!DOCTYPE html PUBLIC “-//W3C//DTD XHTML 1.1//EN” “http://www.w3.org/TR/xhtml11/DTD/xhtml11.dtd”>
Chapter 56: Artwork Development and Controls
The development of labeling artwork is a collaborative process involving both the commercial side of the organization (for example, Marketing) and the medical and regulatory side of the organization (for example, Medical Affairs, Regulatory Affairs). Often, competing demands for space occur as the groups negotiate how to incorporate all of the required safety and regulatory information while maintaining the look and feel or the corporate branding that is important to the company. This negotiation process ultimately results in the artwork (graphical representation of the proposed labeling) that is used by printing firms to produce the final printed labeling.
Like the drug product itself, the labeling that accompanies the product has a life cycle of its own. The collaborative development of labeling begins early in the product development phase and evolves as more information is learned about the drug, specifically its utility and safety profile. The labeling evolves after approval as more is learned about the drug product through its use in the general population. Product labeling needs to be current with all new information to ensure that medical practitioners and patients have the information that they need to make the best possible healthcare decisions.
A graphical representation of the product labeling is developed and is typically what is reviewed and approved internally before being sent to the printers for conversion to the actual labeling materials. These graphical files need to be controlled to ensure that what is submitted to the printers is current and contains the most accurate information regarding the safety and efficacy of the product. Version control is critical to this process, and procedures should be in place, both within the organization and at the labeling printers, to control current and obsolete versions of the graphical files.
Printing Process
Regulatory agencies expect that there will be appropriate rigor in the printing process to ensure that labeling is accurate and that errors do not occur. Pharmaceutical companies should treat labeling vendors as they would any other vendor (that is, labeling vendors should be evaluated or audited and qualified in a manner similar to any other raw material or packaging component vendor).
Vendor Proof
Once the graphical representations are reviewed and approved internally, the files are forwarded to the labeling vendors to be printed. The labeling vendor should be expected to take the files and generate a vendor proof that is reviewed by the pharmaceutical company to ensure that the new or revised labeling is accurate and matches the internally approved artwork. If issues are noted, procedures should be in place to ensure that corrections are made and that preventive measures are implemented to preclude future problems.
Gang Printing
Gang printing is a practice that involves placing many different print projects on the same printing sheet in an effort to reduce printing costs and paper waste. The United States Food and Drug Administration (FDA) good manufacturing practices (GMP) regulations explicitly prohibit the use of gang printing of labeling for different drug products or different strengths or net contents of the same drug product unless the labeling from the gang-printed sheets is adequately differentiated by size, shape, or color. Because of the high potential for errors, pharmaceutical companies typically do not allow gang printing of drug product labeling.
Roll Label Splicing
Flexographic printing has become commonplace in the production of pharmaceutical labeling. After the labels are printed, they are typically die cut and, if necessary, wound onto master rolls. These master rolls are then slit into individual label widths and counted to provide the required number of labels per roll. It is not uncommon for the roll stock to break during the various steps of the process or for the process to require multiple rolls of label stock to complete the printing run. When this occurs, it may be necessary to splice the roll stock together. It is critical for the label vendor to clearly identify the presence of splices in each roll of labeling. The vendor should provide a report that demonstrates that they have verified that the labeling on each side of the splice is correct and that there are no issues with the printed copy on either side of the splice. Upon receipt of the labeling at the pharmaceutical company, verification of the spliced rolls should take place.
Off-Line Printing
The packaging and labeling of pharmaceutical products typically occurs together as a single operation. Labeling is applied to the packaged product, and a unique batch number and expiration date is printed on the labeling as part of this operation. In these cases, where the batch and expiration date are printed online, it is possible to return unused labeling to the secured storage area for use on another packaging run.
There are instances, however, where the labeling must be printed off-line with the batch-specific information. Equipment on the packaging lines may not be capable of printing the batch-specific information, or the type of product may preclude the ability to print this information online. In these instances, very tight controls over the use of this batch-specific labeling need to be in place. Any labeling that is printed off-line with batch-specific information should be stored separately from other labeling, and there should be very tight controls on reconciling the quantity used during the packaging run. Any labeling that is printed off-line with batch-specific information can not be returned to inventory and must be discarded and destroyed after completion of the packaging operation.
Secure Storage of Labeling
GMP regulations require that printed materials and labeling be stored in an area with limited access and in a manner that will prevent errors. According to FDA GMP regulations, the labels and labeling materials for each different drug product, strength, dosage form, or quantity of contents should be stored separately (that is, adequately segregated, either spatially or in separate containers) and with suitable identification to preclude errors. The regulations state that access to the labeling storage area should be limited to authorized personnel. Similarly, labeling that is returned to the labeling storage area (for example, after completion of a packaging operation) should be identified appropriately and stored in such a manner as to prevent errors.
Similar requirements are identified in the Canadian GMP regulations. Printed packaging materials need to be stored in an area that is restricted to designated personnel who are supervised by individuals with training and experience and who are directly responsible to the person in charge of the manufacturing, or a person having the same qualification.
Destruction of Labeling
On a global basis, the GMP regulations are consistent when it comes to destruction of labeling. Any labeling that fails to meet specifications upon incoming receipt must be destroyed. Labeling that is superseded by new labeling, or is considered outdated, should be destroyed. Finally, any labeling that is not used, and that has been printed with lot (batch) number and expiration date (or any other batch-specific information) should be destroyed. No matter what destruction process is used, however, it should render the labeling materials unusable to prevent their unauthorized or mistaken use.
