Fig. 3.1
Classification of friction types
At present the integrity of knowledge about friction and phenomena accompanying it are integrated by the science that came to be named tribology. This word originates from two Greek words: tribos—friction and logos—science [3].
Tribology as a scientific discipline appeared in the early 60s and covers a broad range of problems including experimental and theoretical studies of physical (mechanical, electric, magnetic, thermal), chemical, biological and other phenomena connected with friction [4]. Tribology in the recent years has acquired new categories tribochemistry , tribophysics and tribomechanics.
Tribochemistry studies interactions between contacting surfaces and a chemically active environment. It studies the problems of corrosion in friction, chemical principles of selective transfer and the effect of chemically active substances appears in friction due to destruction of polymers or lubricating materials on the surfaces of parts.
Tribophysics studies the physical aspects of interaction between contacting surfaces during mutual displacement.
Tribomechanics studies the mechanics of interactions between contacting surfaces in friction. It deals with the laws of energy dissipation, impulse as well as the mechanical semblance, relaxing vibrations in friction, reversing friction, equations of hydrodynamics and other aspects in relation to the problems of friction, wear and lubrication.
A handbook glossary of over 1,200 terms of friction, wear and lubrication of machine parts was published in 1979 in the USSR. A number of terms relating to Tribology are standardized in the CIS [6] and the far-abroad countries [7]. For example, GOST 27674-88 contains 107 terms classified according to the types of friction, wear, lubrication, methods of lubrication and lubricating materials. We quote some most frequently used terms.
External friction is the phenomenon of resistance to relative displacement appearing between two bodies in the zones of tangential contact between surfaces accompanied by energy dissipation.
Internal friction is the phenomenon of resistance to relative displacement of particles of one and the same body.
Wear is the process of destruction and separation of the material from the solid body surface and (or) accumulation of its residual deformation in friction manifest in gradual change of the size and (or) shape of the body.
Fatigue wear is the mechanical wear due to fatigue fracture during repeated deformation of microvolumes of the material surface layer.
Wear is the wear result determined in established units. Wear can be expressed in the units of length, volume, mass, etc.
Wear resistance are the properties of a material to resist wear under definite conditions of friction estimated by the value inverse to the speed of wear or wear rate.
Friction at rest is the friction of two bodies during microdisplacements to transition to relative motion.
Friction of motion is the friction of two bodies in relative motion.
Sliding friction is the friction of motion of two solid bodies at which the speeds of the bodies in contact points have different magnitudes and directions or different by the magnitude and direction.
Rolling friction is the friction of motion of two solid bodies at which their speeds in contact points have the same magnitude and direction.
Force of friction is the force of resistance during relative displacement of one body over the surface of the other body under the external force tangential to the common boundary between these bodies.
The maximum force friction at rest is the force of friction at rest that induces motion if exceeded.
Sliding velocity is the difference between speeds of bodies in contact points during sliding.
Friction surface are the surfaces of bodies involved in friction.
Coefficient of friction is the relation of the force of friction between two bodies to the normal force holding these bodies together.
Friction without lubricating material is the friction of two when their friction surfaces have no lubricating material of any type.
Friction with lubricating material is the friction of two bodies when their friction surfaces are lubricated with a material of any type.
Lubricating material is the material delivered to the friction surface to reduce the force of friction and (or) the wear rate.
Lubrication is the action of the lubricating material reducing the force of surface friction and (or) the wear rate.
Lubrication is delivery of the lubricating material to the friction surface.
Liquid lubrication is the lubrication when friction surfaces of parts are fully separated by a liquid lubricating material.
Solid lubrication is the lubrication when friction surfaces of parts in relative motion are separated by a solid lubricating material.
Hydrodynamic (gas dynamic) lubrication is the liquid (gaseous) lubrication when the friction surfaces separate fully under pressure that spontaneously appears in the liquid (gas) in relative motion of surfaces.
Hydrostatic (aerostatic) lubrication is the liquid (gaseous) lubrication when the friction surfaces of parts in relative motion or at rest separate fully due to delivery of a liquid (a gas) into the clearance between friction surface under external pressure.
