Jack C. Chu, Leonid Shnayder, and Joe Maida
CONTENTS
Production Facility and Utility Systems Design Must Follow GMP Practice
Integrated Approach to Existing Facilities’ Renovation and Upgrade
Utility Components, Equipment, and Systems Surface Finishes
Utility Systems’ Operational Reliability
Cleanability, Maintainability, and Serviceability
Commissioning and Qualification
Mechanical, Electrical, Piping, and Instrumentation Control Systems
Heating, Ventilation, and Air Conditioning Systems
Contamination Control Criteria
Environmental Control Criteria
Space Supply Air Handling Systems
Process Supply Air Handling Systems
Exhaust and Return Air Systems
Contaminant Characterization and Handling
Vapor and Fume Handling and Treatment
Mechanical System Instrumentation and Control
Purified and Process Water Systems
Hazardous Material Waste and Retention
Plumbing Fixtures and Specialties
Washing Facilities and Gowning Areas
Fire Water Source and Conveyance
Electrical and Power Distribution Systems
Electrical System Design Considerations for Facility Renovation or New Construction
Preventive Maintenance and Cleanability
Process Equipment and Machinery
INTRODUCTION
Under the Food, Drug, and Cosmetic Act, a drug is deemed to be adulterated unless the methods used in its manufacture (processing, packaging, holding, and the facilities and controls utilized) conform to current Good Manufacturing Practices (cGMPs). These require the drug to meet the safety requirements of the act, contain the proper strength and identity, and meet the quality and purity characteristics that it is represented to have. A properly designed and constructed manufacturing facility supports these practices.
The critical quality attributes (CQAs) and critical process parameters (CPPs) must be satisfied by the facility and utility system design and implementation. Professionals from architecture, engineering, and construction management must offer solutions for their portion of the design and installation challenge. Facility and utility design and construction work must be integrated into a complete and operational facility to facilitate the operations of production and maintenance, the company culture, and their quality systems.
This chapter presents pharmaceutical manufacturing utility system design criteria, and installation considerations, as well as critical utility system design concepts applicable to pharmaceutical manufacturing facilities design and construction.
PRODUCTION FACILITY AND UTILITY SYSTEMS DESIGN MUST FOLLOW GMP PRACTICE
Facility utility systems design and installation disciplines have a direct impact on the performance of manufacturing process systems and utility systems. In addition, the facility utility systems will have the greatest impact on the quality and consistency of the drug products, the safety of production personnel, and environmental compliance initiatives. Further, the facility utility systems design and installation can make up as much as 40% of the “brick-and-mortar” capital cost of a pharmaceutical manufacturing facility; the cost of proper maintenance programs could be 10% of the overall production budget.
KEY CONCEPTS
The facility utility systems discussed in this chapter are primarily mechanical systems that include heating, ventilation, and air conditioning (HVAC) systems and associated controls: electrical, plumbing, process piping and instrumentation and control systems, and fire protection systems.
EXECUTIVE SUMMARY
INTEGRATED APPROACH TO EXISTING FACILITIES’ RENOVATION AND UPGRADE
In general, new facilities are built as supplemental to, or phased replacements for, existing production facilities. Most existing facilities have their own unique identities and established operation flows that cannot be disrupted by construction of the new facility. An integral part of programming and designing these projects is the development of phasing strategies that deal not only with construction activities and equipment movement but also with issues of safety and the prevention of product contamination or adulteration during facility construction and operation changeover periods. Design professionals must understand that some existing operational utility systems may not be designed with recognizable logic. Therefore, expediency, rather than flexibility and appropriateness, often dictates the layout of connection to existing utility systems; the possibility of future expansion is seldom a design determinant. A complete survey of these existing systems by a multidisciplinary architectural and engineering team is essential to orderly planning and integration. The project scope of work, and phasing of design and construction, will be based on the results of a thorough survey and the understanding of current and future production process flow, material flow, and personnel flow concepts.
UTILITY COMPONENTS, EQUIPMENT, AND SYSTEMS SURFACE FINISHES
Of all the architectural systems in a pharmaceutical manufacturing facility, the interior finishes are most uniquely identified with this specific building type. Particularly in the process areas, finishes are selected for their durability, resistance to cracking and microbial growth, and cleanability. Exposed engineering system components, and terminal equipment must also be selected to support these criteria to maintain facility integrity. For example, the exposed sheet metal vent ductwork will be made of stainless steel, type 304 or 316L, all electrical and instrumentation wiring will be concealed in the conduits, a metal jacket is required for all insulated piping, and so forth.
