!DOCTYPE html PUBLIC “-//W3C//DTD XHTML 1.1//EN” “http://www.w3.org/TR/xhtml11/DTD/xhtml11.dtd”>
Chapter 55: Filling and Packaging Records
An essential aspect of a robust documentation program is the existence of records that provide a detailed history of the manufacturing stages, testing, and any relevant event that was part of the execution of a batch of drug product. As a result, it is expected that the regulations for good manufacturing practices (GMP) of finished pharmaceuticals (21 CFR 211, Eudralex Volume 3, Chapter 4, among others) require companies to establish not only written procedures for the production of the finished drug products, but also batch production and process control records to assure product identity, strength, quality, and purity. The written procedures, as well as the batch records, provide clear instructions on how to execute a batch of drug product per approved procedures, and at the same time they guarantee uniformity from batch to batch.
Regulations and Guidance Documents
Filling and Packaging Records
Separate batch production record(s) are prepared for each batch of drug product to cover the different manufacturing steps from filling to packaging. The batch production records should be designed in such a way that they provide clear instructions on how to manufacture the batch and ensure consistency in execution from batch to batch even when differently qualified individuals execute the manufacturing operation. The filling batch production record should include:
• Initials or signature of the staff performing the operation.
• Dates.
• Component information including, but not limited to, material description, material number, quantity used, and expiration dating.
• Checks on the work area, such as line clearance procedures before the filling operation begins (area free of items not intended for use in the operation).
• Yield calculations at the end of each manufacturing step; these calculations are performed by a qualified individual and independently verified by another organizational unit staff member.
• Documentation on any major equipment used during the production of the batch and documentation of equipment suitability verification (for example, checks on calibration due dates, cleaning status).
• Manufacturing time constraints. When appropriate, time limits should be established for the completion of the filling step to guarantee the quality of the drug product; when deviation to the production time limit occurs, the event should be documented with a justification on the batch record.
• Fill weight calculation/verification
• Interventions and line stoppages on the filling batch record listing the time of the event and the duration of the intervention or line stoppage
• Any sampling performed
The packaging batch production record should include:
• Initials or signature of the staff performing the operation
• Product description (name, type, strength, pack size)
• Product specifications
• Inventory record of each component used during the packaging operation (cartons and labels, among others)
• Review of the label information against the established label specifications, including a copy of each label signed and dated by the staff responsible for label approval
• Line clearance operation of the packaging area before and after use
• Special precautions to be observed during the packaging process
• Any sampling performed
Production, Process Control, and Laboratory Record Review
The filling, packaging, and labeling records must be reviewed by the corresponding organizational unit and the quality unit (QU) to ensure that the finished drug product was manufactured according to the established and approved procedures. The review of the production and process control records must include an assessment of any event failures or deviations that could potentially affect the sterility of the product. Where deviations to the written procedures exist, the appropriate organizational units must document the changes and their corresponding justification. The production record review should include, but it is not limited to:
• Events that could have impacted the environment in the critical zone (an area designed to maintain sterility of sterile materials). Sterilized product, containers, closures, and equipment may be exposed in the critical zone.
• Review of maintenance activities that could have impacted the execution of the batch.
• Batch and trending data for utility and support systems (heating, ventilation, and air conditioning [HVAC], particle monitoring system, and so on).
• Documentation concerning adherence to critical process parameters such as fill time limits and sterilization expiration dates.
The laboratory records are reviewed to ensure compliance with specifications and standards. The information contained in these records comprises descriptions of the samples received for testing, batch number, quantity, the date the samples were taken, the date the samples were received for testing and tested, calculations, and the initials or signatures of the staff that performs and verifies the test results.
