Staged Materials
Staging materials properly is a key process that prevents contamination or substitutions in a filling process and is accomplished through good line-clearance procedures with appropriate checklists and documentation of activities for each fill. The staging area for filling should be clearly marked for each filling process or line. All components needed for that fill should be brought to the corresponding staging area for the fill, and only components needed for that fill should be there. QA should check and ensure that all components are tested and released before staging for fill. Filled goods should have a location of their own and should not be commingled with components staging. Different products should not be packaged in close proximity unless there is clear physical segregation. The name and batch/lot number of each product being staged for fill, and the fill line, should be clearly displayed in the area. Filled goods should also be labeled immediately with the product name, batch number, and its release status. All staged materials should be reconciled at the end of the fill process, including any labels printed during the fill process.
Status Labeling
Products should be labeled immediately after fill, preferably in-line with the fill process to avoid any mistakes. Appropriate procedures for labeling in-line and off-line should be in place in case of any delays. All products at all stages should have a status label. The product should at a minimum have the batch number, product name, and release status. If a particular filled product is removed from the line for any reason, then the status label for that product should contain the reason, for example, QA sample, retain, nonconforming sample, and so on. Any filled goods without a status label are considered contaminated product. Therefore, care must be taken to have status assigned to products at all stages. Once the filling process is completed, all filled goods are removed from the line and located in a designated area with the status of “Hold.”
For each batch/lot of drug product, appropriate laboratory tests should be used to determine conformity to the finished product specifications. The filled goods taken from the filling process periodically as per filling procedures for quality control (QC) testing are tested for the criteria specified. Once these tests have been satisfactorily completed, the filled goods of that lot can be released. The products of that lot can be moved to released inventory. Products failing to meet the established specifications must be quarantined and a nonconformance process initiated. Products not meeting the specifications must be rejected and appropriately disposed of.
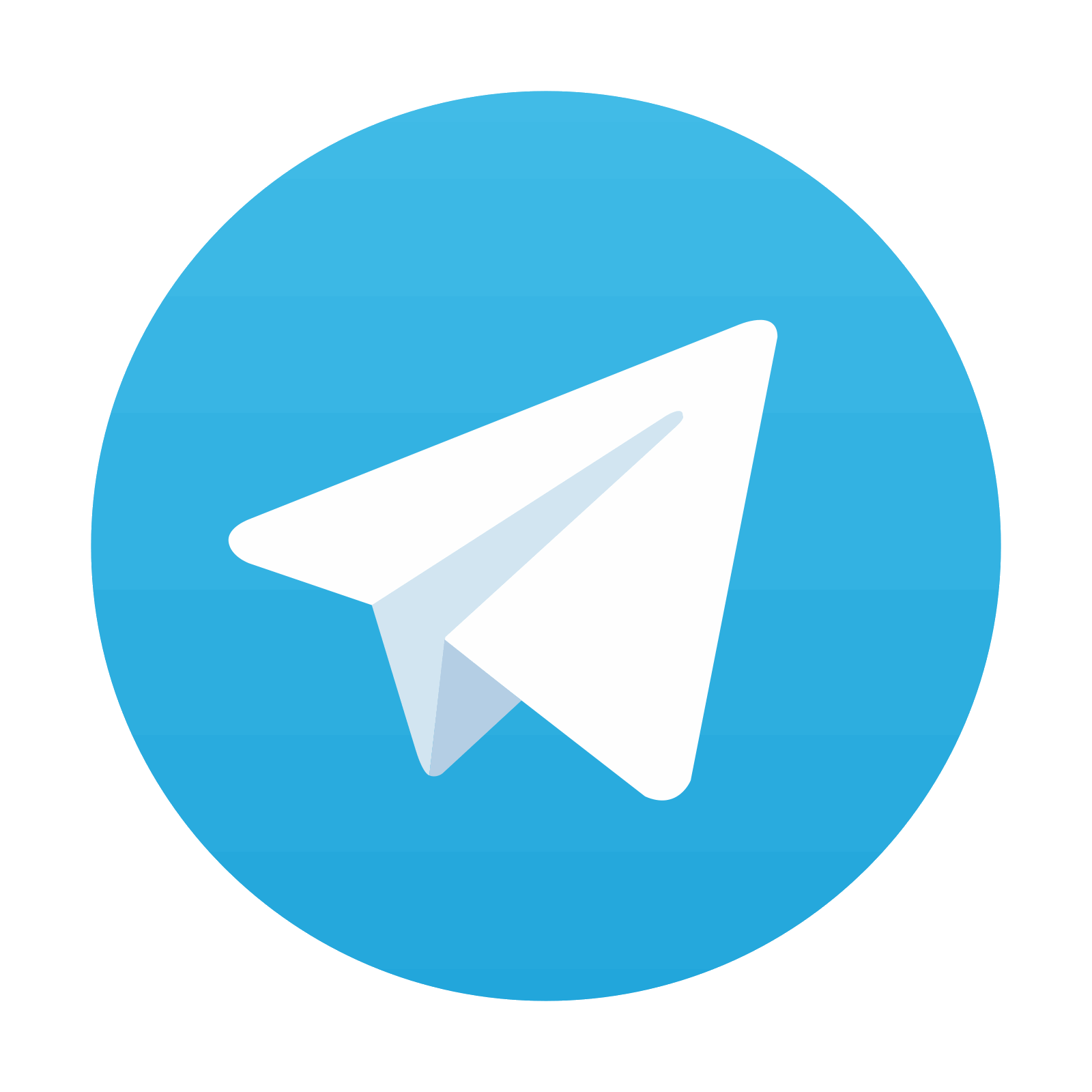
Stay updated, free articles. Join our Telegram channel
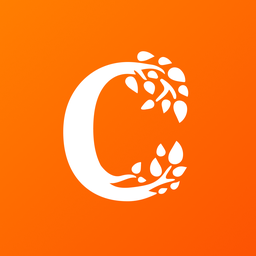
Full access? Get Clinical Tree
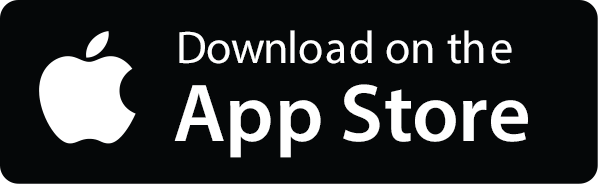