UTILITY SYSTEMS’ OPERATIONAL RELIABILITY
Risk-based asset management (RBAM) must be performed for all facility utility systems to identify probable failure modes and operational reliabilities. Asset risk evaluation and assessment focus on the system-based approach. Components’ risk assessment will be done by a preestablished preventive maintenance (PM) program. An engineering solution will be presented to production management based on the system risk identifying evaluation and mitigation processes. The following utility risk management strategies are commonly recommended:
Business continuity: Assets will continue their functionality as originally intended. This requires establishment of a maintenance and operational plan to minimize asset malfunctioning and eliminate critical single-point failures, for example, predictive maintenance (PdM), PM, and corrective maintenance (CM) programs.
Equipment redundancy: An alternative asset will be available to perform the same function as each existing asset. This requires a redundant asset or equipment in place for backup, for example, an online standby fan or pump unit.
Contingency plan: A disaster recovery plan will be provided to manage potential asset or equipment failure. Backup procedures to restore the normal operational condition are required, for example, automatically switching the power supply from a failed centralized supply line to a localized power source.
Minimize impact: Processes to minimize the impact due to the asset or equipment failure will be preestablished. Provide localized utility systems in addition to the centralized utility system, or multiple localized critical utility assets and equipment to support critical processes, for example, a local water-for-injection (WFI) system add-on to the centralized WFI distribution system, or multiple freezers with 35% spare capacity for backup to a failed freezer.
The cost of such strategies for asset redundancy or availability must be thoroughly assessed and justified based on the critical nature of the operations and the risks and consequences of failure. A cost-and-benefit model can be used for such assessments and will include the following primary factors:
Drug product quality and GMP compliance requirements, which could have an impact on patient safety, for example, cross-contamination and microbial problems
Production safety, for example, equipment safety and operator safety
Business impact, for example, environmental compliance and product recall
CLEANABILITY, MAINTAINABILITY, AND SERVICEABILITY
The utility system’s reliability requirements can be achieved by good engineering design practice, achievable construction deliverables, and a reliable maintenance program. Each utility system should be reviewed for maintainability by subject matter experts (SMEs), the group that will be responsible for operating and maintaining the system. Furthermore, utility system components should be located in a position where routine PM or CM can easily be performed with minimal impact to normal operations. Scheduled system shutdowns for service, in-line testing, and sampling methods should be carefully designed to minimize interruptions to production operations.
COMMISSIONING AND QUALIFICATION
Commissioning is required for all utility systems and equipment prior to putting in service, for example, HVAC, chiller system, domestic water system, and electrical distribution system. In general, validation (qualification) may not be required for the utility system unless it is classified as a critical utility system or equipment that has a direct impact on drug product quality and safety, for example, HVAC, WFI system, clean-in-place and steam-in-place (CIP/SIP) system, and compressed gas system. Reverification at a preestablished frequency will be required if the material produced by the utility system will be part of the drug, for example, WFI water and clean steam.
Commissioning, as defined in the American Society of Heating, Refrigerating and Air-Conditioning Engineer (ASHRAE) guideline, is
the process of ensuring that systems are designed, installed, functionally tested, and capable of being operated and maintained to perform in conformity with the design intent … commissioning begins with planning and includes design, construction, start-up, acceptance and training, and can be applied throughout the life of the building.
The qualification process is a documented program that provides a high degree of assurance that a specific process, method, or system will consistently produce a result that meets predetermined acceptance criteria. See Chapter 7 for more discussion of commissioning and qualification.
MECHANICAL, ELECTRICAL, PIPING, AND INSTRUMENTATION CONTROL SYSTEMS
OVERVIEW
The primary objective for the design of production facility utility systems is to ensure that products manufactured using these systems are fit for use. Specifications and the CQAs of production should be understood in order to determine CPPs.