Elastohydrodynamic lubrication is the lubrication when the characteristics of friction and thickness of the liquid lubricating film between the two surfaces in relative motion are determined by the elastic properties of the materials of two bodies and by the rheological properties of the latter.
Boundary lubrication is the lubrication when friction between the surfaces in relative motion and their wear are determined by the properties of the lubricating material different from the volume viscosity.
Semiliquid (mixed) lubrication is the lubrication when partially hydrodynamic and partially boundary lubrication appears.
Viscosity is the volume properties of the liquid, semiliquid or semisolid substance to exert resistance in friction.
Lubricity is the properties of a lubricating material to reduce wear and the force independently of its viscosity.
3.2 Friction of Lubricated Solids
3.2.1 Molecular-Mechanical Theory of Friction
The modern ideas about the nature of friction of solid bodies are based on the molecular mechanical (adhesion deformation) theory of friction [8–12]. According to this theory, the force of friction F fr both with and without a lubricating material is due to the forces of intermolecular interaction and the forces of resistance to viscoelastic and plastic deformation of near-surface layers in solid bodies in the zone of contact . Both the first and the second components of the forces of friction are directed opposite to the motion of rubbing bodies. The component due to the forces of intermolecular interaction are termed the molecular or adhesive component of the forces of friction F a , while the component relating to deformation of near-surface layers in rubbing bodies is termed mechanical or cohesive component of the forces of friction F к . With these designations in mind the force of friction according to the molecular mechanical theory is a sum of the above forces:
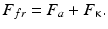
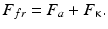
(3.1)
It is the most general tribological law. Depending on the type and conditions of friction, the structure of the bodies, and bonds in them, individual components can increase or reduce or even disappear altogether. For example, in case of internal friction in a liquid the adhesive component F a is close to zero, while in case of external friction of perfectly smooth surfaces the cohesive component F k would have been equal to zero.
Adhesion and cohesion are known to be due to one and the same forces, their localization is different [13]. If the forces act within the body, they produce cohesion, if they act on the surface; they produce adhesion (Fig. 3.2).
Meanwhile, in the real conditions these forces result from formation and rupture of bonds (often termed as friction bonding) in the contact zone during tangential displacement of contacting solid bodies. The magnitude of the forces appearing between rubbing bodies is hugely affected by the physico-mechanical and chemical properties of surface layers and by the properties of the lubricating medium. The notion of lubricity serves to assess the latter.
According to [11], lubricity is the integrity of physical and chemical properties of a lubricating material causing reduction of the adhesive and cohesive interaction between rubbing solid bodies. The higher the lubricity, the weaker are the forces of friction bonds between rubbing surfaces.
Wear is not always due to the parameters of lubricity; it can be due to other factors [13]. That is why investigation of lubricity aims at identifying specifically the physical and chemical properties producing the integral or lubricating effect and at establishing how these properties on the physical state and chemical composition of a lubricating material [11–14].
The thickness and the nature of the latter in the zone of dynamic contact determine the type of lubrication and thus the type of friction. The notion of relative thickness is used to characterize the thickness of the lubricating layer. The lubricating layer relative thickness h l is determined as a ratio between the lubricating layer thickness h and the sum of mean arithmetic deviations of profiles R a1 and R a2 of contacting surfaces [3]:
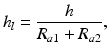
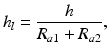
(3.2)
The lubricating layer relative thickness is an essential criterion of classification of types of lubrication.
The following types of lubrication are identified: boundary, liquid (hydrodynamic, elastohydrodynamic, hydrostatic , etc.) and mixed (partially boundary, partially liquid) [3, 15]. Figure 3.3 shows the classification of the types of lubrication based on the criterion h l .
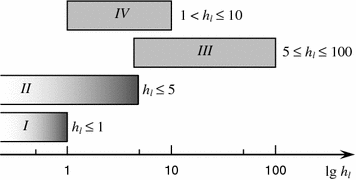
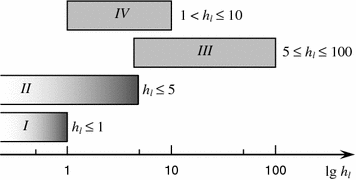
Fig. 3.3
Classification of types of lubrication based on criterion of lubricating layer relative thickness h l : I boundary; II mixed; III liquid (hydrodynamic, hydrostatic, aerostatic); IV elastohydrodynamic (liquid) [3]
Because among the above-listed types of lubrication the boundary lubrication challenges the tribologists most, below the relevant processes will be considered.
