NDCs follow one of the following numeric sequence configurations to make up the total 10 digits: 4-4-2, 5-3-2, or 5-4-1. For example, the NDC number for a 30-count bottle of Lexapro 10 mg tablets labeled by Physician’s Total Care, Inc., is 54868-4700-1, which follows the 5-4-1 numeric sequence configuration.
The first segment, or the labeler code, is assigned by the Food and Drug Administration (FDA) and identifies the labeler (manufacturer, repackager, or distributor).
The second segment, or the product code, is assigned by the labeler and identifies the drug product, including its strength and dosage form for the specific manufacturer.
The third segment, or the package code, is also assigned by the labeler and identifies package size and type.
In the Lexapro 10 mg example (NDC = 54868-4700-1), the numeric segments provide the following information:
54868 | Labeler code; indicates Physician’s Total Care, Inc. |
4700 | Product code; indicates product is Lexapro 10 mg tablets. |
1 | Package code; indicates package type and size is a bottle of 30. |
When pulling drugs from the shelf, technicians must verify that the intended and actual NDC numbers match. A mismatched NDC could indicate that the wrong drug, formulation, strength, or package size is being ordered or dispensed.
B. Manufacturers use lot numbers to identify internal production batches of drugs and other products. Lot numbers help trace specific products that require recall or removal from inventory.
C. The manufacturer’s expiration date, or shelf life, must appear on drugs and other pharmacy products. The expiration date indicates the date until which the manufacturer can guarantee the full potency and safety of the drug, provided that it is stored under required conditions.
Technicians should never dispense drug products after their expiration date. Inventory systems must include a process for detecting and returning expired or “short-dated” medications and products (products very close to the manufacturer’s expiration date).
D. The beyond-use date indicates the date after which the prepared or dispensed prescription may not be used by the patient. Technicians must clearly differentiate this date from the manufacturer’s expiration date.
As detailed in Section IV, the beyond-use date for compounded prescriptions is set at the time of preparation. For nonsterile medications repackaged from the manufacturer’s stock bottles into multi-dose or unit-dose containers, many state Boards of Pharmacy require that the beyond-use date be set at one year from the original dispensing date. The beyond-use date should never exceed the manufacturer’s expiration date.
III. Inventory Terminology
A. The term inventory refers to pharmacy products or merchandise (e.g., drugs, devices) available to meet future demand.
B. Inventory management is the system of ordering, storing, repackaging, and disposing of pharmacy products and merchandise. Pharmacies must have an inventory management system to ensure that:
- Needed drugs remain available to fill prescriptions;
- Unexpected drug shortages remain minimally disruptive to patient care;
- Products get purchased at the best price; and
- Drugs are ordered and disposed of efficiently.
C. Pharmacies use specific inventory control procedures to purchase products in sufficient quantity to meet the anticipated demands of customers, while controlling inventory size and costs. Chapter 19 contains additional information on inventory control.
D. Inventory turnover rate refers to the number of times pharmacies purchase, sell, and replace a product during a specific accounting period.
E. Par level denotes the inventory level at which a drug is automatically reordered. For example, when one stock bottle of amoxicillin 500 mg capsules remains on the shelf, pharmacies may automatically reorder the drug.
F. Stock rotation involves managing inventory costs by first using drug products that will expire soonest. For example, if two bottles of sertraline 50 mg remain on the pharmacy shelf, try to dispense the one that will expire first. This will help minimize the risk of a product expiring and then needing to be returned to the wholesaler for a partial credit.
G. Some pharmacies use automated order systems along with their inventory systems. Automated order systems reconcile actual drug inventory levels in the pharmacy computer when a drug gets dispensed, using bar code or other technology. When a drug quantity reaches a predetermined par level, that drug is automatically added to a daily order list or ordered electronically.
IV. Ordering Inventory
A. Identifying products that require ordering
- Determining which products to order depends on the inventory purchasing procedures of each individual pharmacy. Factors that influence product ordering decisions include expected inventory turnover rate, manufacturing sources, and purchase price.
- The formulary or preferred drug list will also influence ordering decisions, because medications included in the institution’s formulary or those medications preferred by payers will be dispensed more frequently. Chapter 7 contains additional information on formulary and preferred drug lists.
B. Depending on the pharmacy’s ordering system, technicians may need to enter the following information when ordering products:
- Pharmaceuticals
a. Drug name and manufacturer
b. Strength and dosage form of the medication (e.g., tablets, capsules, solutions, suspensions, injections, suppositories)
c. Type of packaging (unit-dose or bulk packaging)
d. Quantity contained in the unit desired (e.g., 100’s, 16 oz.)
e. Number of units
- Equipment, devices, and supplies
a. Name and manufacturer of product
b. Strength or size (if applicable) of product
c. Quantity contained in the unit desired
d. Number of units
e. Other information as required
C. Each pharmacy’s ordering policies will determine the product sources. Technicians should familiarize themselves with the ordering practices within their pharmacy. Drugs may be ordered and received from:
D. Controlled substances
Ordering procedures for controlled substances may require additional documentation. Controlled substances are classified as Schedules I through V, with the most frequently encountered controlled substances falling in Schedules II, III, and IV. Schedule II drugs such as oxycodone or methadone have a higher abuse potential and are subject to stricter documentation requirements than Schedule III or IV medications (e.g., hydrocodone combination products, alprazolam). Chapter 3 outlines the recordkeeping requirements of controlled substances.