In general, facility-related mechanical systems include the following functional outputs:
Heat transfer (both process and facility), for example, glycol chillers and heat exchangers
Space temperature, humidity, and pressurization controls, for example, HVAC and building automation system (BAS)
Space cleanliness and air filtration for space particle control: International Organization for Standardization (ISO) classification and high-efficiency particulate air (HEPA) filtration
Provision of water and gases for product and process requirements: Domestic water and water softener
Wastewater drainage and disposal of wastes
Utility systems are designed to accommodate facility and processes requirements that are determined primarily by the products manufactured, the processes utilized, established machinery and user criteria, and operational and maintenance factors and economic and scheduling requirements. Some specific requirements depend on whether the utility system or equipment comes in contact with product. The following sections discuss the various mechanical services, including HVAC systems, process and piping systems, and fire protection systems, and how these relate to the process requirements outlined elsewhere in this text.
HEATING, VENTILATION, AND AIR CONDITIONING SYSTEMS
The HVAC disciplines play a critical role in the manufacture of pharmaceutical products. The Food and Drug Administration (FDA), through current Good Manufacturing Practices and guidelines, has set strict facility requirements for the manufacturing environment that the HVAC systems support.
System Design Criteria
For people’s comfort, ASHRAE standard 55, “Thermal Environmental Conditions for Human Occupancy”; ASHRAE standard 62.1, “Ventilation for Acceptable Indoor Air Quality” (Reference 3, Appendix 5); and ISO standard 7730 should be followed. If operators are wearing protective suits such as Tyvek suits, full-face respirators, or full-body suits with breathing air equipment, then lower space temperatures than those defined by ASHRAE may be required to provide operator comfort. For process and product controls, product may dictate the operating or process environment conditions. Many products can be hygroscopic or temperature sensitive during the manufacturing process. All of these conditions should be defined prior to selecting and sizing the HVAC system.
While regulations change over time and vary across countries, the major principles of regulation and guidance impacting HVAC design, installation, qualification, and maintenance in pharmaceutical manufacturing facilities are generally consistent. A few key principles are listed below:
Process contamination control and cross-contamination control: Control of pharmaceutical dust (from processing), air filtration, once-through air or recirculation air, space pressurization, and control of contaminants from personnel, and so forth
Production facility environmental control of critical parameters: Temperature, humidity control, pressurization, and filtration
HVAC system risk assessment: By processing zone, product or process specific, qualitative or quantitative
Contamination Control Criteria
The production environment where the drug is processed must be appropriately designed, constructed, and maintained. At every stage of processing, products and materials must be protected from microbial and other contamination. In oral products, the most serious potential contamination may be the contamination of one drug by another. Regulations predominantly suggest that the dissemination of pharmaceutical dust, including active product, must be controlled. This requirement for control of pharmaceutical dust includes minimizing the escape of dust from the process and the control of fugitive dust within the room.
Many common practices have been recognized by pharmaceutical professionals: In cases where dust is generated (e.g., during sampling, weighing, mixing, and processing operations, and packaging of dry products), specific provisions should be taken to avoid cross-contamination. When working with dry materials and products, special precautions should be taken to prevent the generation and dissemination of dust. This applies particularly to the handling of highly active or sensitizing material. Contamination of a starting material or a product by another material or product must be avoided. The risk of accidental cross-contamination arises from the uncontrolled release of dust, gases, vapors, sprays, and so forth, from active substances. Dust control systems for the removal of dust should be close to source of the contaminant.
Control of pharmaceutical dust in the ambient environment is the reason that regulations typically require “minimizing the risk of contamination caused by recirculation or re-entry of untreated or insufficiently treated air” (EudraLex Vol. 4 5.19 and Agência Nacional de Vigilância Sanitária [ANVISA]). This regulatory requirement is often used as the justification for using 100% exhausted systems without recirculation. However, regulatory agencies do recommend conducting an evaluation of cross-contamination potential in lieu of a ban on recirculation of air in multiproduct facilities. “A Quality Risk Management process, which includes a potency and toxicological evaluation, should be used to assess and control the cross-contamination risks presented by the products manufactured” (EMA EU Gudielines for Good Manufacturing Practice for Medicinal products for Human and Veterinary Use. Part 1. Chapter 5: Production).