3.2.2 Boundary Lubrication of Solids
According to international standard ISO 4378/3, the boundary lubrication implies the type of lubrication to which the properties of the lubricating material in the volume cannot be attributed and which is determined by the properties of the boundary layers that appear during interaction between the surface and the lubricating material as a result of physical and chemical adsorption [7].
The boundary lubrication of surfaces of interfaced bodies separates them with a rather thin layer of the lubricating material thickness (the thickness is from one molecule to 0.1 µm) (Fig. 3.3). The protective boundary films in the process of friction prevent seizure of solid bodies, and it is a decisive factor when hydrodynamic lubrication is impossible due to small thickness of the lubricating layer [8–12, 16]. These films can appear continuously in friction due to the effective environment performing the lubrication action.
The surface layers of solid bodies are known to possess the structure and properties different from those of the material lying deeper [5, 8, 11]. Each particle within the body (the atom or molecule making it up) is exposed to the forces of interaction (repulsion or attraction) from the part of surrounding particles (Fig. 3.2). The resultant of these forces is equal to zero in this case.
The force directed away from the surface inwards the solid body acts in the layer with thickness comparable with the radius of molecular interactions due to their asymmetric effect on each particle. It induces excessive potential energy termed the surface energy [12].
Thus, the particles in the surface layer create the field of surface forces. Due to them the molecules of gases, liquids and other substances are adsorbed by the solid body surface when they approach it and reduce the surface energy [17]. The substances with definite properties, structures and adsorbability tend most to be adsorbed [18]. These substances are called surfactants. There are two large classes of surfactants with different absorption patterns and some other properties.
The first class is low-molecular compounds of biophilic nature. These compounds have the hydrophilic “head” (one or several polar groups, for example, –OH, –COOH, –SO3H, –OSO3H, –COOMe, –N+(CH3)3I, –NH2) and the hydrophobic “tail”. As a rule, it is an aliphatic chain that includes sometimes an aromatic group.
The second class is high-molecular surfactants in which hydrophilic and hydrophobic groups alternate and distribute regularly throughout the polymeric chain.
The molecules of a low-molecular surfactant, for example, are organic acids, their metallic soaps, alcohols, etc., that orient during adsorption perpendicular to the surface. The active “head” of the surfactant molecule disposes on the surface, the hydrophobic “tail” orients normally to it.
The adsorbed surfactant layer can be both monomolecular or polymolecular (Fig. 3.4). Each layer of the polymolecular film consists of the similarly oriented molecules. The active parts of surfactant molecules of the first row attach to the solid body surface, the molecules of the second row attach to them and then the molecules of the hydrophobic “tail” facing the hydrophobic “tails” of the first row. The orientation of the molecules of the first group, of the second row of the fourth group, etc., repeats [11, 12]. Even if non-polar molecules occur among surfactant molecules in some layer, they orient parallel to the surfactant molecule. As a result the boundary layer appears on the surface in which surfactant molecules are oriented properly rather than chaotically like in a liquid.
The boundary layers are in a specific aggregate state having the quasicrystalline structure that justifies to assert their specific liquid phase, or the boundary phase [11, 15]. Here physical adsorption and chemosorption can take place. In case of physical adsorption, that is very fast-evolving reversible process, the molecules of the medium on the solid body surface retain their individuality [19]. The physical adsorption is typical when the molecules of the adsorbed substance stay for some time on the surface, then they can desorb in case of suitable conditions, for example temperature rise [11, 20].
The adsorption of the surfactant on the solid body surface can result in the effect of strength drop due to adsorption (the Rebinder effect) [13]. There are external and internal adsorption effects.
