Copper Alloy Surfaces Kill Bacteria and Reduce Infections
James H. Michel
Harold T. Michels
Corinne A. Michels
Disinfection and sterilization, as well as ordinary cleaning, are necessary for infection control. Beyond the situations where surgical instruments and medical devices touch sterile surfaces within the human body, there are many opportunities to transmit infections in hospitals. These include interactions involving touching between patients, patient and visitor, and patient and health care worker as well as touching environmental surfaces by patient, visitor, and health care worker. It is well known that infection control and prevention is a serious problem not only in hospitals but also in other health care facilities, schools, public transportation systems, food production facilities, restaurants, public and office buildings, and cruise ships. According to a report from the Centers for Disease Control and Prevention, 1.7 million patients were infected (in 2002) while in a US hospital causing approximately 100 000 deaths and resulting in $35.7 to $45 billion in additional treatment costs.1 Bacteria commonly reside in health care facilities and continue to cause health careassociated or health care-acquired infections. This together with emergence of new antibiotic-resistant strains complicates an already difficult situation. The ability of microbes to survive on surfaces for prolonged periods increases the probability that they will be transferred to patients and others. In addition, a variety of staph strains, sometimes including aggressively infectious strains, are found on the skin of most people and are easily transferred between patients, from visitors, from health care workers, and to objects. These objects are sources that transfer contaminants to others who touch them. Thus, it is not surprising that the microbial burden of frequently touched surfaces in health care facilities play a significant role in infection causality.2
Microbes are everywhere, not just in hospitals. You can become infected anywhere, just by going to work, at an event at your child’s school, or having a night out at the movies. Mass transit systems are particularly problematic. A recent study conducted in the subway system of New York City identified 1688 bacterial, viral, archaea, and eukaryotic taxa in public areas.3 Because this included disease-causing organisms, it is suggested that it is prudent to minimize touching of surfaces in transit systems and to wash or use hand sanitizers as soon as possible upon exiting. Then there are numerous school closings due to outbreaks of H1N1 influenza and even methicillin-resistant Staphylococcus aureus (MRSA) infections reported among school athletes; norovirus episodes on cruise ships that sometimes cause the vessels to return to port early4; as well as outbreaks of Escherichia coli O157:H7 related to ingesting contaminated food from major national restaurant chains, distributors of ground beef and poultry products, and tainted supermarket-prepared foods.
Aggressive sanitation procedures, like handwashing and regular cleaning and disinfecting, are the first line of defense. However, this alone has not solved the problem. In this chapter, the benefits of adding antimicrobial copper touch surfaces to help in the fight against infections are described and discussed. Antimicrobial copper should be viewed as an addition to and not a substitute for good sanitization and disinfection procedures. Keep in mind that antimicrobial copper surfaces, unlike other methods, require neither staff training nor behavioral changes to be effective. Antimicrobial copper alloys are continuously active, 24 hours a day, 7 days a week, without any human intervention. They are our newest weapon in the fight against infections.

Copper is listed in the periodic table of elements as a metal. Metals are usually solid at room temperature; have a luster; are hard, ductile, and malleable; and are good conductors of electricity and heat. Alloys are made by combining one metal with one or more other elements,
typically metals, to create improved properties such as strength, hardness, and corrosion resistance. For example, C26000, a brass alloy, consists of 70% copper and 30% zinc. In this case, zinc is added to increase strength and decrease cost. Other attributes of brass include an attractive yellow gold-like appearance and acoustical properties desirable for musical instruments. Even C10200, which contains a minimum of 99.95% copper, is classified as an alloy. Modern metallurgy continues to develop alloys for specific uses and over 800 copper alloys of a variety of compositions and properties are available today. Of these, 500 are registered with the US Environmental Protection Agency as having significant antimicrobial activity. Table 24.1 lists the composition of a few examples of copper alloys.
typically metals, to create improved properties such as strength, hardness, and corrosion resistance. For example, C26000, a brass alloy, consists of 70% copper and 30% zinc. In this case, zinc is added to increase strength and decrease cost. Other attributes of brass include an attractive yellow gold-like appearance and acoustical properties desirable for musical instruments. Even C10200, which contains a minimum of 99.95% copper, is classified as an alloy. Modern metallurgy continues to develop alloys for specific uses and over 800 copper alloys of a variety of compositions and properties are available today. Of these, 500 are registered with the US Environmental Protection Agency as having significant antimicrobial activity. Table 24.1 lists the composition of a few examples of copper alloys.