In production areas, a risk evaluation plan should be established for the production facility and utility systems, production equipment, and manufacturing process systems. The production facility risk assessment should include weighing and dispensing, solution preparation, mixing and granulation, drying, tableting and encapsulation, tablet coating, and other processes. Risk analysis will determine whether a once-through air system or a filtered return air system is appropriate for a specific application. A risk-based approach to determining critical parameters is suggested by most regulations. The list of parameters that may be judged as critical can be broad. For instance, the following citation from WHO TRS 937, Annex 2 suggests a long list of parameters that may need to be qualified in an oral solid dosage (OSD) facility’s HVAC design:
#8.2.17 for a pharmaceutical facility, based on a risk assessment, some of the typical HVAC system parameters and functions that may be qualified can include:
temperature
relative humidity
supply air quantities for all diffusers
return air or exhaust air quantities
room air change rates
room pressures (pressure differentials)
room airflow patterns
unidirectional flow velocities
containment system velocities
HEPA filter penetration parameters
particle counts in the room air
room clean-up rates
microbiological air and surface counts where appropriate
operation of de-dusting
warning/alarm systems where applicable
Environmental Control Criteria
Although cGMP regulations establish the requirements for classified environments for bio and sterile manufacturing environments, most regulations do not require a classified environment for oral dosage manufacturing. However, this does not mean that OSD manufacturing environments are uncontrolled; rather, it suggests that oral drug manufacturing should be managed and well understood, though the cleanliness requirements are less than those for sterile products. The traditional approach to meeting control expectations was to “design to class 100,000 (ISO 8) but not certified” or “controlled but not classified space.” This approach has been successful, but it does not offer a means of verifying that the intended goal has been reached. There is a growing regulatory expectation that facilities will be tested and qualified to an objective standard. For oral dosage facilities, the consensus appears to be that class 100,000 (ISO 8) in the “at-rest” state—equivalent to EU grade D—is a suitable background environment. As an example, the following is a citation from WHO TRS 937, Annex 2:
HVAC systems and components
Note: The required degree of air cleanliness in most OSD manufacturing facilities can normally be achieved without the use of high-efficiency particulate air (HEPA) filters, provided the air is not recirculated. Many open product zones of OSD form facilities are capable of meeting ISO 14644-1 Class 8, “at-rest” condition, measured against particle sizes of 0.5 μm and 5 μm, but cleanliness may not be classified as such by manufacturers.
A rough comparison of the ISO and Federal Standard 209E is shown in Table 5.1.
Table 5.1 does not reflect the complexity of the ISO clean room standards. These should be considered thoroughly before embarking on a clean room design.
Specific facility and process criteria are defined in the following sections.
Temperature and Relative Humidity
Production facility temperature and relative humidity controls are critical to both process and production personnel. United States Pharmacopoeia (USP) excursion limits for finished product storage are 59°F–86°F (15°C–30°C) with a controlled room temperature (CRT) working environment of 68°F–77°F (20°C–25°C) with a maximum mean kinetic temperature (MKT) of 77°F (25°C). However, individual products may require a more stringently controlled environment.
TABLE 5.1
ISO and U.S. Federal Standard 209E
Product temperature monitoring may be performed as an alternative to room temperature monitoring. Room temperature can be monitored by return or exhaust duct-mounted sensors or wall-mounted sensors that relay information to the BAS or separate sensors connected to an independent environmental monitoring system (EMS). Typically, a relatively tight control range is specified (i.e., 68°F–72°F), with an excursion alert occurring when a wider range is exceeded (i.e., 65°F–75°F), and a further excursion alarm occurring when a maximum range is exceeded (62°F–78°F). All values must be well inside the USP excursion limits.
Allowable space and system control tolerances must also be identified, as well as the impact of these tolerance requirements on the systems design. Proper outdoor ambient design conditions must be determined in order to select the air conditioning equipment. If outdoor conditions are chosen too conservatively, the equipment will be oversized, costing more than required and requiring more energy for operation. Conversely, if the selection does take variation of ambient conditions into consideration, the facility or process conditions may not be met under certain circumstances. An assessment must be made of the possible risks of not meeting space or process condition requirements and the effects on productivity.
Air Cleanliness
The level of acceptable airborne contamination within the space must be identified, whether required for product quality or employee safety. Environmental cleanliness is determined by several factors, including the quality and quantity of air introduced into the space, the effectiveness of air distribution through the space, and the effectiveness of the removal of the air contaminants. Removal of the contaminant as close to its source as possible is always the most effective method of contamination control—whether it is central filtration at an air handling unit before supply to the facility or dust collection at a point source of contamination within a space.
