Preparation of solutions to be used in the analysis can be documented on the controlled document or in a logbook designated for such preparations. Most laboratories have a solution preparation book where all solution preparations are documented. All pertinent information, such as chemical name, manufacturer, grade/purity, lot number/identification number, and expiration date, pertaining to reagents used and the method used to prepare the solution are documented. A unique identification number is assigned to the solution along with the appropriate expiry date. The solution is labeled with the unique numbers, solution description, and expiration date for future use. As the analyst follows the test method, all standard, if applicable, and sample preparations must be documented. If the analyst is making further dilutions, the dilution scheme must be documented. If the analyst uses timers, thermometers, sonicators, or water baths, all associated identification numbers and calibration/service due dates are recorded.
Once the sample preparation is complete, the analyst prepares the instrument used in the analysis. The analyst verifies that the instrument is within calibration; if not calibrated, the analyst ensures that the calibration is completed before use. The analyst captures the instrument identification number and calibration due date on the controlled document. The analyst conducts the analysis. If the instrument requires a sample sequence, the analyst will complete the necessary data entry before starting the analysis. Most computerized systems have a set method of analysis in the system; the analyst will verify that the correct method is used for the analysis. In most data acquisition systems, only system administrators with a certain level of authority are allowed to set up methods and revise them. The analyst conducting routine testing only has access to create run sequences. The analyst either documents or prints out the parameters used in the analysis. All printouts generated must be labeled with notebook and page/controlled document number, sample identification, number of pages, and the analyst name/date.
Once the run is complete, the analyst can evaluate the data. In some instances, the data acquisition system used has validated templates in which the data require no further calculations. If there is no associated template, the analyst may need to manually calculate the results or use a nonvalidated template in Excel. A sample calculation should be included to demonstrate how the analyst calculated the result. Once the analyst has completed the calculations, all paperwork can be completed, including reporting the final results on an analytical result form or in a data management system.
The analyst must review his or her work to ensure there are no obvious errors and must initial/date it to signify the work is complete. If errors were made, the error must be crossed out with a single line and initial/date/explanation included, then the correct information can be added (Figure 23.2). If one digit of a number or one letter of a word is incorrect, the analyst must cross out the entire number or word and make the correction. Any deviations from the method must be documented either as a planned or unplanned deviation and approved by management.
The analyst can begin to clean up the work area, but keeps all glassware in the bench area until it can be verified by a second analyst. All solutions are maintained until the analysis is complete and known to be correct.
Once the analysis is complete and documented, a second individual must review and understand the data and calculations. The reviewer ensures that all documentation is complete and accounted for. The data reviewer must ensure that the correct method and revision were used to perform the analysis. The data reviewer checks that all solutions used were prepared correctly and that all materials used were within expiry dating. The reviewer verifies that all instrumentation used was identified and within calibration. The data reviewer ensures that all the documentation is clear, and that comments are appropriate and easily understood. All laboratory investigations and deviations are reviewed, which will ensure that laboratory management has approved them. Any calculations made that are not part of a validated template must be verified. The data reviewer initials and dates the controlled document and any attachments to signify review. If any information needs to be corrected or added, the data reviewer does not sign until the analyst has made the correction/addition. When adding information after the analyst had added the final sign-off, he or she must designate the additional information with a late entry/initials/date to flag the additional information.
If a company has a validated electronic system, data are captured electronically. Such validated electronic systems include instrumentation data acquisition systems or electronic notebooks. These systems have routine backups and built-in security. System administrators are designated to maintain and qualify the system, and change controls are used to document any changes to the validated system. Each user must have a unique user name and a password to access the system. For a review, some validated electronic systems will flag the errors, such as out of specification (OOS) or out of calibration (OOC). Calculations do not need to be verified each time since the system was validated. All analyst and administration activities are documented in an audit trail that the reviewer can view. The audit trail review will indicate any suspicious activity that may require additional investigation.
Upon completion of the final data review, laboratory management conducts a final review to approve the data. Management ensures that all results meet the approved acceptance criteria and that all documentation is complete. Upon completion of the management assessment, laboratory management approves the data.
Once the raw data have been reviewed, they will be archived. If raw data are on paper, all raw data will be filed in a document control system. If the raw data have been collected electronically, the electronic information will be saved to a server that has routine backup and scheduled maintenance. Each company establishes its own document retention policy. Typically, raw data are maintained for seven years.
Once the data are approved, a certificate of analysis (COA) is generated. If data are stored in a validated electronic system, a COA may be generated automatically. The COA contains pertinent batch information, such as batch number and expiration date, and the test, acceptance criteria, and results. In some cases, a good manufacturing practices (GMP) compliance statement may be included. The COA may contain an electronic signature or a wet signature that indicates all results have been reviewed or approved. If a COA is manually generated, all information must be reviewed and approved to ensure accuracy. The COA is not considered raw data and does not need to be retained. In most cases, the COA is produced upon request from a customer, and the original is sent to them.