Copper, as a metal, has been used by man since prehistoric times. It was one of the first metals to be used by humans,6 most likely because it was found as “native copper,” a natural uncombined metallic form of copper. The earliest copper artifacts are from the Neolithic period. Early uses include jewelry, figurines, tools, bells, vessels, coinage, and weapons. The discovery of the 5300-year-old mummified body of the “Ice Man,” in the Swiss Alps in 1991 was widely reported. He was found with a copper axe. This is just one indication of how copper was used in ancient times. Two periods in history are named after the metal, the Copper Age and the Bronze Age. Bronze is an alloy of copper and tin. Because bronze is strong and can hold a sharp edge, it was widely used in weapons until the introduction of iron.
|

Thousands of years before the discovery of bacteria by Louis Pasteur, the ancients were aware of the sanitizing properties of copper.7 The bible suggests that water stored in copper or bronze vessels was free of disease-causing agents. Ancient Hindu tradition recommends storing household water in copper vessels for improved health. It was confirmed in a recent study that overnight storage
of contaminated water in copper vessels kills bacteria, making the water safe to drink.8
of contaminated water in copper vessels kills bacteria, making the water safe to drink.8
An ancient medical text, written in Egypt circa 2400 BCE, was purchased in 1862 by a book dealer named Smith. Now commonly referred to as the Smith Papyrus, this text provides insight into the use of copper in medicine. It describes how to treat infected chest wounds and promote healing with copper. The Papyrus speaks of a “green pigment” that is believed to be a copper compound such as malachite (copper carbonate hydroxide mineral). It was also written in another ancient text, the Ebers Papyrus circa 1500 BCE, that metallic copper splinters and shavings, copper salts and oxides, can treat burns and promote healing of infected wounds. Similarly, the Hippocratic Collection (written, in part, by the Greek physician in 460-380 BCE) indicates that leg wounds can be treated with a poultice that includes verdigris, the natural patina formed when copper is exposed to air or seawater, and red copper oxide among other oxides and natural products, all dissolved in wine.
Hippocrates also recommended the use of bronze for medical instrumentation due its propensity to promote healing. The famous Roman surgeon Galen (130-200 CE) fabricated and used bronze instruments, which were found in Pompeii and Herculaneum. Many examples of early bronze surgical instrumentation survive until today.9
Even when the germ theory of infections was known, reports of the benefits of copper continued to be recorded. During two Paris cholera epidemics (1865 and 1866), the French physician Victor Burq determined, by statistical analysis, that only 16 deaths occurred among 30 000 workers in the copper industry, whereas the death rate was 10 to 40 times higher among similar noncopper workers. During World War I, it was found in a few cases that, when fragments from copper-containing projectiles were not removed from a wound, the wound healed surprisingly well and infection free.7

Copper, which is highly recyclable, continues to be used in large quantities today in electrical applications (65%), construction (25%), transportation (7%), and elsewhere (3%). Some specific applications include industrial and home electrical wiring, potable water plumbing tube, electronic connectors, heat exchanger tubing in steam power plants, circuitry wiring and electrical contacts, tubing for natural gas, magnetrons on microwave ovens, seawater lines, welding electrodes, irrigation systems, medical gas distribution systems, printed circuit boards, locks and door hardware, wiring for glass defrosting systems, hydraulic lines, electromagnets, electrical motor windings, sleeve bearings (bronze), ship propellers, heat sinks in electronic devices, fittings, fasteners, screws, plumbing faucets, architectural roofing, statues, transformers, and the subject of this chapter, antimicrobial touch surfaces.

