappropriate placement of activities. If a holistic approach that considers the entire facility is not undertaken, the only way to resolve odd placements of function is with the introduction of circuitous and inefficient circulation patterns. Circuitous circulation, as the name implies, leads to flows that are not directionally linear and frequently places unit operations out of sequence.
Crossing and backtracking of in-process materials, along with equipment increases the risk of both product mix-ups and cross-contamination. Also, the lack of integration within the existing flows inevitably increases the handling and staging of material.
Excessive handling of material is counter to the fundamentals of lean manufacturing and erodes operational efficiency and escalates handling time, as well as staffing requirements and ultimately operational costs.
Gowning needs to be appropriate for the processes being accessed. Because the greatest source of contamination in a GMP environment is typically the operators, gowning is a critical strategy for protecting drug products from contamination. While gowning also serves to protect the operator, this aspect is generally considered to be secondary unless a potent compound is involved. Properly locating de-gowning operations is important to avoid transporting product residue to adjacent areas, which, of course, increases the risk of product cross-contamination. In older facilities, confused or muddled placement of process operations can result in inadequate gowning and de-gowning locations and protocols. Or, alternately, the older gowning strategies that the facility was previously designed for may simply not be appropriate any longer.
Another concern with gowning is operational effectiveness. Gowning and de-gowning are time-consuming and require an abundance of gowning supplies (gowns, hair nets, booties, etc.). If not strategically located, gowning can occur too frequently. Multiple gowning operations just to gain access to a single manufacturing task slows the operation, which leads to excessive operating costs due to the inefficient consumption of time and materials. For this reason, when possible, gowning should be centralized, located to provide access to aggregated areas of the same level of gowning. Such a configuration will result in maximizing the operators’ time for actual production.
Segregation is another important GMP concept. Physical separation that creates autonomous spatial environments maintains isolation of different unit operations, raw materials, batches, and products. Keeping these materials from being exposed to each other prevents cross-contamination. In legacy facilities, after years of modifications, segregation can be poorly organized, inefficient, or ineffective. As a result, the risk of cross-contamination is increased. An alternative approach is to choose chronological segregation, which is to say careful timing and sequencing of the use of spaces and equipment, including cleaning. This approach is labor-intensive and not an efficient use of the building and its infrastructure, which is expensive to own and operate. A clear and simple physical segregation strategy is always the best approach and eliminates the human error that is possible when relying exclusively on procedures.
Related to segregation is the idea of hygiene zoning. This is a concept that goes by several different titles. Some organizations refer to it as cleanliness levels and some hygiene zones, while the International Society for Pharmaceutical Engineering (ISPE) refers to levels of protection. Regardless of the name, the idea revolves around the integration of several of the previous concepts. Working together, product quality is protected by the combined action of environmental control, segregation of product, segregation of unit operations, and appropriate gowning. These varying levels of operational zoning also require the design of clean room air systems, which minimize the risk of contamination through pressurization, air change rates, and air filtration. Like segregation, ill-defined and poorly organized hygiene zones that create isolated pockets of the same type of space almost always lead to increased staging and material handling, again leading to excessive operational costs. Grouping similar levels of protection together maintains the least amount of work from gowning and wiping down of materials that enter the area. In addition, air systems can realize improved economies of scale due to larger air handling units and more efficient ductwork. One of the best ways to uncover GMP issues in an existing facility is to plot the existing hygiene zones on a plan. The extent to which it is disjointed and unorganized represents a potential for GMP issues to exist. Such conditions are usually also representative of inefficient air systems, excessive material handling, and gowning problems. If such challenges are ignored and not corrected, the facility will increasingly become at risk of being identified by the regulating agencies as needing correction.
Incremental changes that occur in isolation can reduce the effectiveness of the entire facility. A change in one area can lead to bottlenecks, crossing of flows, or other inefficient and unproductive operational results. These are wasteful of time and manpower, all of which results in higher operating costs. Incremental changes also encourage expedient solutions that respond narrowly to the immediate business goal and discourage full consideration of the larger impacts to the facility now and in the future. It is necessary to have a larger game plan to avoid succumbing to these natural tendencies.
THE BUSINESS CASE FOR LEGACY FACILITIES
Why bother to preserve a legacy facility? In a global economy, surely there are alternatives to maintaining an old and outdated facility. By building new, however, there is much to be lost. Regardless of the current condition, by definition, legacy facilities have had a history of success. As such, established facilities incorporate attributes that can make them attractive to maintain as a vital part of a company’s current and future supply chain.
The first and most obvious reason to maintain an existing, aging facility is the capital investment already in the physical plant. Over the years, a significant amount of money and time have gone into establishing and maintaining a site. Expenditures in the physical plant include the structure, foundation, and building enclosure; utility feeds both to the site and into the building; and to the extent they can be reused, the internal utilities and services. In addition, there are usually numerous support functions already in place, such as warehouse, office, cafeteria, and quality assurance and quality control (QA/QC) laboratories that can continue to be leveraged. To replace such a facility means the previous investment disappears in its entirety.