The external effect is observed during adsorption of the surfactant on the external surface of the deformable solid body and it is typical for comparatively large surfactant molecules (the molecules of organic acids, alcohols, etc.). As a result of the external adsorptive effect the surface energy of the solid body diminishes leading to a drop of the flow limit of the material in the surface layer. In this case it is termed as the plasticizing effect of the surfactant.
The internal adsorptive effect is due to adsorption of comparatively small molecules of the surfactant (the molecules of wear, etc.) on the internal surfaces of the interface, or nucleation of fracture microcracking. The walls of microcracks tend to cover the entire surface, the surfactant molecules travel to its top. But they are unable to penetrate to the very top because of the comparability between the surfactant molecules and the microcrack width near the top (Fig. 3.5).
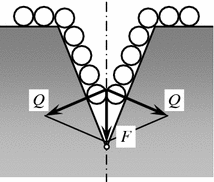
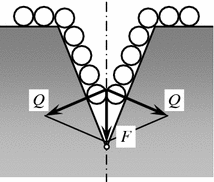
Fig. 3.5
Scheme of wedging effect of adsorption of polar molecules of lubricating material. F Pressure of adsorbed layer; Q wedging forces
The forces of repulsion between the molecules and the surfactant begin to wedge the microcrack walls out assisting further growth of microcracking. Reduction of the surface energy of the microcrack walls favors it during adsorption of surfactant molecules. These processes result in the embrittlement of the surface layer on solid bodies.
Thus, adsorption of the surfactant alters significantly the mechanical properties of surface layers on solid bodies that can play a decisive role in controlling the process of friction and attendant wear [10–12, 21].
Adsorption of polar molecules of organic acids exerts a significant effect on the surface properties. When adsorbed on the solid body surface these molecules attach to it with carboxyl groups and orient perpendicularly [11]. The structure of the first layers of molecules adsorbed on the solid surface resembles the crystalline structure. The higher disposed layers have a lamellar structure (Fig. 3.6). Then the mechanical strength of the boundary layers of molecules grows as they approach the solid body surface [11].
The surface layer changes still more during chemical adsorption (chemosorption). When the molecules are adsorbed on the surface of the solid adsorbent the adsorbate enters into chemical interactions with the surface layer material and form chemical compounds.
It is used in modern lubricating oils in which additives are applied with the action based on the chemical interaction between their active components and solid bodies. As a result of chemosorption, the friction surfaces are modified chemically and acquire the surface compounds reducing friction and wear [22, 23]. The chemical mechanism of the lubricating effect relates directly in this case to the original lubricity of the lubricant. It acts as a carrier of components in the chemical reaction, while friction unit acts as a reactor in which the processes are controlled both by the composition of the lubricant and the nature of the rubbing surface and friction conditions [11].
The significance of the chemical factors of the lubricating effect is considerably greater at elevated temperature when lubricating materials or their components are exposed to mechanochemical transformations. The resulting products prevent seizure and reduce wear. Specific antiwear and antiscoring additives boost these effects [22–24]. Among them the most popular compounds containing chemically active groups including atoms of chlorine, sulfur, phosphorus, nitrogen. The chemical interaction of such additives , for example, with metallic friction surfaces is affected considerably by elevated temperature and the catalytic effect of the metal. Temperature measurements in the contact spots in friction have revealed that it can reach 700–800 °C in separate contact spots. Meanwhile, the recent data justify to believe that some active additives interact chemically with the rubbing surface already at temperatures of the order of 20–30 °C [23–27].
Other methods of applying antiwear and antiscoring films are determined and extensively studied recently. Specific attention is paid to investigation of the “wearless” friction characterized by abnormally low coefficients of friction and wear. the so-called “third body”, or a fine separating layer with low mechanical properties acting as a lubricant appears and regenerates in the process friction over the interphase boundary between contacting bodies [35, 36] under the specific conditions of the effect of the medium when there is the effect of selective transfer [28–31], grafted polymerization [32–34] or irradiation. The positive gradient of mechanical properties appears in the near-surface contact layer the lubricating effect in the boundary lubrication mode is known to have no relation with the viscosity or chemical transformations in the zone of dynamic contact [10–12]. It has a more intricate pattern and is due to appearing of the specific boundary layer because of the effect of active lubricating components on the mechanical properties of surfaces of solid bodies [11, 37]. Hence, on the one hand, an adsorptional layer appears with its specific structure [11, 38–40] and, on the other hand, adsorption plasticizes the rubbing surface significantly contributing to the lubricity of the friction system [41]. The process of boundary friction evolves in the surface layers on interfaced bodies and the boundary layer on the lubricating substance with the comparable thicknesses of these separating layers.
