At the highest level of the documentation hierarchy in most companies sits the quality manual, which defines the corporate objectives related to quality and compliance. It establishes a figurative road map including guiding principles (regulatory and internal) that employees and other users may refer to in meeting organizational objectives related to the quality system.
Just below the quality manual sit corporate policies that describe, in general terms, how the company intends to conduct their business in compliance with the requirements defined in the quality manual. A more detailed discussion of how the company will comply with individual aspects of the requirements in the quality manual is found in documents such as standard operating procedures (SOPs) and validation master plans (VMPs). SOPs describe, in detail, how firms will conduct operations related to each requirement in the GMP regulations, such as receipt of materials, operation of equipment, and handling of investigations. VMPs provide a detailed description of how a firm will qualify their facility or equipment and the governance program that will ensure that it remains in a qualified state. Additional detail, including step-by-step instructions on how to perform a specific task or activity within a GMP environment, can be found in documents such as master batch records, test methods, protocols, and work instructions. Master manufacturing and packaging batch records (sometimes referred to as manufacturing formulae, processing, and packaging instructions) detail each step of the processing and packaging of the drug product and are used by operations personnel to produce the finished drug product. Test methods provide the detailed steps for testing incoming materials and in-process or finished product. Protocols are often generated for special studies, such as validation studies or stability studies. Work instructions may provide even greater detail and are often used when step-by-step instruction is critical to ensure that processes are performed consistently and reliably. Records, internal communications, and notes represent the data that demonstrate that a company has operated in compliance with their own documentation and the regulations that govern their business.
Documents and Records
It is important to distinguish between the concepts of documents and records. Documents, in a GMP environment, refer to the how-to instructions that outline what needs to be done to produce the product or operate in compliance with the regulations. Records, in a GMP environment, refer to the body of information (history) or data related to the manufacturing, packaging, testing, and holding of each batch of finished product. Once a document has data written on it, it becomes a record.
In 1997, the United States Food and Drug Administration (FDA) issued the Part 11 regulations to ensure the authenticity and integrity of documentation and records that are maintained in an electronic format. After much discussion with industry and contractors, FDA moderated their position related to Part 11 and narrowed the scope of the requirements. What did not change, however, was FDA’s commitment to enforcement of all predicate rule requirements, including those that cover GMP records and record-keeping requirements. If a company chooses to use GMP documents or records in an electronic format in place of a paper format, the requirements of Part 11 apply.
Good Documentation Practices
Master Documents
GMP regulations require that master documents (for example, SOPs, master batch records, protocols, and specifications) be:
• Designed, prepared, and reviewed in accordance with the requirements in the regulations
• Clearly written and unambiguous
• Approved (signed and dated) by appropriate (that is, qualified by education and/or experienced) and authorized individuals
• Identified with a number or code that is unique to the document
• Regularly reviewed and maintained up to date
Executed Documents
GMP regulations specify several practices to be followed in the execution of GMP documents:
• Recording of information and data should be clear, legible, and indelible (typically recorded in ink; pencil and erasable forms of ink are not allowed).
• Information and data should be recorded at the time the activity or step is completed and in a manner that ensures that all of the significant activities associated with the manufacturing and packaging of the drug product are traceable.
• Any alteration or correction to information or data that were previously recorded should be crossed out with a single line, the new information recorded, and signed and dated by the individual making the correction (Figure 15.2).
• Electronic capture of data and information is allowed once the electronic system has been qualified and secured. An audit trail, that is, a record of all data recording, changes, and deletions, must also be in place and secure.
• The executed documents are managed in a manner that allows for ease of retrieval and ensures that the documents are retained in compliance with regulatory requirements.
GMP Records
Globally, GMP regulations mandate the recording of data and information about pharmaceutical products and the materials, equipment, processes, and people involved in their manufacture. It is through this recording of data that GMP records evolve. While some believe that this data recording is an onerous task, there is tremendous value in the data, and they can often be used to benefit the organization.
Training Records
GMP regulations require that personnel have the education, training, and experience needed to perform their assigned responsibilities. Training on both specific job tasks and GMP regulations is required. Training related to job tasks is necessary when a task is new to the employee, when procedures, batch records, and/or test methods are revised, or when a task has not been performed recently. Similarly, when an employee’s job changes within an organization, his or her education, experience, and training should be reevaluated to determine what areas need to be addressed to perform the new job. Education and experience are typically documented in a resume or employee work history. Ongoing training is typically documented in separate training records for each training event. These training records can be used to:
• Demonstrate compliance with the personnel requirements in the GMP regulations
• Identify knowledge gaps within a functional area and support the justification for additional training
• Assess the needs for additional training after an investigation or product issue
• Assess the effectiveness of various training programs and methodologies
Facility Records
A considerable number of records need to be generated and maintained regarding the qualification and ongoing maintenance of the facilities used to manufacture pharmaceutical products. Some of the records (for example, qualification of utilities or equipment) are generated when the facilities or equipment are first commissioned for use. They may be amended or updated when changes to the facilities or equipment take place, but are relatively static in nature. They provide a snapshot in time of the particular utility or piece of equipment in question. Other records (for example, unscheduled maintenance, preventive maintenance, or calibration documentation) are updated regularly and provide a historical record of what has happened to a piece of equipment over time. These equipment records can be used to demonstrate compliance with the regulations covering the qualification, maintenance, and calibration of facilities and equipment, troubleshoot equipment failures and determine the impact of the failure on previously produced product, and investigate out-of-specification (OOS) test results to determine whether the equipment might have played a role in the product failure.