A less obvious advantage of a legacy facility is the knowledge embodied in the staff. Developing, sharing, and effectively using organizational knowledge is no small endeavor and impacts product quality, as acknowledged by the International Conference of Harmonisation (ICH) Q10, “Pharmaceutical Quality System.” A tremendous amount of information is generated in establishing the critical process parameters and quality attributes of each product. While a formal system to gather, distribute, and utilize this information is important, the human factor cannot be undervalued, especially when dealing with existing products and processes. It is the existing staff that is the storehouse of this institutional knowledge. In addition, instilled in experienced staff is the company ethos and the industry’s culture of quality. Staff knowledge and experience, if completely eradicated, are not easily or quickly replaced. Recruiting and training new personnel takes a significant amount of time and money.
The previous examples illustrate monetary and operational losses that occur when an existing facility is taken out of service. But the financial losses do not end there. Before a new facility can produce product, design, construction, and validation must occur. This takes a prolonged period of time that is measured in years. By itself, the design and construction of a new facility is a multiyear effort. Commissioning and validation extend that timeline even further. And at the end of this long road, regulatory approval is not guaranteed. The financial commitment for a company is huge, easily taking hundreds of millions of dollars. The extended time required to design, build, and validate a new facility, as well as hire and train personnel, is a monumental undertaking. In contrast, working with an existing facility will save time and represents a substantial savings.
The potential loss of a facility should give a company pause. There is much to be lost in terms of investment, infrastructure, institutional knowledge, and skilled personnel. The closing of an existing facility is disruptive and should only be undertaken if a significant benefit is realized. Yet, in spite of the natural advantages of any particular legacy facility, such a plant must also fit into the larger strategy of the company’s entire global supply chain. But a strong and healthy facility, even if it is old, will invariably attract new products and will make a decision to close that site hard to justify. In this way, a plant’s long-term sustainability can be ensured.
THE MASTER PLAN
As outlined in the preceding sections, there are numerous tendencies and pressures for existing facilities to become outmoded. An additional tendency is the natural inclination for people to opt for expedient solutions, which is to say prioritizing facility modifications that address the narrow needs and concerns of the immediate without maintaining a view toward long-term sustainable value for the plant. It is tempting to choose the expedient because it can appear to be the easiest to implement, the least disruptive, perhaps the least amount of work, and often the least first cost. However, focusing only on the expedient can lead to existing deficiencies being exacerbated, especially those related to material handling and personnel circulation. In other words, yielding to the expedient can create greater problems over time. It is in a facility’s long-term interest to do more than just what it already does well. It needs to strive to stay vital within the larger context of the global organization and its supply chain. This means that a broader perspective must be used when making changes to the facility.
To be sustainable into the future, it is necessary to be strategic. Being strategic means having a set of goals and priorities, a considered policy, what is often referred to as a vision. It is necessary to continually ask: Where should the facility be in 5–10 years? What are the trends in the industry? What are the trends within the corporation? And ultimately, how can the facility position itself for a stronger future? Again, it is not enough to just do what a facility already does well. To not structure facility decisions strategically can result in options becoming limited and future opportunities lost. This in turn can only reduce a facility’s value to its parent company.
The solution then is to create a strategic plan for the facility, what is commonly called a facility master plan. The goal of the master plan is to create a program, based on careful planning, that ensures the realization of the site’s full value now and into the future. There are numerous functional components typically required for a manufacturing facility. These include the production area itself, but also all of the functions that support the manufacturing. These support functions typically include warehouse, QA/QC laboratory, office space, mechanical equipment, and personnel amenities such as cafeteria and gym. All of these need to be addressed in the master plan.
In developing a master plan, it is necessary to take a few common steps that can be enumerated simply as follows:
Define the issues (problem) and desired outcome.
Generate alternatives.
Evaluate the alternatives.
Formalize the final solution.
DEFINE THE ISSUES
The first step in any master planning process is to define the issues that need to be addressed. However, this is not always as easy as it may sound. Defining the issues requires the collection and processing of information. Correctly identifying information that is pertinent to fostering quality decisions is a critical first step. Sometimes planning personnel are overwhelmed by the accumulated detail and “can’t see the forest for the trees.” Alternately, if bad information is processed, you can end up with a situation described in a more contemporary phrase: “garbage in, garbage out.” In addition, to overcome the tendency to view problems only in established and accustomed ways, it is important to not rely exclusively upon solutions that have worked before. It is the process of master planning that provides a disciplined approach that goes beyond existing assumptions and helps identify the real constraints and opportunities of a site. Gathering and processing data in this systematic way allows you to prevail against those natural but counterproductive tendencies.