Control of Graphical Files and Printing Plates
One of the major challenges in the area of label printing is the frequency with which product labeling changes in today’s regulatory environment. Regulatory agencies want to ensure that healthcare providers and patients have access to current information related to the safety of pharmaceutical products, and, as a result, updates to the labeling are common. Version control and the handling of current and obsolete graphical files and printing plates is of critical importance to ensure that this current information is incorporated correctly and in a timely fashion.
Labeling vendors, like the pharmaceutical company itself, should have procedures in place to control current and obsolete versions. Current versions should be accessible for use, while obsolete versions should be archived or removed from an active file location. Printing plates for obsolete versions should be destroyed and documentation of their destruction provided to the pharmaceutical company for verification of the destruction process.
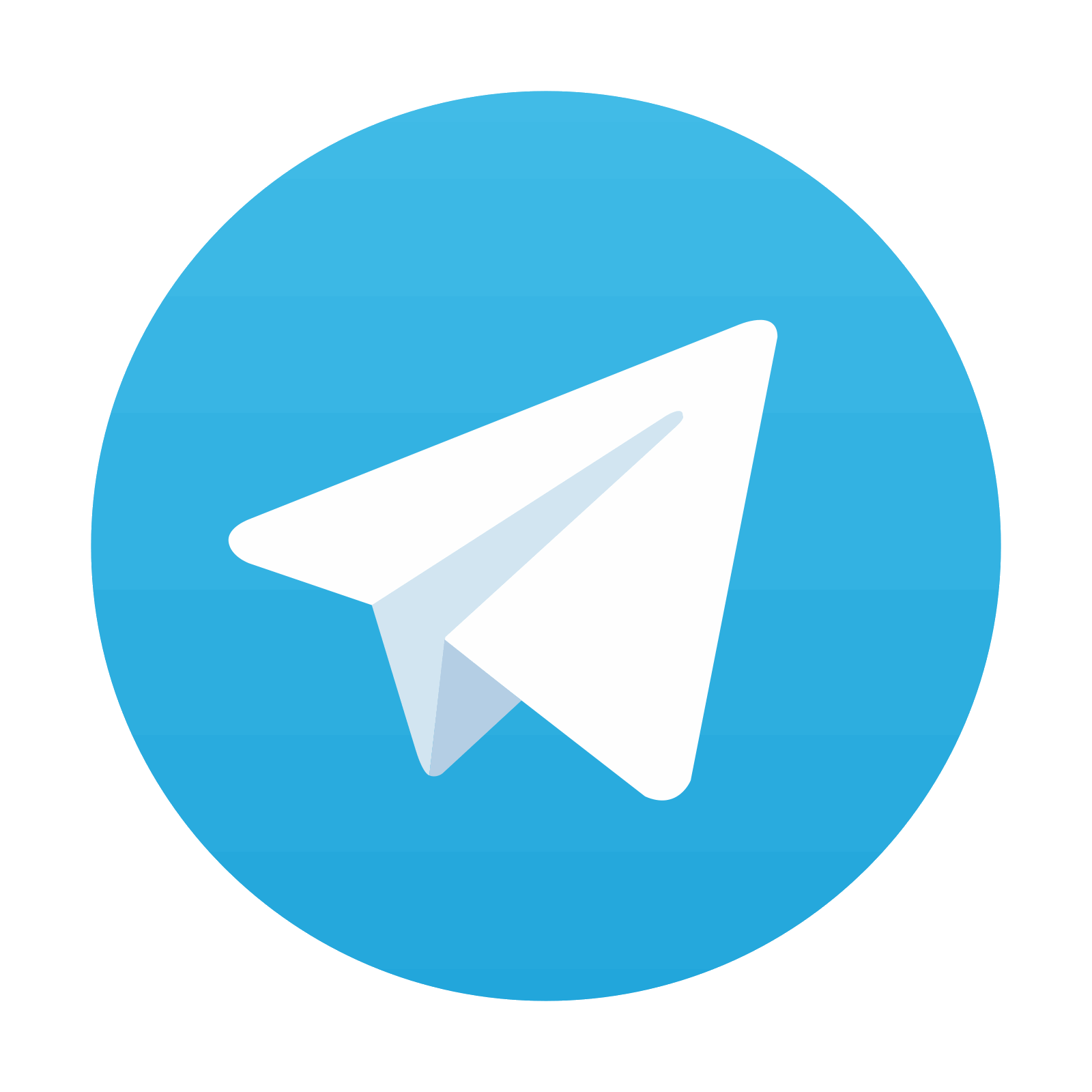
Stay updated, free articles. Join our Telegram channel
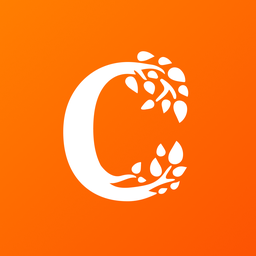
Full access? Get Clinical Tree
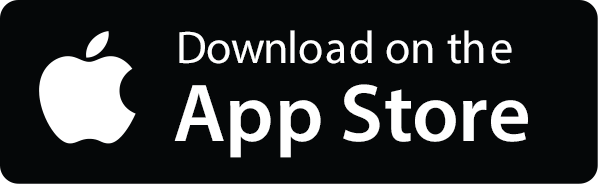