As described in the following text, copper alloys have strong efficacy against a wide range of both gram-negative and gram-positive bacteria. Copper alloys are also effective against fungi and inactivate viruses.
In 1983, Kuhn10 published a study of bacterial levels found on brass (C26000: 70% copper, 30% zinc) and stainless steel (S304000: 18% chromium, 8% nickel) doorknobs in a hospital in Erie, Pennsylvania. Whereas stainless steel doorknobs were heavily contaminated, the brass doorknobs contained only a few isolates of strep and staph bacteria. Almost 20 years later, this paper came to the attention of H. Michels, a coauthor of this chapter. It was decided to confirm the antimicrobial activity of copper alloys using E coli O157:H7, a toxin-producing bacterium responsible for numerous food recalls, that leads to hemorrhagic diarrhea and kidney failure.
As reported by Wilks et al,11 a concentrated suspension of this microorganism was spread over the surface of coupons of several compositions of copper alloys in a sterile environment at room temperature and ambient relative humidity. At specified time intervals, the microorganisms were removed from the coupon surface and survival determined, with stainless steel as the experimental control. More than a 7.5 log (<99.99999%) in bacterial levels was observed at 45 minutes on two 99.9% copper containing alloys (C10200 and C11000), and only a few, if any, survivors were observed by 100 minutes of exposure. The other alloys showed similar but less dramatic results in proportion to their copper contents.
A few years later, Hong et al12 observed similar results in a study using a standard laboratory E coli strain. The initial inoculum contained about 109 colony-forming units (CFUs), and at 45 minutes, a 9-log drop was measured indicating that all were killed, as can be seen in Figure 24.1. An approximately 1-log decrease was observed at 15 minutes, the time required for the sample to dry on the coupon surface, and more rapid killing occurred between 15 and 45 minutes. Again, no significant decrease in live bacteria was observed on the stainless steel. In regard to specific alloys, Hong et al12 compared a series of copper alloys ranging from nearly 99.9% copper (C11000) to 60% copper (C28000). They found that the extent of initial killing at 15 and 30 minutes correlated with the copper content of the alloy (see Figure 24.1). However, complete killing was observed in all of the alloys at 45 minutes, ranging in copper content down to 60%. Several others achieved similar results and showed a strong correlation between the copper content of the alloy and killing efficacy, when challenged by E coli.13,14,15,16
![]() FIGURE 24.1 Escherichia coli survival on copper-zinc alloy surfaces containing different copper concentrations. E coli strain ATCC 23724 was grown in Luria Broth to mid-log phase (OD600 about 0.3), harvested by centrifugation from 100 mL of culture, and resuspended in 0.85% sodium chloride (NaCl) to a final volume of 500 µL. The 100 µL of concentrated cells were spread over the surface of metal coupons of 304 stainless steel (S30400); 99.90% copper (C11000); and copper-zinc alloys C24000, C26000, and C28000 containing 80%, 70%, and 60% copper, respectively (alloy compositions are listed in Table 24.1). Following the indicated time of exposure, the cells were washed from the coupon surface with 100 µL of 0.85% NaCl and samples taken to titer survival. The results represent at least two independent trials. Abbreviations: CFU, colonyforming unit; Cu, copper. From Hong et al.12 Reproduced with permission from American Society for Microbiology. Copyright © 2012 American Society for Microbiology. |
The “dry inoculation method” that uses a smaller inoculum was developed by Espírito Santo et al17 to better simulate how environmental surfaces become contaminated. By limiting the sample volume, this method favors very rapid drying. When this “dry inoculum method” was used, it was observed that bacterial killing initiated immediately. When alloy C11000 (99.9% copper) was challenged with E coli O157:H7, a 9-log drop was observed in only 1 minute.17 The dry inoculum method was also used to test a copper-nickelzinc alloy (C75200, 65% copper) and a brass (C28000, 60% copper). The result was over 9 logs of killing of E coli on both alloys within 15 minutes. These findings suggest that the killing times reported by Wilks et al11 and Hong et al12 were a result of the time required for the larger sample applied to dry, thus effectively delaying direct contact between the microorganism and the alloy surface.