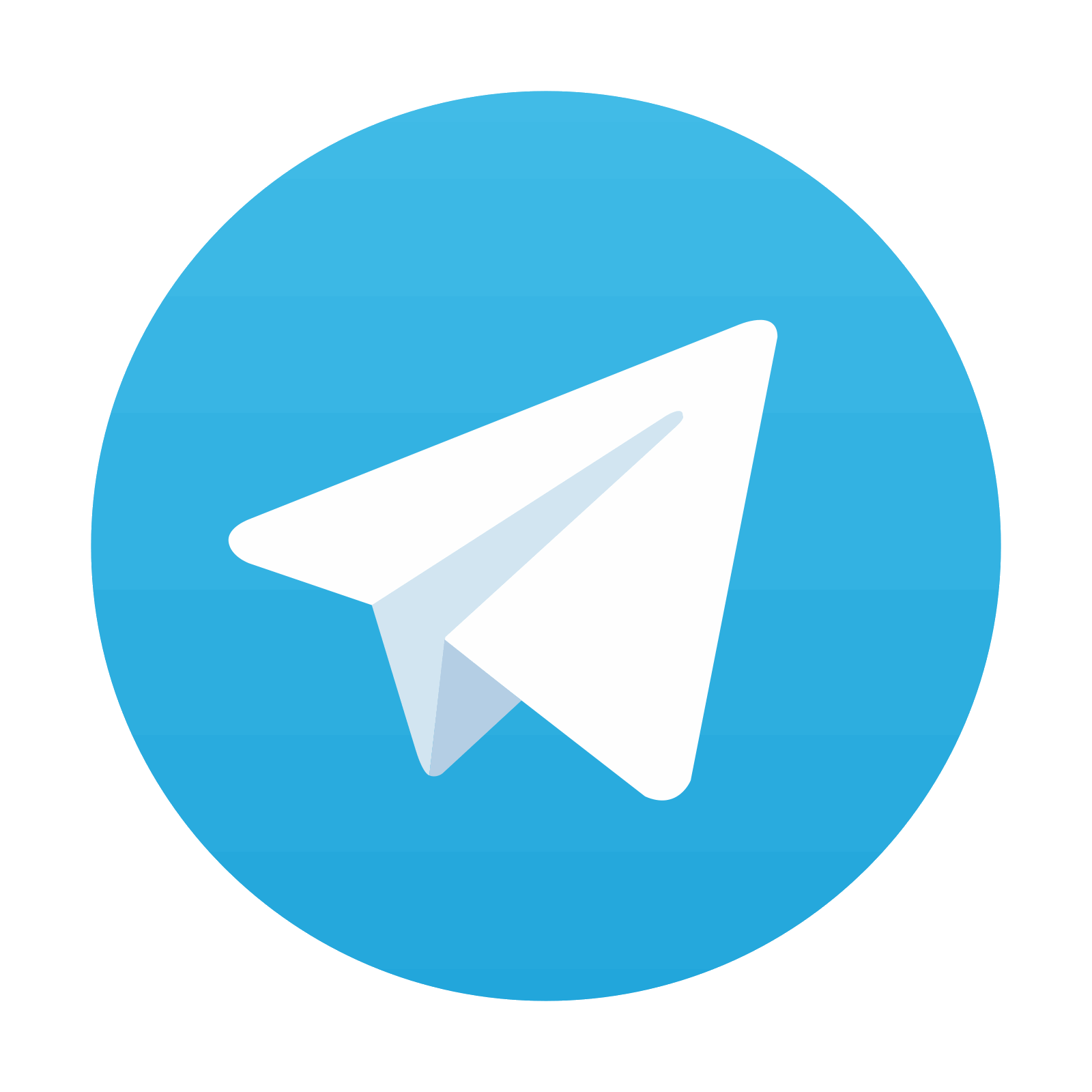
Stay updated, free articles. Join our Telegram channel
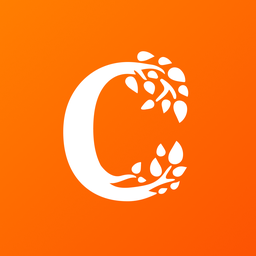
Full access? Get Clinical Tree
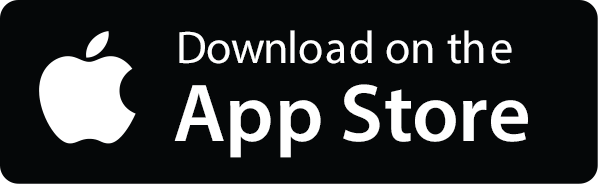