Lubricity in boundary lubrication relates to the state of the surface of the “solid body—lubricant” interface. The interface manifests a sharp leap of shear resistance. Due to formation of the boundary layer and adsorptional plasticization the leap is somewhat smoothed [8, 11].
Since the surfaces of solid bodies are rough, the conditions of formational of adsorptional layers are different. There are three types of portions of contact surfaces [11]: (a) the portion separated by the polymolecular boundary layer; (b) the portion separated by mono- and bimolecular layers; (c) the portion over which projections come into contact and crumble by shear deformation. As a result, the total resistance to mutual shear of the surfaces at low shear rates when temperature and tribochemical effects van be ignored is a sum of their resistances: (a) the shear in the polymolecular layer; (b) the shear of the surfaces separated by monomolecular layers; (c) the shear of the surface layer on the solid body [11, 14].
Formation of the polymolecular boundary layer and the surfactant it contains is observed by different methods [11, 38–40]. The most comprehensive review of the modern methods of studying liquid boundary layers on solid surfaces is made [11]. These methods are based on determination of thicknesses of boundary layers under different conditions. They have revealed sufficiently reliable characteristics of the lubricating effect of various materials during boundary lubrication.
Application of the methods to determination of the thickness of boundary layers has enabled to establish that formation and thickness of the polymolecular boundary layer depends much on the composition and structure of surfactant molecules. The molecules with short or ramified alkyl radicals yield just fine boundary layers or do not produce them at all [11]. The decisive role in producing thicker boundary layers plays the alkyl radical length [11, 42, 43]. Solution of higher alcohols and amines are capable too to form polymolecular boundary layers [40], but they are weaker than the boundary layers from the fatty acids with the same alkyl radical length [14].
The shear resistance in the polymolecular boundary layer from the solutions of fatty acids and alcohols declines as the alkyl radical gets longer. If the clearance between rubbing surfaces is stabilized by external, the alkyl radical length stops affecting the shear resistance [11].
Moreover, it is a typical feature that the polymolecular boundary layer becomes stronger as it gets thinner [11–13].
Any experimental study of the lubricating effect of monomolecular surfactant layers is impeded due to the inhomogeneity of the real solid body surface and practically impossible shear localization between adsorbed layers of molecules since flow of the substrate destroying these layers cannot be prevented. Such flow can occur if the contact zone is loaded even without shear [11, 14].
The force of the contact interaction in case of the monomolecularгo adsorptional layer depends primarily on the degree of filling of the layer and relates correspondingly to the adsorbability of the surfactant in this case, unlike the polymolecular boundary layer, the length of the alkyl radical of the adsorbed surfactant has little significance. If the adsorptional layer is not filled, short-chain molecules can be more effective. It is explained by their easier orientation in the unfilled layer and their considerable role in reducing the surface energy [11]. Therefore the regularities relating the lubricity to the chemical composition of the adsorbed surfactants are the same for the cases of the poly- and monomolecular boundary layers.
It is indicated above that plasticization of the surface layers of rubbing solid bodies by adsorption matters significantly for the lubricating effect of various substances. The degree of plasticization is determined by the pattern of deformation and the nature of dynamically contacting bodies and lubricating media.
Adsorptional plasticization affects the friction contact in two ways and hence the friction. First, the shear resistance in the surface layer on the solid body drops. Second, resistance to normal stresses declines thus the contact surface smoothes and local stresses on this surface are relieved. On the whole, surface shear resistance reduction with the related deformable volume decrease diminish the forces of friction, while the surface smoothness and smaller brittleness reduce wear [41, 44].