Approximately 126 000 hospitalizations each year in the United States are caused by the “super bug” MRSA.18 The efficacy of copper alloys against MRSA has been repeatedly confirmed in independent studies.15,16,19,20,21 The power of copper alloys is its ability not only to kill bacteria after its surface is initially contaminated but also to keep on killing after being repeatedly recontaminated, without any intermittent cleaning. As illustrated in Figure 24.2, C11000, containing 99.9% copper, maintains efficacy after a total of 8 inoculations without cleaning between inoculations over 24 hours.13 Although a fall-off in efficacy is seen in C11000 between 12 and 24 hours, this will decrease if the reinoculation time is extended. In contrast, the quantity of MRSA increases after each inoculation on the stainless steel.
![]() FIGURE 24.2 Methicillin-resistant Staphylococcus aureus (MRSA) survival on copper (C11000) and stainless steel (S30400) following multiple inoculations. S aureus (MRSA) samples spread over the surface of metal coupons of 304 stainless steel (filled diamonds) and nearly 100% copper (open squares). Following the indicated time of exposure, the cells were washed from the coupon surface and samples taken to titer survival. Reprinted with permission from Anderson and Michels.13 |
Three out of five clinically important MRSA strains tested on pure copper were killed within 60 minutes, and the remaining two strains were killed within 80 to 100 minutes, as reported by Gould et al.16 A series of copper alloys, including brass and bronze, were challenged by MRSA inoculations as high as 105 to 108 CFUs per coupon, and greater than 99.9% kill was observed within 2 hours, as reported by Anderson and Michels.13 Noyce et al15 found that lowering the initial bacterial load resulted in a shorter time for pure copper to kill MRSA, from 60 minutes at 107 CFUs per coupon to 15 minutes at 103 CFUs per coupon. The lower level is more representative of the amount of contamination found on surfaces in hospitals.
One-third of enterococcal infections that occur in intensive care units (ICUs) in the United States are caused by vancomycin-resistant enterococci (VRE).22 It is primarily transferred from environmental surfaces to patients and health care workers by touch.23 Strains of vancomycinresistant Enterococcus faecalis and Enterococcus faecium were killed in less than an hour by copper alloys containing at least 90% copper, but in contrast, they survived for several weeks on stainless steel, as reported by Warnes et al.22 Gould et al16 also reported similar results. The aforementioned
studies imply that the use of copper alloy surfaces in hospitals should help fight VRE infections in ICUs.
studies imply that the use of copper alloy surfaces in hospitals should help fight VRE infections in ICUs.
Clostridium difficile is hard to kill. Its spores survive under extreme conditions, including up to 5 months on dry inanimate surfaces.24 They are also not killed by all hospital-grade disinfectants, including those containing quaternary ammonium. Patients taking broad-spectrum antibiotics or who are otherwise immunocompromised are quite susceptible to C difficile, and it is very hard to cure. Weaver et al25 reported that C difficile vegetative cells are highly sensitive to exposure to copper alloys, but C difficile spores are relatively resistant. Copper alloys ranging from 65% to 100% copper killed 105 C difficile spores in between 24 and 48 hours, a rather prolonged period. However, no loss in viability was seen on stainless steel. Wheeldon et al26 reported that, after inducing C difficile spore germination, greater than 99% reduction from 106 CFUs/cm2 was observed within 3 hours of exposure to a pure copper surface. Another spore-forming Bacillus species displayed similar results, in that the vegetative cells were highly sensitive to copper alloys, whereas the spore form was resistant.27,28 It was also reported that a sporulation-defective strain of Bacillus subtilis was rapidly killed on copper alloy surfaces containing 60% to 100% copper, but a sporulation-competent strain exhibited only 1 log of killing, according to San et al.28 These findings suggest that the addition of germinant to cleaning formulations could enhance the antimicrobial efficacy of copper alloys against spore-forming bacteria.
