!DOCTYPE html PUBLIC “-//W3C//DTD XHTML 1.1//EN” “http://www.w3.org/TR/xhtml11/DTD/xhtml11.dtd”>
Chapter 45: Dispensing and Weighing Controls
Dispensing and weighing controls should be such that the identity, purity, and quality of the raw materials are maintained throughout the process. In addition, the controls should be such that there is complete traceability of the materials. The requirements for weighing controls are covered in 21 CFR 211.101.
Weighing Equipment
Clearly written procedures for use and maintenance of weighing equipment should be available for training the operators. The procedures dictate the scales to be used for each range of weights. Weighing and measuring devices should be of suitable accuracy for the intended use, and they are be calibrated to ensure accurate results within appropriate ranges. Weighing scale calibration is performed every three to six months as per the procedures. In addition, a daily weight check in the range the scale is used within is performed with a National Institute of Standards and Technology (NIST)–calibrated weight set, and the information is logged in. The weight set should be calibrated annually. These procedures ensure that the scales are accurate when they are used for weighing of materials for commercial batches of pharmaceutical products.
Dispensing Utensils
Utensils used for dispensing materials should be nonreactive to the material. If the utensils are reusable, they should be clean, sanitized, and dry before each use. The cleaning process needs to be validated to ensure that no cross-contamination occurs. Clean utensils should be stored properly in clean, labeled areas/bins and separated in the weigh room from used utensils that need cleaning.
If weighed material needs to be transferred to a secondary container, the secondary container should be clean, sanitized, dry, and nonreactive. The secondary container must be labeled immediately with the component name or item code, control or lot number of component, weight or measure transferred to the container, and batch number of product for which this component was weighed.
Staging Areas
A clearly marked staging area for materials that need to be weighed is necessary. This area should be large and free-flowing enough to maintain adequate separation between materials and for operators to easily take one item at a time to the weigh room. Components for each batch of product need to be segregated from each other. Material being returned to inventory after removal of required component should be staged in a separate area. These areas should be clean and with a good flow to prevent mixing of chemicals. The material names, item code, and lot number should be clearly visible at all times in order for operators to easily pick the items they need.
Weigh Room
The weigh room should be separated from the rest of the production area to allow for easy material handling and dispensing without the material flying and settling on or otherwise contaminating other processes in the production area. Proper environmental controls (ISO 14644) need to be maintained as per the requirements of the raw materials that are to be weighed and the stringency of the product being manufactured. Even in the least stringent pharmaceutical product manufacture, at a minimum, the area should be ISO 14644 class 8. Only one chemical is taken into and handled in the weigh room at a time. Materials needed for each batch of product are weighed, reconciled, and removed from the weigh room before starting on a second batch. Material weighed for each product batch is separated from other batches. The pallets used to store the weighed material are labeled with the batch number, product name, pallet number, and total number of pallets. The pallets are staged in a labeled designated area for further batching.
Weighing Process
Weighing, measuring, or subdividing operations for components must be adequately supervised. Each container of component dispensed must be examined by a second person to assure that the component was released by the quality control (QC) group, the weight or measure is correct as per the production batch record, and the containers are properly identified as per 21 CFR 211.101.
Electronic processes can be used to increase controls over the weighing pro-cess, but these processes need to be validated. The most common electronic process is attaching a printer to the weigh scales to print the tare, gross, and net weights dispensed. The printers can be programmed with readers that can read bar codes of the items being weighed. These printers can be made to communicate to the material resource planning software to reconcile the material weighed from inventory. These processes do decrease the sources of errors if the programs are all validated completely to ensure that they are free of ambiguity.
Audit
Periodic audit of production batch records should be conducted to ensure that the dispensing process retains all traceability of materials used in any batch of product. Ensure that when multiple lots of one component are used in a production batch, there is information about the quantities of each lot used in the batch record.