Differentiated approach to the adsorptional effects governing the lubricity of various materials in boundary friction shows that the optimal additives to lubricants ensuring higher lubricity are different for each of the three types of the surface contact sites.
In case of the polymolecular boundary layer, the decisive role belongs to the molecular-kinetic factors determining resistance to thinning of the layer. In case of the monomolecular adsorptional layer, they are the strength of the adsorptional bonding and the kinetics of restoration of the adsorptional layer on the juvenile surface. In case of the adsorptional plasticization the whole surface activity and the kinetics of diffusion of molecules into the defects in the surface layer on the solid body are determined.
The analysis of the said above leads to the conclusion that high lubricity is ensured providing shear localizes fully or in its considerable portion in the polymolecular boundary layer in which the shear resistance is minimal or absent practically. Such high lubricity can be achieved if the lubricating layers in the friction zone acquire the liquid crystalline structure [42, 45, 46].
So far it is established that the seizure of surfaces in friction during boundary lubrication can occur only when the temperature of the friction contact exceeds some critical value T cr for the given combination of the lubricating material and the friction couple material [13, 24]. The effect of the friction couple material manifests itself in the weakening of the latter with other unchanged conditions leading to a sharp drop of the critical temperature. disintegration of the lubricating layer and seizure onset take places most probably due to desorption of the surfactant agents the lubricating material contains [20].
It is shown that the properties of boundary lubrication can change in time. This boundary lubrication feature relates closely to the kinetics of adsorption of polar molecules . The time interval within which the polar molecules orient properly on the rubbing surfaces has been termed the latent period. Therefore, the friction process should stabilize within the latent period and influence considerably the wear resistance of dynamically contacting materials. Sometimes the surfactants the lubricating material contains rival with the molecules and the lubricant base during adsorption on the surface of the solid body. It prolongs the latent period that affects negatively also the wear resistance of friction couples [47].
3.2.3 Solid Lubricants
One effective way to promote lubricity developed in the recent years is introduction into the lubricant the additives of layered (lamellar) solid substances [48]. These substances include molybdenum disulfide, graphite that produce colloid solutions in the lubricant and oil soluble compounds. They are specifically promising because they assist in forming stable lubricating systems [49]. The specificity of the lubricants with the compounds of this type is that they decompose at elevated temperatures and undergo a sequence of transformations forming simpler products than the original.
These transformations occur primarily in boundary layers, as a result of the surface compounds appear in the zone of friction ensuring their effectiveness.
The appeal of the lamellar solid substances is to their some specific properties. For example, graphite is capable of oriented adsorption on the metallic surface [11]. The adsorptional graphite layer represents seemingly a single endlessly long molecule in two measurements. The bonding between these two planar layers of molecules is very weak, so that graphite splits up easily into numerous very fine flat scales. These scales orientate tangentially to the solid body surface and make its microgeometrical profile more like a plane. Secondary adsorption occurs exactly on this surface rejuvenated by graphite, for example, adsorption of fatty acid molecules that in combination yields a positive effect on the boundary friction process.
Many hypotheses and assumptions have been advanced to explain this low friction of lubricating materials with solid lamellar substances. The hypothesis belied most justified is advanced in [50]. From its standpoint the mechanism of the lubricating effect of both lamellar solid substances and high-molecular linear polymers can be explained. Its essence is the following.
To ensure low friction of solid lubricating materials the surface energy should be low over the planes of their cleavage or over the surfaces of bidimensional molecules (lammels), while the interaction between the planes should be weak enough. The additional factor is lack of high enough potential barriers and relative constancy of potential energies of the supposed sliding planes. This requirement presumes that the atoms or molecules adsorbed by substances can under certain conditions easily travel over the surface representing the so-called bidimensional gas (or the bidimensional liquid). This behavior is possible for physically adsorbed molecules and little probable in case of chemosorption. Hence, if physical adsorption of the surface energy declines and molecules locate in interlayer spaces, the spacing between the planes grows so that the friction coefficient should drop. While, if the adsorbed molecules or atoms enter into chemical interactions with contacting contact e surfaces, they inhibit their easy sliding relative one another and increase the coefficient of friction and wear.