Viruses must invade other organisms to reproduce. However, copper alloy samples were found to permanently inactivate 75% of influenza A (H1N1) in 1 hour and almost 100% after 6 hours, according to Noyce et al.29 Norovirus can ruin a cruise ship vacation. It is insidious because it can be transferred by hand-to-hand contact, touching environmental surfaces, and even ingesting contaminated food. Presently, the only method available to control norovirus outbreaks is to thoroughly clean and disinfect surfaces with bleach. Neither a vaccine nor an effective treatment exists. It is also hard to study because human norovirus cannot be cultured in the laboratory. However, murine norovirus, MNV-1, has been identified as a close surrogate. In one study, murine norovirus was found to be no longer infectious after as little as 30 minutes of exposure to copper (99.9% copper) and 60 minutes of exposure to copper-nickel (90% copper) surfaces, but the viral particles remained infectious when exposed to stainless steel for even longer times, according to Warnes and Keevil.30 When using the “dry inoculum method,” the inactivation rates were found to be 5 minutes for both copper (99.9% copper) and copper-nickel (90% copper) surfaces. In a subsequent study, Warnes et al31 observed that capsid integrity was compromised upon coming in contact with copper alloys. These findings suggest that copper alloy railings in hallways and stairs, elevator buttons, and door hardware on cruise ships should help control and prevent norovirus outbreaks.
There is significant variability in the sensitivity of fungal species to copper alloy surface exposure.32,33 Quaranta et al33 found that Candida albicans and Saccharomyces cerevisiae vegetative cells were both extremely sensitive to copper alloy surface exposure when tested using either the wet or dry inoculums. However, when Weaver et al32 tested a number of spore-forming species including Aspergillus niger, Aspergillus flavus, Aspergillus fumigatus, Penicillium chrysogenum, Fusarium culmorum, Fusarium oxysporum, and Fusarium solani on copper and aluminum coupons, it was observed that spores of all of these species were extremely resistant to copper surface exposure. Note that Weaver et al32 choose aluminum rather than stainless steel as the control material because their study was aimed at air conditioning systems where mold is a problem. Aluminum is commonly used as fins on tubes to facilitate heat (and cold) transfer. Aluminum, like stainless steel, has no antimicrobial efficacy. P chrysogenum and the Fusarium species were found to not survive on copper after 24 hours. In contrast, the spores exposed to the aluminum surface showed no decrease in viability over the same time period. It required 4 to 10 days of exposure to copper for complete killing of the spores of A flavus and A fumigatus. Amazingly, A niger spores were still viable and showed no evidence of killing even after 10 days of exposure to copper. However, when A niger was in the vegetative state, its hyphae were unable to grow over a copper coupon, demonstrating significant inhibition, but were able to readily grow over the surface of the aluminum coupon. Thus, growth and survival of vegetative cells of these fungal species appears to be sensitive to copper alloy surface exposure, but spores are extremely resistant.