E. Investigational drugs
Physicians conduct investigational drug studies in various practice settings to gather information about the appropriate use, efficacy, dosage, and safety of drugs that look promising for treating particular diseases. Chapter 3 contains more information on recordkeeping procedures for investigational drugs.
F. Expediting emergency orders
- Technicians should understand the delivery timetables of goods ordered from various sources. In the event that the pharmacy needs drugs quickly, technicians can obtain them from the most desirable source in accordance with pharmacy policies and procedures.
- In an emergency, the usual preferred sources may not be feasible, and the pharmacy may need to borrow or purchase the product from a nearby pharmacy or institution.
V. Receiving Inventory
A. Verifying specifications on original purchase orders
- Verifying products ordered versus products received. To ensure that the correct product was sent by the manufacturer or wholesale distributor, the technician must carefully examine the order and confirm that the information is consistent in all the components. Technicians should verify consistency with the original purchase order or “want book,” the invoice or packing slip received with the order, and the products received in the order.
The following information should be compared and verified in each of the following components for appropriateness and accuracy:
a. Drug name and manufacturer
b. Strength and dosage form of medication
c. Appropriateness of packaging type (e.g., unit-dose versus bulk packaging)
d. Quantity contained in the unit desired (e.g., 100’s, 16 oz.)
e. Number of units received versus number ordered
- Documenting goods received
a. Pharmaceuticals, durable medical equipment, devices, and supplies
(1) Technicians should note on the invoice the products received, as well as any product shortages.< div class='tao-gold-member'>Only gold members can continue reading. Log In or Register a > to continue
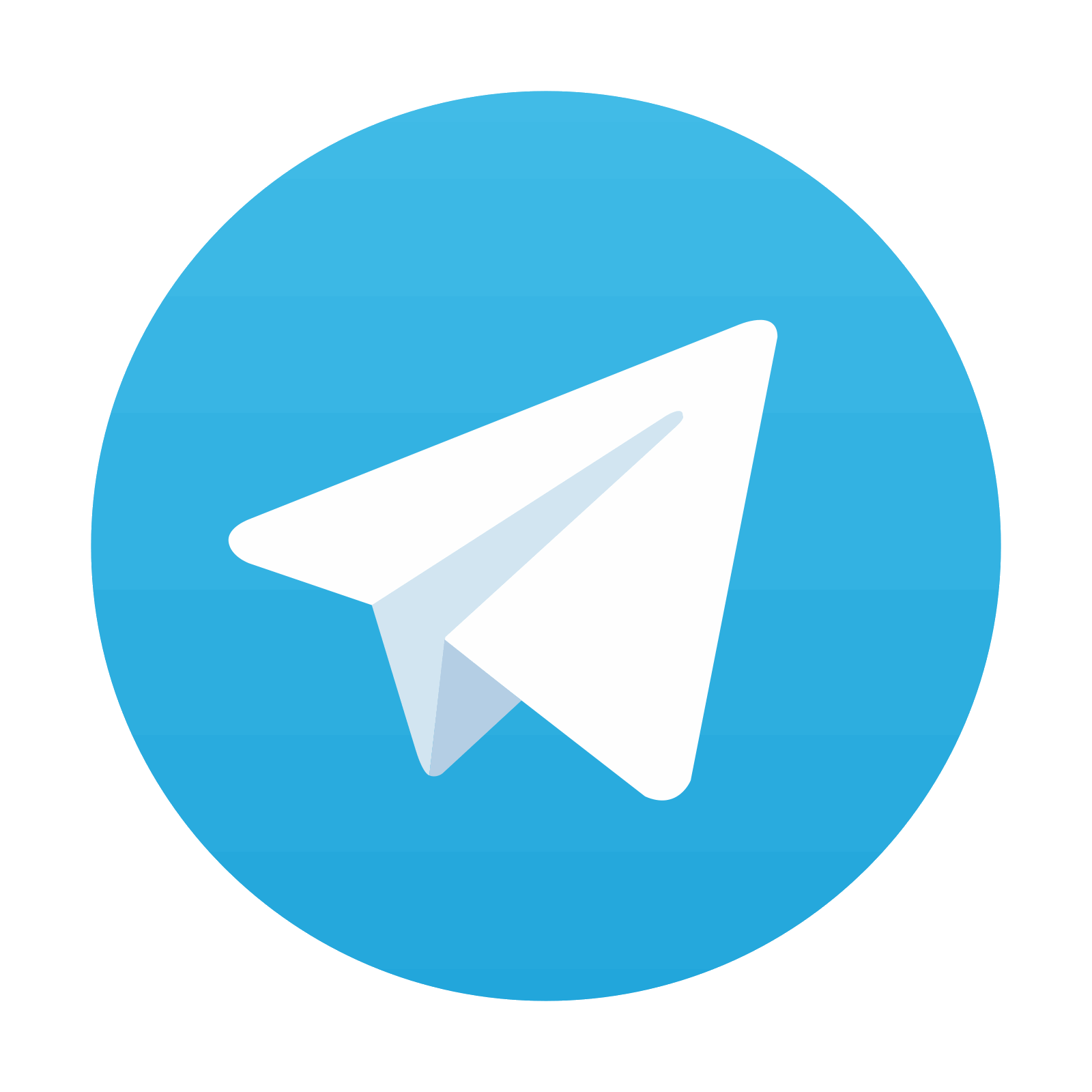