Clean room design takes contamination control to its highest level. Federal Standard 209 historically was the document governing clean room design. This standard has been replaced by the ISO 14644 and 14698 global clean room standards. Cleanliness is categorized by cleanliness classes, which are qualified by the quantity of 0.5 micron or larger particles per cubic foot of air within a specific area. Standard categories of cleanliness used in the pharmaceutical industry are ISO 5, 7, and 8 (Classes 100, 10,000, and 100,000 per U.S. Federal Standard 209E, which was replaced by the ISO standard). See Table 5.1.
Pressurization and Air Change Rates
Where airborne contamination, cross-contamination, or potent or hazardous material containment is a concern, one tool for control of airborne particulates is control of the differential pressure or direction of airflow between spaces with the following common practices:
Bio and sterile operations: 15.0 Pa (0.06 in. of water column (WC))
OSD operation: Between 5.0 Pa (0.02 in. WC) and 12.5 Pa (0.05 in. WC)
The velocity and direction of airflow between spaces should be satisfactory to reduce the transfer of airborne particulates or vapor. While there is not a numerical value for pressurization required in regulation, many current guidance documents suggest a mass airflow velocity of 100–200 fpm to control light dusts moving across a work area. Generally, smoke tests and Baulin Tubes may be used as evidence of the establishment of directional airflow between work areas. The air changes per hour method has been practically applied for engineering design and HVAC equipment specification. Common practice demonstrates the effectiveness of the proper air changes per hour (ACH) for various production facilities. See Table 5.1 for reference.
In many cases, the cleanliness of the production facility can be achieved by employing space temperature and relative humidity controls, airflow pattern and space pressurization controls, and air filtration and air system configuration controls, and controlling the air changes per hour within the space.
Other Considerations
The relative pressurization of the space will be determined primarily by the requirements of the product, but also by characteristics of the product that may adversely affect personnel. Space containment and isolation techniques can protect the product, the operator, or both. Where product contamination control is required, the space relative pressurization must be designed to ensure that the movement of exfiltrated air is from the clean to the less clean areas. In some cases dealing with hazardous products (e.g., high-potency compounds), this relative pressurization and the resultant air movement are reversed to contain the hazard and protect personnel. In these cases, product contamination can be controlled by the use of special laminar flow hoods or personal isolation suits, or positive and negative pressurization utilizing airlocks. Some operations may require flexibility for either positive or negative pressurization, depending on the application. A pressure differential of at least 0.05 in. water gauge with all doors closed is preferable between spaces with a pressure differential requirement. See Chapter 14 for more discussion on this topic.
Careful attention must be paid to the incoming air quality. This can be specific to the area in which the facility has been constructed, such as an agrarian or industrial area. An industrial area may have more corrosive or chemical-laden air, while an agrarian area may have a higher level of seasonal airborne particulate and bioburden. These issues must be carefully considered when selecting filtration systems so as to minimize the possibility of product contamination.
Most often, however, building intake reentrainment of its own effluent is the greater problem. Careful consideration must be made as to the impacts of building exhaust and relief systems, loading docks, and other incidences of vehicle exhaust and electrical generator exhaust. Analysis must be made of the building’s impact on itself and other surrounding buildings, and their impact on the subject building. Potential future building activities should also be considered. Rooftop activity safety should also be analyzed, and a safe rooftop environment should be provided for routine maintenance activities.
Noise Considerations
Given the overriding concerns for durability and cleanability in process spaces, little can be done to dampen the acoustic qualities of finished surfaces. By definition, a cleanable space has smooth, hard finishes with simple geometries that reflect rather than absorb sound. This makes the control of noise contributed by utility systems critical in these spaces. Sound attenuation can be added to supply and exhaust air systems. Dust collection inlets tend to be the greatest contributor to space noise. Attention to design parameters can minimize the sound radiated from these inlets.
Manufacturing facilities also tend to utilize large process and utility equipment that can radiate noise to the outdoor environment. Local ordinances and the neighboring community may require that noise generated by this equipment be minimized. Methods of enclosure and the specification of sound attenuation devices can significantly reduce noise transmitted outside of the facility.