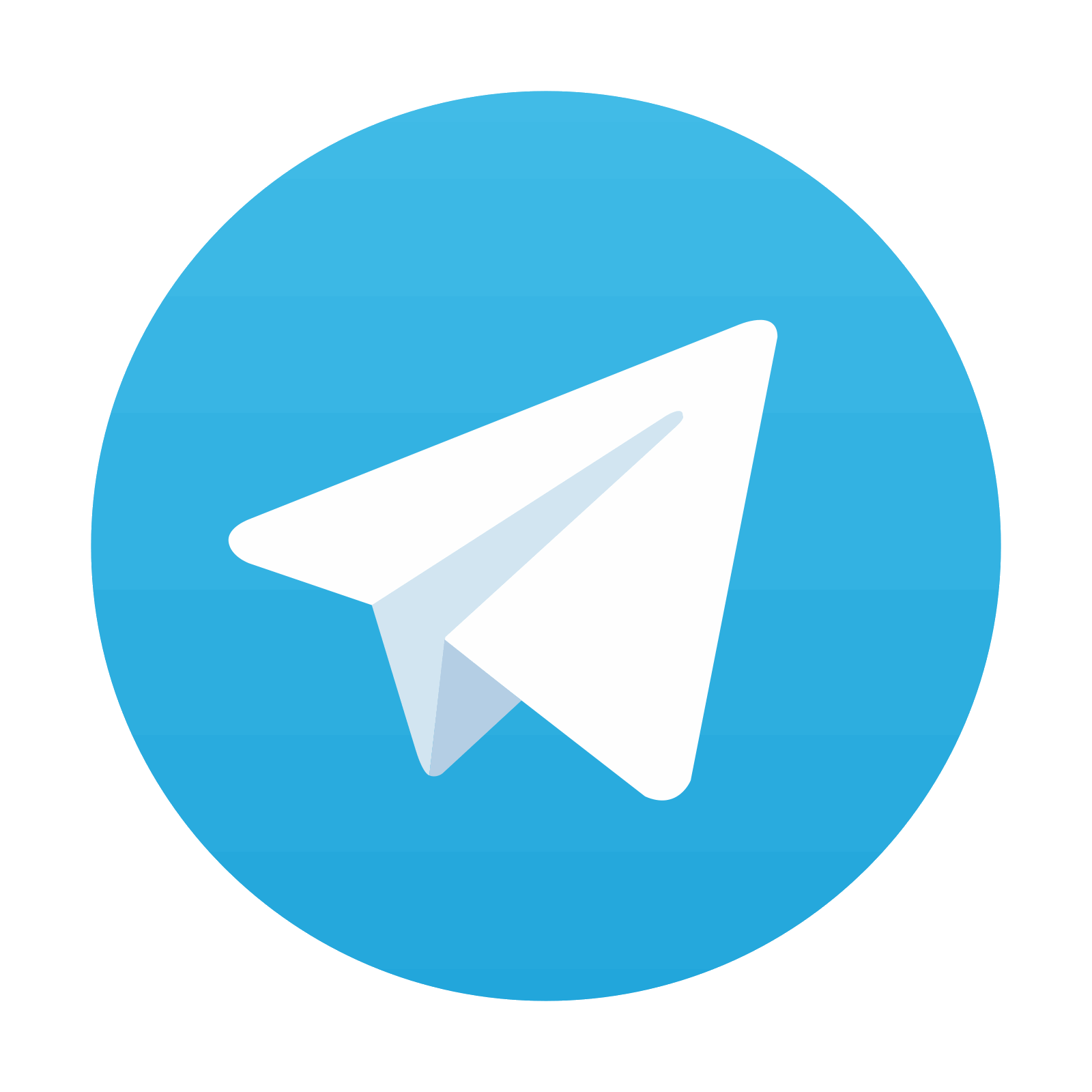
Stay updated, free articles. Join our Telegram channel
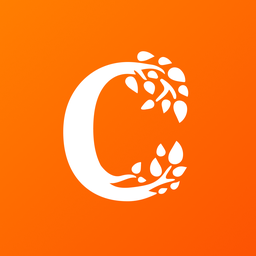
Full access? Get Clinical Tree
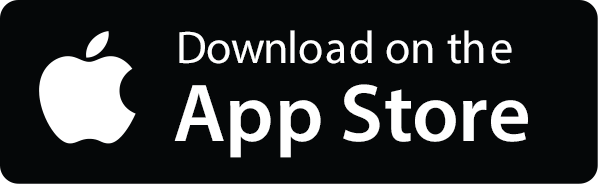