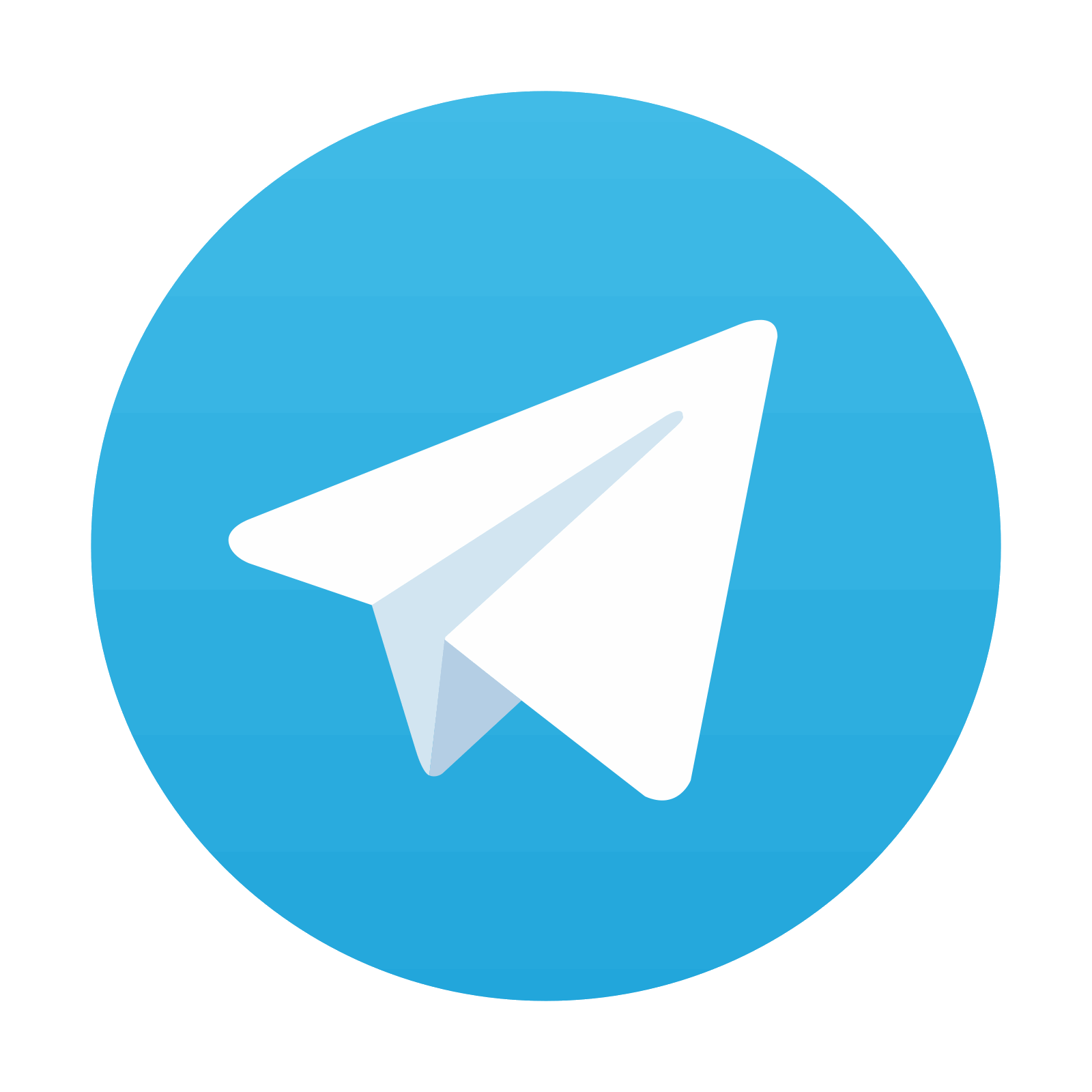
Stay updated, free articles. Join our Telegram channel
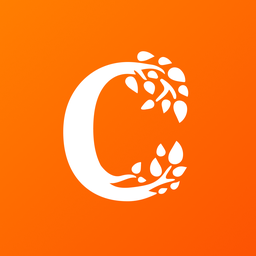
Full access? Get Clinical Tree
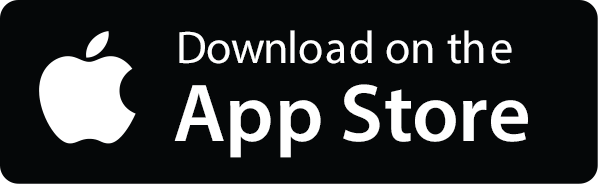