This approach permits to explain rather well both high and low friction of lamellar solid substances when they operate under different conditions. The experience shows that these conditions affect considerably both the energy of bonding between sliding planes and the pattern of adsorptional interactions between molecules and their ability to migrate easily towards rubbing surfaces, i.e. the antifriction properties of lamellar lubricating materials in general [46–50].
3.2.4 Hydrodynamic Lubrication of Solids
It has been noted before that the lubricity during boundary lubrication of solid bodies does not depend on the viscosity of lubricating materials and it is rather due to formation of interphase boundary layers with the specific structure in the contact zone.
In case of liquid lubrication it is different when the lubricating layers are not enough thick and viscosity determines resistance of the lubricating material to motion (the internal friction) and it does depend on the nature of the interfaced surfaces [5–7, 12]. The ribbing surfaces are separated by a film of the liquid lubricating material under pressure. Since the pressure on the lubricating material equalizes the external loading, the force of friction in liquid lubrication is a sum of resistance to sliding of its layers over the thickness of the lubricating interlayer and results therefore from the rheological properties of the latter.
Hydrostatic and hydrodynamic lubrications are discriminated in response to pressure in the lubricating film and the way of its formation.
The hydrostatic lubrication implies formation of liquid films between interfaced surfaces in which static pressure results from continuously externally maintained circulation of the liquid and balancing of external loading so that the rubbing surfaces are separated [5]. Special methods serve to produce the hydrostatic pressure sufficient to separate friction surfaces (Fig. 3.7), while leak of the lubricant through the ends of the hydrostatic bearing is compensated, as a rule, by relevant external delivery.
During hydrodynamic lubrication the pressure in the lubricating film develops and continues automatically. It is ensured by suitable design means in friction systems and selection of the lubricating material in response to the speed of sliding [12]. The mechanism of creating pressure in the bearing layer is most vividly examplified by the flat bearing (Fig. 3.8).
Assume the plate A–A travels with a speed v at an angle α to the stationary substrate B–B. The space between the plate and the substrate is filled with a viscous liquid. The liquid layer wets the plate A–A, while the forces of viscous friction move the adjacent as high layer. The motion is thus transmitted between the layers, excepting the layer wetting the stationary substrate B–B. As a result the lubrication is sucked into the narrowing wedge clearance and definite pressure is maintained in it that determines the load bearing capacity or the load lifting capacity of the lubricating layer.
So, the wedge clearance is the necessary condition to maintain the hydrodynamic lubrication mode.
It is apparent that a definite thickness of the lubricating interlayer is as essential for existence of both hydrostatic and hydrodynamic lubrication when the interlayer manifests the volume properties of the liquid. Because of that the pressure in the lubricating film in real conditions should be maintained such that the least thickness of the lubricating layer is not equal to the sum of mean projections on interfaced surfaces. It is achieved in friction units with special technological and design methods and techniques.
However, in the majority of cases, there are several or at least two types of effective friction. In this case the portion of the rubbing surfaces contact directly (friction without the lubricating material) and there is a portion separated by the boundary film (boundary friction) or by the film of the lubricating material (hydrodynamic or elastohydrodynamic friction). Frequently microwedges appear due to interactions between individual projections so that the load carrying capacity of the films increases additionally. The simultaneous integrity of the concurrent phenomena is called mixed friction.
When analyzing mixed the physical (viscosity , density, compressibility, etc.) and physico-chemical (the affinity to adsorption and chemosorption, chemical affinity of additives with the surface) properties of the liquid and rubbing bodies should be taken into account. The lubricating films appearing during mixed are 2–5 times thicker than the sum of projections on contacting surfaces (Fig. 3.3).