Cost Considerations
Pharmaceutical manufacturing facilities and processes are extremely costly to design, construct, and operate. When designing a facility and process, careful consideration must be given to the initial construction cost, balanced against life cycle operating costs. Careful analysis must be made of all of the components of the facility or process design. A cost-cutting measure taken during the initial capital expenditure may sometimes result in huge operating costs from years of inefficient operation. Conversely, a complex, capitally cost-intensive project can take too long to build and commission, which may affect the speed to market the product, and ultimately production and sales.
HEATING SYSTEMS
Heating of facility and process systems is generally accomplished utilizing steam or hot water as the heat source. There may also be intermediate methods of heat transfer utilizing a secondary steam or heating hot water system. Heating can also be provided by electric means, which is easily controlled but is expensive to operate and therefore not widespread. Heating systems for process equipment steam-in-place (SIP) for equipment sanitation are not covered in this chapter.
Heating of primary air at the central air handling unit is generally accomplished using hot water or low-pressure steam. Incoming ventilation air on high outside air volume systems in colder climates is generally heated utilizing low-pressure steam or a separate hot water system with a concentration of propylene glycol sufficient to prevent water system freezing (Figure 5.1).
It is preferred that heat required in a jacketed heat exchange process such as a kettle that has one level of product containment (the kettle wall) be provided by a non-plant source. This may be accomplished by using a secondary heat source such as an independent water or steam system utilizing plant steam as the primary heat source. This prevents plant system contamination in case of a boundary wall failure.
COOLING SYSTEMS
Cooling of facility and process systems is generally accomplished utilizing chilled water, condenser water, or direct refrigerant expansion (DX) as the heat sink. In isolated cases, a water and antifreeze solution or other heat exchange fluid may be utilized, generally without a phase change. There may also be an intermediate method of heat transfer utilizing a secondary chilled water system in concert with the plant systems outlined above. Primary chilled and condenser water is usually generated by a central cooling system. It is then distributed throughout the facility to points of use that include cooling coils, heat exchangers, and jacketed heat exchange processes. Piping for these plant water systems is generally welded or screwed black steel. Mechanical coupling systems are also utilized.
Plant chilled water is generally produced utilizing water-cooled or air-cooled chillers. Chilled water supply temperatures are usually in the range of 40°F–45°F and are determined by the requirements of the cooled medium, generally air.
Condenser water cools the condenser side of the chiller and is of a higher temperature. Condenser water supply temperatures are usually in the range of 85°F–95°F in the summer. Nonsummer condenser water supply temperatures can generally be maintained at lower temperatures. Water is typically cooled by open cooling towers or closed-circuit coolers. Open towers utilize outside air to cool the water directly. Closed-circuit coolers circulate the water through tubing in the tower that is air cooled and sprinkled with water. Condenser water can also be used to cool processes besides chiller condensers. These include cooling of purified water processes, refrigerated processes, and jacketed processes. If the process does not require the lower temperatures of chilled water, condenser water can be a cost-effective solution, as it does not require the additional energy of the mechanical refrigeration process.
FIGURE 5.1 Typical heating system.
Cooling of space or process supply air is generally accomplished at the central air handling unit. Incoming ventilation air on high outside air volume systems may require additional dehumidification that the chilled water system cannot achieve (see the “Dehumidification Systems” section below). Terminal cooling is often required when an area with lower environmental temperature or humidity levels is served by a central system designed for maintaining higher temperatures and relative humidity (Figure 5.2).
HUMIDIFICATION SYSTEMS
In most cases, air supplied to the space or process will require moisture to be added to maintain relative humidity conditions. Moisture is generally provided utilizing steam injection and, in some cases, water atomized by utilizing compressed air. In the cGMP environment, the moisture added must not be a source of contamination. Its source is therefore generally purified water that is then atomized or converted to clean steam. These humidifiers are typically constructed of stainless steel.
FIGURE 5.2 Typical cooling system.
DEHUMIDIFICATION SYSTEMS
In cases of high latent loads from processes or high quantities of outside ventilation air, the building cooling system must be designed for the higher dehumidification requirements. Several moisture removal methods are available. These include low-temperature latent cooling used in concert with reheating, solid and liquid desiccant drying systems, and the injection of sterile, dry compressed air into the airstream. In all cases, room or process air can be treated centrally or locally. All methods must consider minimization of product contamination.