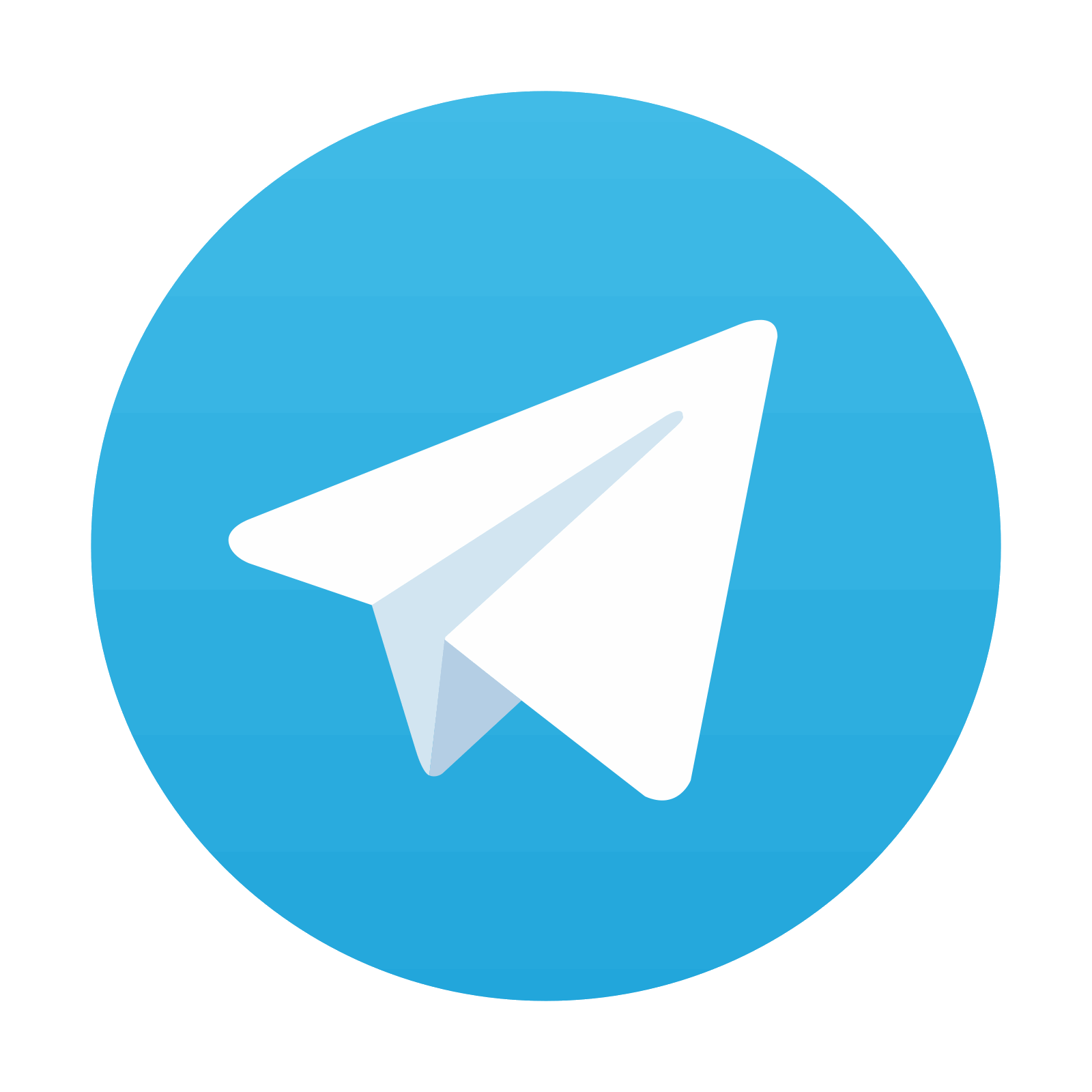
Stay updated, free articles. Join our Telegram channel
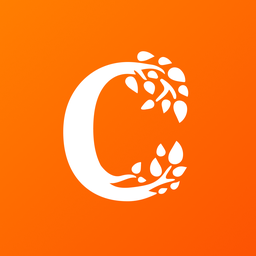
Full access? Get Clinical Tree
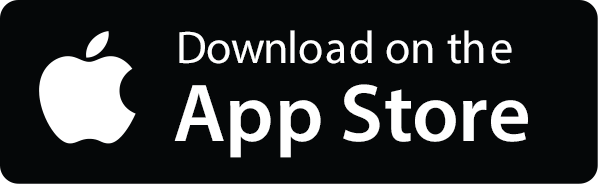