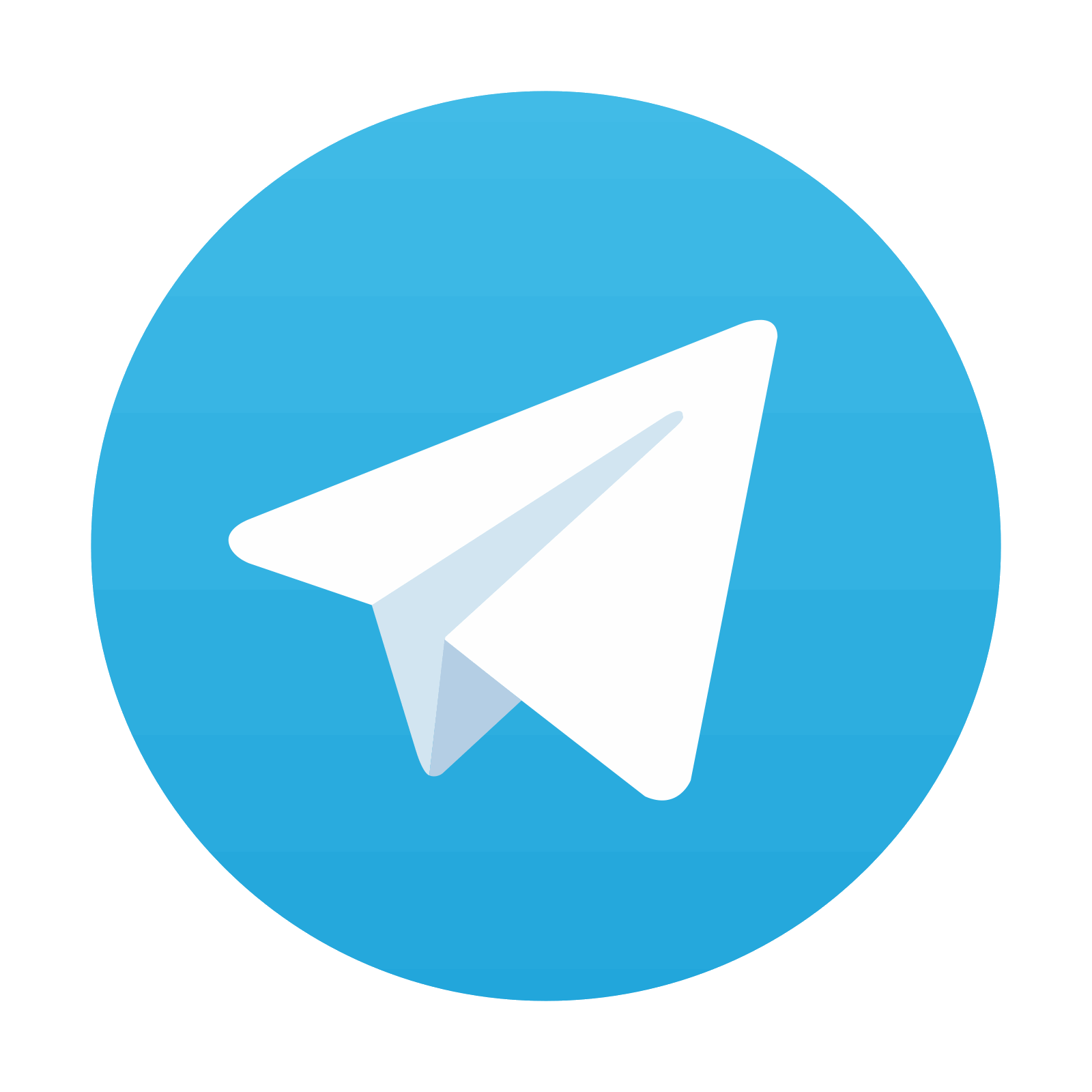
Stay updated, free articles. Join our Telegram channel
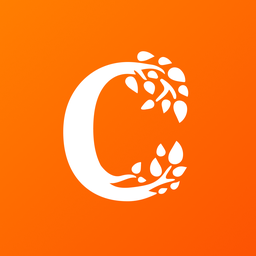
Full access? Get Clinical Tree
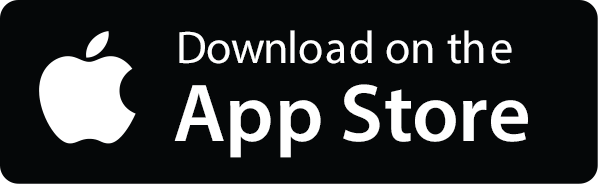