SUPPLY AIR HANDLING SYSTEMS
An air system has the greatest influence over the environment within the space or process that it serves. It assists in determining the temperature, moisture level, and cleanliness of that environment. It also assists in the relative pressurization of the space or process.
SPACE SUPPLY AIR HANDLING SYSTEMS
Supply air systems are divided into four specific components: prime movers, distribution, terminal control equipment, and terminal distribution equipment.
Prime movers on the supply air system are generally enclosed in an air handling unit comprising several components. The device that drives the air is a fan. The largest consideration for supply air fans in this industry is generally capacity control and turndown capability to accurately match the requirements of the supply air system. Coils are used to transfer heat into or out of the airstream. As described in the heating and cooling discussions above, many different heat transfer fluids may be used for heating and cooling.
Humidification devices are often placed inside of the air handling unit, but can also be installed within the ductwork outside of the unit, saving unit casing cost. Primary concerns in their specification are the moisture source and vapor trail, which are both potential contributors of biological and chemical contamination.
Air systems tend to be noisy. Contributors are primarily fans, dampers, and terminal air control boxes. Sound attenuation devices are often placed in or near the air handling unit to decrease the radiated noise of the fan. Attention must be paid to the type of attenuator, which could be a source of particulates and microbial contamination.
Filters are generally the first and last devices in the pharmaceutical manufacturing air handling unit. Intake prefilters protect the unit components from dirt and contamination. Final filters at the unit discharge protect the system and ultimately the space and process. Terminal filters are also often specified. See discussion below on terminal distribution equipment (Figure 5.3).
Distribution is generally sheet metal ductwork, although it can be piping or other materials. The greatest consideration is often the material. Galvanized sheet steel is most often used, but it is difficult to sanitize. If the ductwork material is open to product or product space or must be frequently decontaminated, it is often specified as stainless steel. Another important consideration is accessibility, both inside and outside for cleaning and testing. Other considerations for the ductwork design are the size of the ductwork and leakage rate.
Terminal control equipment includes air volume control boxes, terminal heating and cooling coils, terminal humidification, and sound attenuation. Air volume control boxes control the air quantity delivered to the space, and in concert with other supply, return and exhaust boxes within the space and adjacent spaces control space relative pressurization. Terminal cooling coils provide for space subcooling and dehumidification. Terminal heating coils are provided for reheat of space air to support dehumidification and room temperature control. Accessibility for maintenance is the primary concern for these devices. Terminal humidifiers may be used if needed to provide additional moisture to the processing spaces. As with central humidifiers, the primary concern is potential contamination from the moisture source or carryover. Terminal sound attenuation masks the noise from terminal boxes, and as with central attenuators, proper selection of the attenuator type is important to limit potential contamination from particulates and microbial growth.
Terminal distribution equipment includes diffusers, registers, grilles, and terminal filtration. Diffusers, registers, and grilles introduce air into a space. Proper application of the different types of devices is critical to maintain effective distribution. The airflow direction into the space is important. Unidirectional diffusers are often specified instead of aspirating type to provide, in concert with the exhaust terminal device, a “sweeping” effect in the room to more effectively remove particulate from the space. Another important consideration is device cleanability within the space. The device must not be a source of contamination. Terminal filtration is applied most often where space cleanliness is paramount. While this application of filtration can protect the space and product from contaminants within the air system, it can also protect the air system from product or contaminants within the space in case of system failure. Important considerations for the selection and placement of terminal filtration are its location, change-out requirements, and accessibility for testing.
Other important design considerations are as follows: The supply air system, more than any other system, controls the space temperature and relative humidity. Utilizing cooling and heating coils and methods of humidification and dehumidification, all within the supply airstream, each space is controlled to maintain the required conditions.
FIGURE 5.3 Typical air handling unit configuration.