Material Receipts
GMP regulations require that materials are purchased from approved suppliers and that they are received, sampled, tested, and stored in such a manner as to prevent deterioration or contamination. When a material is first received into the pharmaceutical company’s warehouse, a record of its receipt is generated. This initial step can verify that the material received matches the material requested (for example, on a company purchase order) and that it is from the approved supplier. The quantity of the material is typically recorded along with the number of containers and any supplier-specific batch or control number. The material typically moves on to a quarantine area (either physical or virtual) and waits to be sampled. Sampling is usually performed by the quality unit (QU), and the material is placed back into a quarantine status until testing is complete and the material has been released. After testing by the QU, the material may move to a different area of the warehouse or, in the case of an electronic quarantine system, have its status changed to “released,” which allows it to be used in manufacturing. All of these steps are typically recorded on the material receipt record. This material receipt record can be used to:
• Demonstrate compliance with the GMP requirements for material receipt (that is, demonstrate to the regulators that the material was received appropriately, its identity was appropriately verified, and it was stored appropriately until use)
• Evaluate vendor performance (for example, determine whether the vendor met the required delivery date and supplied the requested quantity of material)
• Facilitate traceability to a specific batch of material in the event of a recall by the vendor
• Improve internal operations by evaluating metrics related to material processing time, number of material movements, testing time, and inventory turns.
Batch Records
Pharmaceutical companies are required to develop batch processing records (master batch records [MBR]) that outline the steps required to manufacture and package pharmaceutical products. Clearly written, detailed batch records are critical to ensuring product quality. The executed batch records provide a record of how the product was manufactured or packaged (for example, the materials and equipment used, the personnel involved). These records can be used to:
• Demonstrate compliance with the requirements for written batch-processing records
• Demonstrate compliance with the processes outlined in approved marketing authorizations
• Facilitate investigations into product problems
• Demonstrate employee proficiency through the lack of process problems or deviations
• Demonstrate that the product remains in a state of control (validated state)
• Identify areas for improvement
Log Books
Log books are typically used throughout a GMP facility to document the work that has been done in a particular area or to record the activities performed on individual pieces of equipment. Log books are generally assigned to an area or piece of equipment and provide a chronological history of the products that were produced in the area/equipment and any other work that has been conducted (for example, maintenance, calibration). Log books can be used to demonstrate compliance with the requirements for capturing equipment or area usage, facilitate investigations into product problems, demonstrate that appropriate cleaning procedures have been followed, and identify opportunities for improvements to equipment based on historical calibration or maintenance activities.
Complaint Records
GMP regulations, specifically in 21 CFR 211.198, require companies to maintain written records of each drug product complaint and the investigation conducted to determine the root cause of the complaint. These records demonstrate a company’s commitment to its customers and compliance with the requirements for complaint handling, and identify product or process issues that require correction or improvement.
Records Management
The ISO 15489-1: 2001 standard defines records management as “the field of management responsible for the efficient and systematic control of the creation, receipt, maintenance, use and disposition of records, including the processes for capturing and maintaining evidence for and information about business activities and transactions in the form of records.” Records management is critical, not only from a GMP perspective, but from a company business perspective, as well. Company records provide the evidence that an organization has operated in a compliant and lawful manner. In addition, they provide the historical context in which business decisions were made and allow personnel to better understand the reasoning behind those decisions. Without good records management, a company runs the risk of repeating past mistakes.
Record Retention
A key component of any records management program is a documented record retention process. Records, and the information contained within those records, have a useful life during which they are an asset to the company. Beyond that useful life, records become an unnecessary expense and can be a corporate liability. It is important to define the retention requirements (or useful life) of each type of record and have a process in place for disposing of records once they have moved beyond their established retention period.
Throughout the GMP regulations, a number of record types have specified retention periods. These retention periods become the minimum requirements for record retention. A company may maintain these records for a period of time beyond the minimum requirements outlined in the regulations, but should do so only if business needs or litigation requirements dictate. Specific retention periods are identified in the GMP regulations (Figure 15.3).
