Fig. 1
Seven-hole locking reconstruction plate

Fig. 2
Schematic illustration of the bone–plate fixation using monocortical locked screws
2.2 Data Acquisition
The information about the geometry was obtained with two methods. The first method was the profile projection and the second one was the micro CT. The profile projector used was a Mitutoyo PJ311.
With this information, it was possible to evaluate the larger sizes such as length, thickness, diameters, and others. These values were compared with the ones obtained with the digital caliper rule Western DC-60.
The micro CT SkyScan 1176 was used to obtain details about curves and radius. It is important to remember that with the files generated with micro CT, it is possible to reconstruct the 3D file using medical softwares and export the results in Stereolithography (stl) files. However, in the present study the main objective was to develop the geometry using only direct measurements, a type of method more efficient for simple geometries and resulting in fewer problems with surfaces in meshing for FEA.
In order to show an example of SkyScan results in micro CT, the Fig. 3 presents some projected images from the process. These projections need to be transformed into slices for reconstruction.

Fig. 3
Some projection images from process of micro CT
2.3 Image Treatment
During the work with images obtained using CT or micro CT, it is common to present noises or contours less defined. If the interest is to reconstruct the three-dimensional image with quality in measurements and details, the image treatment is crucial. For this, there are many ways to convert the files with problems into quality files within the tolerance.
The suggested method for the present study was to use one algorithm written in MATLAB code with a simple algorithm that is able to convert one image file of CT to a binary image which is formed by zero and one that represent the black and white colors.
The control of boundary in the image is made with values obtained from manual and visual measurements already made before. So, if the contour is a resolved problem, the details of geometry can be observed with more precision.
The simple routine used is described in Fig. 4, and an example (one slice image of micro CT) before and after of the treatment with algorithm can be visualized in Fig. 5.

Fig. 4
Matlab routine used to convert the slices of micro CT in binary images for reconstruction
2.4 CAD Software and Mesh File
After obtaining all information about the geometry, the next step was to load them in CAD software. There are many types of softwares that can be applicable, but in the present study it was chosen Solidworks 2012, because the tools are very simple and the toolbox of surfaces and molds are very useful for reconstructed geometries. In this software is possible to define regions of interest for analysis.
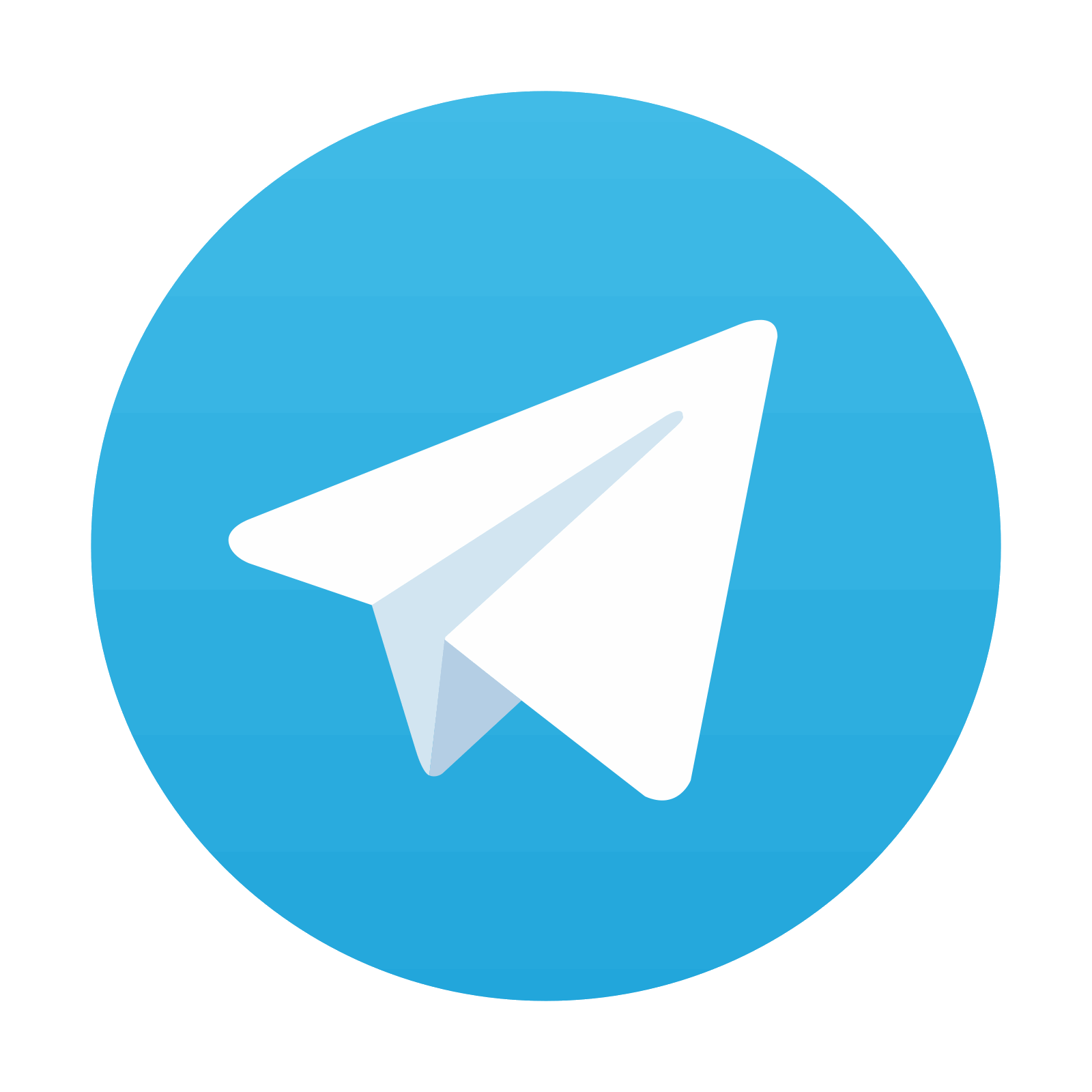
Stay updated, free articles. Join our Telegram channel
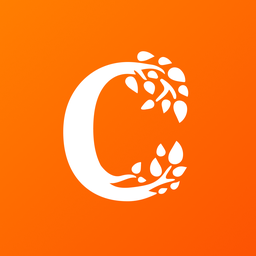
Full access? Get Clinical Tree
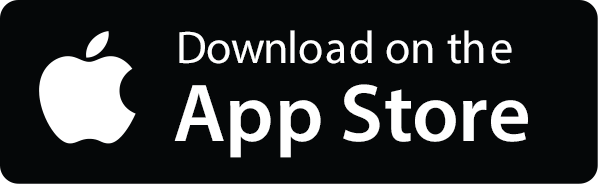
