Others may be involved for parts of the planning, for example, Health & Safety, Document Control, IT, etc., since almost every department will have some input into the program. The announcement of the project should be widely distributed and meetings publicized to allow input from all sources. A project manager or coordinator will integrate all aspects of the project and increase the likelihood that the project will run smoothly. The size of the facility, the types of products, and the experience of the staff (training) will have major impacts on the execution of the project.
Each department should provide the input necessary based on their expertise or needs. For example, the operations group will know how the equipment will be used during actual commercial production. They are the ones who will be providing the user requirements to the engineering group. The engineers will then develop the functional requirements and, subsequently, the design requirements. The functional requirements are those that set the way the equipment will operate and thus be able to perform their user requirements. The design requirements are those that are used to actually make the unit work, that includes the programming, the utility requirements, as well as all the process specifications. After the design is complete the request is sent to the purchasing department who will then request bids (with specifications) from vendors who can provide the unit of choice. Fig. 4.2 shows a general approach to a project that starts with the pharmaceutical company and moves through validation consultants and to the vendor.
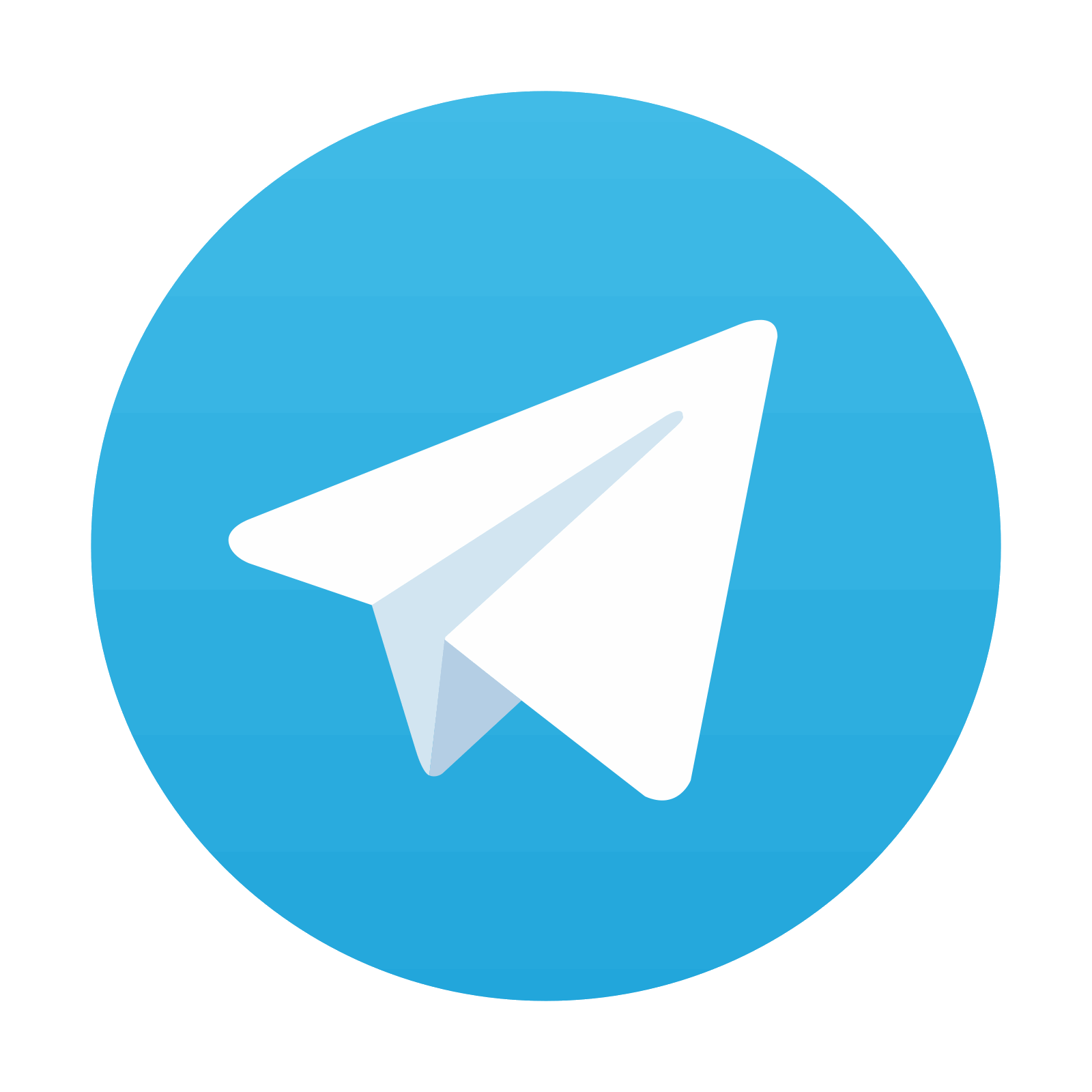
Stay updated, free articles. Join our Telegram channel
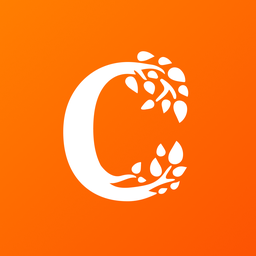
Full access? Get Clinical Tree
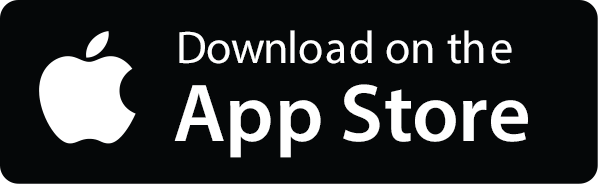