Gather Data
The first step in defining the issues for a master plan is to gather the pertinent data. This information will serve as the basis for understanding and evaluating the existing constraints and opportunities of the site. Attention needs to be given at this stage to ensure that the information is complete and accurate. Required data that should be gathered include, at a minimum, the items shown in Table 3.1.
TABLE 3.1
Data
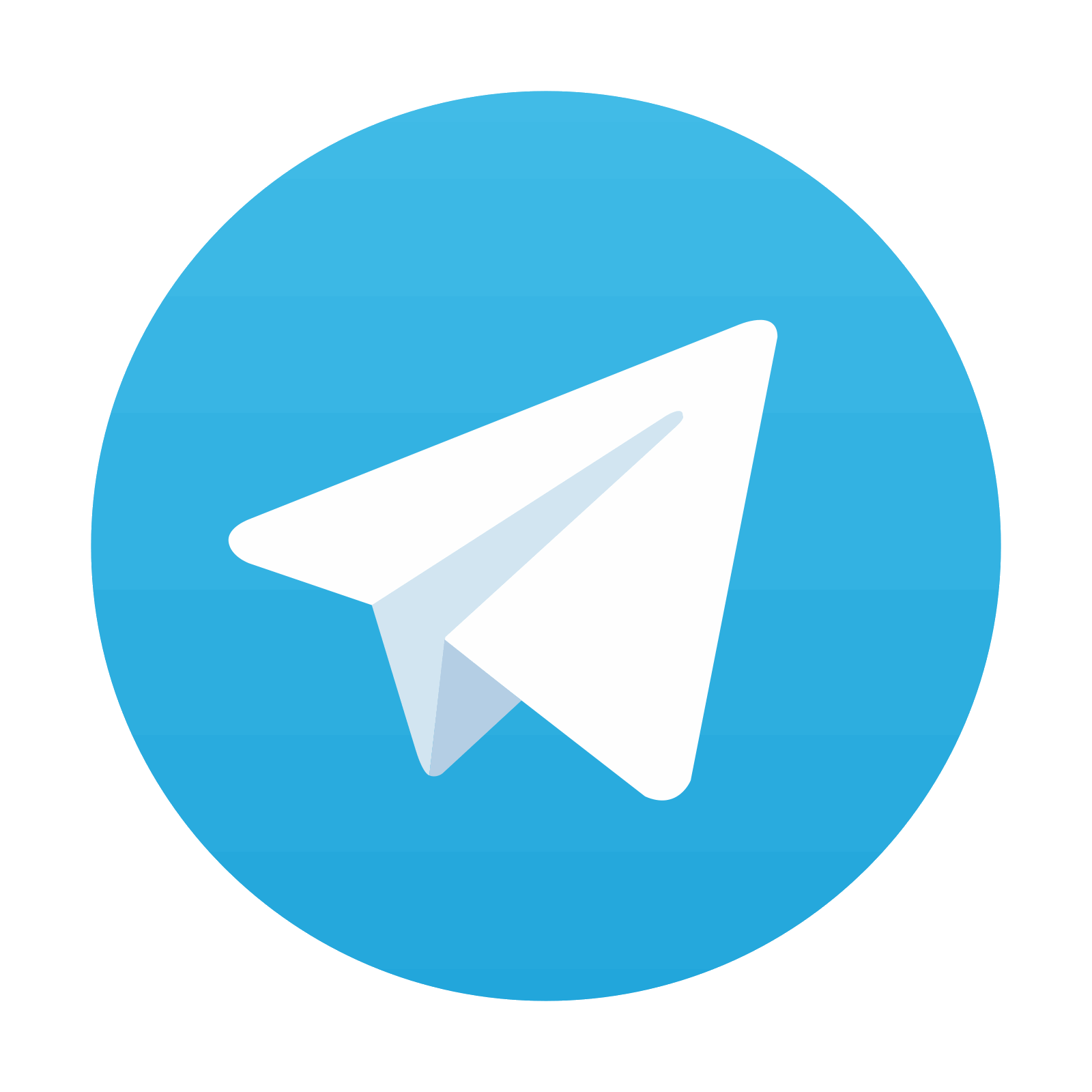
Stay updated, free articles. Join our Telegram channel
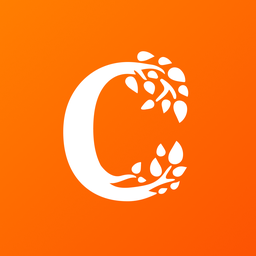
Full access? Get Clinical Tree
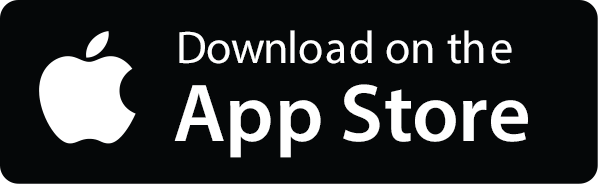