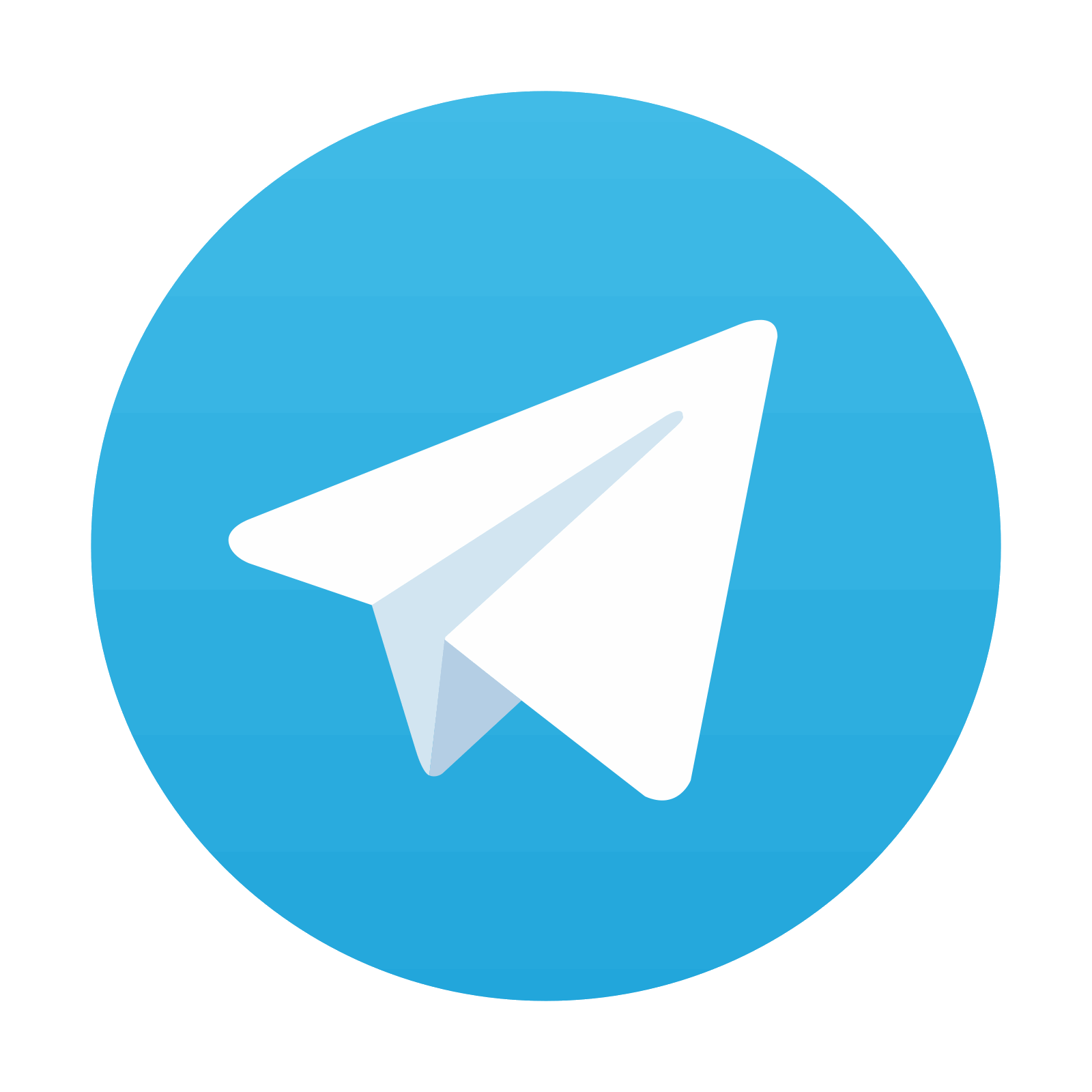
Stay updated, free articles. Join our Telegram channel
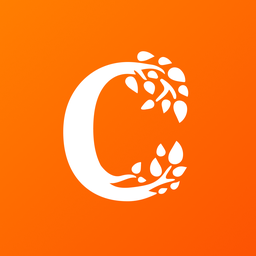
Full access? Get Clinical Tree
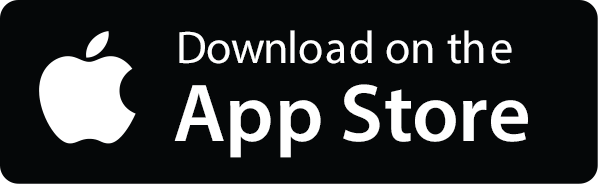