Litigation Concerns
Properly maintained records can provide significant value to an organization. Unorganized, inaccessible records, or records that are retained after their useful life has passed, can become a corporate liability. While not a GMP concern per se, it is important for companies to have processes in place to notify employees regarding new and ongoing litigation matters. Many of these matters will require employees to maintain or produce, for the attorneys, the applicable documents that are the subject of the litigation. If a document is covered by a litigation matter, it can not be destroyed even if it has reached the end of its established retention period.
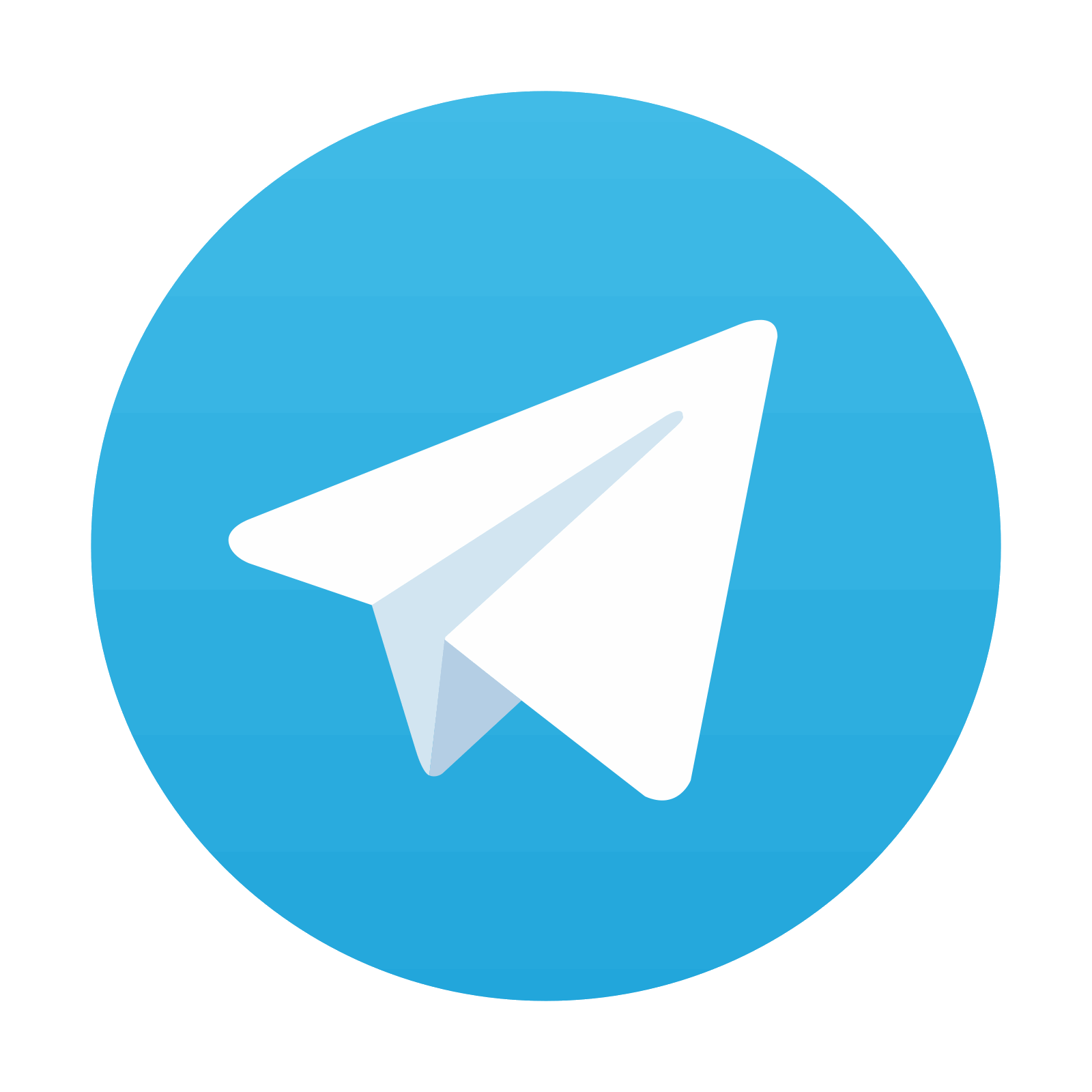
Stay updated, free articles. Join our Telegram channel
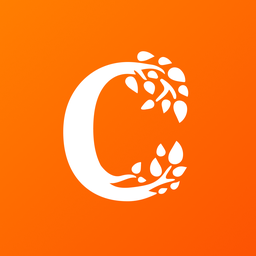
Full access? Get Clinical Tree
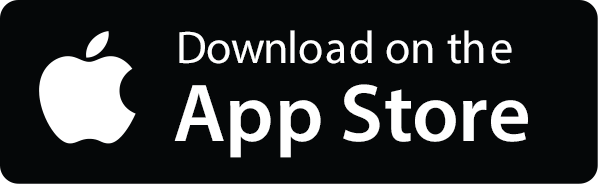
